How to Be Occupational Health and Safety Officer - Job Description, Skills, and Interview Questions
The Occupational Health and Safety Officer is an important role in any workplace, as they are responsible for ensuring the safety of employees. They work to identify, assess, and analyze potential risks, and then implement preventative measures to reduce the chances of accidents or injury. This, in turn, can lead to improved morale, increased productivity and a safe working environment for all.
The Officer also has the responsibility of training staff in safety procedures, helping to create an awareness of potential risks, and monitoring safety compliance. An effective Occupational Health and Safety Officer is essential for the health, safety and wellbeing of a businessâs employees.
Steps How to Become
- Obtain a Bachelor's Degree. Most employers require Occupational Health and Safety Officers to have a minimum of a bachelor's degree in occupational health, safety, or a related field. It is important to find a school that offers an accredited program.
- Obtain an Internship. Many employers prefer to hire candidates who have some type of practical experience. An internship in the field of occupational health and safety is a great way to gain experience and make valuable connections.
- Obtain Certification. Certification is not required for all positions, but it can increase chances for employment. The Board of Certified Safety Professionals offers the Certified Safety Professional (CSP) certification.
- Consider Pursuing Advanced Degrees. Those who want to pursue more advanced positions may consider earning a master's degree or doctorate in the field of occupational health and safety.
- Stay Current with Regulations. It is important for Occupational Health and Safety Officers to stay up-to-date on all regulations related to occupational health and safety. This requires constant learning and research.
The role of an Occupational Health and Safety Officer is essential in ensuring the safety of employees in the workplace. When an Occupational Health and Safety Officer is reliable and capable, it can lead to improved employee morale, increased productivity and reduced workplace risks. Reliable and capable officers are able to identify potential hazards, develop safety plans and protocols, provide safety training, and ensure that safety policies are followed.
They also have the ability to communicate effectively with staff, evaluate workplace conditions, and conduct investigations into workplace incidents. The presence of a reliable and capable Occupational Health and Safety Officer can create a culture of safety in the workplace which can have a positive effect on overall employee well-being and work performance.
You may want to check Occupational Psychologist, Occupational Health and Safety Technician, and Occupational Therapist Assistant for alternative.
Job Description
- Develop and implement health and safety plans and procedures in accordance with organizational policies and government regulations.
- Monitor workplace activities to ensure compliance with health and safety standards and regulations.
- Investigate workplace incidents and accidents to identify causes and implement preventive measures.
- Inspect workplaces, equipment, and processes to identify potential safety hazards.
- Educate employees on health and safety issues through training sessions, seminars, and meetings.
- Develop emergency preparedness and response plans in case of accidents or hazardous situations.
- Prepare reports on health and safety issues such as inspections, incidents, and corrective actions taken.
- Keep up-to-date with industry changes and developments in health and safety legislation.
- Participate in risk assessments and hazard identification procedures.
- Develop safety management systems to ensure compliance with applicable laws and regulations.
Skills and Competencies to Have
- Knowledge of occupational health and safety regulations, standards and best practices
- Excellent communication and interpersonal skills
- Ability to identify, evaluate and control workplace hazards
- Ability to conduct workplace inspections and assessments
- Experience in writing detailed reports
- Knowledge of emergency response procedures
- Ability to develop, implement and monitor safety programs
- Proficiency in data analysis and problem solving
- Ability to facilitate safety training programs
- Understanding of industrial hygiene principles and practices
Having a strong knowledge of occupational health and safety regulations is essential for any occupational health and safety officer. Without understanding the health and safety laws, an occupational health and safety officer cannot effectively protect employees from harm while they are on the job. Knowing the safety guidelines helps the officer recognize potential dangers in the workplace and take action to reduce the risk of an accident or injury.
This knowledge is essential for ensuring the well-being of employees, which is the main focus of an occupational health and safety officer. effective communication skills are necessary because the officer must be able to effectively convey information to employees and explain why certain protocols are being put in place. The ability to work closely with all levels of management is also important for any occupational health and safety officer.
