How to Be Welding Worker - Job Description, Skills, and Interview Questions
Welding is an essential process in many industries, and welding workers are a necessary part of the workforce. A skilled welder has a number of responsibilities, including reading blueprints and diagrams to determine the correct welding process, setting up and preparing welding equipment, and monitoring the welds to ensure they meet quality standards. The quality of the weld is critical, as any mistakes can lead to costly delays and repairs.
In addition, welding workers must take safety precautions while operating their equipment, as the process involves intense heat and hazardous fumes. With proper training and experience, welding workers can become an invaluable asset to any organization, providing precision and quality workmanship.
Steps How to Become
- Obtain a High School Diploma or GED. Most employers require welding workers to have a high school diploma or GED. There are some welding trade schools that may accept applicants without a high school diploma or GED.
- Complete an Apprenticeship Program. Many welding workers, particularly those that specialize in industrial and structural welding, begin their careers by completing an apprenticeship program. These programs combine on-the-job training with classroom instruction and typically last for two or three years.
- Earn a Certificate or Associate Degree. Depending on the type of welding job you are seeking, you may need to earn a certificate or associate degree in welding technology. These programs typically last one year or two years, respectively.
- Obtain Certification. The American Welding Society offers certification for welders at various levels. To obtain certification, you must pass a written test and demonstrate your skills on a welding test.
- Gain Experience. Most employers prefer to hire welders who have at least two years of experience in the field. You can gain experience by working as an apprentice, volunteering at a local shop, or taking on odd jobs.
Welding is a vital skill in many industrial and manufacturing fields, and reliable and efficient welders are essential for the successful completion of a wide range of projects. To become a reliable and efficient welder, it is important to first have a thorough understanding of the welding process and the associated safety precautions. Properly maintaining and calibrating equipment is also critical, as this helps to ensure that the welds are strong and consistent.
having a steady hand, good eye-hand coordination, and strong concentration skills are all important for producing high-quality welds. Finally, investing in the right materials and protective gear for the job is also important for both safety and efficiency. By adhering to these guidelines, welders can become reliable and efficient professionals.
You may want to check Warehouse Associate Worker, Landscaping Worker, and Machine Worker for alternative.
Job Description
- Operate welding equipment to weld metal components together in accordance with blueprints and specifications.
- Position and clamp together component parts of metal objects prior to welding.
- Grind and smooth metal surfaces to be joined.
- Monitor the fitting, burning, and welding processes to avoid overheating of parts or warping, shrinking, distortion, or expansion of material.
- Inspect completed work for conformance to specifications.
- Operate manual and/or semi-automatic welding equipment to fuse metal segments, using processes such as gas tungsten arc, gas metal arc, flux-cored arc, plasma arc, shielded metal arc, and submerged arc welding.
- Select and install torches, torch tips, filler rods, and flux, according to welding chart specifications or types and thicknesses of metals.
- Analyze engineering drawings and specifications to plan layout, assembly, or welding operations.
- Weld components in flat, vertical, or overhead positions.
- Prepare and maintain detailed records and reports of work activities.
Skills and Competencies to Have
- Ability to read and interpret blueprints, welding symbols and technical drawings
- Knowledge of welding techniques, tools and processes
- Working knowledge of safety protocols when welding
- Ability to use oxy-acetylene and electric arc welding equipment
- Proficiency in MIG, TIG and stick welding
- Ability to use grinders, drills and other metalworking tools
- Good manual dexterity and eye-hand coordination
- Ability to work with a variety of metals, including aluminum and stainless steel
- Ability to be detail-oriented and precise in quality control
- Good communication skills for working on a team
Welding workers must possess a variety of skills in order to be successful. The most important skill for a welding worker is the ability to read and interpret blueprints. This skill allows the worker to understand the specifications of a project and determine the best way to complete it.
Furthermore, welding workers must also have a strong understanding of the different types of welding techniques, such as oxy-fuel, MIG, and TIG welding. They must also possess a good working knowledge of the materials they are working with and the processes that are required to complete the work efficiently. Lastly, welders must have the ability to safely operate welding machines and equipment to ensure that the welds are completed correctly and safely.
With these skills, a welding worker can confidently complete any welding project and produce high-quality results.
Janitorial Worker, Heavy Equipment Operator Worker, and Maintenance Worker are related jobs you may like.
Frequent Interview Questions
- What experience do you have in welding?
- Describe a welding project you have completed.
- What type of welding equipment are you most familiar with?
- Do you have any certifications or qualifications in welding?
- Are you familiar with safety protocols related to welding?
- How do you stay up to date with the latest welding techniques?
- What welding processes have you used in the past?
- Are you comfortable working with different metals and alloys?
- Describe a situation where you had to troubleshoot a welding issue.
- What challenges have you faced while welding and how did you address them?
