How to Be Quality Control Technician - Job Description, Skills, and Interview Questions
The role of the Quality Control Technician is essential in maintaining a high level of quality across a range of products and services. This is achieved by testing and inspecting incoming materials, components and finished products, to ensure they meet the required standards and specifications. In addition, they monitor production processes to ensure they are operating efficiently.
If any problems are identified, the Quality Control Technician will take corrective action to ensure quality is maintained. The result of this is that the company can maintain a reputation for producing and delivering high-quality products and services, increasing customer satisfaction and improving financial performance.
Steps How to Become
- Obtain a high school diploma or GED. Quality control technicians typically need a high school diploma or GED to qualify for entry-level positions.
- Consider earning a certificate or degree. While some companies may hire quality control technicians with only a high school diploma, others may prefer applicants who have earned a certificate or associate degree in a related field, such as manufacturing technology or quality assurance.
- Pursue on-the-job training. Many employers offer on-the-job training programs for quality control technicians. Employers may provide hands-on training and instruction in topics such as quality control principles and methods, testing procedures, and product inspection standards.
- Obtain certification. Although not required in all states, certifications may help quality control technicians demonstrate their expertise and stand out among other job applicants. Certifications are available through organizations such as the American Society for Quality (ASQ).
- Consider further education. Quality control technicians who have an associate degree may pursue a bachelors degree in an area such as engineering or business management to advance their career.
Quality Control Technicians are essential for maintaining high standards in a variety of industries. They ensure that products and services meet predetermined standards of quality. To become a successful Quality Control Technician, one must first have the right education, training, and experience.
Educational requirements typically involve a high school diploma or equivalent, as well as specialized training in the areas of mathematics, science, and engineering. Quality Control Technicians must have a good understanding of production processes, quality assurance methods, and problem-solving techniques. Once educated and trained, Quality Control Technicians must also gain experience in their desired field.
This may include working on a production line, inspecting products and services, or participating in quality control audits. With the right education, training, and experience, Quality Control Technicians are able to ensure that products and services meet the desired quality standards and help organizations maintain their competitive edge.
You may want to check Telecom Technician, Machine Technician, and Pharmacy Technician for alternative.
Job Description
- Perform quality control tests on products and materials to ensure compliance with product specifications.
- Monitor production processes to identify any issues that could lead to non-conforming products.
- Inspect finished products for defects and document results.
- Maintain accurate records of test results and report any discrepancies to management.
- Create and implement quality control procedures to ensure consistency in production and testing processes.
- Troubleshoot any production issues and recommend corrective actions.
- Utilize a variety of measuring and testing instruments to ensure accuracy and precision.
- Perform regular maintenance of testing equipment and record all servicing activities.
- Communicate with other departments to ensure quality control procedures are being followed.
- Assist with the development of quality control standards to ensure product safety and reliability.
Skills and Competencies to Have
- Ability to identify defects and suggest improvements
- Knowledge of quality assurance principles, techniques, and procedures
- Attention to detail and accuracy
- Ability to work independently as well as in teams
- Proficiency in using measuring tools, such as calipers, micrometers, and gauges
- Knowledge of ISO 9001 and other quality systems
- Understanding of statistical process control (SPC)
- Problem-solving and analytical skills
- Excellent communication, organizational, and record-keeping skills
- Ability to use computers and various software programs
Quality Control Technicians play a vital role in ensuring product quality throughout the entire production process. They are responsible for inspecting products, testing materials, and performing other duties to guarantee that products meet specified standards. To be successful in their role, Quality Control Technicians must possess certain skills and competencies.
The most important skill for a Quality Control Technician is attention to detail. Quality Control Technicians must be able to identify even the smallest of defects, inconsistencies, and irregularities, as these can indicate problems with the product or production process. They must also be able to use specialized equipment and tools to test the quality of materials.
Quality Control Technicians must be familiar with industry regulations and safety guidelines, as well as the quality management system of their employer. Good problem-solving skills and the ability to work independently are also essential for success in this role. With these skills and competencies, Quality Control Technicians can ensure that products meet the highest standards of quality.
Research Technician, Industrial Technician, and Process Technician are related jobs you may like.
Frequent Interview Questions
- What experience do you have with quality control and inspection processes?
- How do you evaluate product quality to ensure it meets customer requirements?
- Describe a time when you identified an issue with a products quality and implemented a corrective action.
- How do you maintain accurate records related to the quality control process?
- What tools and equipment have you used for measuring product quality?
- What techniques do you use to ensure compliance with industry standards?
- What approaches have you used to investigate complaints or issues related to product quality?
- How do you ensure that inspection results are properly documented and reported?
- How do you handle a situation when a product fails to meet the required quality standards?
- Describe a time when you had to use your problem-solving skills to identify the root cause of a quality issue.
Common Tools in Industry
- Calipers. Used to measure internal and external dimensions of objects (eg: measuring the diameter of a bolt).
- Micrometers. Used to measure small distances accurately (eg: measuring the thickness of a sheet of paper).
- Gauges. Used to check the size and shape of objects (eg: checking a hole diameter against a standard).
- Optical Comparator. Used to compare the dimensions of parts against a master template (eg: comparing a machined part to a blueprint).
- Force Gauges. Used to measure the amount of force applied to an object (eg: measuring the resistance of a spring).
- Ultrasonic Tester. Used to detect flaws in materials such as cracks and voids (eg: inspecting welds).
- Spectrophotometer. Used to measure and analyze the color of materials (eg: comparing paint swatches).
- Hardness Tester. Used to measure the hardness of materials (eg: verifying that a steel part meets a required hardness rating).
- Laser Scanner. Used to quickly measure the dimensions of objects (eg: measuring the length and width of a box).
