How to Be Machine Technician - Job Description, Skills, and Interview Questions
The lack of qualified machine technicians can have serious implications for a business. When machines malfunction or need repairs, production can be halted, resulting in lost time and money. Furthermore, without properly trained personnel, machines can be misused or damaged, leading to additional costs for repairs or replacements.
To ensure the efficient and safe operation of machinery, it is essential to have skilled and experienced technicians who can diagnose and repair malfunctions quickly and correctly. Investing in the training and development of technicians can help reduce downtime, protect equipment from damage, and improve the safety of the workplace.
Steps How to Become
- Obtain a High School Diploma or GED. Most employers require machine technicians to have at least a high school diploma or GED. Consider taking classes in math and science, which are important for operating and troubleshooting machines.
- Consider a Technical School or College Degree. Consider taking courses at a technical school or college to gain a degree in industrial maintenance or machine technology. This can give you a leg up when applying for jobs and make you more qualified for positions.
- Complete On-the-Job Training. Many employers provide on-the-job training for machine technicians. You may have to spend some time shadowing experienced technicians or attending seminars and workshops.
- Get Certified. You may be able to get certified as a machine technician by taking a certification exam. This can help you stand out when applying for jobs and make you more attractive to employers.
- Get Licensed. Depending on the state you live in, you may need to get a license to practice machine technology. Check with your states licensing board for specific requirements.
Staying ahead and qualified as a Machine Technician requires dedication, commitment, and a passion for learning. The technology used in the industry is ever-evolving, and therefore it is essential to stay up to date on the latest advancements. This can be done by attending workshops, seminars, and conferences related to the field, taking online courses to broaden knowledge, and networking with other professionals.
having certifications in the specific technology used can be beneficial, as it shows employers that the individual is qualified and up to date. dedicating time and effort to continuously educating oneself on the industry will keep Machine Technicians ahead of the curve and qualified for any job.
You may want to check Network Technician, Pharmacy Technician, and Field Service Technician for alternative.
Job Description
- Diagnose machine malfunctions, using knowledge of machine operations, electrical and electronic theory and mechanical principles.
- Assemble and install new machines or replace defective components.
- Repair machines, using hand tools, power tools, precision measuring instruments, and machine shop equipment.
- Read blueprints, schematics and diagrams to determine the method and sequence of assembly of a part, machine, or piece of equipment.
- Perform regular preventive maintenance on machines to ensure their proper functioning.
- Disassemble machines, replace worn parts, reassemble and test operation of machines after completion of repairs.
- Set up and adjust production equipment according to product specifications.
- Direct activities of workers engaged in machine set-up, operation, maintenance and repair.
- Create and maintain maintenance records for all equipment.
- Recommend design modifications to eliminate machine or system malfunctions.
Skills and Competencies to Have
- Knowledge of mechanical systems and components
- Ability to read and interpret blueprints and schematics
- Proficiency in using hand and power tools, such as drills and saws
- Ability to troubleshoot and diagnose mechanical problems
- Knowledge of safety protocols when working with machines
- Ability to use computer-aided design (CAD) software
- Ability to assemble and disassemble machinery
- Knowledge of basic electrical principles
- Ability to operate various types of machinery
- Ability to modify and maintain machinery
Having a good technical understanding of machines is an essential skill for any machine technician. When diagnosing a problem or performing maintenance, it is important to understand the underlying mechanisms and components in order to effectively resolve the issue. This requires a comprehensive knowledge of how the machine functions, from its electrical systems to its mechanical parts.
knowledge of the applicable safety regulations and best practices is also necessary to ensure the work is completed safely and in compliance with industry standards. With all these skills, it is possible to troubleshoot and repair machines quickly and accurately, saving time and money for the company.
Maintenance Technician, Quality Control Technician, and Industrial Technician are related jobs you may like.
Frequent Interview Questions
- How do you troubleshoot mechanical and electrical problems?
- Describe a situation where you had to use your technical problem solving skills to resolve a complex issue.
- What experience do you have working with CNC machines?
- What is your experience in programming, setting up, and maintaining robotic systems?
- What processes have you implemented to ensure machine quality and consistency?
- How do you handle difficult technical challenges?
- What safety protocols do you follow when working with machinery?
- How do you stay up-to-date with the latest technical innovations?
- How do you handle situations where you are asked to work on unfamiliar machinery?
- Describe a complex project you completed successfully in a machine technician role.
Common Tools in Industry
- Hand Tools. A variety of hand tools used to perform manual operations, such as screwdrivers, hammers, wrenches, pliers, saws, and chisels (eg: screwdriver).
- Power Tools. Tools powered by electricity, such as drills, saws, grinders, and sanders (eg: drill).
- Electrical Testing Equipment. Equipment used to diagnose or measure electrical current or voltage in a circuit (eg: multimeter).
- Lifting Devices. Devices used to lift heavy objects, such as hoists and cranes (eg: crane).
- Pneumatic Tools. Tools powered by compressed air, such as impact wrenches and grinders (eg: impact wrench).
- Hydraulic Tools. Tools powered by hydraulic pressure, such as presses and jacks (eg: press).
- Machine Shop Tools. A variety of tools used in a machine shop to cut, shape, and finish metal parts (eg: lathe).
- Computer-controlled Tools. Tools operated by computer programs, such as CNC machines (eg: CNC machine).
