How to Be Industrial Safety Officer - Job Description, Skills, and Interview Questions
The lack of an industrial safety officer in a workplace can have serious consequences. Without the expertise and experience of a safety officer to oversee operations, hazardous materials could remain undetected, leading to potential accidents and injuries. In addition, employees may not be properly trained, increasing the risk of injury or illness.
Without proper safety protocols, the risk of fire and explosions increases, posing even greater danger to the workers and property. Furthermore, the lack of an industrial safety officer can lead to costly fines and lawsuits brought against the employer. By having a qualified safety officer on staff, employers can ensure that their workplaces are safe and compliant with industry standards, thus protecting workers and avoiding financial repercussions.
Steps How to Become
- Earn a Bachelor's Degree. Industrial safety officers must have a bachelor's degree in occupational health and safety or a related field such as engineering, environmental science, or chemistry. Education should include courses in hazardous materials management, environmental law, workplace safety, and industrial hygiene.
- Obtain Certification. Certification is voluntary but may be required by employers. Industrial safety officers can become certified as a safety professional by the Board of Certified Safety Professionals or by a state-level certification program.
- Gain Experience. Entry-level positions in industrial safety require at least one year of experience. Experience can be gained by working in a related field such as engineering or environmental science.
- Attend Training Courses. Industrial safety officers should stay up to date on new regulations and technologies related to the field. Training courses are available through professional organizations and colleges.
- Take on Leadership Roles. Industrial safety officers should demonstrate leadership skills and take on supervisory roles. This may include developing safety protocols, training employees, and conducting safety audits.
You may want to check Industrial Process Operator, Industrial Refrigeration Technician, and Industrial Welder for alternative.
Job Description
- Develop and implement safety programs designed to prevent accidents and minimize risks
- Conduct safety training, safety inspections and safety audits
- Monitor compliance with safety regulations in the workplace
- Investigate accidents and incidents to identify root causes and recommend corrective action
- Oversee the installation, maintenance and use of safety equipment
- Prepare reports, presentations and other documents related to safety
- Respond to emergency situations and coordinate emergency response activities
- Develop and update emergency response plans
- Develop and implement strategies for identifying and mitigating hazards
- Monitor hazardous materials storage, handling and disposal
- Prepare and analyze safety data to identify trends and recommend improvements
- Collaborate with other departments to ensure compliance with safety regulations
Skills and Competencies to Have
- Knowledge of industrial safety laws and regulations.
- Knowledge of hazardous materials and their effects.
- Knowledge of hazard analysis and risk assessment techniques.
- Ability to develop and implement safety programs and procedures.
- Ability to conduct safety audits and inspections.
- Ability to counsel and train employees on safety practices and procedures.
- Ability to respond to and investigate accidents and incidents.
- Ability to interpret engineering drawings and schematics.
- Knowledge of hazardous waste management and disposal practices.
- Knowledge of safety equipment, supplies, and tools.
- Skill in using computers for data collection and reporting.
- Ability to communicate effectively orally and in writing.
- Strong organizational and problem solving skills.
- Ability to work independently with minimal supervision.
Industrial safety officers are responsible for ensuring the safety of workers in industrial settings. As such, it is essential that they possess a broad range of skills to enable them to effectively identify and address potential hazards. The most important skill that an industrial safety officer should possess is the ability to identify and assess the risks associated with any given environment.
This involves the application of knowledge of safety laws and regulations, as well as the use of appropriate risk assessment tools and techniques. Furthermore, industrial safety officers must have excellent communication skills in order to effectively educate and inform employees and management teams of the risks involved in their work environment. Finally, they must have the capacity to develop and implement effective strategies to mitigate risks, such as implementing safety protocols and conducting regular safety inspections.
These skills are essential in order to ensure that industrial operations are conducted in a safe and secure manner, minimizing the potential for workplace accidents and injuries.
Industrial Painter, Industrial Project Manager, and Industrial Automation Technician are related jobs you may like.
