How to Be Chemical Process Design Engineer - Job Description, Skills, and Interview Questions
Chemical process design engineers are responsible for designing and analyzing chemical processes to identify potential risks and develop solutions to minimize them. They play a key role in the development of the industrial infrastructure by designing processes that produce chemicals, materials, and products in an efficient and cost-effective manner. By understanding the principles of thermodynamics, fluid dynamics, heat transfer, mass transfer, and reaction kinetics, they are able to optimize the process parameters such as temperature, pressure, and flow rate.
This helps to reduce energy consumption, reduce capital costs, and improve product quality. Chemical process design engineers also work closely with operational and maintenance personnel to ensure that the process operates safely and efficiently. Their expertise is essential for the successful design of new processes, as well as for the enhancement and optimization of existing ones.
Steps How to Become
- Obtain a bachelor's degree in chemical engineering. This is the minimum educational requirement to become a chemical process design engineer. Most employers prefer candidates with a master's degree in chemical engineering.
- Gain experience in the field. Many employers prefer applicants who have at least one year of experience in chemical engineering, especially with process design.
- Become knowledgeable about process design software. Many employers require applicants to be familiar with process design software such as Aspen HYSYS and AutoCAD.
- Obtain certification as a professional engineer. This is not required for all chemical process design engineers, but it can be beneficial for career advancement opportunities.
- Expand your knowledge of safety regulations and environmental concerns. These are important aspects of chemical process design and employers will be looking for candidates who are up to date on these topics.
- Develop excellent communication skills. Chemical process design engineers must be able to communicate effectively with other engineers and technicians, as well as clients and stakeholders.
- Stay current on industry trends and technology advancements. This is essential for any chemical process design engineer so that they can remain competitive in the field.
Being a Chemical Process Design Engineer requires staying ahead and efficient to be successful. One way to do this is to stay up-to-date on the latest trends and technologies in the industry. Researching new innovations and attending conferences are a great way to gain knowledge and stay informed.
staying organized and creating a plan of action for a project can help ensure success. Planning out the steps needed to complete a task efficiently and ensuring there is proper communication between all parties involved can help streamline the process. having a good support system of colleagues and mentors can give valuable insight and help prevent costly mistakes.
Lastly, utilizing software tools to automate routine tasks can help save time and increase productivity. By taking these steps, Chemical Process Design Engineers can stay ahead and be efficient in their work.
You may want to check Chemical Process Engineer, Chemical Process Safety Engineer, and Chemical Production Technician for alternative.
Job Description
- Develop process design and engineering documents to support the implementation of new or modified chemical processes.
- Identify and implement cost-effective process engineering solutions.
- Develop process flow diagrams, equipment specifications, and process control systems.
- Analyze process data to improve process efficiency, reduce costs, and eliminate safety issues.
- Design, implement, and monitor process safety measures.
- Develop and execute project plans, budgets, and timelines.
- Ensure compliance with all applicable safety and environmental regulations.
- Monitor process performance and analyze data to identify process improvements.
- Provide technical support to plant personnel for troubleshooting and problem resolution.
- Interface with vendors, contractors, and other outside resources to ensure quality and timely completion of projects.
Skills and Competencies to Have
- Knowledge of chemical process engineering principles, theories, and concepts
- Ability to develop process models and simulations
- Proficiency in process design and optimization software
- Knowledge of safety regulations for chemical processes
- Ability to analyze data and develop solutions to technical problems
- Experience with computer-aided design software
- Ability to collaborate effectively with other departments
- Excellent written and oral communication skills
- Thorough understanding of relevant industry codes and standards
- Organizational and time management skills
For a Chemical Process Design Engineer, the most important skill to have is a strong understanding of chemistry and chemical engineering. This knowledge will enable the engineer to develop and implement the most efficient and safe chemical processes. the engineer should possess strong problem solving and analytical skills so they can properly identify, analyze, and develop solutions for any issues that may arise.
