How to Be Industrial Project Manager - Job Description, Skills, and Interview Questions
Steps How to Become
- Earn a Bachelors Degree. Most industrial project managers have at least a bachelors degree in a field related to engineering, construction management, or a related field.
- Obtain Certification. Some employers may require industrial project managers to be certified in their field. It is also possible to gain certification through professional organizations such as the Project Management Institute (PMI).
- Gain Relevant Experience. Industrial project managers must have significant experience in the construction, engineering, or management fields. It is important to gain experience with industrial projects and the tools and processes associated with them.
- Develop Leadership Skills. Industrial project managers must be able to lead teams of diverse professionals and effectively manage projects from start to finish. They must be able to manage risk, delegate tasks, and resolve issues quickly.
- Stay Up to Date. The technology and processes used in industrial project management are constantly changing. Industrial project managers must stay up to date on the latest advancements in their field in order to stay competitive.
The successful completion of an industrial project requires a qualified and reliable project manager. To ensure the successful completion of an industrial project, the project manager must possess a variety of skills including strong organizational and communication skills, knowledge of relevant regulations, and the ability to manage resources, meet deadlines, and stay within budget. Furthermore, a qualified project manager should have experience in the specific industry in which the project will be taking place.
Finally, the project manager must be able to work collaboratively with all stakeholders, including team members, clients, subcontractors, and suppliers, to create a successful outcome. When a qualified and reliable project manager is chosen, the chances of completing the industrial project on time and within budget are significantly increased, making it easier to achieve success.
You may want to check Industrial Painter, Industrial Machinist, and Industrial Safety Officer for alternative.
Job Description
- Manage industrial projects from concept to completion, ensuring successful and timely delivery of projects.
- Develop and update project plans, track progress, and provide regular updates to stakeholders.
- Manage budgets, resources and timelines for industrial projects.
- Monitor project performance, identify areas of risk, and make appropriate recommendations for corrective action.
- Analyze project data and prepare comprehensive reports to keep stakeholders informed of progress.
- Develop relationships with suppliers and contractors to ensure successful project execution.
- Assess project viability and provide recommendations to improve efficiency and reduce costs.
- Liaise with relevant departments to ensure that project requirements are met.
- Ensure compliance with safety regulations and industry standards on all industrial projects.
- Provide technical guidance and training to team members and contractors as needed.
Skills and Competencies to Have
- Excellent communication and interpersonal skills
- Knowledge of project management tools, processes and techniques
- High level of organizational skills
- Ability to multi-task, prioritize and manage time effectively
- Problem-solving skills
- Negotiation and conflict-resolution skills
- Ability to work under pressure and meet tight deadlines
- Knowledge of safety regulations and procedures
- Knowledge of budgeting and cost control
- Ability to lead and motivate a team
- Ability to think creatively and develop innovative solutions
- Understanding of industrial regulations and standards
- Knowledge of the companys products and services
- Ability to work with cross-functional teams
- Ability to develop and implement project plans
- Knowledge of relevant industry sectors and markets
Being a successful Industrial Project Manager requires a set of specific skills and knowledge, as well as exemplary leadership abilities. One of the most important skills for an Industrial Project Manager to possess is the ability to effectively manage people and resources. This includes the ability to create and implement plans, allocate resources, meet deadlines, and ensure that all team members are working together cohesively to achieve the desired results.
Furthermore, an Industrial Project Manager must be able to effectively communicate and collaborate with stakeholders, clearly explain objectives and tasks, and make sure that everyone is on the same page when it comes to the project. strong problem-solving skills are necessary, as well as the ability to analyze data and make informed decisions. Finally, an Industrial Project Manager needs to have a good understanding of the industry they are working in, allowing them to anticipate potential risks or issues and address them as needed.
All of these skills, combined with effective leadership, are essential for a successful Industrial Project Manager.
Industrial Quality Inspector, Industrial Process Operator, and Industrial Refrigeration Technician are related jobs you may like.
Frequent Interview Questions
- What experience do you have managing industrial projects?
- How do you prioritize tasks in a complex project?
- Describe a successful project you managed from start to finish.
- What strategies do you use to ensure deadlines are met?
- How do you motivate a team to complete challenging tasks?
- How do you handle difficult stakeholders or situations?
- What is your experience with budgeting and cost management?
- What safety protocols do you follow when managing industrial projects?
- How do you ensure that quality control standards are met during a project?
- What experience do you have using project management software?
Common Tools in Industry
- Project Management Software. A software system designed to help project managers plan, monitor, and control their projects. (e. g. Microsoft Project)
- Gantt Chart Software. A software application used to create a visual representation of project schedules. (e. g. TeamGantt)
- Risk Management Software. A software system used to identify, analyze, and manage project risks. (e. g. RiskyProject)
- Cost Estimation Software. A software system used to estimate the cost of a project. (e. g. Costimator)
- Resource Allocation Software. A software system used to allocate resources for a project. (e. g. Float)
- Collaboration Tools. A set of tools and applications used to facilitate communication and collaboration among team members. (e. g. Slack, Trello)
- Task Management Software. A software system used to plan and track tasks within a project. (e. g. Asana)
- Quality Management Software. A software system used to ensure that a project meets its quality requirements. (e. g. Qualityze)
- Data Analysis Software. A software system used to analyze and visualize data related to a project (e. g. Tableau)
Professional Organizations to Know
- Project Management Institute (PMI)
- Association for Project Management (APM)
- International Association of Project and Program Management (IAPPM)
- American Association of Cost Engineers (AACE)
- Institute of Industrial and Systems Engineers (IISE)
- International Society for Quality in Health Care (ISQua)
- International Project Management Association (IPMA)
- Society of Construction Law (SCL)
- Institute of Electrical and Electronics Engineers (IEEE)
- National Institute of Building Sciences (NIBS)
Common Important Terms
- Project Scope. The project scope is the set of activities required to deliver a product or service within a given time frame. It includes the resources and tools needed, the timeline for completion, and any constraints or assumptions associated with the project.
