How to Be Mining Equipment Operator - Job Description, Skills, and Interview Questions
Mining equipment operators are responsible for the safe and efficient operation of the equipment used to extract valuable minerals and metals from the earth. The operator must be highly skilled in the operation of the machinery, as it can cause serious safety concerns and environmental damage if operated incorrectly. The operator must be able to follow safety protocols, as well as operate and maintain the equipment in accordance with manufacturer guidelines.
The major cause behind these responsibilities is to ensure that the extraction process is done in an environmentally friendly manner, whilst also minimizing any risks associated with the operation. The effects of this responsibility are beneficial for both the environment and the mining industry, as the equipment operators can help reduce waste, control dust and noise pollution, and prevent damage to land from mining activities.
Steps How to Become
- Obtain a high school diploma or equivalent. Mining equipment operators typically need a high school diploma or equivalent to enter the field.
- Enroll in post-secondary education. Though not required, many mining equipment operators enroll in a post-secondary program in mining technology or heavy equipment operations.
- Obtain on-the-job training. Most mining equipment operators learn their skills on the job through a combination of classroom instruction and hands-on experience.
- Get certified. Many employers require mining equipment operators to be certified in heavy equipment operation. Organizations like the National Commission for the Certification of Crane Operators (NCCCO) and the Mine Safety and Health Administration (MSHA) offer certification programs for various types of heavy machinery.
- Consider pursuing additional certifications. Obtaining additional certifications, such as those offered by the National Association of Heavy Equipment Training Schools (NAHETS) or the Association of Equipment Manufacturers (AEM), can also help to make a mining equipment operator more competitive in the job market.
Staying ahead and efficient as a Mining Equipment Operator requires dedication, knowledge and practice. To ensure success, miners should stay up to date with advances in the field, make sure their equipment is properly maintained and serviced, and practice safety protocols. Keeping up with industry trends and developments ensures that miners are familiar with the latest technology, enabling them to make informed decisions about the best way to operate their equipment.
Keeping equipment well maintained is key to efficient operations, as worn or damaged parts can cause operational problems and lead to hazardous situations. miners should always adhere to safety protocols, such as wearing personal protective equipment and maintaining a clean workspace, to prevent accidents and injuries. With these practices in place, Mining Equipment Operators can remain ahead of the curve and remain efficient in their operations.
You may want to check Mine Automation Engineer, Mining Production Manager, and Mining Logistics Coordinator for alternative.
Job Description
- Load-Haul-Dump (LHD) Operator: Responsible for operating underground mining vehicle to transport ore and other materials to designated areas.
- Driller: Responsible for drilling holes into the earth to facilitate the extraction of ore.
- Crusher Operator: Responsible for operating and maintaining crushers and related equipment used to crush and grind ore.
- Shovel Operator: Responsible for operating large power shovels to move and load ore, waste materials, and rock.
- Haul Truck Driver: Responsible for operating large haul trucks to transport ore, waste materials, and rock from the mining site.
- Maintenance Technician: Responsible for conducting repairs and maintenance on mining equipment.
- Tugger Operator: Responsible for operating tuggers to move heavy equipment or supplies around the mining site.
- Blasting Technician: Responsible for setting explosives and conducting blasting operations in order to loosen ore and rock for extraction.
Skills and Competencies to Have
- Knowledge of mining processes, procedures, and regulations
- Familiarity with the operation of heavy machinery and vehicles used in mining
- Ability to read and interpret blueprints, technical diagrams, and other operational instructions
- Ability to accurately measure and calculate distances, depths, and weights
- Excellent communication and interpersonal skills
- Ability to interpret safety guidelines and follow safety protocols
- Ability to identify and address problems quickly and efficiently
- Ability to work in a physically demanding environment
- Ability to work long hours in sometimes hazardous conditions
- Attention to detail and accuracy in completing tasks
The ability to operate mining equipment safely and efficiently is essential for success as a mining equipment operator. This requires a combination of technical knowledge, problem solving skills, and physical strength. Technical knowledge is important to understand the different functions and features of the equipment and to be able to diagnose and resolve any issues that may arise.