- Temperature and Humidity Gauge. Used to measure temperature and humidity levels (eg: verifying conditions in a storage room).
Professional Organizations to Know
- American Quality Assurance Association (AQAA)
- American Society for Quality (ASQ)
- Institute of Quality Assurance (IQA)
- International Association for Six Sigma Certification (IASSC)
- International Organization for Standardization (ISO)
- Society of Manufacturing Engineers (SME)
- International Society of Automation (ISA)
- National Institute of Standards and Technology (NIST)
- American National Standards Institute (ANSI)
- National Quality Forum (NQF)
We also have Field Service Technician, Network Technician, and Chemical Technician jobs reports.
Common Important Terms
- Quality Assurance. Quality assurance is the process of verifying that a product or service meets quality standards or regulations.
- Calibration. Calibration is the process of ensuring that a measuring instrument is accurate and reliable.
- Testing. Testing is the process of evaluating a product or system to determine its performance and compliance with specified requirements.
- Acceptance Criteria. Acceptance criteria are the criteria used to determine if a product or service meets the desired quality level.
- Traceability. Traceability is the ability to trace the history, application, or location of a product or service.
- Statistical Process Control. Statistical process control is the use of statistical methods to monitor and control a process.
- Root Cause Analysis. Root cause analysis is a method of problem solving used to identify the underlying cause of a problem.
- Process Mapping. Process mapping is a method of documenting and analyzing business processes.
Frequently Asked Questions
What is the role of a Quality Control Technician?
Quality Control Technicians are responsible for ensuring that products meet specified standards of quality by inspecting, testing, and measuring products and materials. They use a variety of tools and techniques to carry out their job duties.
What are some of the key responsibilities of a Quality Control Technician?
Quality Control Technicians typically conduct inspections to ensure that products meet quality standards, analyze test results, record data, and recommend corrective actions when needed. They also may be responsible for calibrating and maintaining testing equipment, troubleshooting production problems, and providing training and guidance to other personnel.
What qualifications are needed to become a Quality Control Technician?
Most Quality Control Technician positions require at least an Associate's degree in a field related to Quality Control or a related field such as engineering or science. Other qualifications may include experience with laboratory testing, strong problem-solving skills, and knowledge of the principles of quality control.
What type of environment do Quality Control Technicians work in?
Quality Control Technicians typically work in manufacturing or industrial settings where they inspect raw materials and finished products to ensure they meet quality standards. They may also work in laboratories performing tests and analysis.
What is the average salary for a Quality Control Technician?
According to the U.S. Bureau of Labor Statistics, the median annual wage for Quality Control Technicians was $41,820 in May 2019. Salaries vary based on experience, location, and industry.
What are jobs related with Quality Control Technician?
Web Resources
- Quality Control Technician | Gateway Technical College - GTC www.gtc.edu
- Quality Technician Certificate | Northcentral Technical College www.ntc.edu
- Quality Technician - Anoka Tech anokatech.edu
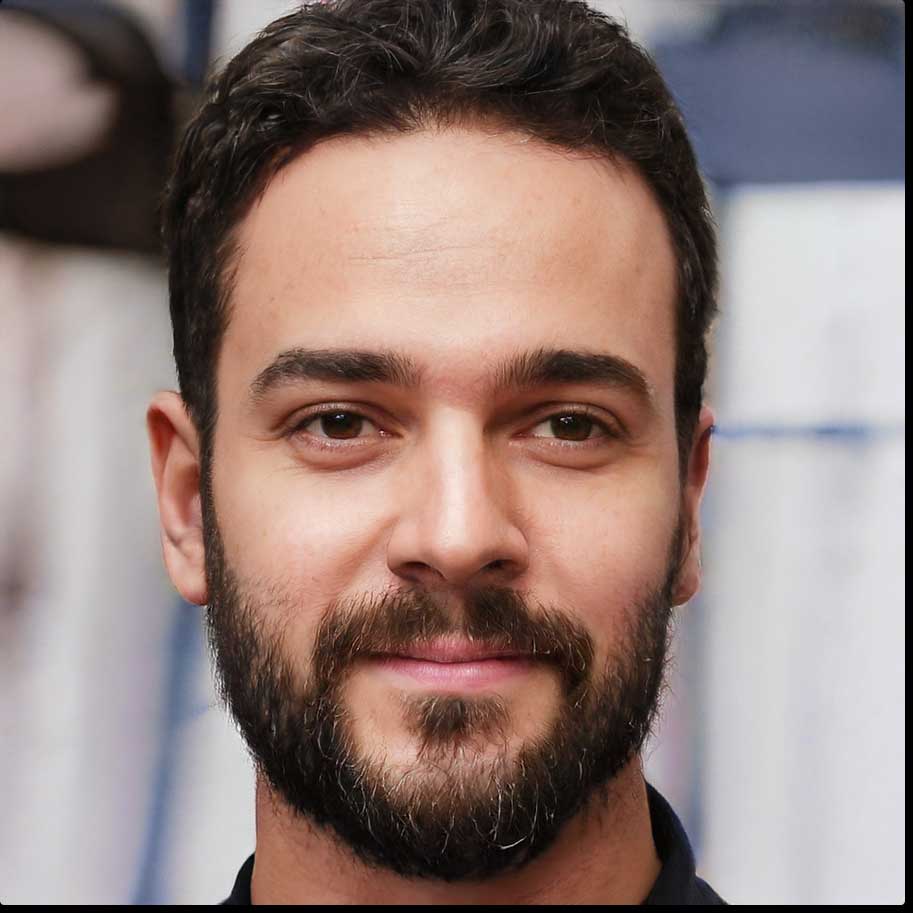