- Project Plan. The project plan is a document that describes the tasks, resources, and timeline for completing a project. It is created before the project begins and helps to keep the project on track.
- Risk Management. Risk management is the process of identifying, assessing, and responding to potential risks before they become problems. This includes identifying potential risks, evaluating their impact, developing strategies to mitigate them, and monitoring their progress.
- Stakeholder Management. Stakeholder management is the process of managing relationships between stakeholders in order to ensure that their interests are taken into account during the project. This includes understanding stakeholders needs and expectations, communicating with them throughout the project, and resolving any conflicts that arise.
- Change Management. Change management is the process of managing changes to the project plan during its execution. This includes identifying changes, assessing their impact, developing strategies to implement them, and communicating them to stakeholders.
Frequently Asked Questions
What are the primary responsibilities of an Industrial Project Manager?
The primary responsibilities of an Industrial Project Manager include leading teams in the development and implementation of industrial projects, overseeing project budgets, scheduling resources, and ensuring completion of projects on time and within budget.
What qualifications are needed to become an Industrial Project Manager?
To become an Industrial Project Manager, one typically needs a bachelors degree in engineering, business, or a related field. Additionally, experience in project management and a knowledge of industrial processes is required.
What type of environment does an Industrial Project Manager typically work in?
An Industrial Project Manager typically works in a manufacturing or industrial setting, such as a factory, warehouse, or production facility.
How much can an Industrial Project Manager expect to earn?
According to salary data from PayScale, the median annual salary for an Industrial Project Manager is $77,898.
What tools and technologies do Industrial Project Managers typically use?
Industrial Project Managers typically use project management software such as Microsoft Project, ERP systems such as SAP, and industrial automation tools such as PLCs and HMI software.
What are jobs related with Industrial Project Manager?
Web Resources
- What Does a Project Manager Do? | Roles and Responsibilities www.northeastern.edu
- BS in Industrial Management | University Of Cincinnati business.uc.edu
- Project Manager - Stanford University Careers careersearch.stanford.edu
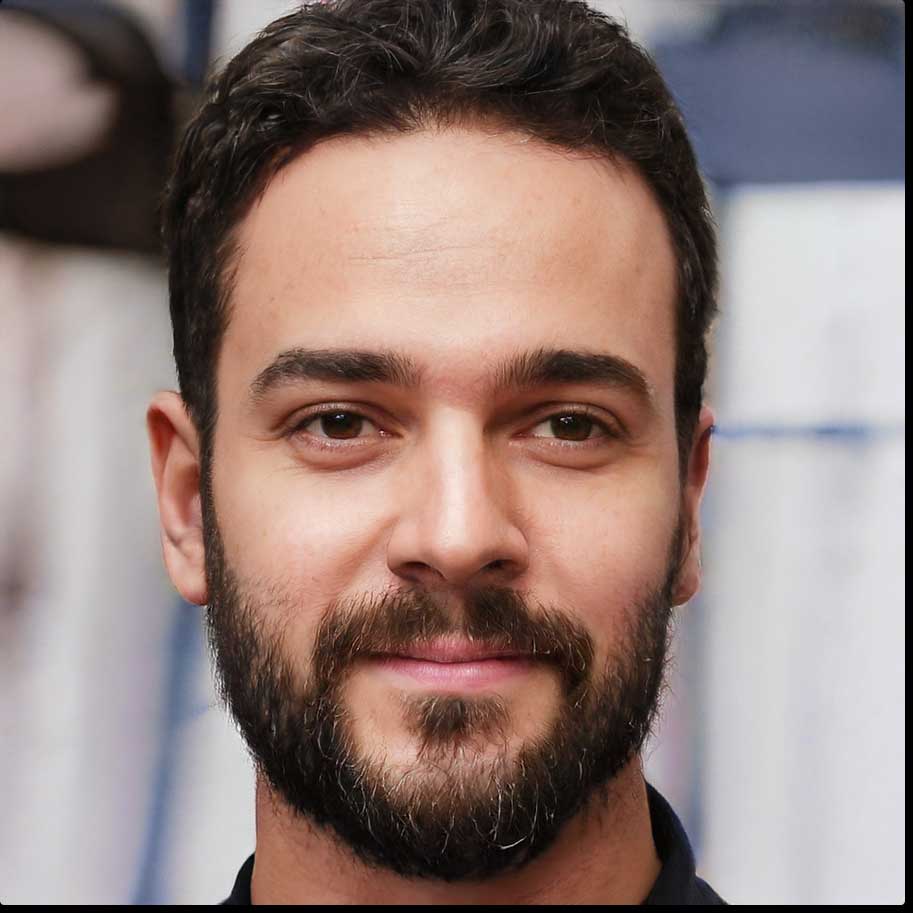