How to Be Industrial Machinist - Job Description, Skills, and Interview Questions
Industrial machinists are highly-skilled professionals who are responsible for operating and maintaining sophisticated machinery used in a variety of industries. Their expertise and knowledge of engineering principles play an important role in producing high-quality products. As a result, they help to increase productivity, reduce costs, and ensure the safety of the manufacturing process.
their experience with precision tools and techniques helps to improve the accuracy and reliability of the end product. As a result of the industrial machinist's contributions, businesses can experience improved efficiency, increased profits, and a higher level of customer satisfaction.
Steps How to Become
- Obtain a high school diploma or equivalent. Many employers prefer applicants who have a high school diploma. In addition, some technical schools and community colleges require applicants to have a high school diploma or equivalent before entering a machinist program.
- Enroll in a machinist program. Machinist training programs are offered through technical schools and community colleges. Programs typically last one to two years and may provide certification or an associate degree. Coursework includes mathematics, blueprint reading, metallurgy, computer-aided design and machine tool operations.
- Obtain an apprenticeship. Apprenticeships are available through labor unions, private companies and the military. Apprenticeships provide hands-on training in a variety of machining areas, including welding and grinding.
- Get on-the-job experience. After completing an apprenticeship or training program, industrial machinists usually work under the supervision of experienced machinists. As they gain skills, they can advance to positions that involve setting up and operating machines and making minor repairs.
- Join a professional organization. Professional organizations, such as the National Tooling and Machining Association, provide resources and information to industrial machinists. Membership can also help machinists stay up to date on new technologies and industry trends.
Industrial machinists must stay up to date on the latest trends and technologies in order to remain efficient and productive. To do this, they should regularly attend workshops and seminars, read trade journals, and keep up with the latest advancements in their field. they should have access to the right tools and equipment so that they can easily and quickly complete tasks.
Finally, having a good support system of colleagues and mentors is essential in order to stay informed and on top of their work. All of these steps can help industrial machinists maintain their high standards of productivity and efficiency.
You may want to check Industrial Safety Officer, Industrial Welder, and Industrial Painter for alternative.
Job Description
- Setup and operate milling and lathe machines, grinders, and other precision tools to produce parts according to customer specifications and standards.
- Read and interpret blueprints, sketches, drawings, manuals, and specifications to determine the dimensions and tolerances of finished work pieces, sequence of operations, and machine setup requirements.
- Inspect parts using precision measuring instruments such as calipers, micrometers, and gauges to ensure conformance to customer and industry standards.
- Perform regular maintenance, troubleshoot and repair of machinery on the production floor.
- Select appropriate cutting tools, materials, and machine speeds and feeds based on work piece features and requirements.
- Calculate cutting speeds, feeds, depths of cuts, and tool selection to provide optimal results.
- Monitor machine operations and adjust settings as necessary to ensure quality production.
- Troubleshoot and resolve issues with machines, tools, and processes in a timely manner.
- Ensure safe operation of machinery at all times and adhere to safety protocol.
- Maintain a clean and organized work area to ensure all tools are in proper working order.
Skills and Competencies to Have
- Understanding of engineering drawings and specifications.
- Knowledge of machine tools and the ability to set them up and operate them.
- Ability to read calipers and micrometers for precision measurements.
- Proficient in the use of shop math to calculate dimensions and tolerances.
- Ability to troubleshoot machining processes to correct errors or improve quality.
- Skill in using basic hand tools such as wrenches, screwdrivers, and pliers.
- Knowledge of safety procedures for working with industrial machinery.
- Understanding of basic machining principles such as cutting speeds and feeds.
- Knowledge of tool selection and changing procedures.
- Ability to monitor machines during operation to identify potential problems.
Industrial Machinists play an essential role in the manufacturing process by operating and maintaining a variety of machinery. To be successful in this position, it is important to have a strong working knowledge of machines and tools, as well as the ability to read and interpret technical documents. Having good problem-solving skills is also essential, as Industrial Machinists must be able to troubleshoot and repair any issues that arise during the manufacturing process.
