How to Be Occupational Health and Safety Manager - Job Description, Skills, and Interview Questions
Steps How to Become
- Get a Bachelor's Degree. Those wanting to become an occupational health and safety manager should pursue a bachelor's degree in occupational health and safety, or a related field such as engineering, industrial hygiene, or biology.
- Get Relevant Work Experience. After earning a bachelor's degree, individuals should strive to gain relevant work experience in the field. This can be done through internships or volunteer positions.
- Obtain Certification. Certification is often not required for this position, but it can give an individual an advantage when applying for jobs. The Board of Certified Safety Professionals (BCSP) offers a Certified Safety Professional (CSP) certification that can be obtained by taking an exam.
- Apply for Jobs. With the necessary education, work experience, and certifications, individuals can apply for occupational health and safety manager positions. Many employers prefer applicants who have a master's degree in occupational health and safety or related field.
- Advance in the Field. Those who want to advance in the field may choose to pursue a Master of Science in Occupational Health and Safety or earn additional certifications.
You may want to check Occupational Kinesiologist, Occupational Safety Engineer, and Occupational Health Advisor for alternative.
Job Description
- Develop and implement occupational health and safety policies, procedures, and programs.
- Develop and oversee safety training for employees and contractors.
- Monitor the safety of the workplace and investigate any incidents or accidents.
- Establish risk assessment and hazard control methods.
- Monitor compliance with health and safety regulations.
- Prepare reports and presentations on safety performance.
- Provide technical advice and guidance on health and safety matters.
- Maintain employee health records.
- Analyze safety data to identify trends and patterns.
- Liaise with relevant authorities, such as fire departments and local government bodies.
Skills and Competencies to Have
- Knowledge of applicable health, safety and environmental laws, regulations, standards and industry best practices.
- Ability to develop, implement and evaluate health and safety programs.
- Ability to investigate accidents, near misses and other incidents, and to recommend corrective actions.
- Knowledge of industrial hygiene principles and practices.
- Knowledge of ergonomic principles, hazard control techniques and engineering controls.
- Ability to assess workplace safety and health hazards.
- Knowledge of safety management systems, such as hazard identification, risk assessment, and corrective action plans.
- Ability to develop emergency response plans and procedures.
- Ability to develop, implement and evaluate training programs related to health and safety.
- Knowledge of first aid, fire safety and emergency response procedures.
- Ability to develop, implement and evaluate safety incentive programs.
- Excellent communication, interpersonal, problem-solving and organizational skills.
Having a comprehensive understanding of Occupational Health and Safety (OH&S) is essential for any Occupational Health and Safety Manager. This includes having an in-depth knowledge of health and safety regulations, as well as the ability to identify and control hazards in the workplace. Furthermore, an OH&S manager must possess excellent communication skills to be able to effectively share safety information with employees, provide guidance on safety policies, and ensure that all staff are aware of their legal obligations.
they must have strong problem-solving skills in order to identify potential risks and develop appropriate safety measures. Finally, they must be proactive and constantly seek out ways to improve the workplace environment, while being prepared to respond quickly to any emergency situations. All of these skills combined create a professional who can ensure that all employees are safe and secure in their workplace.
Occupational Psychologist, Occupational Health and Safety Officer, and Occupational Training Specialist are related jobs you may like.
Frequent Interview Questions
- What experience do you have in managing an occupational health and safety program?
- How do you keep up with changes in health and safety legislation?
- What steps do you take to ensure that the work environment is safe for employees?
- How do you identify, assess and control workplace hazards?
- What methods do you use to train and educate employees about health and safety issues?
- How do you investigate accidents and incidents to determine root causes?
- What strategies do you use to motivate employees to comply with health and safety regulations?
- How would you handle a situation where an employee is non-compliant with health and safety standards?
- What proactive measures do you take to reduce the risk of accidents in the workplace?
- How do you ensure that safety equipment is properly maintained and inspected?
Common Tools in Industry
- Risk Assessment Tool. An analysis tool used to identify potential hazards and determine the level of risk associated with them (e. g. Job Safety Analysis).
- Incident Reporting System. A system used to track and investigate any occupational health and safety incidents that occur in the workplace (e. g. Near Miss Reporting System).
- Safety Training Program. A program designed to teach employees how to work safely in the workplace (e. g. Hazard Communication Training).
- Personal Protective Equipment (PPE). Clothing and equipment designed to protect workers from injury or illness (e. g. Hard Hats, Safety Goggles).
- Emergency Response Plan. A plan outlining the steps to be taken in the event of an emergency occurring in the workplace (e. g. Fire Evacuation Plan).
- Compliance Monitoring System. A system used to ensure compliance with all applicable laws and regulations (e. g. Regulatory Auditing).
- Hazard Communication Program. A program designed to ensure employees are aware of any potential hazards in their environment (e. g. Material Safety Data Sheets).
- Ergonomic Evaluation. An assessment of the workplace environment to identify potential risk factors for musculoskeletal disorders (e. g. Posture and Workstation Evaluation).
Professional Organizations to Know
- American Society of Safety Professionals
- National Safety Council
- American Industrial Hygiene Association
- American Association of Occupational Health Nurses
- National Institute for Occupational Safety and Health
- Canadian Society of Safety Engineering
- International Labour Organization
- International Association of Industrial Accident Boards and Commissions
- International Commission on Occupational Health
- European Agency for Safety and Health at Work
We also have Occupational Physiotherapist, Occupational Therapist Assistant, and Occupational Environmental Scientist jobs reports.
Common Important Terms
- Risk Assessment. The process of identifying hazards and assessing the risks associated with them in order to reduce the likelihood of an incident or accident occurring.