Professional Organizations to Know
- Association for Manufacturing Technology (AMT)
- Society of Manufacturing Engineers (SME)
- The American Society of Mechanical Engineers (ASME)
- International Federation of Robotics (IFR)
- Robotics Industries Association (RIA)
- International Society of Automation (ISA)
- National Institute for Metalworking Skills (NIMS)
- Automate - The Association for Advancing Automation (A3)
- Industrial Maintenance & Plant Operations (IMPO)
- International Association of Machinists & Aerospace Workers (IAMAW)
We also have Process Technician, Audio/Visual Technician, and Chemical Technician jobs reports.
Common Important Terms
- Troubleshooting. The process of diagnosing and fixing a technical issue or problem.
- Diagnostics. The testing of a device to identify and diagnose a problem.
- Maintenance. Regularly scheduled activities that are done to prevent a machine from breaking down.
- Parts Replacement. The process of replacing worn or defective parts in a machine.
- Alignment. The process of adjusting the components of a machine to ensure it is functioning properly.
- Calibration. The process of ensuring the accuracy of a machine's performance by verifying that it is within certain parameters.
- Programming. The process of writing or updating code for a machine to perform specific tasks.
- Electrical Wiring. The process of connecting electrical components in a machine to ensure it is functioning correctly.
- Soldering. The process of joining metal components together with a hot metal alloy.
- Cleaning. The process of removing dust and debris from a machine in order to keep it in good working condition.
Frequently Asked Questions
What are the duties of a Machine Technician?
The primary duties of a Machine Technician include repairing and maintaining machinery, diagnosing mechanical issues, and performing preventative maintenance.
What type of skills do Machine Technicians need?
Machine Technicians need strong mechanical aptitude and problem-solving skills, as well as knowledge of electrical systems, hydraulics, pneumatics, and other related systems.
What is the average salary for a Machine Technician?
The average salary for a Machine Technician is around $50,000 per year, depending on experience and location.
What educational requirements are necessary to become a Machine Technician?
Generally, most employers require that Machine Technicians have a high school diploma or GED and have completed a formal training program or apprenticeship.
What tools do Machine Technicians use to diagnose and repair machinery?
Machine Technicians use a variety of tools, including wrenches, screwdrivers, pneumatic tools, gauges, calibrators, and computers to diagnose and repair issues with machinery.
What are jobs related with Machine Technician?
Web Resources
- Machine Tool Technician - Fox Valley Technical College www.fvtc.edu
- Certified Machine Technician | Tulsa Technology Center tulsatech.edu
- Machine Technology - Machine Technology Machine laney.edu
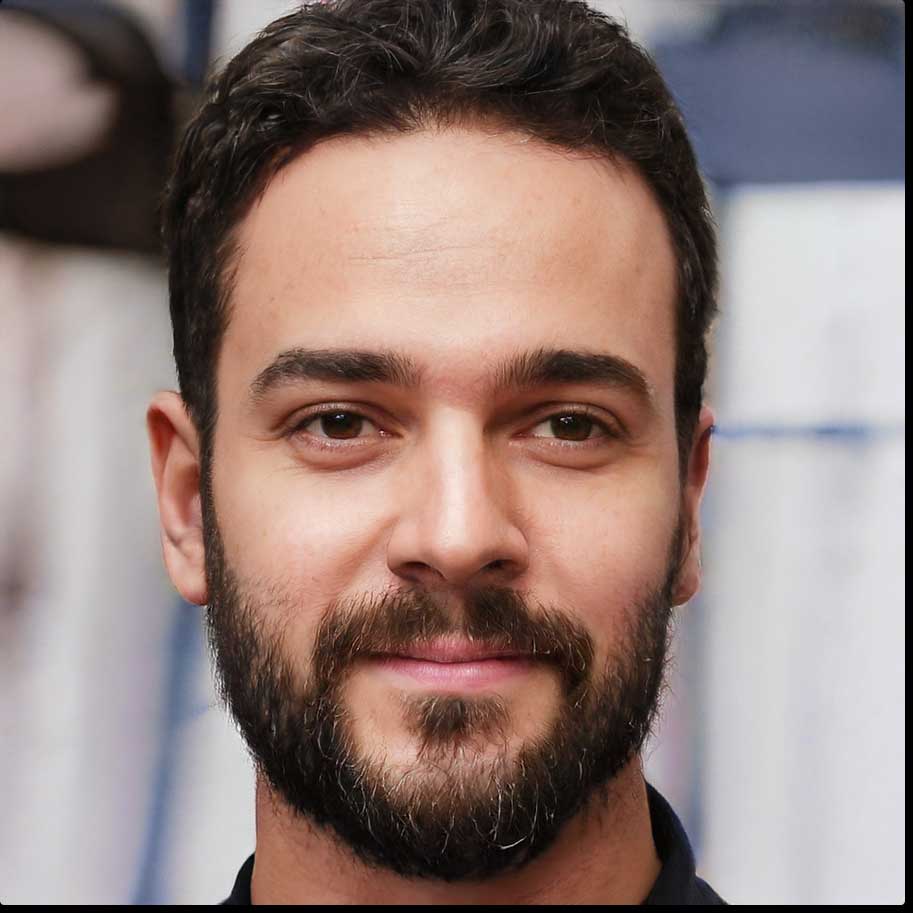