How to Be Industrial Quality Inspector - Job Description, Skills, and Interview Questions
Industrial quality inspection is a crucial step in the manufacturing process which helps to ensure that the end product meets the standards of quality that it was designed for. Poor quality inspection can cause a number of issues, such as customer dissatisfaction, increased warranty costs, and decreased revenue. In order to prevent these issues, it is essential that an industrial quality inspector evaluates the product for accuracy and defects.
This evaluation typically includes taking measurements, testing materials, and conducting a visual inspection. If any problems are identified, the inspector can suggest corrective actions that need to be taken in order to meet the desired quality standards. By utilizing such practices, companies can ensure they are producing high-quality products that meet the needs of their customers.
Steps How to Become
- Obtain a High School Diploma or GED. Most employers require industrial quality inspectors to possess a high school diploma or its equivalent.
- Complete a Postsecondary Program. Industrial quality inspectors may enroll in a postsecondary program to gain skills in math, science and quality assurance.
- Gain On-the-Job Experience. Employers may require industrial quality inspectors to have several years of experience in a related field.
- Obtain Certification. Professional certification is not required for industrial quality inspectors, but it can demonstrate knowledge and proficiency in the field.
- Seek Employment. Industrial quality inspectors can find open positions through job search websites and classified ads in local newspapers. They may also contact employers directly to inquire about open positions.
The importance of having a reliable and competent industrial quality inspector cannot be overstated. High quality and safety standards are essential for the success of any industrial operation, and a qualified inspector is the key to ensuring these standards are met. Poor quality control can lead to costly losses in terms of both time and money, and can even result in serious injuries or fatalities.
A reliable and competent industrial quality inspector will be able to spot any potential issues before they become major problems, thereby reducing the risk of costly incidents. They will also be able to provide valuable feedback on the effectiveness of safety measures being adopted by the organization, helping to improve operations and ensure compliance with relevant regulations.
You may want to check Industrial Painter, Industrial Refrigeration Technician, and Industrial Project Manager for alternative.
Job Description
- Perform detailed visual, dimensional and functional inspections of production parts and assemblies.
- Inspect parts and assemblies for compliance with customer drawings and specifications.
- Utilize precision measuring tools such as calipers, gauges, and micrometers to ensure product accuracy.
- Identify, document and report defects, non-conformances and areas of improvement.
- Maintain records of inspection results and provide reports to management.
- Participate in continuous improvement initiatives to ensure processes are maintained at highest quality standards.
- Collaborate with other departments to ensure quality standards are met.
- Ensure that all safety procedures are followed in the production area.
- Monitor and adjust production processes to ensure product quality is maintained.
- Troubleshoot quality related issues and work to resolve them in a timely manner.
Skills and Competencies to Have
- Attention to Detail
- Technical Knowledge
- Problem-Solving Skills
- Analytical Skills
- Computer Proficiency
- Documentation Skills
- Communication Skills
- Teamwork Skills
- Time Management
- Math Skills
- Quality Control Procedures
- Quality Assurance Procedures
- Knowledge of Statistical Process Control
- Knowledge of Metrology Principles
- Knowledge of Inspection Tools and Techniques
- Understanding of Manufacturing Processes
- Ability to Interpret Drawings and Specifications
- Ability to Interpret Technical Data
- Ability to Interpret Quality Standards
- Ability to Read and Understand Technical Documents
The success of an Industrial Quality Inspector is highly dependent on their ability to possess a number of key skills. Attention to detail and problem solving are two of the most important skills needed to be successful in this role. By carefully examining the quality of materials, components and products, potential issues can be identified early, allowing for quick and efficient problem solving.
An Industrial Quality Inspector needs to be able to anticipate potential issues and come up with innovative solutions. a keen eye for detail and the ability to work with precision and accuracy are essential, as any mistakes can have serious consequences. Furthermore, having good communication and interpersonal skills to explain complex issues to other members of the team is also essential.
With these skills, an Industrial Quality Inspector can ensure that the finished product meets the highest standards and that no defects are present.
Industrial Machinist, Industrial Safety Officer, and Industrial Automation Technician are related jobs you may like.
Frequent Interview Questions
- What experience do you have with quality control systems?
- How do you stay up-to-date on industry standards and regulations?
- What methods do you use to identify and measure process performance?
- Describe your experience in performing quality inspections.
- What is your approach to training employees to understand and adhere to quality standards?
- What strategies do you use for ensuring that products meet customer expectations?
- How do you ensure accurate and consistent documentation of quality inspections?
- How would you handle a situation where a product does not meet the required quality standards?
- What techniques do you use for root cause analysis of quality issues?
- How do you handle difficult feedback from customers about product quality?