- Hazard Identification. The process of recognizing situations that could create a risk of harm to people, property, or the environment.
- Incident Investigation. A process of collecting information about an incident to determine its cause and to prevent similar incidents from occurring in the future.
- Accident Prevention. A system of processes and procedures designed to prevent accidents from occurring in the workplace.
- Emergency Response Planning. The process of developing plans, procedures, and strategies for responding quickly and effectively to potential emergencies or disasters.
- Workplace Safety Training. Instruction provided to employees to ensure they understand the risks associated with their job and how to work safely and avoid injury.
- Ergonomics. The study of how people interact with their environment and how design, tools, and equipment can be used to minimize the risk of injury or illness.
- Health Surveillance. A system of monitoring workers to ensure they are not exposed to hazardous substances or situations that could lead to ill health.
- Occupational Hygiene. The practice of controlling workplace hazards and maintaining the health of workers by monitoring the environment they work in and identifying any potential risks.
- Personal Protective Equipment (PPE). Clothing and equipment used to protect workers from potential hazardous conditions such as extreme temperatures, sharp objects, hazardous chemicals, or dust.
Frequently Asked Questions
What qualifications are required to become an Occupational Health and Safety Manager?
Typically, an Occupational Health and Safety Manager must possess at least a bachelor's degree in occupational health and safety, safety management, or a related field. They may also need to have professional certifications such as Certified Safety Professional (CSP) or Associate Safety Professional (ASP).
What duties does an Occupational Health and Safety Manager typically perform?
The primary duties of an Occupational Health and Safety Manager are to develop, implement and monitor health and safety policies, procedures and programs to ensure a safe work environment for employees. They also conduct risk assessments, ensure compliance with health and safety regulations, and inspect work areas for potential hazards.
What is the average salary of an Occupational Health and Safety Manager?
According to the Bureau of Labor Statistics (BLS), the median annual salary for Occupational Health and Safety Managers in the United States was $100,310 in 2019.
What type of work environment do Occupational Health and Safety Managers work in?
Occupational Health and Safety Managers typically work in an office setting, but may also be required to visit worksites to inspect for hazards or to provide safety training.
How long does it usually take to become an Occupational Health and Safety Manager?
The amount of time it takes to become an Occupational Health and Safety Manager depends on the individual's educational background and experience. Generally, it can take anywhere from two to five years of experience in the field before one can become a Manager.
What are jobs related with Occupational Health and Safety Manager?
- Occupational Hazard Analyst
- Occupational Medicine Physician
- Occupational Health and Safety Technician
- Occupational Safety Inspector
- Occupational Disability Case Manager
- Occupational Exposure Scientist
Web Resources
- Occupational Health and Safety (OHS) Manager online-distance.ncsu.edu
- Occupational Health and Safety | UC Davis Continuing and ¦ extension.ucdavis.edu
- Occupational Safety Management - EmbryRiddle Aeronautical ¦ erau.edu
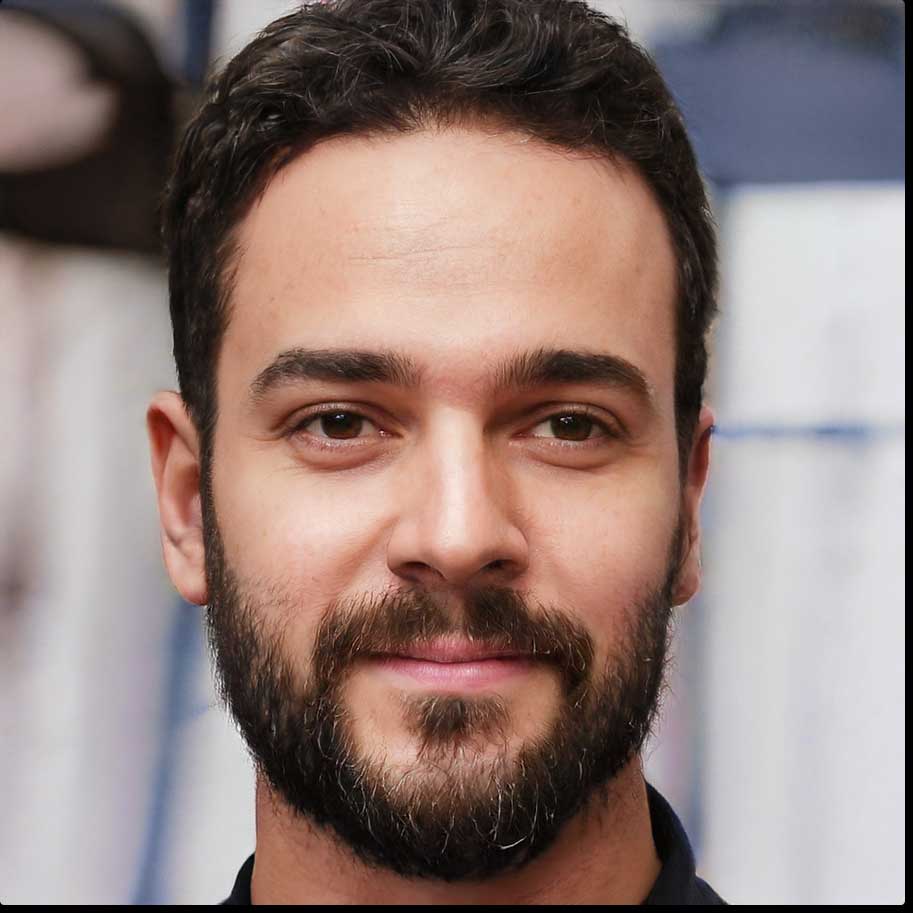