The ability to work with precision is another key skill for Industrial Machinists, as accuracy is critical for producing high-quality products. Finally, having excellent organizational skills is important to ensure that the production process runs smoothly and efficiently. All of these skills combined make Industrial Machinists essential to the success of any manufacturing business.
Industrial Project Manager, Industrial Maintenance Engineer, and Industrial Automation Technician are related jobs you may like.
Frequent Interview Questions
- What experience do you have in setting up and operating industrial machines?
- How familiar are you with safety protocols for operating industrial machinery?
- What experience do you have in making intricate parts with a milling machine?
- How do you troubleshoot mechanical issues when operating industrial machines?
- Describe your experience in making metal components with a lathe.
- What techniques do you use to ensure accuracy when operating industrial machines?
- Describe your experience with CNC machines.
- What measures do you take to ensure quality control when using industrial machines?
- How do you ensure that the parts you make meet the required specifications?
- What additional training have you taken to improve your skills in operating industrial machines?
Common Tools in Industry
- Milling Machine. Used to shape metal or other materials by cutting, drilling, or grinding. (eg: CNC Milling Machine)
- Lathe. A machine tool that rotates a workpiece on its axis to perform various operations such as cutting, sanding, knurling, drilling, or deformation. (eg: CNC Lathe)
- Drill Press. A machine tool used to drill holes in materials like metal and wood. (eg: Radial Drill Press)
- Grinder. A machine tool used to grind or sand materials such as metal, plastic, or wood. (eg: Bench Grinder)
- CNC Machine. Computer numerical controlled machines that allow for greater speed and accuracy than manual machining. (eg: CNC Milling Machine)
- Boring Machine. A machine used to make holes in materials like metal and wood. (eg: Vertical Boring Machine)
- Sander. A machine tool used for sanding materials like wood, metal, or plastic. (eg: Belt Sander)
- Saw. A machine tool used to cut materials such as wood, metal, or plastic. (eg: Table Saw)
- Press. A machine tool used to press or shape materials such as metal and plastic. (eg: Hydraulic Press)
- Welding Machine. A machine tool used to weld materials such as metal and plastic. (eg: TIG Welder)
Professional Organizations to Know
- Association for Manufacturing Excellence (AME)
- American Machine Tool Distributors' Association (AMTDA)
- National Institute for Metalworking Skills (NIMS)
- Society of Manufacturing Engineers (SME)
- International Organization of Industrial Automation (IOIA)
- National Tooling and Machining Association (NTMA)
- National Association of Manufacturers (NAM)
- Tooling and Manufacturing Association (TMA)
- Industrial Machinery Mechanics, Machinery Maintenance Workers, and Millwrights (IMMMMW)
- International Association of Machinists and Aerospace Workers (IAMAW)
Common Important Terms
- CNC Machining. CNC machining is the use of computer numerical control equipment to cut, shape, and finish metal and plastic parts.
- Lathe. A lathe is a machine tool used to shape and finish metal and plastic parts by spinning them against a cutting tool.
- Milling. Milling is a machining process used to shape metal and plastic parts using a rotating cutting tool.
- Drilling. Drilling is a machining process in which holes are made in metal and plastic parts using a rotating cutting tool.
- Turning. Turning is a machining process in which metal and plastic parts are shaped by rotating them against a cutting tool.
- Grinding. Grinding is a machining process used to shape metal and plastic parts by abrading them with a rotating cutting tool.
- Shaping. Shaping is a machining process in which metal and plastic parts are shaped by cutting them with a rotating cutting tool.
- Boring. Boring is a machining process in which holes are made in metal and plastic parts using a rotating cutting tool.
- Chamfering. Chamfering is a machining process used to create an angled edge on metal and plastic parts.
- Reaming. Reaming is a machining process used to enlarge and smooth the interior surfaces of metal and plastic parts.
