How to Be Occupational Health Technician - Job Description, Skills, and Interview Questions
When an individual is exposed to certain occupational hazards, it can cause health problems such as respiratory illnesses, occupational illnesses, and skin diseases. It is the responsibility of an Occupational Health Technician to identify potential hazards in the workplace and take steps to address them. This includes evaluating the health of employees, conducting safety inspections, and providing education on proper safety practices.
they can provide medical treatment and rehabilitation services, as well as advice on how to reduce or eliminate workplace hazards. By doing so, Occupational Health Technicians help to ensure that employees are safe and healthy while they work, reducing the risk of health problems and helping to create a productive work environment.
Steps How to Become
- Earn a High School Diploma or GED. Most employers require applicants to have at least a high school diploma or GED before they will consider hiring them as an occupational health technician.
- Complete a Post-Secondary Training Program. The majority of employers prefer to hire technicians who have completed a post-secondary training program in occupational health technology. Programs typically last two to four years and cover topics such as safety, first aid, hazardous materials, chemical safety, and ergonomics.
- Obtain Certification. It is recommended that occupational health technicians become certified in their field. Certification is available through the American Board of Industrial Hygiene (ABIH) or the National Institute for Occupational Safety and Health (NIOSH).
- Obtain Work Experience. Many employers prefer to hire technicians who have some previous work experience in the field. It is possible to gain this experience through internships or volunteer work.
- Obtain Licensure. Some states require occupational health technicians to be licensed in order to practice. Licensure requirements vary by state but may include passing an exam and completing continuing education courses.
Being a reliable Occupational Health Technician requires having a broad knowledge base, a well-developed skill set, and an eagerness to learn. It is essential to understand the health and safety risks associated with the workplace, as well as the regulations set by the Occupational Safety and Health Administration (OSHA). By having a deep understanding of these topics, a technician can properly and effectively identify potential hazards, develop safety protocols, and provide guidance to employees.
strong analytical and problem-solving skills are needed in order to quickly diagnose and address any health or safety issues. Finally, having a commitment to ongoing learning and education is essential in order to stay up to date on the latest safety regulations and procedures. All of these qualities together make an Occupational Health Technician reliable and capable.
You may want to check Occupational Health and Safety Manager, Occupational Safety Inspector, and Occupational Therapist Assistant for alternative.
Job Description
- Develop and implement health and safety policies.
- Monitor workplace environment and equipment to ensure compliance with health and safety regulations.
- Train employees on health and safety procedures, such as proper lifting techniques and proper use of safety equipment.
- Inspect workplace for potential safety hazards.
- Maintain accurate records of safety inspections and training sessions.
- Investigate workplace accidents and recommend corrective action.
- Provide first aid and emergency response when needed.
- Perform periodic fitness-for-duty evaluations for employees.
- Monitor employee exposure to hazardous materials and provide medical surveillance for workers at risk of occupational illnesses.
- Monitor immunization programs for employees who work in healthcare industries.
- Manage workers compensation claims and coordinate return-to-work programs for injured employees.
- Educate employers and employees about workplace health and safety issues.
- Consult with management and human resources staff on health and safety issues.
- Develop and implement ergonomic programs to reduce the risk of workplace injuries.
Skills and Competencies to Have
- Knowledge of safety and health regulations
- Knowledge of medical terminology
- Ability to recognize potential health hazards
- Knowledge of medical equipment and its use
- Ability to maintain accurate records and reports
- Basic computer skills
- Excellent communication skills
- Ability to assess workers for health risks
- Ability to perform physical exams
- Knowledge of testing and diagnostic methods
- Ability to provide first aid and emergency treatment
- Knowledge of hazardous materials and their effects on health
- Ability to explain health risks to workers
- Ability to develop safety programs and procedures
- Ability to work with a multidisciplinary team
- Ability to work with diverse cultures
- Ability to recognize signs and symptoms of illness or injury
- Knowledge of ergonomics and job hazard analysis
The ability to communicate effectively and empathize with patients is a key skill for an Occupational Health Technician. Effective communication is essential in order to build trust and understanding between the technician and the patient, ensuring that the technician can provide knowledgeable and accurate health advice. empathy is key when dealing with patients who may be suffering from physical or mental health issues, as it allows the technician to be sensitive to their needs and provide understanding and support.
