How to Be Occupational Safety Inspector - Job Description, Skills, and Interview Questions
When occupational safety inspectors are not present in the workplace, it can lead to numerous consequences. Without their expertise and oversight, workers can be exposed to hazardous conditions and dangerous equipment, leading to an increased risk of workplace injuries and fatalities. employers may be in violation of labor safety regulations and face fines or other penalties.
Furthermore, a lack of workplace safety can create a negative atmosphere in the workplace, reducing morale, productivity, and employee retention. It is therefore essential that employers prioritize the presence of occupational safety inspectors to ensure a safe and compliant workplace.
Steps How to Become
- Earn a Bachelor's Degree. Most employers prefer that occupational safety inspectors have at least a bachelor's degree in safety engineering, industrial hygiene, occupational safety or a related field.
- Obtain Relevant Work Experience. Employers also prefer applicants to have some relevant work experience. This can be obtained through internships or other practical training programs related to safety engineering, industrial hygiene or occupational safety.
- Earn Professional Credentials. Many employers prefer workers to hold professional credentials, such as the Certified Safety Professional (CSP) or the Professional Engineer (PE) certification. To obtain these certifications, applicants must meet certain requirements and pass an exam.
- Complete a Training Program. Many employers require occupational safety inspectors to complete a training program related to their job duties. This can be obtained through an employer, trade school or community college.
- Obtain a State License. Some states require occupational safety inspectors to have a license in order to practice in the state. Requirements for licensure vary by state, but may include passing an exam and completing continuing education courses.
- Get Certified by OSHA. The Occupational Safety and Health Administration (OSHA) provides voluntary certification programs for occupational safety inspectors. To obtain certification, applicants must complete an OSHA-authorized training program and pass an exam.
Staying ahead and efficient as an Occupational Safety Inspector requires dedication, discipline and a commitment to excellence. Keeping up to date with the latest regulations, laws and industry trends is essential for staying informed about the best practices in safety. investing in the necessary training, such as CPR and First Aid certifications, can help ensure that inspectors are prepared for any situation that may arise.
Finally, taking the time to develop and maintain relationships with key stakeholders, including employers and employees, can help build trust and confidence in the safety protocols being implemented. By taking these steps, Occupational Safety Inspectors can remain ahead and efficient in their work.
You may want to check Occupational Hazard Analyst, Occupational Health Advisor, and Occupational Health and Safety Manager for alternative.
Job Description
- Inspect workplaces for compliance with regulations, laws and health and safety standards.
- Investigate workplace accidents and dangerous incidents to identify the cause and prevent future occurrences.
- Monitor hazardous materials and equipment to ensure safety.
- Identify potential safety risks and hazards in the workplace.
- Issue written or verbal notices of violations and recommendations for corrective action.
- Prepare written reports to document findings, corrective actions and recommendations.
- Develop safety policies and procedures, and ensure they are followed.
- Provide safety training to workers on topics such as accident prevention, hazardous material handling, and emergency protocols.
- Work with employers to develop comprehensive safety programs to reduce accidents and injuries.
- Monitor compliance with state and federal regulations related to occupational safety.
Skills and Competencies to Have
- Knowledge of health and safety regulations, codes, and standards.
- Knowledge of applicable laws, rules, and regulations related to occupational safety and health.
- Knowledge of hazardous materials, hazardous waste, and hazardous substances.
- Ability to identify hazards in the workplace and develop strategies for mitigating them.
- Ability to inspect and evaluate workplaces for compliance with safety regulations.
- Ability to assess potential safety hazards and develop strategies for resolving them.
- Ability to maintain accurate records and reports related to safety inspections and other activities.
- Ability to review safety equipment, such as protective clothing, and make recommendations for improvements.
- Ability to communicate effectively with employees and management regarding safety issues and concerns.
- Ability to develop and deliver safety training programs.
Occupational safety inspectors play an important role in ensuring that workplaces are safe and healthy for workers and visitors. They inspect workplaces to identify potential hazards and then take measures to reduce or eliminate the risks. To be a successful occupational safety inspector, one must possess strong communication, problem-solving, and organizational skills.