Frequently Asked Questions
What qualifies a person to become an Industrial Machinist?
To become an Industrial Machinist, individuals must typically possess a high school diploma or equivalent and complete a training program in machining, mechanical engineering, or another related field.
What type of tools do Industrial Machinists use?
Industrial Machinists use a variety of tools, including lathes, milling machines, drill presses, grinders, and saws.
What tasks does an Industrial Machinist typically perform?
Industrial Machinists typically perform tasks such as fabricating and assembling parts, machining and repairing parts, setting up and operating production machines, troubleshooting malfunctions, reading blueprints and specifications, and performing quality assurance checks.
What safety protocols do Industrial Machinists need to follow?
Industrial Machinists need to follow safety protocols such as wearing protective clothing, observing safety guidelines for operating machinery, and adhering to safety regulations and standards.
What is the median salary for an Industrial Machinist?
According to the Bureau of Labor Statistics, the median salary for an Industrial Machinist in the United States is $44,610 per year.
What are jobs related with Industrial Machinist?
Web Resources
- Industrial Machinist - Umpqua Community College www.umpqua.edu
- Industrial Maintenance and Machining | Polk State College www.polk.edu
- Machinist I | Ogden-Weber Technical College www.otech.edu
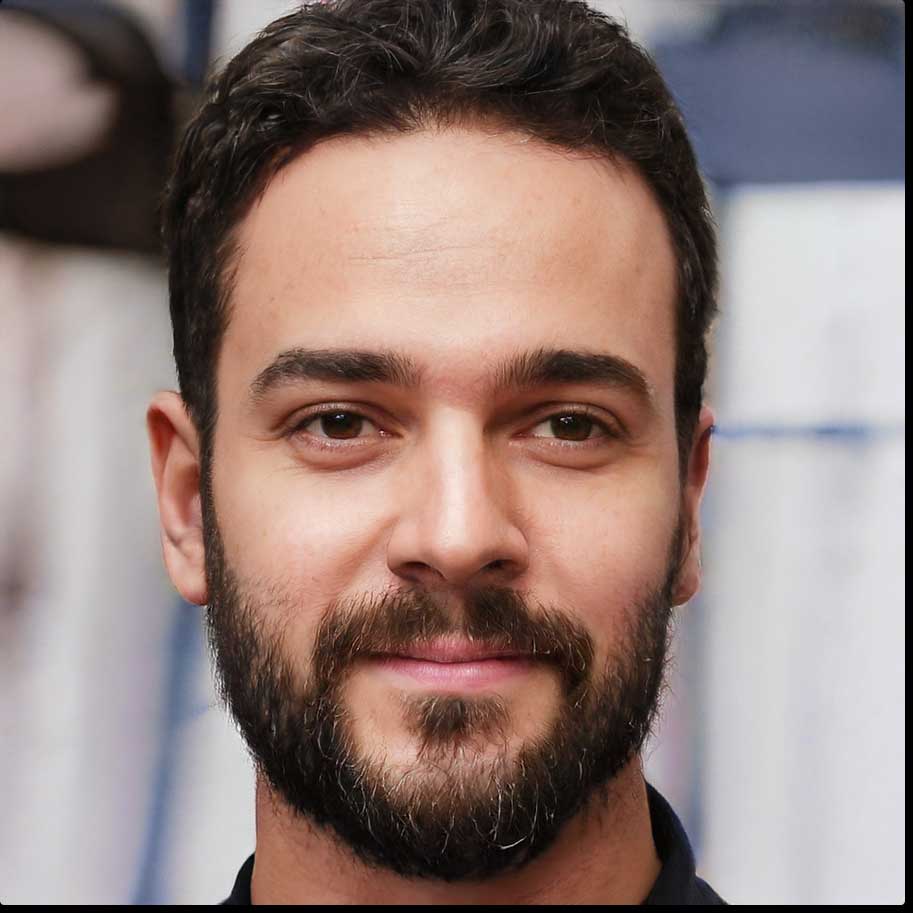