Furthermore, an Occupational Health Technician must have strong critical thinking and problem solving skills. This is necessary in order to accurately assess and diagnose health issues, develop effective treatment plans, and recognize potential hazards in the workplace. Finally, an Occupational Health Technician must possess a comprehensive knowledge of medical terminology and protocols, as well as have a deep understanding of occupational health laws and regulations.
Having these skills will ensure that Occupational Health Technicians are able to provide the highest level of care to their patients.
Occupational Training Specialist, Occupational Health Advisor, and Occupational Safety Engineer are related jobs you may like.
Frequent Interview Questions
- What experience do you have in Occupational Health?
- How familiar are you with health and safety regulations?
- Describe a successful Occupational Health project you have completed in the past.
- What methods do you use to measure and assess employee health?
- How do you communicate health and safety information to employees?
- How do you develop and implement health and safety programs?
- What strategies do you use to ensure compliance with health and safety regulations?
- What have you done to promote healthy lifestyle choices among employees?
- What challenges have you faced in providing Occupational Health services?
- What skills do you possess that make you a good Occupational Health Technician?
Common Tools in Industry
- Blood Pressure Monitor. A device used to measure blood pressure levels. (eg: Omron Blood Pressure Monitor)
- Respiratory Protection Equipment. Protective gear used to protect against hazardous airborne particles. (eg: 3M Half Face Respirator)
- Hearing Test Equipment. Devices used to assess hearing loss and other auditory issues. (eg: Audiometer)
- Vision Test Equipment. Devices used to measure visual acuity and other vision issues. (eg: Snellen Chart)
- Ergonomic Evaluation Tools. Tools used to assess the design of a workspace and its potential impact on a workers health. (eg: Quick Risk Assessment Tool)
- Respiratory Fit Testing Equipment. Devices used to test the fit of respirators on workers. (eg: TSI Portacount Fit Tester)
- Drug Testing Kits. Kits used to test for drugs in the workplace. (eg: Alere iCup Drug Test Kit)
- Noise Dosimeters. Devices used to measure and record noise levels in the workplace. (eg: Larson Davis 800 Series Dosimeter)
Professional Organizations to Know
- National Institute for Occupational Safety and Health (NIOSH)
- American Association of Occupational Health Nurses (AAOHN)
- American Board of Industrial Hygiene (ABIH)
- International Commission on Occupational Health (ICOH)
- American Industrial Hygiene Association (AIHA)
- American College of Occupational and Environmental Medicine (ACOEM)
- International Labour Organization (ILO)
- American Association of Occupational Health Professionals (AAOHP)
- American College of Occupational and Environmental Health Nursing (ACOEHN)
- British Occupational Hygiene Society (BOHS)
We also have Occupational Psychologist, Occupational Health and Safety Officer, and Occupational Environmental Scientist jobs reports.
Common Important Terms
- Occupational Health and Safety. Refers to the practice of protecting the health, safety, and welfare of employees in the workplace.
- Hazard Identification. The process of identifying potential hazards in the workplace and assessing their risk.
- Risk Assessment. The evaluation of potential hazards and their associated risks in order to develop strategies to reduce or eliminate them.
- Ergonomics. The study of how people interact with their work environment in order to optimize comfort, efficiency, and safety.
- Industrial Hygiene. The practice of preventing or controlling worker exposure to hazardous materials or conditions in the workplace.
- Hazard Communication. The process of providing employees with information about potential hazards in the workplace and how to protect themselves.
- Workplace Inspection. The systematic examination of a workplace to identify hazards and evaluate safety and health risks.
- Emergency Preparedness. The process of planning and preparing for potential workplace emergencies.
- First Aid. The immediate treatment of injuries and illnesses in the workplace to prevent further harm or illness.
- Record Keeping. The process of documenting workplace safety and health activities, such as accident reports, training records, inspection results, etc.