Common Tools in Industry
- Welding Torch. A device used to heat and melt metal for joining pieces together. (eg: oxy-fuel torch)
- Grinder. A tool used to shape and finish metal surfaces. (eg: angle grinder)
- Hand Tools. Tools used to form, cut, and shape metal, such as pliers, hammers, and chisels. (eg: wire cutters)
- Safety Equipment. Protective equipment worn to protect the worker from sparks, heat, and other dangers associated with welding. (eg: welding gloves, helmet)
- Power Tools. Powered tools used to make cuts and welds, such as an electric drill or plasma cutter. (eg: arc welder)
- Cleaning Supplies. Cleaning supplies used to clean and prepare surfaces before welding. (eg: steel brush, degreaser)
Professional Organizations to Know
- American Welding Society (AWS)
- American Society of Mechanical Engineers (ASME)
- Canadian Welding Bureau (CWB)
- The Fabricators & Manufacturers Association (FMA)
- International Institute of Welding (IIW)
- National Center for Welding Education & Training (NCEWT)
- International Brotherhood of Boilermakers (IBB)
- International Association of Bridge, Structural, Ornamental & Reinforcing Iron Workers (IABSORIW)
- National Association of Professional Welders (NAPW)
- American Welding Institute (AWI)
We also have Utility Worker, Fabrication Worker, and Industrial Worker jobs reports.
Common Important Terms
- Welding. The process of joining two or more pieces of metal together by melting and fusing them together.
- Brazing. A process of joining two or more metals together using a non-ferrous filler metal.
- Metal Inert Gas (MIG) Welding. A welding process that uses a continuous wire feed and an electric arc to join two pieces of metal together.
- Tungsten Inert Gas (TIG) Welding. A welding process that uses a tungsten electrode and an inert gas to weld two pieces of metal together.
- Shielded Metal Arc Welding (SMAW). A welding process that uses a consumable electrode and a flux-coated electrode to weld two pieces of metal together.
- Flux-Cored Arc Welding (FCAW). A welding process that uses a flux-cored wire to weld two pieces of metal together.
- Oxyacetylene Welding. A welding process that uses an oxygen-acetylene flame to weld two pieces of metal together.
- Soldering. A process of joining two or more metals together using a non-ferrous solder material.
Frequently Asked Questions
What is the typical salary of a Welding Worker?
The average salary of a Welding Worker is $44,568 per year.
What type of welding methods do Welding Workers use?
Welding Workers typically use arc welding, gas welding, and oxy-acetylene welding methods.
What qualifications are needed for a Welding Worker?
Most employers require Welding Workers to have a high school diploma or equivalent and to complete a welding training program.
What safety precautions do Welding Workers need to take?
Welding Workers must adhere to safety protocols such as wearing protective gear and taking proper safety measures when working with hazardous materials.
What is the job outlook for Welding Workers?
The job outlook for Welding Workers is expected to grow by 6% through 2029.
What are jobs related with Welding Worker?
- Security Worker
- Plant Worker
- Carpenter/Furniture Maker Worker
- Packaging Worker
- Mine Worker
- Sanitation Worker
- Shipping Worker
- Cleaning Worker
- Technical Support Worker
- Health Care Worker
Web Resources
- How Welding Works - The Basics of the Welding summitcollege.edu
- Welding - Spoon River College - src.edu www.src.edu
- Career Education - Welding - Compton College www.compton.edu
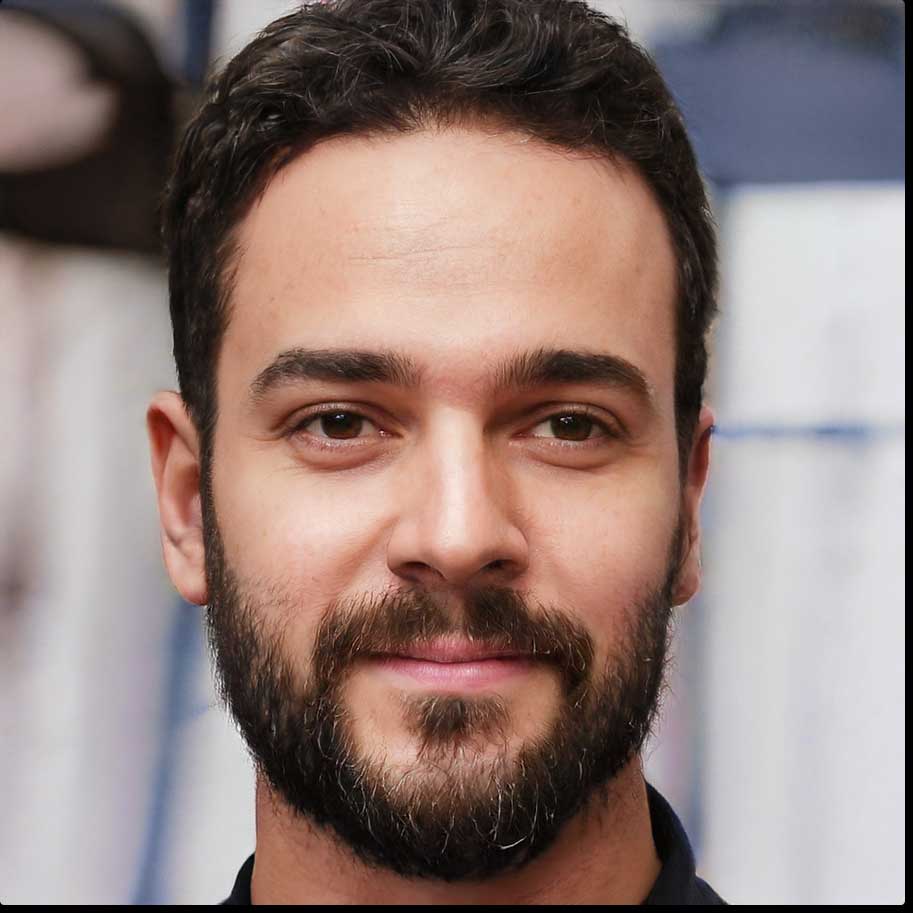