Furthermore, the engineer must be adept at using computer-aided design and engineering software to create accurate and detailed designs of the chemical process. Finally, excellent communication skills are essential for Chemical Process Design Engineers as they will be required to communicate their designs and findings with both colleagues and clients. All of these skills are essential for a successful career in Chemical Process Design Engineering.
Chemical Inspector, Chemical Reactor Operator, and Chemical Research Scientist are related jobs you may like.
Frequent Interview Questions
- How would you describe your experience with process design and optimization?
- What is your approach to process safety when designing new chemical processes?
- How do you stay up to date with the latest process design trends and technologies?
- Describe a recent project that you have worked on that involved chemical process design.
- What challenges have you faced when designing chemical processes?
- What techniques do you use to identify and evaluate process risks?
- How do you ensure that the process designs you create are cost-effective?
- What techniques do you use to troubleshoot process issues?
- How have you incorporated sustainability into your process designs?
- What is your experience with computer-aided design (CAD) software?
Common Tools in Industry
- Process Flow Diagram (PFD). A diagram that depicts the overall flow and design of a chemical process. (e. g. a PFD for an ethylene production plant)
- Computer-Aided Design (CAD). Software used to design products and components, including those in chemical processes. (e. g. AutoCAD for designing a reactor vessel)
- Process Simulation Software. Software used to simulate process conditions and analyze the results. (e. g. Aspen HYSYS for simulating a distillation process)
- Process Control Software. Software used to monitor and control process equipment, such as pumps and valves. (e. g. Emerson DeltaV for controlling a stirring system)
- Process Optimization Software. Software used to optimize process parameters in order to maximize efficiency and minimize costs. (e. g. DynoChem for optimizing a reactor temperature profile)
- Process Safety Analysis Software. Software used to analyze the safety of processes and identify potential hazards. (e. g. Safeti for evaluating the risk of an accidental release of hazardous chemicals)
Professional Organizations to Know
- American Institute of Chemical Engineers (AIChE)
- Institute of Chemical Engineers (IChemE)
- American Chemical Society (ACS)
- Society of Chemical Engineers (SCE)
- Association for the Advancement of Industrial and Applied Mathematics (AIM)
- International Society of Automation (ISA)
- American Society of Mechanical Engineers (ASME)
- American Society for Engineering Education (ASEE)
- American Society for Quality (ASQ)
- National Society of Professional Engineers (NSPE)
We also have Chemical Plant Supervisor, Chemical Engineer Intern, and Chemical Quality Control Analyst jobs reports.
Common Important Terms
- Mass Balance. A process design engineer must be familiar with the principles of mass balance, which involve understanding the balance of material and energy within a system. This is important for understanding the flow of materials through a process and determining how to optimize the design.
- Process Flow Diagrams (PFD). A process flow diagram is a graphical representation of the flow of material through a process. Process design engineers use PFDs to understand the behavior of a process and ensure that it is operating correctly.
- Heat Exchangers. Heat exchangers are used in many chemical processes to transfer heat from one fluid to another. Process design engineers must be familiar with the types of heat exchangers available and how they are used in different processes.
- Process Simulation. Process simulation is an important tool for process design engineers. It allows them to model a process and understand how changes in parameters or variables will affect the performance of a system.
- Process Control. Process control is the use of automation to control a process. Process design engineers must be familiar with the types of control systems available and how they can be used to optimize the performance of a process.
- Instrumentation and Measurement. Instrumentation and measurement is essential for any chemical process. Process design engineers must be familiar with the types of instruments available and how they can be used to measure variables such as temperature, pressure, flow rate, etc.
Frequently Asked Questions
What is a Chemical Process Design Engineer?
A Chemical Process Design Engineer is a professional who designs and develops industrial chemical processes, including optimization, troubleshooting, and safety. They analyze and model chemical processes and create process designs that are safe, efficient, and cost-effective.
What qualifications are needed to become a Chemical Process Design Engineer?
To become a Chemical Process Design Engineer, a Bachelor's degree in Chemical or Process Engineering is typically required. Additionally, knowledge of process design fundamentals, chemical engineering principles, and experience in the chemical process industry is beneficial.
