How to Be Industrial Welder - Job Description, Skills, and Interview Questions
Industrial welding is a process used to join metal components together efficiently and effectively. Welding is a popular choice for industrial applications due to its strength and durability. The process involves the use of heat to melt the metal components in order to join them together.
This intense heat can cause a variety of problems, including warping, distortion, and discoloration of the metal. the heat can cause dangerous fumes to be released, which can be harmful to the environment and workers if not properly vented. To ensure safety, industrial welders must take the proper precautions when performing the welding process, such as using personal protective equipment (PPE) and ensuring proper ventilation.
The quality of the weld is also important, as it directly affects the strength and reliability of the finished product. Therefore, it's important to use high quality materials and welding supplies, as well as to regularly inspect welds for defects.
Steps How to Become
- Research the job. Talk to professional welders, read books and articles about welding, and research welding programs at local trade schools and community colleges. This can help you decide if welding is the right career choice for you.
- Get certified. To become a professional welder, you must earn a welding certification. Take a welding course at a trade school or community college. Admissions departments can provide information about the courses and requirements.
- Obtain on-the-job training. Most employers will require at least one year of on-the-job training before hiring a welder. Look for apprenticeship programs or job shadowing opportunities to get experience in the field.
- Get additional certifications. Welders can obtain additional certifications to increase their job prospects, such as a welding inspector certification, which allows them to inspect welds for quality assurance.
- Stay up-to-date. Technology and welding processes are constantly evolving, so its important for welders to stay up-to-date on the latest advancements in the field. Consider attending conferences or seminars to stay current.
Staying ahead and efficient as an industrial welder requires a combination of knowledge, skill and experience. Knowing the latest welding methods and techniques, as well as understanding the various welding materials and equipment, is essential for staying ahead of the competition. ensuring that ones workspace is organized, well-lit, and free of safety hazards will help to maximize efficiency and productivity.
Furthermore, having access to the right tools and supplies can also improve welding efficiency. Finally, having a strong work ethic, discipline and dedication to the craft can help keep welders ahead of the rest. By following these guidelines, industrial welders will be able to stay ahead of their peers and achieve success.
You may want to check Industrial Automation Technician, Industrial Safety Officer, and Industrial Quality Inspector for alternative.
Job Description
- Read and interpret blueprints, sketches and welding process specifications
- Operate manual or semi-automatic welding equipment to fuse metal segments in flat, vertical, or overhead positions
- Monitor the fitting, burning, and welding processes to avoid overheating of parts or warping, shrinking, distortion, or expansion of material
- Fit and join metal components of products as specified by layouts, blueprints, diagrams, or work orders
- Set up components for welding according to specifications
- Inspect grooves, angles or gap allowances, using micrometers, calipers, and rulers
- Repair machinery and other components by welding pieces and filling gaps
- Maintain equipment in a condition that does not compromise safety
- Select and install torches, torch tips, filler rods and flux, according to welding chart specifications or type and thickness of metal
- Use hand tools such as wire brushes to remove rust and dirt from work pieces
- Interpret application of technical data relative to welding processes
- Maintain accurate records of welds completed
Skills and Competencies to Have
- Ability to read and interpret blueprints and schematics
- Knowledge of welding techniques, processes, and tools
- Knowledge of materials and their properties
- Ability to use and maintain welding equipment
- Ability to plan and layout welding jobs
- Ability to operate oxy-fuel torches, plasma arc welders, and other welding machines
- Ability to inspect and test welds for defects
- Ability to identify and select the appropriate welding technique for a given project
- Ability to work with various metals, including steel, aluminum, brass, and iron
- Ability to read and interpret safety rules and regulations
Being an industrial welder requires a wide range of skills and knowledge. One of the most important skills to have is an understanding of different welding techniques, such as oxy-fuel, plasma arc, and tungsten inert gas welding. This knowledge allows welders to efficiently and effectively complete their tasks.
a good welder should have a strong grasp on safety protocols and regulations, as well as knowledge of the necessary materials and tools to use in the welding process. With these skills, welders can work safely without any risk of injury or damage to the equipment. Furthermore, they will be able to produce quality work that meets industry standards.