Frequent Interview Questions
- What experience do you have in risk management and hazard identification?
- Describe a situation where you had to identify and address an industrial safety hazard.
- How do you keep up with changes in safety regulations and standards?
- What measures do you take to ensure that safety protocols are being followed?
- What strategies have you implemented to reduce workplace accidents?
- How do you prioritize tasks and manage multiple projects related to safety?
- What techniques do you use to ensure that employees understand and follow safety procedures?
- How do you handle situations when safety protocols are not being followed?
- Describe a difficult safety issue you have faced and how you addressed it.
- How have you improved safety culture in past workplaces?
Common Tools in Industry
- Personal Protective Equipment (PPE). Specialized equipment worn by workers to protect against hazards in the workplace, such as gloves, face shields, hard hats, and respirators. (Eg: Hard hats for protection against falling objects).
- Safety Signs and Signals. Signs, symbols, and audible signals used to warn workers of potential hazards. (Eg: A Danger sign to indicate a hazardous area).
- Lockout/Tagout (LOTO). Procedures for disabling machinery and equipment to prevent accidental or unauthorized use. (Eg: Locking and tagging electrical panels to prevent accidental startup).
- Hazard Analysis, Risk Assessment, and Job Safety Analysis (JSA). Processes used to identify and control workplace hazards. (Eg: Conducting a job safety analysis of a work process to identify and eliminate safety risks).
- Training. Training programs to educate workers on safety and health topics. (Eg: Safety training courses on machine guarding).
- Accident Investigation. Systematic process of gathering evidence after an accident or incident to determine its cause. (Eg: Investigating a workplace injury to identify the root cause and develop corrective actions).
- Inspections. Regular inspections of the workplace to identify potential hazards and ensure compliance with safety regulations. (Eg: Inspecting machinery for loose parts or missing guards).
- Emergency Response Plans. Plans outlining procedures for responding to emergencies such as fires, hazardous material spills, and medical emergencies. (Eg: Fire evacuation plans).
Professional Organizations to Know
- American Society of Safety Professionals (ASSP)
- International Institute of Risk and Safety Management (IIRSM)
- British Safety Council (BSC)
- National Safety Council (NSC)
- American Industrial Hygiene Association (AIHA)
- National Fire Protection Association (NFPA)
- Institute of Hazardous Materials Management (IHMM)
- American Association of Occupational Health Nurses (AAOHN)
- Canadian Society of Safety Engineering (CSSE)
- International Association of Emergency Managers (IAEM)
Common Important Terms
- Hazard Analysis. The systematic process of identifying and evaluating workplace hazards to determine the risk they pose and the appropriate control measures to reduce that risk.
- Risk Assessment. The systematic evaluation of potential risks and the implementation of measures to reduce or eliminate those risks.
- Incident Investigation. The process of gathering information to determine the cause and circumstances of an incident in order to prevent future occurrences.
- Job Safety Analysis. The process of studying each job to identify hazards, assess their severity, and implement measures to reduce or eliminate the risk of injury or illness.
- Safety Training. Training provided to employees to help them understand potential hazards and how to work safely.
- Emergency Preparedness. Developing plans for responding to emergencies and training employees on how to respond appropriately.
- Personal Protective Equipment. Specialized clothing and equipment used to protect workers from hazardous conditions.
- Lockout/Tagout Procedures. Safety procedures used when working on or near energy sources to prevent accidental activation or release of hazardous energy.
- Ergonomics. The study of how people interact with their environment, including the design of processes, systems, and tools to ensure the safety and comfort of workers.
Frequently Asked Questions
What is an Industrial Safety Officer?
An Industrial Safety Officer is a professional who is responsible for developing, implementing, and monitoring safety programs to ensure the safety of personnel, property, and the environment in industrial settings.
What qualifications are required for an Industrial Safety Officer?