Good communication skills are necessary to effectively explain safety regulations to employees and management, as well as to negotiate solutions with them. Problem-solving skills are important to anticipate potential hazards and determine the best ways to address them. organizational skills are necessary to keep track of inspections and reports.
Overall, these skills are essential for occupational safety inspectors in order to ensure the safety of workers and visitors in the workplace.
Occupational Safety Engineer, Occupational Environmental Scientist, and Occupational Therapist Assistant are related jobs you may like.
Frequent Interview Questions
- What experience do you have in developing and implementing safety programs?
- How would you handle a situation where an employee is not following safety regulations?
- What steps would you take to make sure a workplace is compliant with OSHA standards?
- How would you go about investigating and reporting a workplace accident?
- What methods do you use to stay current with new safety regulations?
- How do you prioritize safety inspections in a busy environment?
- How would you present safety information in an engaging way?
- How do you motivate employees to follow safety protocols?
- How would you handle a situation where an employer is not willing to comply with safety regulations?
- What challenges have you faced while conducting safety inspections?
Common Tools in Industry
- Personal protective equipment (PPE). Items used to protect oneself from hazards such as masks, gloves, helmets, eye protection, and other items. (Eg: Hard hats, safety glasses, and protective gloves)
- Respirators. Devices used to filter out hazardous particles from the air. (Eg: Dust masks, cartridge respirators, and air-purifying respirators)
- Fire extinguishers. Portable devices used to put out fires. (Eg: Water, foam, carbon dioxide, and dry chemical fire extinguishers)
- Lockout/tagout systems. A procedure used to prevent accidental re-energizing of equipment that has been isolated for servicing or maintenance. (Eg: Electrical locks, warning tags, and lockout boxes)
- Hazard communication systems. A way to inform workers of potential hazards they may encounter while on the job. (Eg: Material safety data sheets and hazard warning signs)
- First aid kits. Used to provide medical treatment for minor injuries or illnesses. (Eg: Bandages, antiseptic wipes, and over-the-counter medications)
- Emergency response plans. Plans used to respond to an emergency such as a fire or hazardous material spill. (Eg: Evacuation plans and emergency contact information)
- Chemical detection devices. Instruments used to detect hazardous chemicals in the workplace. (Eg: Gas detectors, sniffers, and radiation detectors)
Professional Organizations to Know
- American Society of Safety Professionals (ASSP)
- National Safety Council (NSC)
- International Safety Equipment Association (ISEA)
- International Association of Industrial Accident Boards and Commissions (IAIABC)
- American Industrial Hygiene Association (AIHA)
- Occupational Safety and Health Administration (OSHA)
- National Fire Protection Association (NFPA)
- Canadian Society of Safety Engineering (CSSE)
- Institute of Hazardous Materials Management (IHMM)
- American Conference of Governmental Industrial Hygienists (ACGIH)
We also have Occupational Kinesiologist, Occupational Medicine Physician, and Occupational Health Technician jobs reports.
Common Important Terms
- Hazardous Materials. Substances that are potentially dangerous to people, property, or the environment.
- Risk Assessment. The process of identifying and evaluating potential hazards in an environment, and determining the best course of action to reduce the potential for injury or damage.
- Accident Investigation. The process of collecting and analyzing data to determine the cause of an accident.
- Occupational Safety and Health Administration (OSHA). The federal agency responsible for protecting workers in the United States from workplace hazards.
- Emergency Response Plan. A written document that outlines how to respond to a workplace emergency.
- Personal Protective Equipment (PPE). Clothing or equipment worn to protect the wearer from potential hazards in the workplace.
- Workplace Safety Training. Training that provides workers with information on how to safely perform their job duties.
- Workers€™ Compensation. A system of benefits provided to workers who have been injured on the job.
- OSHA Standards. Regulations set by OSHA that outline safety and health requirements for employers and workers.
Frequently Asked Questions
What is the job of an Occupational Safety Inspector?
An Occupational Safety Inspector is responsible for ensuring compliance with safety regulations in the workplace. They inspect equipment, machinery, and materials to ensure they are safe to use and in compliance with safety regulations.
What qualifications do I need to become an Occupational Safety Inspector?
