How to Be Field Service Engineer - Job Description, Skills, and Interview Questions
Steps How to Become
- Obtain a high school diploma or equivalent. Field service engineers usually need at least a high school diploma or the equivalent to enter the field.
- Earn a bachelors degree in engineering. Although a high school diploma may be enough to start out in the field, most employers prefer to hire field service engineers with a bachelors degree in engineering.
- Obtain relevant experience. Field service engineers typically need to have experience working with the equipment they will be servicing. A great way to gain this experience is to complete an internship while in college, or to volunteer with a local engineering organization.
- Join professional organizations. Joining professional organizations is a great way to stay up-to-date with the latest developments in the field and to network with other professionals.
- Take certification courses. Many companies require their field service engineers to be certified in specific areas, such as safety, equipment repair, and customer service. Taking certification courses can help you meet these requirements.
- Apply for jobs as a field service engineer. After gaining experience and certifications, you can begin applying for jobs as a field service engineer. You may also want to consider applying for internships or apprenticeships to gain more experience in the field.
The key to being an ideal and capable Field Service Engineer is having the right combination of technical knowledge, problem-solving skills, and customer service expertise. Having the right technical knowledge is essential in order to accurately diagnose and troubleshoot any issues that may arise. Problem-solving skills are also important as they allow the engineer to quickly identify and solve problems with minimal disruption to the customer.
Finally, customer service expertise is an invaluable asset in the field service engineer role, as it allows the engineer to effectively communicate with customers and provide a satisfactory resolution to any issues. All of these components together make for a successful and capable Field Service Engineer.
You may want to check Service Engineer, Security Services Supervisor, and IT Service Desk Analyst for alternative.
Job Description
- Diagnose and repair mechanical, electrical, and software issues with customer equipment.
- Troubleshoot problems and recommend solutions to customers.
- Install and configure equipment and software according to customer specifications.
- Provide onsite training and instruction to customers on the use of their equipment.
- Maintain accurate records of service calls and repairs completed.
- Coordinate with vendors to ensure timely delivery of required parts and supplies.
- Ensure compliance with safety regulations.
- Develop and maintain positive customer relationships.
- Participate in continuing education opportunities to stay current on industry trends and best practices.
- Develop preventative maintenance plans to extend the life of customer equipment.
Skills and Competencies to Have
- Excellent communication skills
- Analytical and problem-solving skills
- Technical aptitude and understanding of engineering principles
- Ability to read blueprints and schematics
- Ability to troubleshoot and diagnose malfunctions
- Ability to operate electronic test equipment
- Proficiency in using hand and power tools
- Ability to lift heavy objects
- Attention to detail
- Time management and organizational skills
- Knowledge of safety regulations and procedures
- Knowledge of industry standards and regulations
Field service engineers play a vital role in keeping machines and other equipment running smoothly, and the most important skill they must have is problem-solving. They must be able to identify a problem quickly and accurately, then diagnose the cause and develop an effective solution. Good communication skills are also essential, as field service engineers must be able to explain complex technical issues to customers in a way that is clear and easy to understand.
With the ability to clearly communicate, they can then go on to provide thorough instructions for repairs and maintenance. field service engineers must be well-versed in the latest technology and be able to quickly learn new systems and equipment. By having these skills, they can ensure that customers receive the most up-to-date advice and solutions.
Service Project Manager, Aviation Service Technician, and Service Desk Analyst are related jobs you may like.
Frequent Interview Questions
- What experience do you have in field service engineering?
- What challenges have you faced in the past as a field service engineer?
- How do you stay up to date on new technologies in the industry?
- Describe a time when you had to troubleshoot a complex issue in the field.
- Describe a time when you successfully collaborated with others to complete a project in the field.
- How do you respond to customer complaints and feedback?
- How do you ensure customer satisfaction in your work?
- How do you stay organized and prioritize tasks while working in the field?
- Describe a time when you successfully identified and resolved a problem using your technical skills.
- How do you ensure safety and compliance with industry regulations while working onsite?
Common Tools in Industry
- Computer. A machine that can perform calculations and other tasks, (eg: laptop, desktop).
- Multimeter. An instrument used to measure electrical properties such as voltage, current and resistance, (eg: Fluke Multimeter).
- Pneumatic Tools. Tools powered by compressed air, (eg: impact wrench).
- Soldering Iron. A tool used to join materials by melting and putting a filler metal into the joint, (eg: Weller Soldering Iron).
- Oscilloscope. An instrument used to measure and analyze the waveforms of electronic signals, (eg: Tektronix Oscilloscope).
- Hand Tools. Manual tools used for various tasks such as cutting, drilling and fastening, (eg: screwdriver, wrench, pliers).
- Diagnostic Software. Applications used to diagnose and troubleshoot computer hardware and software problems, (eg: Microsoft Diagnostic Toolkit).
- Networking Equipment. Equipment used for connecting computers and other devices in a local area network, (eg: routers, switches).
- Test Equipment. Hardware and software used to test electronic components and systems, (eg: logic analyzer, spectrum analyzer).
- Power Supplies. Devices used to convert electrical current from one form to another, (eg: AC-DC power supply).
