How to Be Occupational Hazard Analyst - Job Description, Skills, and Interview Questions
Working as an Occupational Hazard Analyst can be a difficult but rewarding job. It involves the identification, analysis, and assessment of potential occupational risks and hazards in order to protect employees from injury or illness. This job requires a great deal of research and knowledge in order to properly evaluate the risks associated with a particular workplace.
In order to effectively identify potential hazards, analysts must familiarize themselves with OSHA regulations, industry standards, safety protocols, and other pertinent information. Once identified, the analyst must assess the level of risk posed by each hazard and recommend appropriate measures to mitigate or eliminate the hazard. This may include changes in work practices, use of protective equipment, or installation of safety measures.
The effectiveness of the analystâs recommendations is then measured by the number of workplace accidents and injuries that are prevented. an Occupational Hazard Analyst plays an important role in ensuring the safety of workers and promoting a safe working environment.
Steps How to Become
- Earn a Bachelor's Degree. Individuals interested in becoming an Occupational Hazard Analyst must first earn a bachelor's degree in a field such as occupational health and safety, engineering, or industrial hygiene. During their undergraduate studies, students may take courses in chemistry, physics, mathematics, engineering, and other sciences.
- Obtain Certification. Although certification is not always required, some employers may prefer or require applicants to have the Certified Safety Professional (CSP) credential. To obtain this credential, applicants must pass an exam and have a bachelor's degree with at least four years of safety experience.
- Gain Work Experience. Many employers may require applicants to have at least two to four years of work experience in the safety field before they can become an Occupational Hazard Analyst. Work experience may include inspecting and testing workplace safety equipment, investigating accidents, and writing safety policies and procedures.
- Earn a Master's Degree. Those interested in advancing in the field may consider pursuing a master's degree in occupational health and safety or a related field. During their studies, students may take courses in hazardous materials management, industrial hygiene, and ergonomics.
- Obtain Professional Licensure. Depending on the state in which they work, Occupational Hazard Analysts may need to obtain professional licensure from the states public health department. Requirements for licensure vary by state, but applicants typically must have at least four years of work experience and pass an exam.
Working in the field of Occupational Hazard Analysis requires a combination of education, experience, and skill. To become an ideal and qualified hazard analyst, one must first possess a degree in a relevant field such as occupational safety or health, engineering, or chemistry. Then, they must have relevant experience in job safety analysis, risk assessment, and hazard control.
they must possess strong analytical and problem-solving skills in order to evaluate data, identify risks, and recommend solutions. Finally, they should have a working knowledge of relevant regulations and laws in order to ensure that their analysis is compliant. With these qualifications, a hazard analyst is well-prepared to identify and assess potential risks in the workplace and recommend effective solutions to reduce and mitigate hazards.
You may want to check Occupational Training Specialist, Occupational Health Technician, and Occupational Health and Safety Technician for alternative.
Job Description
- Collect and analyze data related to occupational safety and health, such as hazardous materials and risks associated with specific jobs.
- Identify potential hazards and develop strategies to minimize or eliminate them.
- Develop safety training programs for employees and monitor their implementation.
- Prepare reports and presentations detailing the results of research and analysis.
- Monitor compliance with safety regulations and recommend changes in procedures to ensure compliance.
- Develop and implement strategies to assess risk levels and evaluate the effectiveness of safety measures.
- Investigate accident sites and conduct analyses to determine the cause and potential liability.
- Inspect premises for safety violations and recommend corrective action.
- Keep abreast of new legislation, regulations, and industry standards related to safety.
- Consult with employers to develop safety policies and procedures.
Skills and Competencies to Have
- Knowledge of safety regulations and best practices
- Ability to analyze potential hazards in the workplace
- Strong communication skills
- Proficiency in using computer software for data analysis
- Ability to interpret statistical data
- Problem-solving and critical thinking skills
- Knowledge of industrial hygiene and toxicology
- Ability to identify potential risks and develop strategies to mitigate them
- Knowledge of relevant industry standards and protocols
- Excellent organizational and time management skills
As an Occupational Hazard Analyst, it is important to have a number of skills to be successful. These include strong organizational, research, communication, and analytical skills. Organization is key in order to keep track of all data, reports, and regulations that may need to be consulted when making decisions.
