How to Be Factory Worker - Job Description, Skills, and Interview Questions
Factory workers have an important role in the production of goods and services, as they are responsible for a variety of tasks such as assembly, packaging, and quality control. As a result, factory workers often work long hours in order to meet production demands and deadlines. This can lead to fatigue, stress, and mental exhaustion, which can have a negative impact on their overall health and wellbeing.
factory workers often face dangerous working conditions, such as exposure to hazardous materials, loud noises, and extreme temperatures. This can lead to physical health issues such as respiratory illnesses, hearing loss, and fatigue. poor ergonomic conditions can also lead to musculoskeletal pain and discomfort.
Therefore, it is important for employers to ensure that factory workers are provided with a safe and healthy work environment in order to protect their wellbeing and ensure their productivity.
Steps How to Become
- Obtain a High School Diploma or GED. Most employers will require a high school diploma or GED for entry-level factory worker positions.
- Research Factory Worker Opportunities. Research local and online job postings to find opportunities for factory workers.
- Gain Experience. Most factory worker jobs require at least some minimal experience in a related field. Consider volunteering or getting an internship in a factory setting to gain experience.
- Complete Training and Safety Courses. Many factories will require new hires to complete safety and training courses upon hiring.
- Apply to Factory Worker Positions. Use your network of contacts, job boards, and recruiters to apply to available factory worker positions. Be sure to emphasize your experience and safety training in your cover letter and resume.
- Participate in the Interview Process. Prepare for the interview process by researching the company and practicing answers to commonly asked questions.
- Accept a Position. If offered a position, be sure to read the job offer and contract carefully before signing. This will ensure that you understand the expectations of the job and your rights as an employee.
Factory workers are essential to the smooth running of production processes. The lack of competent and ideal factory workers can have a negative effect on production, leading to delays, missed deadlines, and diminished quality. Poorly trained workers can also cause accidents, resulting in injury, lost time, and higher insurance costs.
On the other hand, a factory staffed with competent and ideal workers can lead to higher production quality, more efficient operations, and greater customer satisfaction. To ensure a safe and productive work environment, it is important that factory workers receive proper training and instruction in the safety protocols and production techniques required for the job. A well-trained staff also enables managers to make timely decisions and adjustments when necessary, while providing the workers with an environment that fosters productivity and encourages a positive work ethic.
You may want to check Forestry Worker, Cleaning Worker, and Packaging Worker for alternative.
Job Description
- Examine and inspect product to ensure quality and conformance to specifications
- Operate machinery and equipment as directed
- Pack, label and organize products for shipment
- Monitor production process and report any issues
- Maintain a clean and safe work environment
- Follow instructions from supervisors and adhere to safety regulations
- Load and unload materials from production or storage areas
- Assemble items according to specifications
- Sort, count, and record items processed
- Troubleshoot production issues and make necessary repairs or adjustments
Skills and Competencies to Have
- Ability to follow instructions accurately.
- Ability to work independently and in teams.
- Ability to learn quickly and efficiently.
- Knowledge of basic safety procedures.
- Strong attention to detail.
- Physical stamina and strength.
- Good hand-eye coordination.
- Solid problem-solving skills.
- Ability to work in a fast-paced environment.
- Proven ability to adhere to quality standards.
The ability to work well as a team is an essential skill for any factory worker. When a factory operates efficiently, it can increase production and create a higher quality product. When workers are able to collaborate effectively and communicate openly, they can quickly identify problem areas and improve processes.
having a basic understanding of safety regulations and being able to follow safety protocols will ensure a safe and healthy work environment. Strong problem-solving skills are also important, as workers must be able to identify and address any potential issues in order to keep the factory running smoothly. Finally, having good organizational skills and the ability to multitask will help factory workers stay on top of their tasks and ensure that deadlines are met.
Maintenance Worker, Process Worker, and Machine Worker are related jobs you may like.
Frequent Interview Questions
- What experience do you have in a factory setting?
- What type of machinery are you most familiar with?
- What safety measures do you take when working on the production line?
- How do you handle working with hazardous materials?
- What strategies do you use to ensure quality control standards are met?
- How do you prioritize tasks to meet tight deadlines?
- How do you collaborate with management and other team members?
- Describe a time when you had to troubleshoot a problem on the production line.
- Do you have any experience with computerized equipment or robotics?
- What is your approach to problem-solving and decision-making in a production environment?
Common Tools in Industry
- Forklift. A vehicle used to move heavy items around a factory floor. (eg: moving pallets of raw materials from the warehouse to the production line)
- Hand Tools. Small tools used for manual tasks such as cutting, drilling and fastening. (eg: screwdrivers, hammers, saws, etc. )
- Machine Tools. Machines used to shape and cut metal and other materials. (eg: lathes, milling machines, grinders, etc. )
- Programmable Logic Controllers (PLCs). Computers used to control machines and automate processes. (eg: controlling the speed of an assembly line or monitoring temperature in a furnace)
- Robotics. Automated machines used to perform tasks that would otherwise be done by humans. (eg: welding car parts together or packing boxes on an assembly line)
Professional Organizations to Know
- National Council for Workforce Education
- American Society for Training and Development
- National Association of Manufacturers
- International Association of Machinists and Aerospace Workers
- National Institute for Occupational Safety and Health
- National Employment Law Project
- National Institute of Occupational Safety and Health
- American Federation of Labor and Congress of Industrial Organizations
- International Brotherhood of Teamsters
- United Food and Commercial Workers International Union
We also have Heavy Equipment Operator Worker, Welding Worker, and Laborer Worker jobs reports.