Problem solving skills are necessary to be able to identify hazardous situations and find solutions to prevent them from becoming a danger to workers and equipment. Physical strength is important to be able to move and control the heavy machinery. All these skills are essential for a successful mining equipment operator and help ensure that the process runs safely and smoothly.
Mining Data Analyst, Mine Operations Manager, and Mining Reclamation Specialist are related jobs you may like.
Frequent Interview Questions
- How would you describe your experience operating mining equipment?
- What safety protocols do you follow when operating mining equipment?
- How do you troubleshoot common problems with mining equipment?
- Tell me about a time when you had to make a quick decision when operating mining equipment.
- What steps do you take to ensure the mining equipment is properly maintained?
- Describe a time when you had to complete a difficult project involving mining equipment.
- How do you ensure that the mining equipment is working in a safe and efficient manner?
- What techniques do you use to maximize the productivity of mining equipment?
- What experience do you have working with remote or automated mining equipment?
- How do you handle the pressure of operating mining equipment in challenging or hazardous environments?
Common Tools in Industry
- Loader. A heavy-duty machine used to move large amounts of material such as dirt, rocks, sand, and coal. (eg: Cat 994F Wheel Loader)
- Haul Truck. A large vehicle used to transport materials from one location to another. (eg: Volvo A35F Haul Truck)
- Excavator. A machine used to dig, scoop, and lift materials. (eg: Hitachi ZX135US-6 Excavator)
- Dozer. A large tracked vehicle used to push or pull materials such as dirt, rocks, and coal. (eg: Cat D9T Dozer)
- Rock Breaker. A powerful machine used to break apart large rocks. (eg: Sandvik MB750 Rock Breaker)
- Grader. A machine used to create a flat surface or smooth out rough terrain. (eg: Cat 140M Grader)
- Drilling Rig. A machine used to bore holes into the earth in order to extract minerals or materials. (eg: Atlas Copco T35 Drilling Rig)
- Blasting Machine. A device used to detonate explosives in order to break apart rock and other materials. (eg: Dyno Nobel E-Max Blasting Machine)
- Air Compressor. A machine which pumps air at high pressure in order to power pneumatic tools. (eg: Sullair 375H Air Compressor)
- Pumps. A machine which transfers fluids from one place to another using pressure. (eg: Gorman-Rupp T Series Pump)
Professional Organizations to Know
- National Mining Association (NMA)
- Association of Equipment Manufacturers (AEM)
- National Stone, Sand & Gravel Association (NSSGA)
- Society for Mining, Metallurgy & Exploration (SME)
- American Exploration & Mining Association (AEMA)
- United Steelworkers (USW)
- International Union of Operating Engineers (IUOE)
- National Institute for Occupational Safety and Health (NIOSH)
- National Safety Council (NSC)
- Institute of Makers of Explosives (IME)
We also have Mining Sales Representative, Mining Cost Accountant, and Mining Machinist jobs reports.
Common Important Terms
- Dragline. A large excavating machine used in surface mining to remove soil and rock overburden covering mineral deposits.
- Haul Truck. A large vehicle used in mining operations to transport ore, overburden, and waste from the mine to the processing plant.
- Shovel. A type of machine used in mining operations to move and dig up material such as earth, ore, and coal.
- Dredge. A machine used to remove sediment from the bottom of a body of water by means of suction or scooping.
- Dozer. A large, tracked vehicle used to move material in mining operations, typically to clear vegetation and other obstructions.
- Loader/Unloader. A machine used in mining operations to move ore, overburden, and waste from one location to another.
- Conveyor Belt. A system of belts and pulleys used to transport materials in mining operations.
- Hoist. A type of machine used in mining operations to raise and lower materials.
- Jackhammer. A type of tool used to break up hard surfaces, such as rock.
- Drill. A type of machine used to drill holes into the ground for various purposes such as ventilating mines or creating tunnels.
Frequently Asked Questions
What is the average salary of a Mining Equipment Operator?
The average salary of a Mining Equipment Operator is approximately $50,000 per year.
What type of equipment do Mining Equipment Operators typically use?