Research skills are also vital in order to find the most up-to-date information on potential hazards and how to mitigate them. Good communication skills are also necessary in order to be able to explain the risks and potential solutions to other parties. Lastly, strong analytical skills are needed in order to assess the risks and come up with the best possible solutions.
Without these skills, an Occupational Hazard Analyst will not be able to effectively identify and evaluate potential risks and provide solutions for those risks.
Occupational Safety Engineer, Occupational Medicine Physician, and Occupational Health and Safety Manager are related jobs you may like.
Frequent Interview Questions
- What experience do you have in assessing and mitigating occupational hazards?
- How would you go about identifying and evaluating potential hazards in a workplace?
- What strategies do you use to ensure compliance with safety regulations?
- How do you stay up-to-date on relevant safety standards and regulations?
- How do you investigate and analyze accident and injury reports?
- How do you develop and implement safety interventions to reduce risks?
- What techniques do you use to create safety awareness among staff and management?
- What strategies do you employ to evaluate the effectiveness of safety protocols?
- How do you manage multiple projects while meeting tight deadlines?
- What strategies do you use to ensure organization-wide safety compliance?
Common Tools in Industry
- Risk Assessment Tool. This tool is used to identify, evaluate, and prioritize risks within a given workplace. (eg: NIST Risk Management Framework)
- Job Hazard Analysis Tool. This tool is used to analyze a job or task to identify hazardous elements and develop safe work practices. (eg: OSHAs Job Hazard Analysis)
- Incident Investigation Tool. This tool is used to analyze the cause and contributing factors of a workplace incident. (eg: OSHA Incident Investigation Form)
- Ergonomics Assessment Tool. This tool is used to assess the physical demands of a job and identify potential ergonomic hazards. (eg: NIOSH Lifting Equation)
- Exposure Monitoring Tool. This tool is used to measure and monitor employee exposure to hazardous substances in the workplace. (eg: Air Quality Monitoring System)
Professional Organizations to Know
- American Society of Safety Professionals (ASSP)
- National Institute for Occupational Safety and Health (NIOSH)
- American Industrial Hygiene Association (AIHA)
- American Association of Safety Engineers (AASE)
- International Safety Equipment Association (ISEA)
- National Fire Protection Association (NFPA)
- International Association of Industrial Accident Boards and Commissions (IAIABC)
- American Society of Safety Managers (ASSM)
- Canadian Society of Safety Engineering (CSSE)
- European Network of Safety & Health Practitioners (ENSHP)
We also have Occupational Therapist Assistant, Occupational Exposure Scientist, and Occupational Psychologist jobs reports.
Common Important Terms
- Risk Management The practice of identifying, assessing, and responding to risks posed by potential events in order to maximize the probability of success.
- Hazard Identification The process of assessing and identifying potential hazards in the workplace.
- Risk Assessment The process of evaluating the likelihood and severity of potential risks associated with a given task or situation.
- Risk Mitigation The process of reducing or eliminating the probability and severity of potential risks through the implementation of preventative measures.
- Control Measures Specific techniques used to reduce or eliminate the likelihood and severity of potential risks, such as engineering controls, administrative controls, and personal protective equipment.
- Occupational Safety and Health Administration (OSHA) A federal agency that oversees the safety and health of workers in the United States.
- Ergonomics The study of how people interact with their environment, including their work environment, in order to improve safety, comfort, and productivity.
- Human Factors The study of how people interact with their environment, including their work environment, in order to improve safety, comfort, and productivity.