They must be able to lead by example and ensure that all safety policies are implemented correctly. Finally, problem-solving skills are a must for any occupational health and safety officer because they must be able to analyze data and come up with solutions that will help keep employees safe. With the right skills, an occupational health and safety officer can help create a safe work environment for everyone.
Occupational Medicine Physician, Occupational Kinesiologist, and Occupational Safety Inspector are related jobs you may like.
Frequent Interview Questions
- What experience do you have in the field of occupational health and safety?
- How would you go about creating an effective health and safety policy?
- What strategies have you used to motivate employees to comply with safety regulations?
- What techniques do you use to communicate safety issues to a diverse workforce?
- What safety programs have you developed or implemented in the past?
- How do you stay up-to-date on changes to safety regulations?
- How do you handle conflicts between safety directives and business needs?
- How do you investigate accidents and implement corrective measures?
- What challenges have you faced in maintaining a safe work environment?
- How would you handle a situation where an employee refuses to abide by safety standards?
Common Tools in Industry
- Risk Assessment Tool. This tool is designed to identify potential hazards in the workplace and to assess the associated risks. (Eg: Job Safety Analysis)
- Hazard Identification Tool. This tool is used to identify potential hazards in the workplace, such as chemical exposure, physical hazards, or ergonomic risks. (Eg: Job Hazard Analysis)
- Training Tool. This tool is used to provide education and training to employees on health and safety topics. (Eg: Online Safety Training Videos)
- Incident Investigation Tool. This tool is used to investigate incidents that have occurred in the workplace and to determine their root causes. (Eg: Accident Investigation Report)
- Emergency Preparedness Tool. This tool is used to develop emergency plans and procedures for dealing with potential workplace emergencies. (Eg: Emergency Action Plan)
- Compliance Monitoring Tool. This tool is used to monitor employee compliance with safety regulations and policies. (Eg: Compliance Checklist)
Professional Organizations to Know
- American Society of Safety Professionals (ASSP)
- National Safety Council (NSC)
- American Industrial Hygiene Association (AIHA)
- Institute of Safety and Health Management (ISHM)
- Canadian Society of Safety Engineering (CSSE)
- International Institute of Risk and Safety Management (IIRSM)
- International Labour Organization (ILO)
- Institute of Occupational Safety and Health (IOSH)
- Health and Safety Executive (HSE)
- National Institute for Occupational Safety and Health (NIOSH)
We also have Occupational Health Technician, Occupational Hazard Analyst, and Occupational Environmental Scientist jobs reports.
Common Important Terms
- Risk Management - The process of identifying, assessing and controlling potential hazards, risks and losses in the workplace.
- Health and Safety Legislation - Laws and regulations that govern the health and safety of workers in the workplace.
- Accident Investigation - The process of identifying the cause of an accident and making recommendations to prevent similar incidents in the future.
- Hazard Identification - The process of identifying potential hazards in the workplace that could cause ill health or injury to workers.
- Incident Reporting - The process of recording and reporting all incidents, injuries and illnesses in the workplace.
- Safety Audits - Evaluations of a workplace to identify any existing or potential safety and health hazards.
- Emergency Preparedness - Preparation for unexpected or potentially dangerous events in the workplace.
- Training and Education - The process of ensuring workers are informed about safety regulations and procedures in the workplace.