Frequently Asked Questions
What qualifications are required to become an Occupational Health Technician?
To become an Occupational Health Technician, individuals must possess a minimum of a high school diploma or GED. A degree in health sciences, health services, or a related field is also recommended.
What is the job outlook for Occupational Health Technicians?
According to the Bureau of Labor Statistics, the job outlook for Occupational Health Technicians is expected to grow at a rate of 15% through 2029.
What duties does an Occupational Health Technician perform?
The primary duties of an Occupational Health Technician involve conducting health screenings and assessments, providing health counseling and education, and developing and implementing health and safety programs.
What type of environment do Occupational Health Technicians work in?
Occupational Health Technicians typically work in industrial settings, such as factories and warehouses, to monitor and address health and safety issues.
What is the average salary for an Occupational Health Technician?
The median salary for an Occupational Health Technician is approximately $46,000 per year.
What are jobs related with Occupational Health Technician?
- Occupational Medicine Physician
- Occupational Kinesiologist
- Occupational Health and Safety Technician
- Occupational Physiotherapist
- Occupational Exposure Scientist
- Occupational Disability Case Manager
Web Resources
- Example Career: Occupational Health and Safety Technicians www.wvu.edu
- Occupational Health and Safety Technician Career Overview online.athens.edu
- Home | Occupational Health Services | Washington University in occupationalhealth.wustl.edu
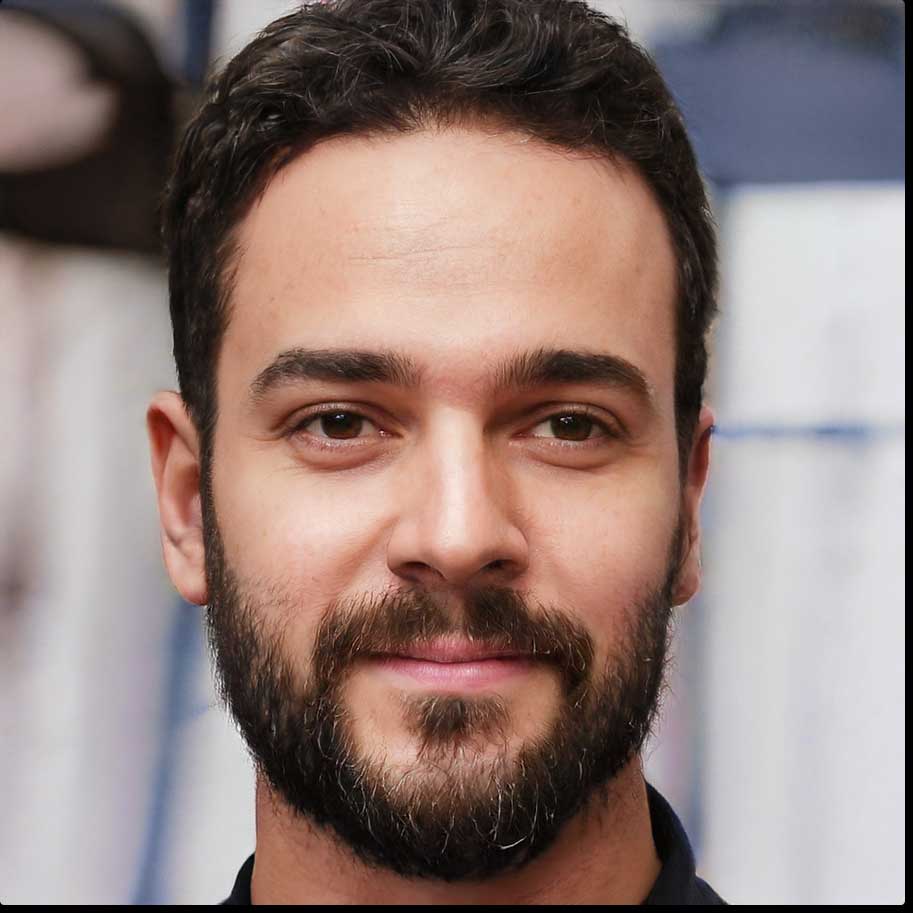