How to Be Metallurgical Welding Specialist - Job Description, Skills, and Interview Questions
The demand for metallurgical welding specialists has grown significantly in recent years due to the increasing use of metals in a variety of industries, such as automotive manufacturing, construction and aerospace. As a result, those with the right qualifications and experience in the field are able to take advantage of the growing job market and enjoy a rewarding career. In addition to a strong understanding of metallurgical welding techniques, metallurgical welding specialists need to be proficient in mathematics, reading blueprints, interpreting safety regulations and using sophisticated welding equipment.
Furthermore, they must be highly knowledgeable of the various types of metals, their properties and the best ways to weld them. a successful metallurgical welding specialist is an invaluable asset for any company that uses metal components in its products or services.
Steps How to Become
- Earn a high school diploma or GED. In order to become a Metallurgical Welding Specialist, the first step is to earn a high school diploma or GED. This will provide a solid foundation for further education and training in the field.
- Enroll in a welding program. The next step is to enroll in a welding program at a community college or technical school. These programs typically last one to two years and include courses in safety, blueprint reading, welding theory and metallurgy.
- Get certified. After completing a welding program, you will need to get certified in order to work as a Metallurgical Welding Specialist. This certification can be obtained through the American Welding Society (AWS) or other professional welding organizations.
- Gain experience. Once you have your certification, the next step is to gain experience in the field. This can be done by working as an apprentice or taking on-the-job training courses.
- Obtain advanced training. To become an expert in the field, you may want to pursue additional educational opportunities such as taking advanced classes or attending seminars. These will help you develop a deeper understanding of metallurgy and welding processes.
- Consider a specialization. To further increase your marketability, you may want to consider specializing in a particular area such as underwater welding or aluminum welding. This can help you stand out from the competition and gain higher wages.
Metallurgical welding requires a high level of expertise and knowledge in order to be successful. To become a competent metallurgical welding specialist, one needs to have a thorough understanding of the various types of metals and how they react to different welding techniques. they must be well-versed in the different tools and techniques used in welding and have the ability to troubleshoot any potential issues that may arise during the process.
they must possess strong problem-solving skills and a good eye for detail so that they can identify any potential defects or inconsistencies in the welds. Finally, they must have strong communication skills to be able to effectively collaborate with other professionals on the job such as engineers and inspectors. With these skills and knowledge, a skilled and competent metallurgical welding specialist can be an invaluable asset to any project.
You may want to check Metallurgical Engineer, Metallurgical Technician/Dimensional Inspector, and Metallurgical Sales Engineer for alternative.
Job Description
- Develop, maintain, and implement welding processes and procedures related to metallurgical operations.
- Perform metallurgical tests on welds to ensure quality and accuracy.
- Analyze welding test results to ensure compliance with established standards.
- Provide advice and consultation to customers regarding welding processes and procedures.
- Monitor metallurgical welding operations and equipment to ensure safety, quality, and efficiency.
- Troubleshoot and correct welding problems as needed.
- Develop and update welding techniques, processes, and procedures to meet changing customer needs.
- Assist in the training of new welding staff members.
- Inspect welds for conformance with specifications and standards.
- Maintain records of all welding operations and activities.
Skills and Competencies to Have
- Knowledge of metallurgical principles and processes
- Ability to read and interpret welding symbols, sketches, and drawings
- Expertise in welding techniques, such as oxyacetylene, arc, and resistance welding
- Familiarity with the use of welding equipment, such as torches, electrodes, and wire feeders
- Ability to operate computerized welding systems
- Knowledge of safety regulations and procedures related to welding
- Understanding of quality control measures and specifications used in welding
- Ability to troubleshoot welding problems
- Proficiency in mathematics, including geometry and trigonometry
- Good communication skills
Welding is a critical skill in metallurgical engineering, as it allows for the joining of two separate components into one cohesive unit. Welding is a process that requires precision and accuracy, as it involves using a variety of tools to heat and reshape metal pieces. It is important for welders to have a good understanding of metallurgy, as welding temperatures and techniques vary depending on the type of metal being joined.
welders must understand the different types of welding processes, such as fusion, resistance, and pressure welding. In order to ensure the quality of the welds, welders must also be aware of the different types of welding defects and how to avoid them. Having these skills is essential for producing reliable and durable welds, which are necessary for the proper functioning of many industrial and structural components.