Professional Organizations to Know
- American Society of Mechanical Engineers (ASME)
- American Institute of Chemical Engineers (AIChE)
- Institute of Electrical and Electronics Engineers (IEEE)
- Association for Manufacturing Technology (AMT)
- Society of Automotive Engineers (SAE)
- International Society of Automation (ISA)
- International Association of Field Service Technicians (IAFST)
- American Society for Quality (ASQ)
- National Society of Professional Engineers (NSPE)
- Field Service Professionals Network (FSPN)
We also have Food Service Manager, Service Delivery Lead, and Facilities Service Supervisor jobs reports.
Common Important Terms
- Maintenance Engineer. A maintenance engineer is responsible for the upkeep and repair of equipment, machines, and buildings in an industrial setting.
- Calibration. The process of adjusting a device to meet a specified set of accuracy requirements.
- Troubleshooting. The process of identifying and resolving issues with equipment or systems.
- Diagnostics. The process of identifying and analyzing the root cause of an issue.
- Commissioning. The process of testing and verifying the operation of a system before it is put into use.
- HVAC. Heating, ventilation, and air conditioning (HVAC) systems are used to control the climate within a building or facility.
- Systems Engineering. The process of designing, developing, and maintaining complex systems.
- Robotics. The branch of engineering that deals with the design, construction, and operation of robots.
- Automation. The use of technology to automate tasks that would otherwise be done manually.
- Networking. The process of connecting multiple devices and systems to each other in order to share data and information.
Frequently Asked Questions
What is a Field Service Engineer?
A Field Service Engineer is a professional who repairs, maintains, and installs complex industrial equipment and systems.
What qualifications do Field Service Engineers need?
Field Service Engineers typically need a degree in engineering or related field, and experience in mechanical, electrical, and electronics engineering.
What type of tasks do Field Service Engineers perform?
Field Service Engineers typically perform tasks such as troubleshooting and diagnosing malfunctions, repairing and replacing components, and providing technical support.
What tools do Field Service Engineers use?
Field Service Engineers use tools such as hand tools, power tools, diagnostic equipment, computers, and control systems.
What are the working conditions for Field Service Engineers?
Field Service Engineers often travel to various job sites and may work long hours in hazardous or uncomfortable conditions.
What are jobs related with Field Service Engineer?
Web Resources
- Field Service Engineer Career and Professional Development ¦ cpd.cau.edu
- Field Service/Start-Up Engineer Career and Professional ¦ cpdcenter.famu.edu
- Field Service/Start-Up Engineer Career Services | Fort Lewis ¦ careers.fortlewis.edu
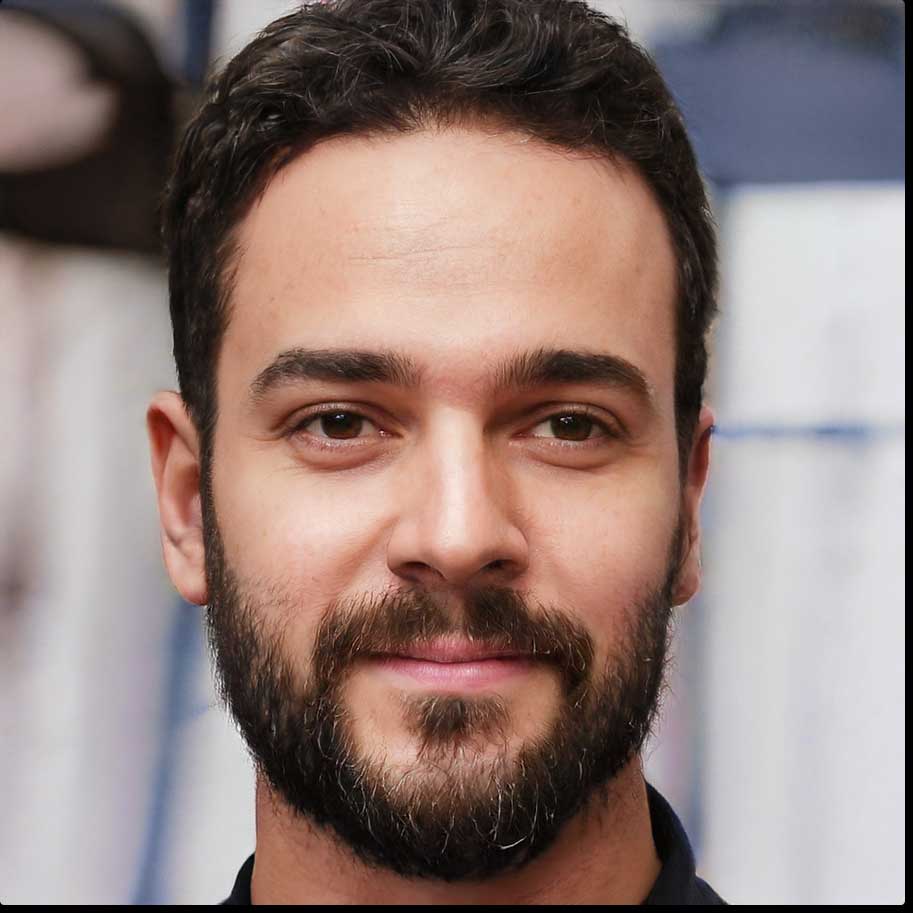