Common Important Terms
- Manufacturing. the process of producing goods from raw materials or components.
- Quality Control. The process of ensuring that products meet certain standards set by the company.
- Assembly Line. A system of production where workers perform specific tasks in a specific order to produce a finished product.
- Machine Operator. A person who operates and maintains factory machines.
- Logistics. The management of the flow of goods and services from the point of origin to the point of consumption.
- Safety Standards. Regulations and guidelines set by a company to ensure workers are protected from harm while on the job.
- PPE (Personal Protective Equipment). Clothing, headgear, and other items worn by workers to protect them from potential hazards in the workplace.
- Hazardous Materials. Substances that can be harmful to people, property, and the environment if not handled or stored properly.
- Inventory Management. The process of tracking and managing the flow of materials and products in a factory.
- Maintenance Technician. An employee in charge of inspecting, repairing and maintaining factory machinery.
Frequently Asked Questions
What are the typical duties of a Factory Worker?
The typical duties of a Factory Worker include operating machinery, assembling products, packaging items, inspecting products, and ensuring quality control standards are met.
What qualifications are necessary to become a Factory Worker?
Qualifications necessary to become a Factory Worker vary depending on the position and the company, but typically include a high school diploma or GED, training in operating machinery, and knowledge of quality control standards.
How many hours does a Factory Worker typically work?
A Factory Worker typically works 8-hour shifts, but may have to work overtime or weekends if production needs require it.
What safety protocols should a Factory Worker adhere to?
Factory Workers should adhere to safety protocols such as wearing protective gear, following proper machine operating procedures, and adhering to all safety regulations.
What is the average annual salary for a Factory Worker?
The average annual salary for a Factory Worker is approximately $30,000 - $35,000.
What are jobs related with Factory Worker?
- Plant Worker
- Warehouse Associate Worker
- Packer/Picker Worker
- Fabrication Worker
- Carpenter/Furniture Maker Worker
- Installation Worker
- Technician Worker
- Warehouse Worker
- Warehouse Manager Worker
- Material Handler Worker
Web Resources
- Factory to the Workers - CLEO cleo.rutgers.edu
- Factory Workers Who Fought Back | BU Today | Boston University www.bu.edu
- Factory workers across the U.S. say they were exposed to ¦ health.wusf.usf.edu
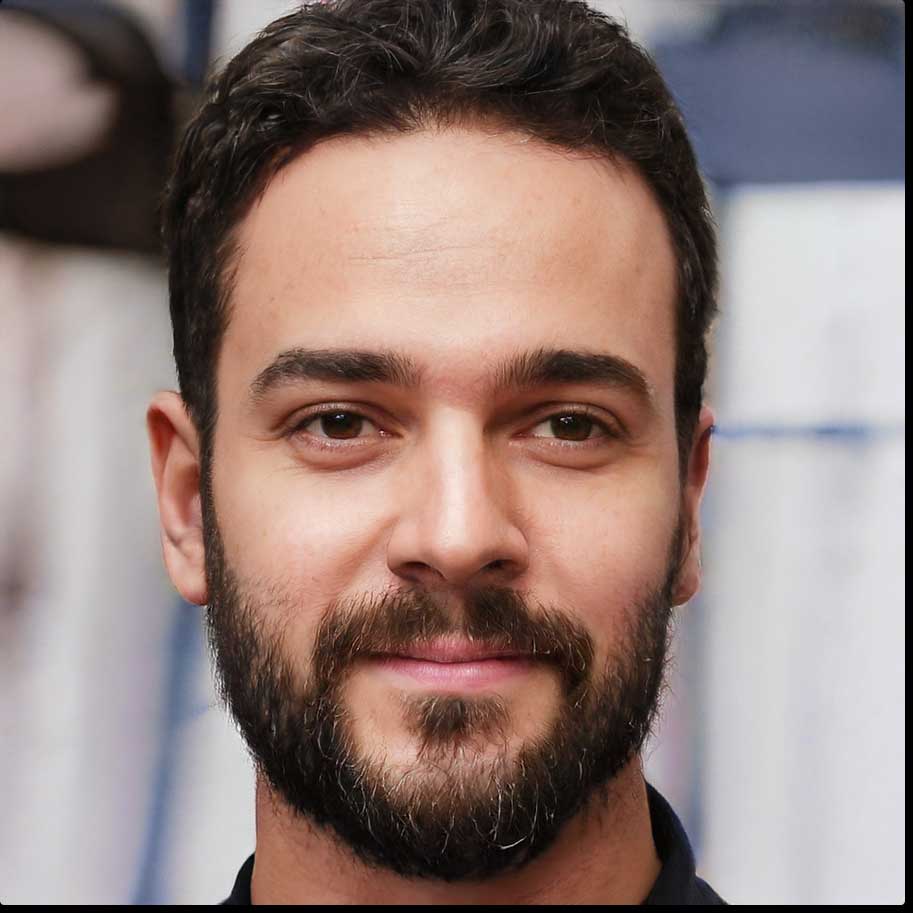