Metallurgical Quality Control Technician, Metallurgical Technician Supervisor, and Metallurgical Draftsperson are related jobs you may like.
Frequent Interview Questions
- What experience do you have working with welding techniques?
- What techniques do you use to ensure quality welds?
- How do you troubleshoot welding problems?
- How do you stay up-to-date with the latest advancements in welding technology?
- What experience do you have working with different materials?
- What safety measures do you take when performing welding tasks?
- Describe a successful welding project you have completed.
- What processes do you use to ensure welds meet industry standards?
- How do you communicate effectively with team members?
- What methods do you use to analyze metallurgical welding data?
Common Tools in Industry
- TIG Welder. Used to fuse two metals together with a tungsten electrode; eg MIG welding.
- MIG Welder. Utilizes a consumable wire electrode and inert gas to join metals; eg welding aluminum.
- Oxy-Acetylene Torch. Combines oxygen and acetylene to produce a flame which can be used to cut, weld, or heat metals; eg cutting a metal bar.
- Plasma Cutter. Uses an electric arc and compressed air to cut metals; eg cutting metal plate.
- Resistance Welder. Uses electric current to weld metals; eg welding steel.
- Spot Welder. Uses electric current to weld two pieces of metal together at specific points; eg welding two metal sheets together.
- Metal Shaper. Used to cut, shape, and form metal; eg cutting a metal pipe into a specific shape.
- Brazing Torch. Uses a torch and filler metal to join two metals together; eg brazing aluminum.
- Soldering Iron. Uses a heated iron and solder to join two metals together; eg soldering two wires together.
- Heat Gun. Uses hot air to heat and bend metals; eg heating a metal pipe before bending it.
Professional Organizations to Know
- American Welding Society (AWS)
- National Center for Welding Education and Training (Weld-Ed)
- The International Institute of Welding (IIW)
- American Society of Mechanical Engineers (ASME)
- Welding Research Council (WRC)
- The Fabricators & Manufacturers Association (FMA)
- American Bureau of Shipping (ABS)
- American Society for Testing and Materials (ASTM)
- Certification and Accreditation Administration of the Peoples Republic of China (CNCA)
- American National Standards Institute (ANSI)
We also have Metallurgical Research Scientist, Metallurgical Operator, and Metallurgical and Materials Engineer jobs reports.
Common Important Terms
- Arc Welding. A welding process that uses an electric arc to create heat for joining two or more pieces of metal.
- Brazing. A type of welding that uses a filler metal, typically an alloy of copper and zinc, to join two or more pieces of metal.
- Soldering. A process similar to brazing, but at a lower temperature, that uses a filler material to join two or more pieces of metal.
- Forge Welding. A welding process that involves heating two pieces of metal and hammering them together to form a bond.
- MIG Welding. A welding process that uses a consumable electrode and inert gas to create an electric arc and form a weld.
- TIG Welding. A welding process that uses a non-consumable tungsten electrode to create an electric arc and form a weld.
- Plasma Arc Welding. A welding process that uses a plasma torch to form a weld between two pieces of metal.
- Oxy-Acetylene Welding. A welding process that uses an oxygen-acetylene flame to form a weld between two pieces of metal.
- Shielded Metal Arc Welding. A welding process that uses a consumable electrode and an external shielding gas to form a weld between two pieces of metal.
- Resistance Welding. A welding process that uses electrical resistance to generate heat and form a weld between two pieces of metal.