Frequently Asked Questions
Q1: What is an Occupational Hazard Analyst? A1: An Occupational Hazard Analyst is a professional who evaluates and assesses potential hazards in the workplace, such as chemical and physical agents, to identify and mitigate potential risks. Q2: What qualifications are needed to become an Occupational Hazard Analyst? A2: To become an Occupational Hazard Analyst, individuals typically need a degree in safety engineering, occupational health and safety, or a related field. Professional certifications may also be required. Q3: What are the key responsibilities of an Occupational Hazard Analyst? A3: The key responsibilities of an Occupational Hazard Analyst include analyzing work areas for potential hazards, identifying sources of danger and recommending solutions to reduce or eliminate risks, and developing safety policies and procedures. Q4: What areas of expertise are necessary for an Occupational Hazard Analyst? A4: An Occupational Hazard Analyst must have knowledge of safety regulations and standards, the ability to interpret data and statistics, and the ability to communicate complex concepts in a clear and concise manner. Q5: What is the average salary of an Occupational Hazard Analyst? A5: The average salary of an Occupational Hazard Analyst ranges from $60,000 to $90,000 per year depending on experience and location.What are jobs related with Occupational Hazard Analyst?
- Occupational Disability Case Manager
- Occupational Health Advisor
- Occupational Environmental Scientist
- Occupational Kinesiologist
- Occupational Physiotherapist
- Occupational Health and Safety Officer
Web Resources
- occupational hazard | Wex | US Law | LII / Legal Information Institute www.law.cornell.edu
- Job Hazard Analysis (JHA) Environmental Health and Safety ehs.ncsu.edu
- Job Hazards Analysis | Environmental Health & Safety www.bu.edu
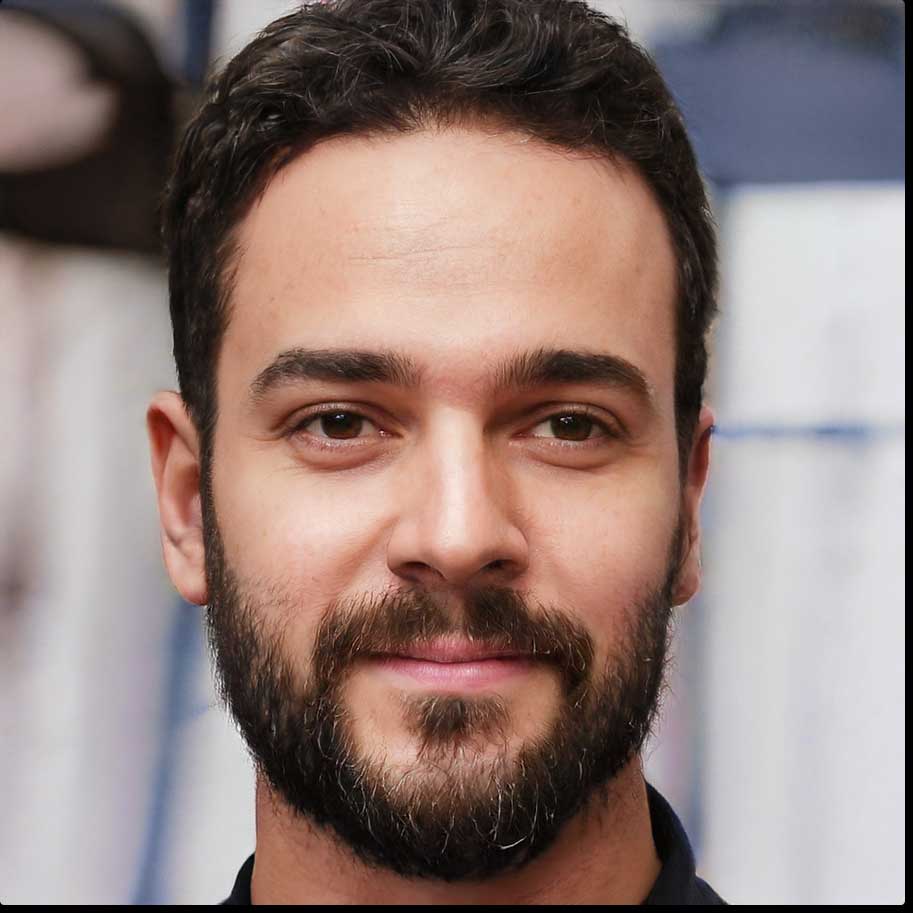