How to Be Service Technician - Job Description, Skills, and Interview Questions
Steps How to Become
- Obtain a High School Diploma or GED. Service technicians must have a high school diploma or the equivalent in order to gain employment.
- Get Vocational Training. Many employers prefer to hire service technicians who have undergone vocational training in areas such as electronics, computer repair, or HVAC (heating, ventilation and air conditioning). Vocational courses can be taken at local technical colleges, community colleges, and some high schools.
- Research Entry-Level Jobs. Research entry-level technician jobs in the chosen field. Job postings can be found on job search websites, as well as on the websites of local employers.
- Apply for Jobs. Submit resumes and cover letters to potential employers. Some employers may require applicants to take a written test or participate in an interview.
- Obtain Industry Certification. Obtaining industry certification is a great way to demonstrate expertise and knowledge in the chosen field. Certification requirements vary by industry, so it is important to research the specific requirements for the chosen career path.
- Get On-the-Job Training. Most employers provide on-the-job training for service technicians. During this training period, technicians learn the skills and techniques needed to perform their job duties.
- Advance Your Career. As service technicians gain experience and knowledge, they may be able to advance their career by taking on more complex tasks or even management roles.
The key to reliable and efficient service technician is preparedness. Being prepared involves having the right tools, parts, and training for the job. Technician must also have a comprehensive understanding of the systems and components they are servicing.
having a good customer service approach and the ability to troubleshoot quickly and accurately can go a long way in providing efficient service. When a technician is well-prepared, they can more quickly and accurately diagnose problems, leading to faster repair times and higher customer satisfaction.
You may want to check Services Consultant, Service Manager, and Services Delivery Lead for alternative.
Job Description
- Diagnose and repair mechanical and electrical problems in a variety of appliances, such as refrigerators, washers, dryers, dishwashers, microwaves, ovens, and other kitchen and laundry appliances.
- Perform preventative maintenance on appliances to ensure proper operation.
- Follow safety guidelines when handling hazardous materials, such as Freon and other chemicals.
- Test and inspect appliances for proper function.
- Consult with customers to determine the nature of the problem and the best solution.
- Provide estimates for repair costs and parts needed.
- Reassemble appliances after repair or replacement of parts.
- Keep accurate records of repairs and customer interactions.
- Maintain clean and organized work areas.
- Stay up-to-date with new technology and techniques in appliance repair.
Skills and Competencies to Have
- Excellent customer service skills
- Technical aptitude for troubleshooting and diagnosing mechanical/electrical problems
- Knowledge of computer systems and applications
- Ability to read and interpret technical documents and manuals
- Proficiency in the use of power tools, test equipment, and hand tools
- Ability to lift heavy objects safely
- Familiarity with safety regulations and industry standards
- Strong communication and problem-solving skills
- Self-motivation and organizational skills
- Ability to work independently and as part of a team
- Flexibility to work on-call and overtime as needed
The ability to troubleshoot and problem solve is essential for any Service Technician. When a customer reports a problem, the technician must use their knowledge and experience to accurately identify the source of the issue. Once the cause has been determined, the technician can then devise an appropriate solution.
This requires a thorough understanding of the components of the system, as well as the ability to think logically and critically. it is important to be able to communicate effectively with customers, clearly explaining the issue and potential solutions. Good interpersonal skills and patience are also important for providing a satisfactory experience for the customer.
a Service Technician must be able to quickly assess a situation, determine the cause of the problem, and then provide an effective remedy.
Services Coordinator, Service Delivery Manager, and Services Representative are related jobs you may like.
Frequent Interview Questions
- Tell me about your experience servicing and troubleshooting HVAC systems?
- What techniques do you use when performing maintenance on equipment?
- What challenges have you faced while working as a service technician?
- How would you handle a difficult customer complaint?
- Describe your experience with safety protocols when servicing equipment.
- How do you handle a situation where a customer is not satisfied with the outcome of a repair?
- What have you done to stay up-to-date on the latest industry technologies and trends?
- How do you prioritize tasks when servicing multiple customers?
- How do you ensure that all repairs are completed according to industry standards?
- Describe your experience working with other technicians in a team environment to complete a project.
Common Tools in Industry
- Wrenches. Used for tightening and loosening nuts and bolts (eg: adjustable wrench).
- Pliers. Used for gripping and cutting (eg: needle-nose pliers).
- Screwdrivers. Used for driving screws into and out of material (eg: Phillips head screwdriver).
- Hammers. Used for driving nails into material (eg: claw hammer).
- Saws. Used for cutting material (eg: coping saw).
- Socket Sets. Used for tightening and loosening nuts and bolts (eg: socket wrench).
- Drills. Used for drilling holes into material (eg: electric drill).
- Soldering Iron. Used for joining two pieces of metal together (eg: soldering gun).
- Torque Wrench. Used for applying a specific amount of torque to a fastener (eg: adjustable torque wrench).
- Multimeters. Used for measuring electrical voltage, current, and resistance (eg: digital multimeter).