What tasks do Chemical Process Design Engineers typically perform?
The tasks performed by Chemical Process Design Engineers typically include concept development, process design and optimization, data analysis, process simulations, preparing process flow diagrams and material balance sheets, and developing safety protocols.
What skills do Chemical Process Design Engineers need?
Chemical Process Design Engineers need strong analytical and problem-solving skills, communication skills, knowledge of process design fundamentals and chemical engineering principles, proficiency with computer software such as MATLAB and Simulink, and an understanding of safety protocols.
What is the average salary for a Chemical Process Design Engineer?
According to PayScale, the average salary for a Chemical Process Design Engineer is $80,523 per year. Salaries can range from $53,000 to $127,000 per year depending on experience, location, and other factors.
What are jobs related with Chemical Process Design Engineer?
- Chemical Safety Coordinator
- Chemical Plant Process Engineer
- Chemical Laboratory Technician
- Chemical Plant Manager
- Chemical Sales Representative
- Chemical Analytical Technician
- Chemical Regulatory Specialist
Web Resources
- Chemical Process Engineer | NC State Online and Distance online-distance.ncsu.edu
- An Overview of Chemical Process Design Engineering www.academia.edu
- Chemical & Process Engineering | The Department of Chemical sta.uwi.edu
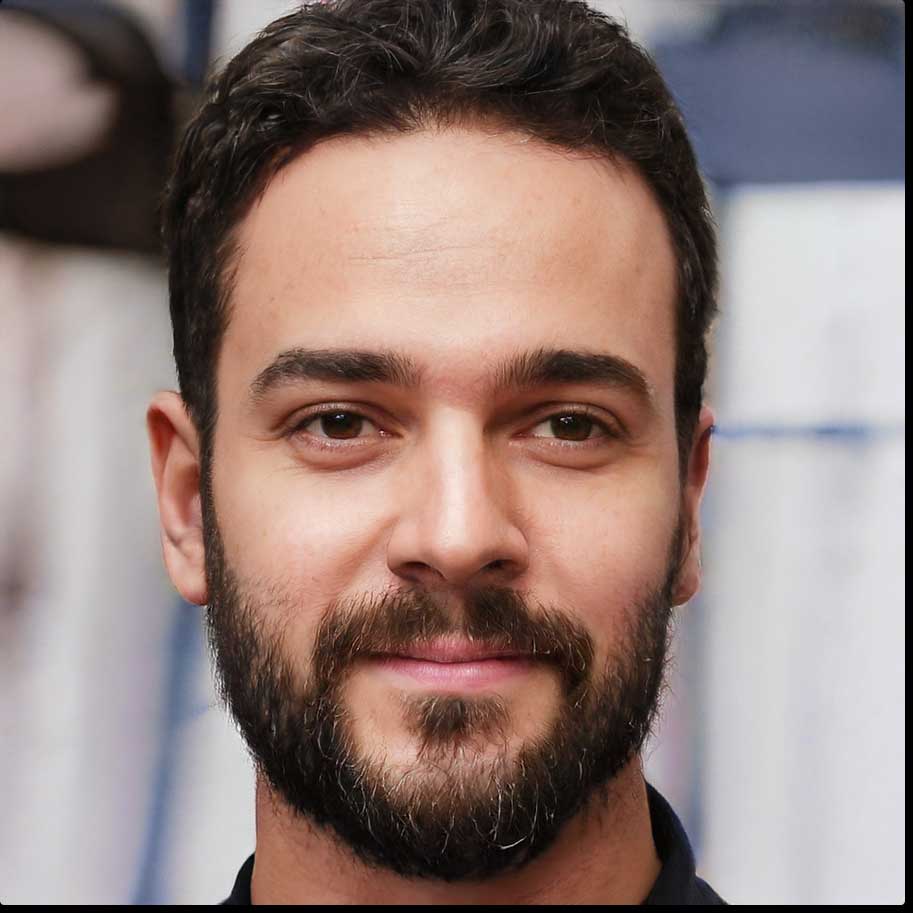