Mining Equipment Operators typically use excavators, haul trucks, bulldozers, graders, and other heavy machinery to move and process materials.
What qualifications are necessary to become a Mining Equipment Operator?
In order to become a Mining Equipment Operator, individuals must typically have a high school diploma or GED and complete on-the-job training.
What are the primary job duties of a Mining Equipment Operator?
The primary job duties of a Mining Equipment Operator are operating and maintaining equipment, adhering to safety regulations, and performing routine maintenance and inspections.
What safety measures do Mining Equipment Operators need to take?
Mining Equipment Operators need to take safety measures such as following safety protocols and regulations, wearing protective gear, and operating equipment in a safe and responsible manner.
What are jobs related with Mining Equipment Operator?
- Mining Hydraulic Engineer
- Mining Inspector
- Mining Project Manager
- Mining Supervisor
- Mining Regulatory Compliance Officer
- Mining Materials Engineer
- Mining Health and Safety Officer
- Mining Business Analyst
- Mining Metallurgist
- Mining Logistics Manager
Web Resources
- Heavy Equipment Operator Training - Workforce ¦ www.vinu.edu
- Mining Mill Op - University of Alaska Fairbanks mirl.uaf.edu
- Heavy Equipment Operator (AAS) - Central Arizona ¦ centralaz.edu
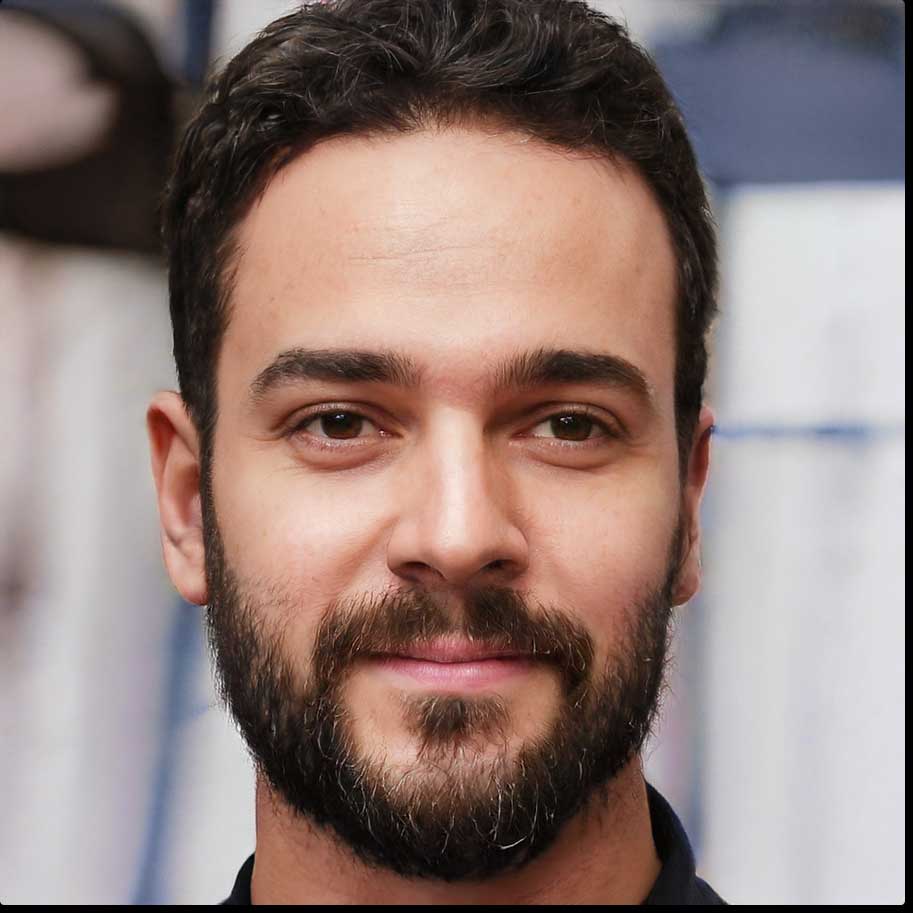