Industrial Safety Officers typically require a bachelor's or master's degree in safety engineering, safety management, or a related field. They may also need to hold a professional certification, such as a Certified Safety Professional (CSP) or Associate Safety Professional (ASP).
What are the main duties of an Industrial Safety Officer?
The main duties of an Industrial Safety Officer include developing and implementing safety plans, ensuring that regulatory standards are met, conducting safety audits and inspections, and providing training to personnel on safety protocols.
What safety regulations must an Industrial Safety Officer be familiar with?
Industrial Safety Officers must be familiar with safety regulations from the Occupational Safety and Health Administration (OSHA), U.S. Environmental Protection Agency (EPA), and other relevant organizations.
What skills are important for an Industrial Safety Officer?
Important skills for an Industrial Safety Officer include strong communication, problem-solving, and decision-making skills; knowledge of safety regulations; and the ability to work in a high-pressure environment.
What are jobs related with Industrial Safety Officer?
Web Resources
- Industrial Safety Iḷisaġvik College www.ilisagvik.edu
- Safety Officers - Occupational Health & Safety www.monash.edu
- Industrial Safety Courses & Universities - Leverage Edu leverageedu.com
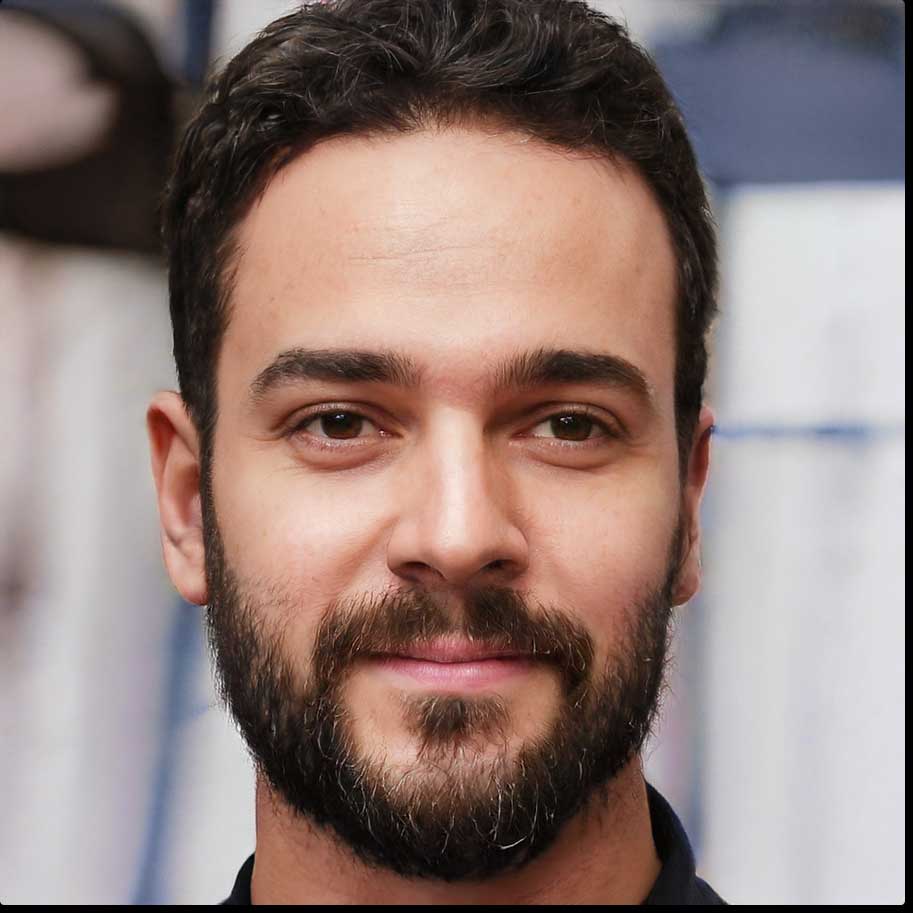