Frequently Asked Questions
Q1: What is a Metallurgical Welding Specialist? A1: A Metallurgical Welding Specialist is a professional who specializes in welding metallurgical structures and components. They are responsible for selecting the appropriate welding technique and materials to join metal parts together, and ensuring the welds are strong and durable. Q2: What qualifications are required to become a Metallurgical Welding Specialist? A2: To become a Metallurgical Welding Specialist, one must have a high school diploma or equivalent, complete an apprenticeship program, and pass an American Welding Society (AWS) certification exam. Additional certifications may be required depending on the industry or job. Q3: What are some of the duties of a Metallurgical Welding Specialist? A3: A Metallurgical Welding Specialist typically performs duties such as inspecting work sites and materials, setting up welding equipment, determining the correct welding techniques and materials to use, and welding metal components. They also may be responsible for analyzing test results to ensure welds meet quality standards. Q4: How much does a Metallurgical Welding Specialist make? A4: According to the US Bureau of Labor Statistics, the median pay for a Metallurgical Welding Specialist in 2020 was $45,460 per year. Pay can vary based on experience, location, and other factors. Q5: What safety precautions must a Metallurgical Welding Specialist take? A5: A Metallurgical Welding Specialist must take proper safety precautions when working with welding equipment and hot metals, including wearing appropriate protective clothing, using eye protection, and properly ventilating their work area. They should also be aware of any potential hazards and take steps to mitigate them.What are jobs related with Metallurgical Welding Specialist?
- Metallurgical Process Engineer/Metallurgist
- Metallurgist
- Metallurgical Engineering Technician
- Metallurgical Technician
- Metallurgical Plant Manager
- Metallurgical Project Engineer
- Metallurgical Lab Technician
- Metallurgical Inspector
- Metallurgical Maintenance Technician
Web Resources
- Welding Certification & Training Program | Phoenix, www.rsi.edu
- Bachelor of Science in Welding and Metallurgical Engineering engineering.wayne.edu
- Welding Career Training Program - MIAT College of Technology miat.edu
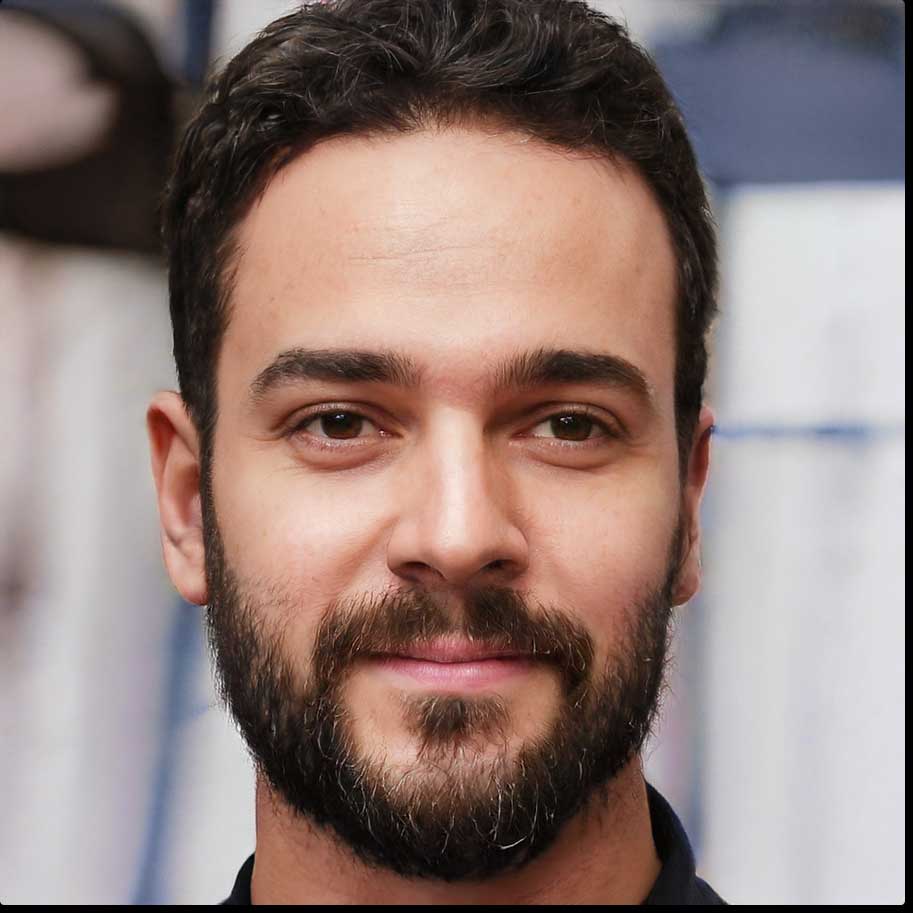