How to Be Service Engineer - Job Description, Skills, and Interview Questions
The lack of proper service engineer leads to multiple detrimental effects. Without a service engineer, the equipment and machinery may not be properly maintained, and can suffer from wear and tear due to lack of maintenance. This can lead to unexpected breakdowns, resulting in costly repairs and downtime.
Furthermore, the lack of a service engineer may lead to safety issues, as the machinery may not be inspected for potential hazards, leading to potential accidents in the workplace. Therefore, it is essential to have a qualified service engineer to guarantee the safety and performance of any equipment or machinery.
Steps How to Become
- Obtain a High School Diploma or GED. Most employers require a high school diploma or equivalent degree before considering applicants for service engineering positions.
- Pursue a Degree in Engineering. Most service engineer positions require applicants to have at least an associate's degree in engineering, typically in electrical engineering or mechanical engineering.
- Consider Certification. Obtaining certification as a service engineer can help to demonstrate one's knowledge and expertise in the field and can lead to more job opportunities and higher salaries.
- Gain Relevant Work Experience. Many employers prefer that service engineers have some prior experience in the field. Working as an intern or an apprentice can provide important work experience and insight into the profession.
- Stay Up-to-Date on Technology. Service engineers must always stay up-to-date on the latest technology and industry trends in order to provide the best service possible to customers. Taking additional classes or reading industry publications can help keep one informed of the latest developments in the field.
Being a Service Engineer, it is important to stay updated and qualified. This can be achieved through continuous learning and training, so that one can stay abreast with the latest technology and industry trends. Regularly attending seminars and conferences can provide exposure to new ideas and techniques, which can be applied in the professional world.
obtaining certifications and other qualifications can be helpful in maintaining a high level of competency. Finally, networking with peers and colleagues can help to share knowledge and expertise, which can result in improved performance and greater success.
You may want to check Aviation Service Technician, Technical Service Representative, and Food Service Manager for alternative.
Job Description
- Install and repair a range of electrical and mechanical equipment, including pumps, motors, generators and other systems
- Troubleshoot and diagnose technical problems
- Perform preventive maintenance and repairs on equipment
- Read and interpret technical manuals, schematics, and wiring diagrams
- Prepare service reports, work orders, and other documents
- Respond to customer inquiries and provide customer service
- Maintain records of parts inventory and service calls
- Follow safety guidelines and regulations
- Monitor and adjust system parameters to maintain optimal performance
- Test and calibrate systems to ensure proper functioning
Skills and Competencies to Have
- Technical knowledge: Ability to diagnose, troubleshoot and repair a wide range of technical problems related to the service engineers area of expertise.
- Communication skills: Ability to clearly explain technical concepts to customers in a way they can understand.
- Problem-solving skills: Ability to identify problems quickly and develop creative solutions.
- Interpersonal skills: Ability to work well with customers and other service engineers.
- Organizational skills: Ability to manage multiple tasks, prioritize tasks, and keep accurate records of all service activities.
- Computer skills: Knowledge of computer hardware and software, as well as maintenance and repair standards.
- Electrical and/or mechanical aptitude: Understanding of electrical and/or mechanical concepts and principles as they relate to the service engineers area of expertise.
- Safety protocols: Familiarity with safety protocols for working with hazardous materials, equipment, and tools.
- Attention to detail: Ability to detect small problems or discrepancies and correct them.
- Time management: Capacity to complete assignments on time and meet deadlines.
Having a strong technical ability is a key skill for a Service Engineer. Having a good understanding of the specific service systems and components, as well as how they work together, enables them to identify and solve issues quickly and efficiently. Being able to troubleshoot and think logically can help them diagnose a problem and come up with a solution quickly.
they must possess good communication and interpersonal skills to effectively communicate with customers and other service personnel. Being organized and detail-oriented is also necessary, as they must keep accurate records of all service activities and repairs. A Service Engineer must also be able to work independently and in a team environment to ensure the best outcome for their customers and the business.
Finally, having excellent problem-solving skills will enable them to understand customer needs and develop effective solutions to meet those needs.
Security Services Supervisor, Field Service Engineer, and Service Delivery Lead are related jobs you may like.
Frequent Interview Questions
- What experience do you have working as a service engineer?
- Describe a challenging service engineering project you have completed.
- How do you stay up to date with the latest technologies and trends in service engineering?
- How do you troubleshoot complex technical problems?
- What customer service techniques do you use when dealing with clients?
- How do you handle difficult customer requests or complaints?
- What methods do you use to ensure customer satisfaction?
- What do you consider to be the key responsibilities of a service engineer?
- What safety protocols do you implement when servicing equipment?
- How do you ensure that all service requirements are met?
Common Tools in Industry
- Screwdriver. A hand tool used to drive screws and fasteners. (eg: Phillips head screwdriver)
- Wrench. A tool used to hold and turn nuts, bolts, and other objects. (eg: adjustable wrench)
- Hammer. A hand tool used to drive nails, break objects, and shape materials. (eg: claw hammer)
- Pliers. A tool used to hold, grip, and bend objects. (eg: slip-joint pliers)
- Socket Set. A set of sockets used to loosen and tighten nuts, bolts, and other objects. (eg: Deep Socket Set)
- Ratchet Set. A set of ratchets used to provide leverage in tightening and loosening fasteners. (eg: 3/8-inch ratchet set)
- Drill. A power tool used to make holes in materials. (eg: cordless drill)
- Allen Wrench. A hexagonal tool used for turning screws with a hexagonal socket head. (eg: metric allen wrench set)
- Soldering Iron. A tool used to join metal parts together with heat and solder. (eg: electric soldering iron)
- Multimeter. An electronic device used to measure voltage, current, and resistance. (eg: digital multimeter)
Professional Organizations to Know
- American Society of Mechanical Engineers (ASME)
- Institute of Electrical and Electronics Engineers (IEEE)
- Society for Automotive Engineers (SAE)
- Association for the Advancement of Artificial Intelligence (AAAI)
- International Society of Automation (ISA)
- Robotics Industry Association (RIA)
- International Institute of Refrigeration (IIR)
- International Council on Systems Engineering (INCOSE)
- Society of Manufacturing Engineers (SME)
- American Welding Society (AWS)
We also have Automotive Service Technician, IT Service Desk Analyst, and Facilities Service Supervisor jobs reports.