Frequently Asked Questions
Q1: What is the primary role of an Occupational Health and Safety Officer? A1: The primary role of an Occupational Health and Safety Officer is to ensure safety compliance in the workplace by developing and implementing safety policies, conducting safety inspections, monitoring hazardous conditions, and providing training and education on safety topics. Q2: What qualifications are required to become an Occupational Health and Safety Officer? A2: Generally, an Occupational Health and Safety Officer must have a bachelor's degree in occupational health and safety, industrial hygiene, or a related field such as engineering, chemistry, or biology. In addition, certification from a recognized safety organization such as the Board of Certified Safety Professionals is usually required. Q3: What duties are typically performed by an Occupational Health and Safety Officer? A3: Typical duties of an Occupational Health and Safety Officer include developing safety plans, inspecting the workplace for hazardous conditions, monitoring safety performance, investigating workplace accidents and incidents, conducting safety training, and providing input on safety-related legislation. Q4: How often are Occupational Health and Safety Officers required to inspect the workplace for hazardous conditions? A4: Depending on the nature of the business, Occupational Health and Safety Officers are typically required to conduct regular inspections of the workplace for hazardous conditions. This could range from weekly or monthly inspections to daily inspections depending on the type of work being performed. Q5: What types of safety measures do Occupational Health and Safety Officers typically recommend to employers? A5: Occupational Health and Safety Officers typically recommend a wide range of safety measures to employers in order to minimize risks and ensure compliance with safety regulations. This could include the use of personal protective equipment, implementing safe work practices, providing adequate training and instruction on safe work procedures, maintaining up-to-date records of hazardous materials used in the workplace, and creating a culture of safety within the organization.What are jobs related with Occupational Health and Safety Officer?
- Occupational Health Advisor
- Occupational Training Specialist
- Occupational Disability Case Manager
- Occupational Physiotherapist
- Occupational Exposure Scientist
- Occupational Safety Engineer
Web Resources
- Occupational Health and Safety Programs and Services ehs.osu.edu
- Occupational Health & Safety - Occupational Health & Safety www.monash.edu
- Occupational Health and Safety Courses - College SA www.collegesa.edu.za
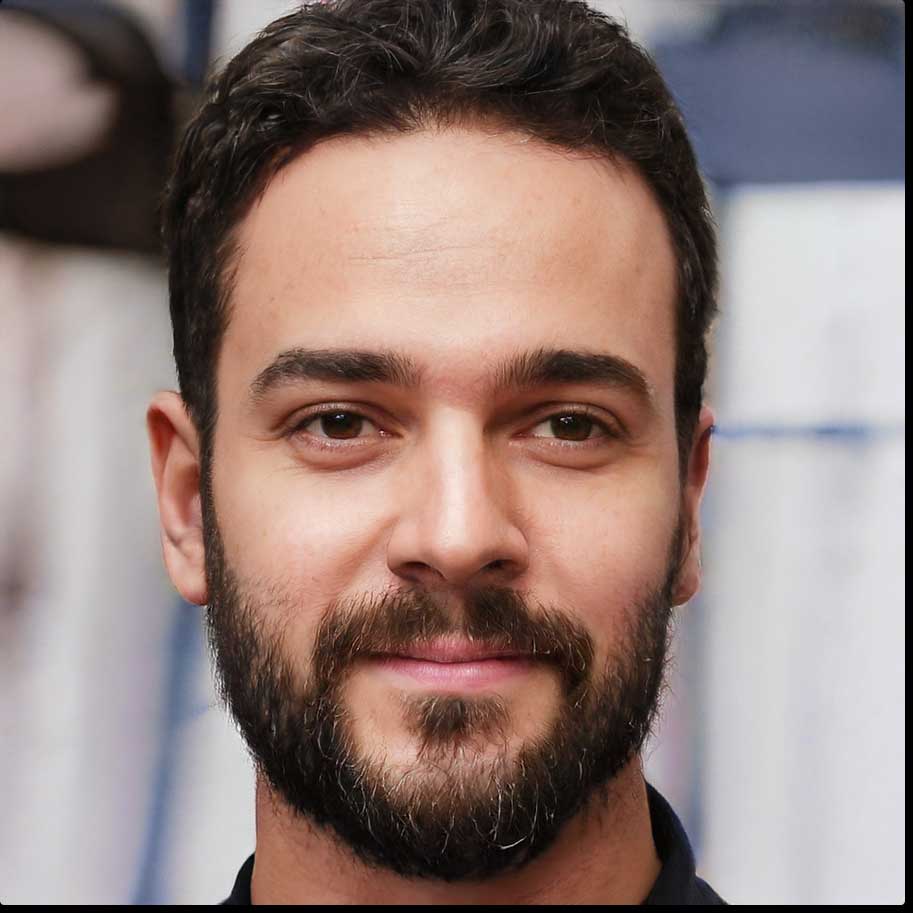