Common Tools in Industry
- Calipers. Used to measure the internal and external dimensions of a part or object. (eg: measuring the diameter of a cylinder)
- Micrometers. Used to accurately measure small distances. (eg: measuring the thickness of a sheet of metal)
- Gauges. Used to measure the size and shape of an object. (eg: measuring the depth of a hole)
- Vision Systems. Automated systems incorporating cameras and software to inspect parts for defects or inconsistencies. (eg: inspecting a circuit board for cracks and other defects)
- Force Gauges. Used to measure the force or tension exerted by a material or object. (eg: measuring the tension on a screw or bolt)
- X-Ray Machines. Used to inspect objects for internal defects that may not be visible on the surface. (eg: inspecting a welded joint for cracks or other flaws)
- Ultrasonic Testing Equipment. Used to detect flaws in materials by sending sound waves through them and measuring the amount of time it takes for the sound waves to bounce back. (eg: inspecting a cast iron pipe for cracks)
- Magnetic Particle Testing Equipment. Uses magnetic fields to detect surface and subsurface flaws in metal objects. (eg: inspecting a gear for cracks or other defects)
Professional Organizations to Know
- American Society for Quality (ASQ)
- International Society of Automation (ISA)
- Quality Control Institute (QCI)
- American Welding Society (AWS)
- Society of Quality Engineers (SQE)
- Institute of Industrial and Systems Engineers (IISE)
- American Society for Testing and Materials (ASTM)
- International Association for Six Sigma Certification (IASSC)
- National Institute of Standards and Technology (NIST)
- The British Quality Foundation (BQF)
Common Important Terms
- Quality Assurance (QA). A systematic approach to ensuring that products and services meet standards of quality established by a company or industry.
- Quality Control (QC). The process of verifying that a product or service meets predetermined standards of quality.
- Metrology. The science of measurement, including the study of instruments and techniques used to accurately measure physical quantities.
- Calibration. The process of adjusting a measuring instrument to indicate a known value.
- Statistical Process Control (SPC). A quality control method that uses statistical analysis to monitor and control a process.
- Risk Management. The process of minimizing potential losses through effective planning and decision-making.
- Inspection. A close examination of a product or service for the purpose of evaluating its quality or condition.
- Non-destructive Testing (NDT). A technique used to examine a product or material without causing damage or harm.
- Traceability. The ability to trace the origin or history of a product or service.
Frequently Asked Questions
What is the job of an Industrial Quality Inspector?
An Industrial Quality Inspector is responsible for inspecting and testing products, materials and components to ensure they meet the required quality standards.
What skills are needed to be an Industrial Quality Inspector?
An Industrial Quality Inspector needs to have strong attention to detail and excellent problem-solving skills, as well as good communication and organizational skills. They should also be familiar with relevant industry standards and regulations.
What is the average salary for an Industrial Quality Inspector?
The average salary for an Industrial Quality Inspector is approximately $45,000 per year.
What qualifications are needed to be an Industrial Quality Inspector?
Generally, Industrial Quality Inspectors need to have a high school diploma or equivalent, although some employers may require additional qualifications such as a diploma or degree in a related field.
What are the duties of an Industrial Quality Inspector?
The primary duties of an Industrial Quality Inspector include inspecting and testing products and components, ensuring they meet the required quality standards; recording and reporting any defects; and providing feedback to management on any quality issues.
What are jobs related with Industrial Quality Inspector?
Web Resources
- Online Quality Inspector from Arkansas State University ed2go.degree.astate.edu
- Quality Inspector - Anoka Tech anokatech.edu
- Industrial Instrumentation | (877) 211-7165 iticollege.edu
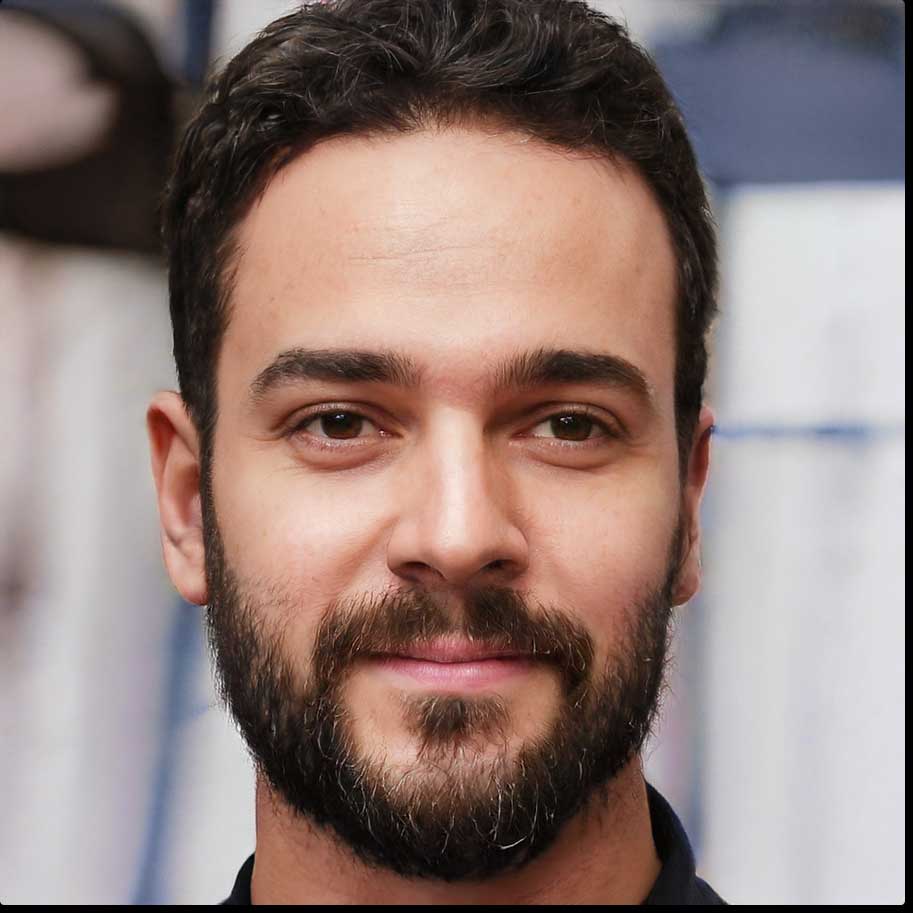