Lastly, welders must be able to read and interpret engineering drawings in order to understand the job they're working on. Having this mastery of all these skills is essential for a successful industrial welder.
Industrial Maintenance Engineer, Industrial Project Manager, and Industrial Machinist are related jobs you may like.
Frequent Interview Questions
- What experience do you have in industrial welding?
- Describe a welding assignment you have completed in the past.
- What methods of industrial welding are you most proficient in?
- How do you handle welding in confined spaces?
- What safety precautions do you take when working with industrial welding?
- How do you stay up to date on the latest industrial welding techniques?
- What challenges have you faced while working with industrial welding?
- How would you rate your knowledge of welding materials?
- What processes do you use to ensure proper welds are achieved?
- Are there any particular welding projects that you are more experienced in?
Common Tools in Industry
- Arc Welder. A welding tool that uses electricity to create an electric arc between an electrode and the base material to form a strong bond. (Eg: Miller Electric Arc Welder)
- Gas Welder. A welding tool that uses fuel and oxygen to create a flame that melts the base material and filler metal to form a joint. (Eg: Victor Thermal Dynamics Gas Welder)
- TIG Welder. A welding tool that uses a non-consumable tungsten electrode to heat and fuse the base material and filler metal. (Eg: Miller TIG Welder)
- MIG Welder. A welding tool that uses a consumable wire electrode to heat and fuse the base material and filler metal. (Eg: Lincoln Electric MIG Welder)
- Spot Welder. A welding tool that uses electricity to create a spot weld between two pieces of metal. (Eg: Miller Spot Welder)
- Flux Core Welder. A welding tool that uses a continuous wire electrode with flux core to heat and fuse the base material and filler metal. (Eg: Esab Flux Core Welder)
- Plasma Cutter. A cutting tool that uses electricity to create a high-temperature arc between an electrode and the base material to form a cut. (Eg: Hypertherm Powermax Plasma Cutter)
Professional Organizations to Know
- American Welding Society (AWS)
- American Society of Mechanical Engineers (ASME)
- American Institute of Steel Construction (AISC)
- Society of Manufacturing Engineers (SME)
- International Institute of Welding (IIW)
- National Institute of Metalworking Skills (NIMS)
- International Brotherhood of Boilermakers (IBB)
- Fabricators & Manufacturers Association International (FMA)
- American Society for Quality (ASQ)
- International Fabricators & Erectors Association (IFEA)
Common Important Terms
- Arc Welding. A process of welding in which an electric arc is used to generate heat to melt the two pieces of metal to be joined.
- MIG Welding. A welding process that uses a gas metal arc welding process to join two pieces of metal together.
- TIG Welding. A welding process that uses a tungsten inert gas (TIG) to join two pieces of metal together.
- Stick Welding. A welding process that uses an arc welding process to join two pieces of metal together.
- Oxy-Fuel Welding. A welding process that uses oxygen and an oxy-fuel gas, such as acetylene, to join two pieces of metal together.
- Brazing. A welding process that uses a filler material, such as copper or silver, to join two pieces of metal together.
- Soldering. A welding process that uses a low-temperature alloy, such as lead or tin, to join two pieces of metal together.
- Flux Cored Arc Welding. A welding process that uses a flux-cored wire to join two pieces of metal together.
- Shielded Metal Arc Welding. A welding process that uses an electric arc and a consumable electrode, such as an E70S-3 wire, to join two pieces of metal together.
- Gas Tungsten Arc Welding. A welding process that uses a tungsten electrode and a shielding gas, such as argon, to join two pieces of metal together.
Frequently Asked Questions
What is an Industrial Welder?
