How to Be Quality Control Worker - Job Description, Skills, and Interview Questions
A Quality Control Worker is responsible for ensuring that the products produced by a company are of the highest quality and meet all industry standards. This is done by conducting detailed inspections and tests on the product before it is shipped out to customers. Poor quality control can lead to customer dissatisfaction, loss of revenue, and even legal action.
A Quality Control Worker must have excellent attention to detail and be able to identify any defects or flaws in the product. Quality Control Workers also work with engineers to address any issues that may arise during the manufacturing process and ensure that the product meets all safety standards. Quality Control Workers must also stay up-to-date with changes in the industry, including new regulations, and ensure that all products meet those standards.
Quality Control Workers play an essential role in ensuring the success of a company.
Steps How to Become
- Obtain a high school diploma or equivalent. A high school diploma is the minimum educational requirement for a Quality Control Worker. In some cases, an associates degree or higher may be required.
- Pursue further education in a related field. Quality Control Workers should have a strong knowledge of industry standards and regulations. Consider earning a degree in a field related to quality control, such as engineering, manufacturing technology, or business.
- Gain experience in quality control. Many employers require Quality Control Workers to have previous experience in quality control. Look for opportunities to gain experience through internships or apprenticeships in the field.
- Obtain necessary certifications. Quality Control Workers may need to be certified in specific areas, such as Six Sigma or ISO 9000. Certifications can help demonstrate competency and may open up more job opportunities.
- Search for open positions. Quality Control Worker positions may be available with a variety of employers, from manufacturers to government agencies. Use resources like job boards, career fairs, and professional organizations to find open positions.
- Apply for the position. Submit a well-written resume and cover letter along with any other required materials to apply for the position. Research the employer and prepare for an interview, if necessary.
- Demonstrate proficiency in the role. Once hired, Quality Control Workers must remain up-to-date on industry standards and regulations and effectively use testing methods and tools to ensure quality control protocols are followed.
The quality of a product is determined by the level of control and inspection during the production process. Quality control workers are essential for ensuring that products meet the standards set by the company and customers. If quality control workers are not present or do not have the right qualifications, it can lead to defective products and dissatisfied customers.
Companies must hire qualified workers who understand the importance of quality assurance and have the technical expertise to analyze and inspect products. The ideal quality control worker must be well-trained, experienced, and have excellent attention to detail. they must possess problem-solving and communication skills to properly document and report any discrepancies or issues found.
Quality control workers are essential for ensuring that companies produce high-quality products and maintain customer satisfaction.
You may want to check Warehouse Worker, Sanitation Worker, and Tool and Die Worker for alternative.
Job Description
- Examine products and materials for defects and malfunctions.
- Test products and materials to ensure they meet quality standards.
- Record inspection and test data.
- Document non-conforming materials and products.
- Report quality control information to supervisors.
- Monitor production processes to ensure quality standards are met.
- Perform routine maintenance on inspection and testing equipment.
- Communicate quality control information to other departments.
- Inspect incoming materials and products for conformance to specifications.
- Investigate customer complaints regarding quality of materials or products.
Skills and Competencies to Have
- Knowledge of quality control processes and standards
- Ability to read and interpret engineering drawings and specifications
- Ability to use precision measuring instruments and tools
- Ability to use computer programs for data entry and analysis
- Good communication and interpersonal skills
- Ability to detect and identify defects in products
- Ability to work independently as well as in a team environment
- Strong problem solving and analytical skills
- Good organizational and time management skills
- Knowledge of health and safety regulations
Quality control workers play a vital role in the success of any organization. They are responsible for ensuring the quality of products or services, and that they meet the standards set by the company. To be successful in this role, quality control workers must have a number of important skills.
These include attention to detail, problem solving skills, organization and communication skills. Attention to detail is essential because quality control workers must be able to spot any potential problems or issues before they become bigger problems. Problem solving skills help quality control workers to quickly identify solutions to any problems they encounter.
Organization is important because quality control workers need to be able to keep track of all the different products or services that need to be checked. Finally, communication skills are essential for working with other departments within the organization to ensure that everyone is on the same page and that any issues are quickly resolved. With these qualities, quality control workers are an invaluable asset to any organization.
Industrial Worker, Plant Worker, and Technical Support Worker are related jobs you may like.
Frequent Interview Questions
- What experience do you have in quality control?
- What processes do you use to ensure product quality?
- How do you identify defective products?
- How do you handle customer complaints related to product quality?
- What challenges have you faced in your previous roles related to quality control?
- How do you ensure that products meet safety standards?
- Do you have any experience using software programs for quality control?
- How do you stay up to date with industry best practices in quality control?
- What techniques do you use to document quality control processes?
- How do you motivate a team to meet quality expectations?
Common Tools in Industry
- Pressure Gauge. Measures and records pressure in various systems (eg: tire pressure gauge).
- Micrometer. Measures the diameter of small objects (eg: a metal cylinder).
- Calipers. Measures the distance between two points (eg: inside and outside diameters of a pipe).
- Force Gauge. Measures the amount of force being applied to an object (eg: pushing on a lever).
- Optical Comparator. Compares objects to a known standard (eg: a dimensioned drawing).
- Dimensional Measuring Instrument. Measures the size and shape of an object (eg: a machined component).
- Vernier Calipers. Measures the distance between two points with precision (eg: inside and outside diameters of a hole).
- Torque Wrench. Applies a specific amount of torque to fasteners (eg: tightening a bolt).
- Dial Indicator. Measures the displacement of an object (eg: measuring the deflection of a beam).
- Ultrasonic Thickness Gauge. Measures the thickness of an object using sound waves (eg: checking the thickness of a steel plate).
