How to Be Cello Maker/Repairer/Restorer - Job Description, Skills, and Interview Questions
Steps How to Become
- Take music lessons. Start by taking music lessons to become familiar with the cello and its techniques. This will help you understand the instrument on a deeper level and provide you with the technical knowledge necessary to become a cello maker, repairer, or restorer.
- Practice often. After you have taken lessons, it is important to practice regularly with your instrument. Regular practice will help you develop a better understanding of the cello and its components.
- Learn woodworking. As a cello maker, repairer, or restorer, it is important to have a good understanding and knowledge of woodworking. You should take classes or workshops in woodworking in order to learn the proper techniques and skills needed to build, repair, and restore cellos.
- Join an apprenticeship. It is recommended that you join an apprenticeship or find a mentor in order to gain practical experience in the field. Apprenticeships are a great way to get hands-on experience and learn from someone who has been doing this work for a long time.
- Set up a workshop. Once you have gained enough experience and knowledge in the field, you should set up your own workshop. This is where you will be able to make, repair, and restore cellos.
- Market yourself. Once you have set up your workshop, it is important to market yourself and your work. You should create a website, join social media platforms, advertise in local newspapers and magazines, and attend trade shows. This will help you get your name out there and attract more customers for your business.
Maintaining the skills of a cello maker/repairer/restorer requires a regular and consistent effort to stay up-to-date with the latest advancements in both tools and techniques. This is essential in order to ensure that one is capable of producing quality, professional instruments and repairs. To do this, it is important to stay abreast of the current trends in the industry, whether it be through online resources, attending workshops and seminars, or collaborating with colleagues.
investing in high-quality tools and materials will help ensure that the work is done properly and with precision. Finally, it is important to practice regularly in order to stay in tune with the instrument, refine techniques, and continually hone one's craftsmanship. By investing time and energy into keeping updated and capable, a cello maker/repairer/restorer can remain a valuable asset for years to come.
You may want to check Music Supervisor/Music Director/Cellist, Principal Cellist, and Audio Visual Technician/Cellist for alternative.
Job Description
- Cello Maker: Responsible for crafting new cellos from start to finish, including carving the wood, assembling the instrument, and finally tuning and polishing it.
- Cello Repairer: Responsible for restoring and repairing existing cellos, including replacing worn strings, fixing broken bridges and tailpieces, and retouching varnish.
- Cello Setup Technician: Responsible for setting up and adjusting cellos to ensure they are in optimal playing condition, including adjusting the bridge, nut, and soundpost.
- Cello Tuner: Responsible for tuning cellos to pitch, using a variety of tuning tools and techniques.
- Cello Restorer: Responsible for restoring old and damaged cellos to their original condition, including repairing cracks, re-varnishing, and making structural repairs.
Skills and Competencies to Have
- Expertise in playing the cello
- Knowledge of the mechanics of cellos and their parts
- Ability to diagnose and repair cello issues
- Ability to read music and understand music theory
- Skill in using hand tools, such as saws, drill presses and sanders
- Expertise in woodworking and wood carving
- Knowledge of the different types of strings, bridges and tailpieces
- Understanding of varnishing, lacquering and oiling techniques
- Ability to assess the condition of cellos and estimate the cost of repairs
- Proficiency in playing multiple stringed instruments
- Attention to detail and creativity in customizing instruments
- Ability to communicate effectively with clients
Having the skill to make, repair, or restore a cello is essential for anyone looking to pursue a career in this field. A cello maker must have an intimate knowledge of the instrument, including its components and how they interact with one another. This includes an understanding of the materials used in construction, such as wood, glue, and varnish, as well as the tools necessary for each stage of the process.
the cello maker must possess a specialized set of skills such as woodworking, lutherie (the art of making stringed instruments), and the ability to use traditional and modern tools with precision and accuracy. With these skills, a cello maker can create a beautiful instrument that will produce beautiful music and last for many years.
Solo Cellist, Digital Media Technology Specialist/Cellist, and Musical Theater Cellist are related jobs you may like.
Frequent Interview Questions
- What experience do you have in making, repairing, and restoring cellos?
- How comfortable are you with using specialized tools for cello making and repair?
