How to Be Industrial Technician - Job Description, Skills, and Interview Questions
Steps How to Become
- Earn a high school diploma or equivalent. Most employers require industrial technicians to have a high school diploma or its equivalent.
- Obtain postsecondary education. Some employers may expect industrial technicians to have an associate degree in industrial technology, but it is not always required.
- Participate in an apprenticeship. Apprenticeship programs provide on-the-job training and can last from two to four years.
- Earn certification. Certification is not required for industrial technicians, but it can help demonstrate your knowledge and skills.
- Pursue additional training. Industrial technicians should stay up to date on new technologies and best practices. They may need to take continuing education courses or attend seminars and workshops to stay current in their field.
- Consider joining a professional organization. Professional organizations such as Society of Maintenance and Reliability Professionals (SMRP) offer members access to educational resources, networking opportunities, and industry-specific events.
Industrial technicians are expected to stay up to date with the latest technologies and advances in their field in order to maintain a competitive edge in the workplace. To keep competent, regular training and continuing education is essential. Keeping up with industry trends, new technologies and changes in regulations can be accomplished by attending seminars, taking online courses, or reading trade publications.
Having a strong knowledge of safety procedures, such as lockout/tagout and emergency shutdown procedures, is also critical for staying ahead in the industry. industrial technicians must maintain an open dialogue with colleagues, supervisors, and customers to ensure they are up to date with the latest advancements and best practices in their field. By utilizing these strategies, industrial technicians can remain competent and competitive in the field.
You may want to check Maintenance Technician, Quality Control Technician, and Chemical Technician for alternative.
Job Description
- Install, maintain and repair industrial equipment, such as pumps, cranes, conveyors, automated systems and other industrial machinery.
- Troubleshoot mechanical and electrical systems to identify, diagnose and repair malfunctions.
- Test industrial equipment for proper performance and safety compliance, using diagnostic tools such as multimeters and oscilloscopes.
- Perform preventative maintenance on industrial equipment to ensure optimum performance and longevity.
- Read blueprints and technical manuals to ensure that equipment is assembled and operated correctly.
- Monitor inventory of spare parts and order replacements when necessary.
- Communicate with customers to assess their needs and provide solutions.
- Fabricate and weld parts as needed to complete repairs.
- Follow safety guidelines when working with hazardous chemicals and materials.
- Train new employees on the operation of industrial machinery.
Skills and Competencies to Have
- Knowledge of electrical systems, wiring and circuitry
- Ability to read and interpret technical drawings, blueprints and schematics
- Familiarity with a variety of hand tools, power tools and specialized equipment
- Ability to troubleshoot and diagnose electrical and mechanical problems
- Proficiency in the use of test instruments such as voltmeters, ammeters, ohmmeters
- Knowledge of basic mathematics, including algebra, geometry and trigonometry
- Ability to use computers for technical calculations and data analysis
- Skilled in welding and soldering processes
- Excellent communication skills, both verbal and written
- Ability to follow safety protocols and procedures
Having a strong set of industrial technician skills is essential for anyone seeking to enter this field. One of the most important skills to have is the ability to troubleshoot and repair complex systems. This requires a deep understanding of the underlying systems, components, and how they work together.
It also requires a good knowledge of the tools and equipment that are used for repairs. Being able to accurately diagnose and solve problems is critical to ensuring that the equipment is running properly and efficiently. having the ability to read and understand technical manuals, schematics and drawings is essential to successful repairs.
Other important skills include strong communication, organizational, problem-solving, and leadership abilities. All these skills are essential for industrial technicians to provide quality service and ensure the safety of personnel, equipment, and processes.
Process Technician, Network Technician, and Field Service Technician are related jobs you may like.
Frequent Interview Questions
- What experience do you have in the industrial technician field?
- How do you stay up to date with industry trends and developments?
- What challenges have you faced while working as an industrial technician?
- Describe a project you have completed successfully as an industrial technician.
- What safety protocols have you implemented in an industrial setting?
- What do you believe are the most important skills for an industrial technician?
- How do you diagnose and troubleshoot mechanical problems in industrial equipment?
- What methods do you use to ensure accuracy and precision in your work?
- How would you approach a complex problem in an industrial setting?
- How do you handle working with difficult clients or customers?
Common Tools in Industry
- Screwdriver. A tool used to drive screws into different materials. (eg: Phillips head screwdriver)
- Wrench. A tool used for turning nuts and bolts. (eg: adjustable wrench)
- Drill. A tool used to create holes in materials. (eg: cordless drill)
- Pliers. A tool used for gripping, twisting, and cutting different materials. (eg: needle-nose pliers)
- Hammer. A tool used for driving nails and other pieces into materials. (eg: claw hammer)
- Soldering Iron. A tool used to join two metals together with melted solder. (eg: butane soldering iron)
- Pipe Wrench. A tool used to tighten or loosen pipes and fittings. (eg: heavy-duty pipe wrench)
- Saw. A tool used to cut through materials such as wood, metal, or plastic. (eg: circular saw)
- Socket Wrench. A tool used to turn nuts and bolts in tight spaces. (eg: ratchet socket wrench)
- Tape Measure. A tool used to measure lengths and distances in a variety of units. (eg: retractable tape measure)
Professional Organizations to Know
- American Society of Mechanical Engineers (ASME)
- Institute of Electrical and Electronics Engineers (IEEE)
- National Institute for Certification in Engineering Technologies (NICET)
- The Society of Manufacturing Engineers (SME)
- Association for Manufacturing Technology (AMT)
- Association for Operations Management (APICS)
- International Facility Management Association (IFMA)
- Robotics Industries Association (RIA)
- American Welding Society (AWS)
- International Society of Automation (ISA)
We also have Telecom Technician, Audio/Visual Technician, and Pharmacy Technician jobs reports.