Common Important Terms
- HVAC. Heating, Ventilation, and Air Conditioning. The technology of controlling the temperature, humidity, and air quality of a space.
- Mechanical Engineering. The application of engineering principles to the design, analysis, and construction of mechanical systems.
- Electrical Engineering. The application of engineering principles to the design, analysis, and construction of electrical systems.
- Plumbing. The installation and maintenance of pipes, fixtures, and other plumbing components used to carry water or other liquids.
- Refrigeration. The process of cooling air or other substances below their normal temperatures.
- Solar Energy. Capturing and converting energy from the sun into usable forms of energy such as electricity or heat.
- Heat Exchanger. A device used to transfer heat from one fluid to another.
- Pumps. Devices used to move fluids from one place to another.
- Motors. Machine components that convert electrical energy into mechanical energy.
Frequently Asked Questions
What is the typical job description of a Service Engineer?
A Service Engineer typically performs maintenance and repairs on a variety of mechanical and electronic equipment, as well as diagnosing problems, testing and replacing parts, and ensuring equipment is running properly.
What kind of skills are necessary to be a successful Service Engineer?
Successful Service Engineers must have strong technical knowledge and problem-solving skills, as well as the ability to read and interpret technical diagrams. They should also have excellent communication skills, in order to effectively communicate with customers and other stakeholders.
What type of qualifications do Service Engineers need?
Most employers require Service Engineers to have at least a high school diploma or equivalent. Additionally, some employers may also require a degree in engineering or a related field.
What is the average salary for a Service Engineer?
According to PayScale, the average salary for a Service Engineer is $55,000 per year.
How many hours do Service Engineers typically work?
Service Engineers typically work 40 hours per week, although they may be required to work additional hours depending on the situation.
What are jobs related with Service Engineer?
Web Resources
- Cal Poly - Details - Building Service Engineer jobs.calpoly.edu
- Engineering Service Learning | School of Engineering engineeringservicelearning.ucmerced.edu
- Details - Building Service Engineer | Job Opportunities | SDSU careers.sdsu.edu
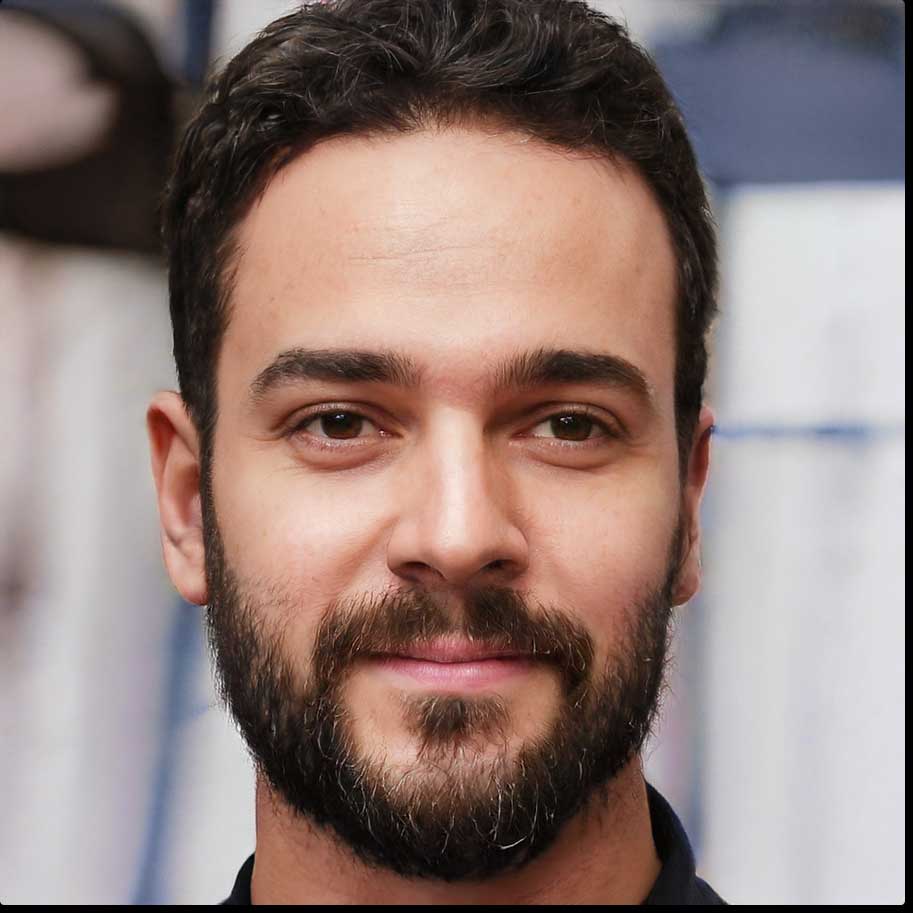