Professional Organizations to Know
- American Society of Mechanical Engineers (ASME)
- Institute of Electrical and Electronics Engineers (IEEE)
- International Association of Refrigeration and Air Conditioning Technicians (IARCT)
- National Institute for Certification in Engineering Technologies (NICET)
- North American Technician Excellence (NATE)
- Plumbing-Heating-Cooling Contractors Association (PHCC)
- Refrigeration Service Engineers Society (RSES)
- Sheet Metal and Air Conditioning Contractors' National Association (SMACNA)
- The Air Conditioning, Heating, and Refrigeration Institute (AHRI)
- The Association of Home Appliance Manufacturers (AHAM)
Common Important Terms
- Repair. The process of restoring something to its original working condition.
- Diagnosis. The process of identifying the cause of a problem or symptom.
- Troubleshooting. The process of analyzing and resolving problems with a system or device.
- Maintenance. The process of regularly inspecting and servicing a system or device to ensure it remains in good working order.
- Parts Replacement. The process of replacing old, worn, or broken parts with new ones.
- Installation. The process of setting up and configuring a system or device.
- Calibration. The process of adjusting a system or device to its optimal performance settings.
- Testing. The process of verifying the accuracy and performance of a system or device.
- Warranty. A guarantee from the manufacturer that a product will meet certain specifications and be free from certain defects for a certain period of time.
- Safety Protocols. Precautions taken to ensure the safety of personnel and equipment when working on a system or device.
Frequently Asked Questions
What qualifications are needed to become a Service Technician?
To become a Service Technician, you typically need a high school diploma or equivalent and some prior experience in technical or mechanical work. You may also need to pass a test or obtain a license, depending on your state.
What is the average salary of a Service Technician?
The average salary of a Service Technician is approximately $44,000 per year.
What are the primary responsibilities of a Service Technician?
The primary responsibilities of a Service Technician include troubleshooting, diagnosing, and repairing various types of equipment and systems; performing routine maintenance; and communicating with customers about service needs.
What type of work environment does a Service Technician typically work in?
A Service Technician typically works in a variety of settings, such as in-home service calls, repair shops, or on-site at customer locations.
What tools and equipment do Service Technicians use?
Common tools and equipment used by Service Technicians include hand tools, diagnostic tools, power tools, and specialized equipment such as lifts and jacks.
What are jobs related with Service Technician?
Web Resources
- Central Service Technician | Renton Technical College rtc.edu
- Central Service Technician - Explore Health Care college.mayo.edu
- Automotive Service Technician Apprenticeship | SCI scitexas.edu
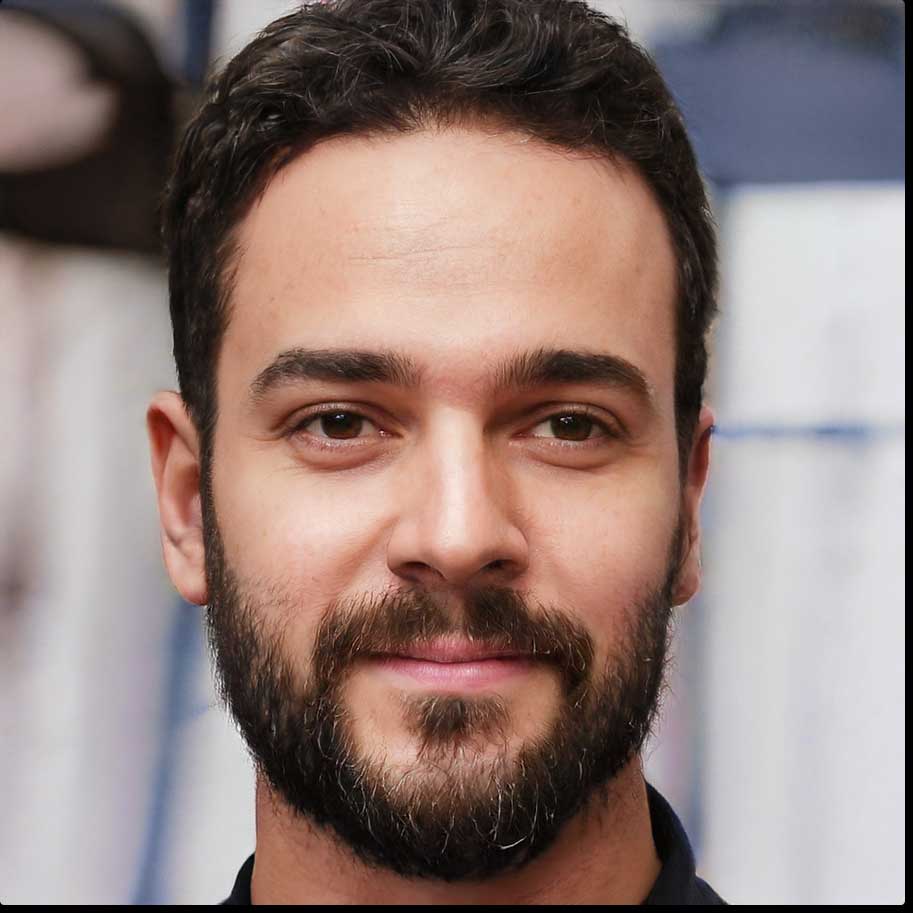