How to Be Plant Worker - Job Description, Skills, and Interview Questions
When a Plant Worker is responsible for the production and maintenance of a facility, they play a vital role in ensuring that the process runs smoothly and efficiently. The Plant Worker must have an understanding of the systems in place and how they work, as well as the safety protocols necessary in the workplace. If they are not familiar with the operations of the facility, they can cause costly delays and mistakes.
They must also be able to diagnose problems quickly and adjust their plan of action accordingly. Furthermore, they must be able to communicate with other personnel onsite and offsite, as well as be able to work independently and as part of a team. When Plant Workers fulfil their duties effectively, this leads to increased productivity, improved quality of products or services, and better customer satisfaction.
Steps How to Become
- Obtain a High School Diploma or GED. A high school diploma or GED is typically required to become a plant worker.
- Get On-the-Job Training. Most employers prefer to hire workers with at least some experience in the production process.
- Obtain Certification. Depending on the industry, a Plant Worker may need to obtain certification through an accredited organization to legally work in the field.
- Learn and Understand Safety Protocols. Plant Workers must be familiar with safety protocols and be able to follow them correctly in order to ensure the safety of everyone involved.
- Be Willing to Work in Unfavorable Conditions. Some plant work requires working in hot, noisy, and dirty environments.
- Possess Good Manual Dexterity. Plant Workers must have good manual dexterity in order to operate machinery and tools.
- Have Good Problem Solving Skills. Plant Workers must be able to troubleshoot problems quickly and efficiently in order to keep the production process running smoothly.
Working in a plant requires reliability and capability. The effects of having reliable and capable workers can be seen in the workplace in a number of ways. When workers are reliable, they are less likely to miss their shifts and cause delays in production.
This helps ensure that the plant runs smoothly and efficiently. when workers are capable, they can complete tasks quickly and accurately, reducing the risk of mistakes and increasing productivity. Finally, having reliable and capable workers can help to create a positive work environment, as employees trust each other to get their work done in a timely manner.
All of these factors contribute to the successful operation of a plant.
You may want to check Logistics Coordinator Worker, Food Service Worker, and Electrical Worker for alternative.
Job Description
- Plant Operator: Responsible for the safe operation and maintenance of plant equipment and systems, including machinery, piping, and electrical components. Monitors production systems and performs troubleshooting when necessary.
- Plant Maintenance Technician: Responsible for ensuring that all plant equipment is operating properly and efficiently. Performs routine maintenance tasks such as lubrication, cleaning, and inspection of machinery and equipment.
- Plant Inspector: Responsible for ensuring that all plant operations comply with applicable laws, regulations, and company policies. Inspects production processes and inspects equipment for safety and efficiency.
- Plant Supervisor: Oversees all plant operations, supervising personnel and delegating tasks. Manages the workflow to ensure that production goals are met in a timely manner.
- Plant Manager: Responsible for the overall operation of the plant, including personnel management, budgeting, and regulatory compliance. Ensures that safety regulations are followed and that production goals are met.
Skills and Competencies to Have
- Knowledge of plant operations and processes
- Ability to follow safety guidelines and procedures
- Ability to read and interpret technical documents
- Ability to use various hand tools, power tools, and other machinery
- Ability to lift heavy objects
- Knowledge of basic computer operations
- Ability to work independently with minimal supervision
- Excellent organizational and problem-solving skills
- Ability to work in a fast-paced environment
- Ability to work as part of a team
- Excellent communication skills
- Ability to handle multiple tasks simultaneously
- Attention to detail and accuracy
The most important skill for a plant worker is the ability to problem-solve. This skill is critical for successful operation of a plant and can be the difference between a successful and unsuccessful outcome. Plant workers must be able to identify potential problems, think critically, and develop solutions that are both effective and efficient.
Good problem-solving will help ensure that the plant runs smoothly, with minimal interruptions. it can also prevent costly mistakes, or even accidents, from occurring. With problem-solving skills, plant workers can quickly assess a situation, identify the cause of the problem, and come up with the best solution.
This ability is essential for successful and safe operation of the plant.
Machine Worker, Technical Support Worker, and Logistics Worker are related jobs you may like.
Frequent Interview Questions
- What experience do you have working in a plant environment?
- How do you handle a fast-paced and physically demanding work environment?
- What safety precautions do you take when operating machinery in a plant setting?
- What measures do you take to ensure that production goals are met?
- How do you handle difficult or problem employees?
- How do you respond to working in hot or cramped conditions?
- What is your experience with working with hazardous materials?
- Describe a time when you had to troubleshoot a technical issue in a plant environment.
- How do you stay organized and manage multiple tasks at once?
- What steps would you take to reduce production costs while maintaining quality?
Common Tools in Industry
- Forklift. Vehicle used to transport and lift heavy loads, (eg: moving pallets of materials).
- Drill Press. Machine used to make holes in materials, (eg: drilling holes in metal).
- Wrench. Tool used for tightening or loosening screws and bolts, (eg: changing a tire).
- Grinder. Machine used to grind or shape materials, (eg: smoothing the edges of a metal part).
- Screwdriver. Tool used to drive screws into material, (eg: installing screws into a piece of wood).
- Hammer. Tool used to drive nails and other objects into material, (eg: hammering nails into a wall).
- Nail Gun. Tool used to drive nails quickly and accurately, (eg: installing trim around a window).
- Tape Measure. Device used to measure length, width, and other measurements, (eg: measuring the length of a piece of wood).
- Saw. Tool used to cut material, (eg: cutting a piece of wood into two pieces).