Common Important Terms
- Automation. Automation is the use of control systems and information technologies to reduce the need for human work in the production of goods and services.
- Robotics. Robotics is the branch of technology that deals with the design, construction, operation, and application of robots, as well as computer systems for their control, sensory feedback, and information processing.
- CNC Programming. CNC programming is the process used to create program instructions for computer numerical control (CNC) machines. These instructions tell the machine how to move and what tasks to perform.
- Machine Vision. Machine vision is the ability of a computer or robotic system to interpret and understand images from its surrounding environment. It is used in a variety of applications such as manufacturing inspection, medical imaging, and autonomous vehicle navigation.
- Pneumatics. Pneumatics is the branch of applied science that deals with the production and use of pressurized gas to transmit and control energy.
- Hydraulics. Hydraulics is the branch of applied science that deals with the production and use of pressurized liquid to transmit and control energy.
- Computer-aided Design (CAD). Computer-aided design (CAD) is the use of computer technology to design objects or systems. CAD software is used by industrial technicians to create detailed drawings and models of components, as well as to analyze product performance.
Frequently Asked Questions
What is an Industrial Technician?
An Industrial Technician is a professional who provides technical support and maintenance for industrial machinery and equipment in a factory or production environment.
What skills are required for an Industrial Technician?
Industrial Technicians must possess a wide range of knowledge, including mechanical, electrical, and electronic skills. They must also have excellent problem-solving abilities, be able to read and understand technical manuals and schematics, and have strong communication and interpersonal skills.
How long does it take to become an Industrial Technician?
It typically takes two years to complete an industrial technician program at a technical college.
What is the salary range for an Industrial Technician?
The median salary range for an Industrial Technician is between $45,000 and $65,000 per year.
What career opportunities are available to Industrial Technicians?
Industrial Technicians can pursue career paths in engineering, manufacturing, production, maintenance, and other related industries.
What are jobs related with Industrial Technician?
Web Resources
- Industrial Technician - Tarrant County College www.tccd.edu
- Energy & Industrial Technician - Northland Pioneer College www.npc.edu
- Industrial Mechanical Technician - Mid-State Technical College www.mstc.edu
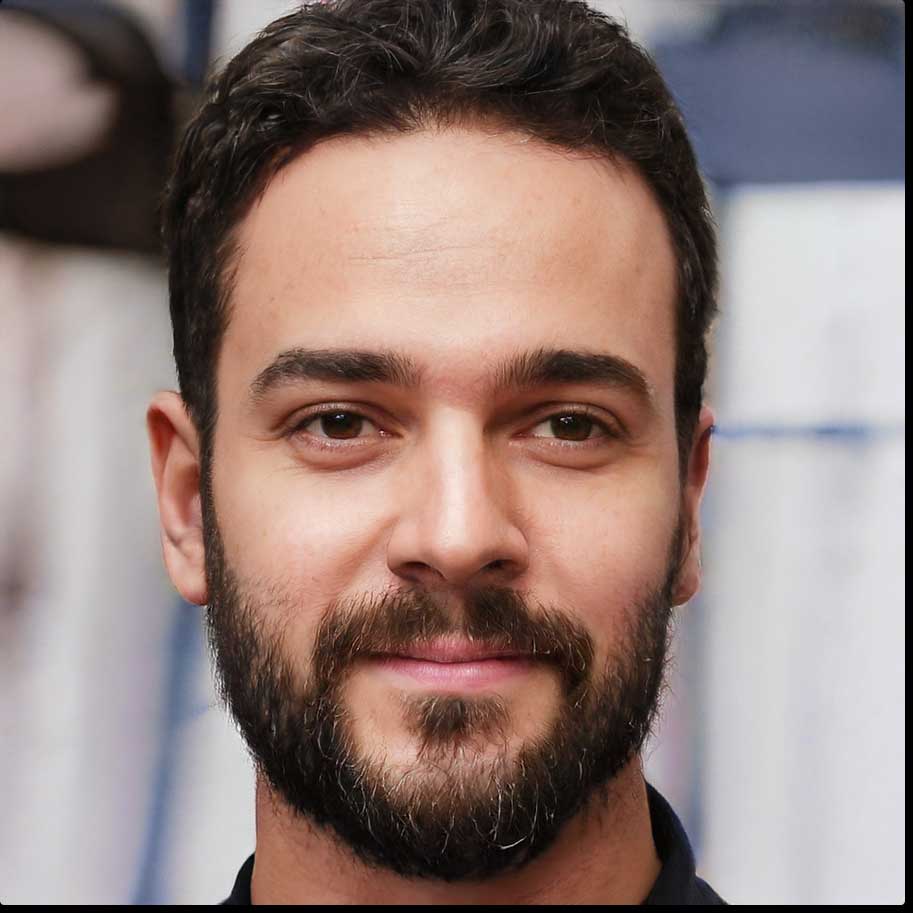