Professional Organizations to Know
- American Society for Quality (ASQ)
- International Organization for Standardization (ISO)
- Institute of Quality Assurance (IQA)
- Association for Quality and Participation (AQP)
- National Association of Professional Quality (NAPQ)
- National Institute of Standards and Technology (NIST)
- International Society of Quality Assurance Professionals (ISQAP)
- American Quality Institute (AQI)
- Institute of Management Sciences (IMS)
- The Global Association for Quality Management (GAQM)
We also have Packer/Picker Worker, Refinery Worker, and Utility Worker jobs reports.
Common Important Terms
- Quality Assurance (QA) - A system of processes and procedures which are used to ensure that products and services meet certain predetermined standards of quality.
- Quality Management (QM) - The overall process used to ensure that products meet certain standards of quality. It involves creating, maintaining, and improving quality standards, as well as assessing customer satisfaction.
- Quality Control (QC) - The process of checking each product or service against known standards of quality to ensure compliance.
- Total Quality Management (TQM) - An approach to management which focuses on continually improving the quality of all products and services. It involves a team effort to ensure that all stakeholders are involved in the quality control process.
- Statistical Process Control (SPC) - A method of quality control which uses statistical methods to monitor and assess the performance of a process or product.
- Root Cause Analysis (RCA) - A process used to identify and eliminate the causes of a defect in a product or service. It involves identifying potential causes and then determining which one is most likely the root cause.
Frequently Asked Questions
What are the duties of a Quality Control Worker?
A Quality Control Worker is responsible for ensuring that products meet quality standards by inspecting and testing materials and products to detect defects. This includes conducting inspections, testing materials, keeping accurate records of test results, and making recommendations to improve production processes.
What skills are needed to be a Quality Control Worker?
Quality Control Workers should have strong attention to detail, problem-solving skills, and technical knowledge of quality control systems. Additionally, knowledge of various quality control processes, industry standards and regulations, and the ability to use specialized tools and equipment is essential.
What qualifications are required for a Quality Control Worker?
Most employers require Quality Control Workers to have a high school diploma or equivalent, as well as experience in a related field. Additionally, certification from a professional organization is often preferred or required.
How much does a Quality Control Worker earn?
The average salary for a Quality Control Worker is $37,906 per year, although this can vary depending on the company and location.
What is the job outlook for Quality Control Workers?
The job outlook for Quality Control Workers is expected to grow 5% from 2019 to 2029, which is faster than the average for all occupations. This growth is due to an increasing demand for products with higher quality standards.
What are jobs related with Quality Control Worker?
- Automotive Worker
- Janitorial Worker
- Assembler Worker
- Security Worker
- Technician Worker
- Warehouse Associate Worker
- Food Service Worker
- Logistics Worker
- Order Filler/Packer Worker
- Grounds Worker
Web Resources
- Quality Control Northwestern State University - nsula.edu www.nsula.edu
- What is a Manufacturing Quality Controller? | Goodwin University www.goodwin.edu
- What Does a Quality Control Inspector Do? | Goodwin University www.goodwin.edu
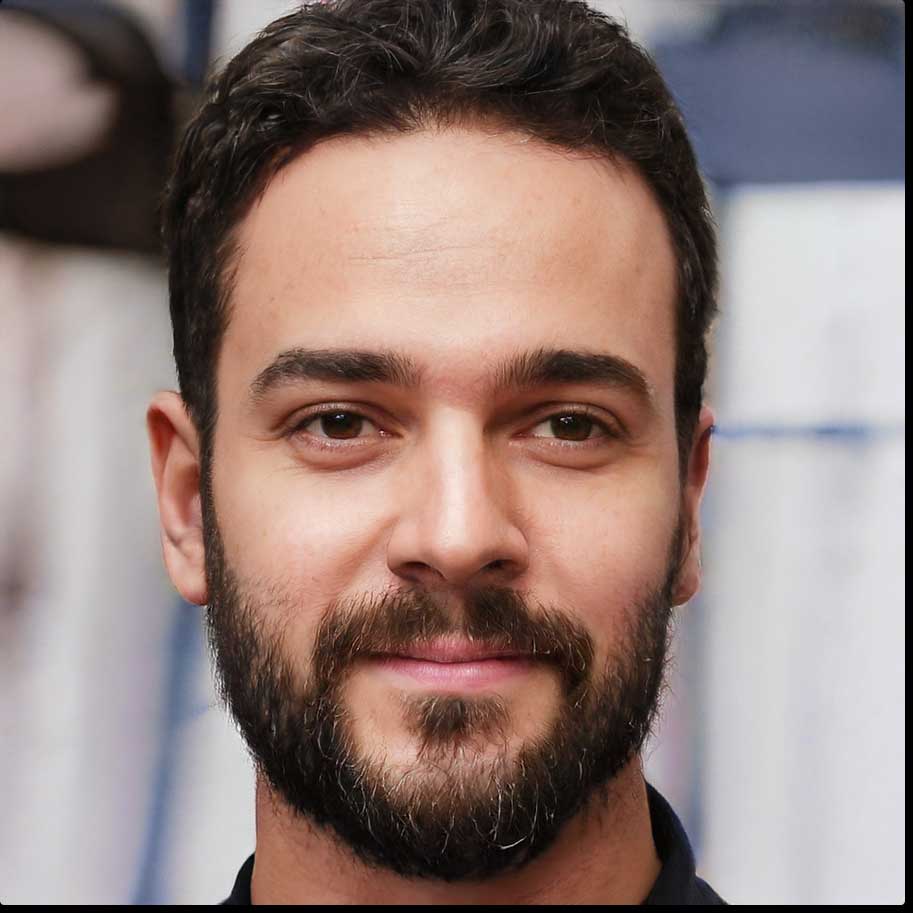