- Welder. Machine that uses electricity or gas to join two pieces of metal together, (eg: welding two pieces of steel together).
Professional Organizations to Know
- American Society of Mechanical Engineers (ASME)
- Institute of Industrial and Systems Engineers (IISE)
- National Association of Plant Operators & Engineers (NAPOE)
- American Federation of Plant Workers (AFPW)
- International Association of Plastics Distribution (IAPD)
- International Union of Operating Engineers (IUOE)
- Automation and Control Technicians Association (ACTA)
- Packaging Machinery Manufacturers Institute (PMMI)
- International Society of Automation (ISA)
- International Organization of Standardization (ISO)
We also have Environmental Worker, Refinery Worker, and Quality Control Worker jobs reports.
Common Important Terms
- Forging. The process of shaping metal into desired shapes and sizes by hammering or pressing.
- Milling. The process of cutting metal into desired shapes and sizes using a milling machine.
- Drilling. The process of making holes in metal using a drill bit.
- Welding. The process of joining two pieces of metal together using heat, pressure, and/or filler material.
- Grinding. The process of using an abrasive material to smooth or shape a surface.
- Assembly. The process of putting parts or components together to form a larger structure or product.
- Painting. The process of applying a protective coating to metal surfaces to protect them from corrosion.
- Quality Control. The process of ensuring that products meet standards and specifications.
- Material Handling. The process of moving and storing materials in a safe and efficient manner.
- Health and Safety. The practice of ensuring a safe working environment for employees.
Frequently Asked Questions
What is a Plant Worker?
A Plant Worker is a professional who operates and maintains industrial machinery for a manufacturing plant.
What qualifications do Plant Workers need?
Plant Workers typically need to have a high school diploma or equivalent, as well as knowledge of safety protocols, mechanical systems, and operation of industrial machinery.
What duties do Plant Workers perform?
Plant Workers are responsible for operating and maintaining industrial machinery, troubleshooting and repairing any malfunctions, monitoring the production line, adhering to safety protocols, and ensuring quality control standards are met.
How much do Plant Workers earn?
According to the U.S. Bureau of Labor Statistics, the median annual wage for Plant Workers was $35,290 in 2019.
What are the working conditions of a Plant Worker?
Plant Workers often work in noisy and potentially hazardous environments, with long hours and overtime. They must be able to stand for long periods of time and lift heavy objects.
What are jobs related with Plant Worker?
- Heavy Equipment Operator Worker
- Packaging Worker
- Process Worker
- Driver/Courier Worker
- Industrial Worker
- Mine Worker
- Line Worker
- Security Worker
- Cleaning Worker
- Maintenance Worker
Web Resources
- Physical Plant Administrative Student Worker Asbury University www.asbury.edu
- Physical Plant - Lee University www.leeuniversity.edu
- Physical Plant | The University of Southern Mississippi www.usm.edu
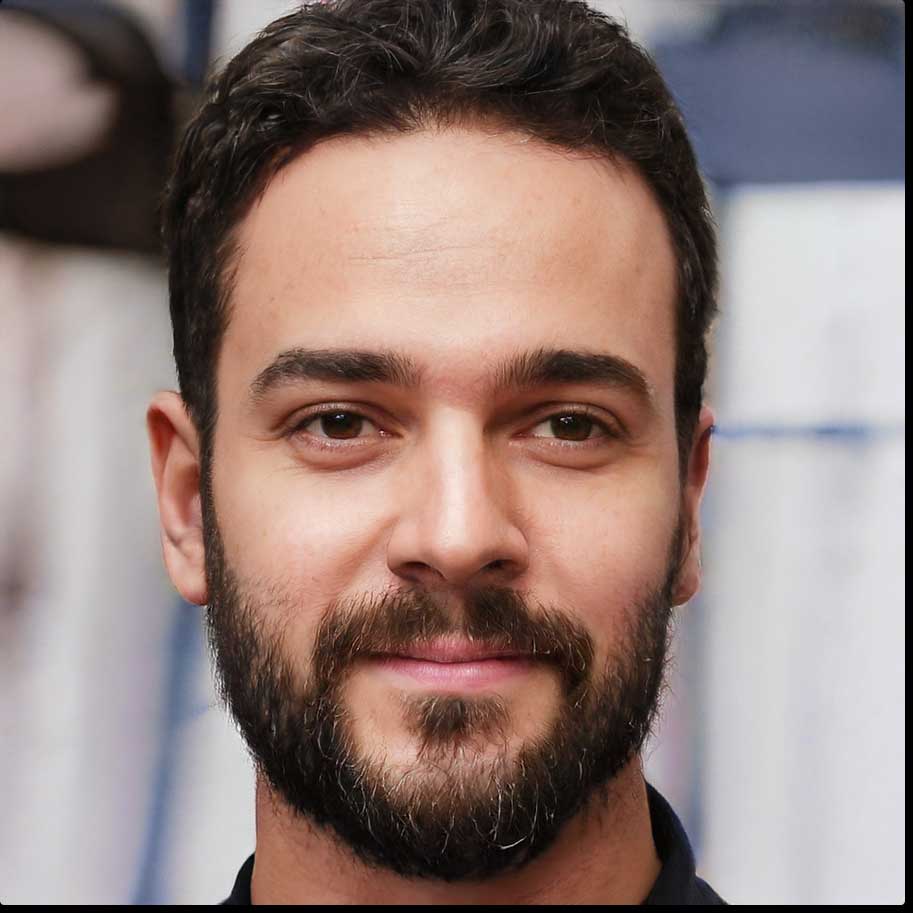