To become an Occupational Safety Inspector, you will need a minimum of a bachelor's degree in safety engineering, industrial hygiene, occupational health, or a related field. You may also need certification from a professional organization such as the National Safety Council or the American Society of Safety Engineers.
What is the average salary for an Occupational Safety Inspector?
According to the Bureau of Labor Statistics, the median annual salary for an Occupational Safety Inspector is $65,170 as of May 2019.
What are the duties of an Occupational Safety Inspector?
The duties of an Occupational Safety Inspector include inspecting workplaces for potential health and safety hazards; identifying and evaluating unsafe conditions; recommending corrective measures; conducting safety training; and documenting violations and corrective actions.
What are the working conditions of an Occupational Safety Inspector?
Occupational Safety Inspectors typically work in a variety of settings such as factories, offices, warehouses, and construction sites. They may work indoors or outdoors and may be exposed to hazardous materials or conditions.
What are jobs related with Occupational Safety Inspector?
- Occupational Disability Case Manager
- Occupational Exposure Scientist
- Occupational Health and Safety Officer
- Occupational Physiotherapist
- Occupational Health and Safety Technician
- Occupational Psychologist
Web Resources
- Occupational Safety | Occupational Safety occupationalsafety.eku.edu
- Occupational Safety | College of Science & Technology www.fairmontstate.edu
- Duke Occupational & Environmental Safety Office www.safety.duke.edu
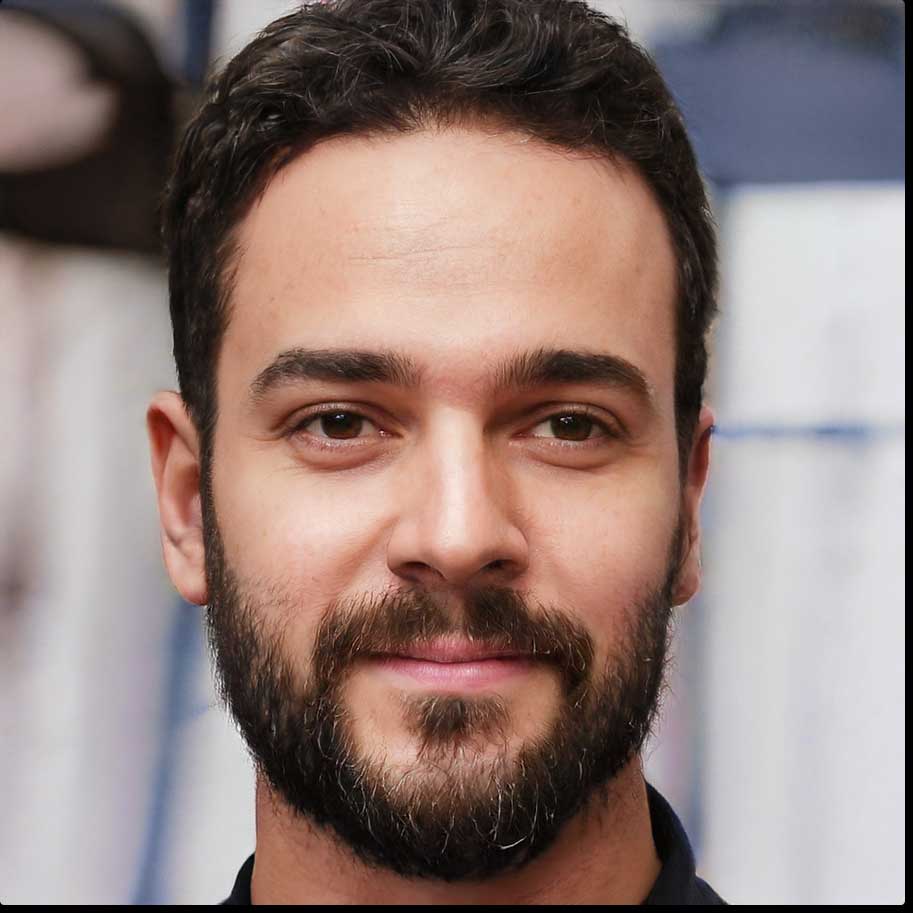