An Industrial Welder is a skilled tradesperson who uses specialized equipment to join or cut metal components together. This is usually done through the use of heat, pressure, and various welding processes.
What types of materials are welded?
Industrial Welders typically weld materials such as stainless steel, aluminum, titanium, and other alloys.
What qualifications are needed to become an Industrial Welder?
In order to become an Industrial Welder, one must typically have a high school diploma or equivalent and pass a welding certification test. Additionally, some employers may require a certificate or degree in welding technology.
What safety precautions should be taken when welding?
When welding, it is important to always wear the proper safety gear, such as face shields, gloves, and fire-resistant clothing. Additionally, it is important to ensure that the workspace is well ventilated and that all flammable materials are kept away from the work area.
What is the average salary for an Industrial Welder?
The average salary for an Industrial Welder is approximately $43,000 per year. Salaries can vary depending on experience, location, and type of welding performed.
What are jobs related with Industrial Welder?
Web Resources
- Industrial Welding | ALASKA VOCATIONAL TECHNICAL CENTER www.avtec.edu
- Welding, Industrial Welder, Level 2 Certificate - San Jacinto College publications.sanjac.edu
- Tri-C Industrial Welding Courses: Cleveland Ohio www.tri-c.edu
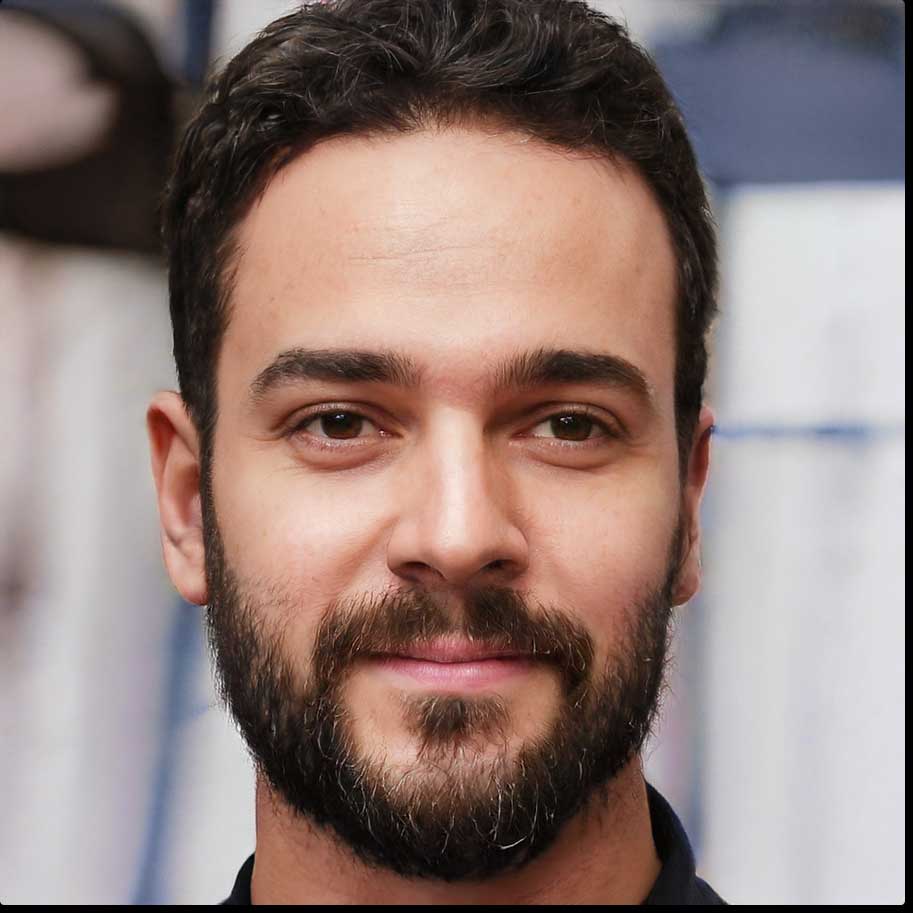