- What techniques do you use to ensure a cello is properly tuned?
- How do you approach a challenging repair or restoration project?
- Describe your experience with assessing the quality of wood used for cello making.
- What methods do you use to ensure a cellos sound quality and playability?
- What methods do you use to determine the value of a cello?
- What experience do you have with the different types of strings and other parts used in cellos?
- How do you assess and address customer needs and expectations?
- Describe your experience in teaching others how to make, repair, and restore cellos.
Common Tools in Industry
- Cello Bow. A bowed string instrument used to play melodies on the cello. (eg: a German-made bow used to play Bach's Cello Suite No. 1)
- Tuning Pegs. Small wheel-like devices used to adjust the tension of the strings on the cello. (eg: a set of ebony tuning pegs used to tune a cello)
- Bridge. A wooden device that holds the strings in place on the cello. (eg: a maple bridge used to hold the strings on a cello)
- Endpin. A metal pin at the bottom of the cello that is used to attach the cello to a stand or chair. (eg: an adjustable endpin used to secure a cello to a chair)
- Rosin. A sticky substance that is applied to the bow hair of the cello bow to help it grip the strings. (eg: high quality rosin used to improve sound quality on a cello)
- Sound Post. A small wooden dowel placed inside the body of the cello to improve resonance and projection. (eg: a spruce sound post used to enhance the tone of a cello)
- Bass Bar. A wooden strip placed within the body of the cello to help balance the tension of the strings. (eg: a maple bass bar used to create a more even sound on a cello)
- Chin Rest. A small device attached to the end of the cello that supports the chin while playing. (eg: an ergonomic chin rest used to provide comfort while playing the cello)
- Nut and Saddle. Small pieces of bone or plastic that are placed at the top and bottom of the cello strings respectively. (eg: bone nut and saddle used to improve sound quality on a cello)
- Plane and File. Hand tools used to shave down various parts of the cello for repair or customization purposes. (eg: a flat plane and round file used for precise measurements on a cello)
Professional Organizations to Know
- American Federation of Violin and Bow Makers
- International Society of Cello Makers
- American String Teachers Association
- Violin Society of America
- International Double Reed Society
- International Violin Making Association
- American Guild of Musical Artists
- Cello Institute of America
- National Association of Music Merchants
- DAddario Foundation for Strings
We also have Program Director/Producer/Cellist, Concert Cellist, and Music Library Technician/Cellist jobs reports.
Common Important Terms
- Cello Construction. The process of building a cello from the ground up, using materials such as wood, glue, varnish, and strings.
- Cello Repair. The process of repairing and restoring a cello to its original condition. This could involve replacing broken parts, adjusting the action and soundpost, as well as cleaning and polishing the instrument.
- Setup. The process of setting up a cello, which includes positioning the bridge, adjusting the strings, and adjusting the soundpost and other parts.
- Tonal Adjustment. The process of adjusting the sound of a cello by adjusting the strings and bridge, as well as changing the internal components.
- Bow Rehairing. The process of re-stringing a bow with new horsehair. This process involves removing the old hair and replacing it with new strands.
- Bow Repair. The process of repairing and restoring a cello bow to its original condition. This could involve replacing broken parts, as well as cleaning and polishing the instrument.
Frequently Asked Questions
Q1: What types of materials does a Cello Maker/Repairer/Restorer use? A1: A Cello Maker/Repairer/Restorer typically uses wood, glue, varnish, metal, and strings to craft or repair a cello. Q2: How long does it take a Cello Maker/Repairer/Restorer to complete a full restoration? A2: A full restoration of a cello typically takes between 20-30 hours of work. Q3: What type of qualifications are required to be a Cello Maker/Repairer/Restorer? A3: A Cello Maker/Repairer/Restorer must have a deep knowledge of the materials and craftsmanship involved in the creation and maintenance of cellos. They may have formal training such as a degree in instrument making or repair. Q4: How much does a Cello Maker/Repairer/Restorer usually charge per hour? A4: The price of labor for a Cello Maker/Repairer/Restorer can vary widely depending on their experience, but it typically ranges from $50-$150 per hour. Q5: What specialized tools does a Cello Maker/Repairer/Restorer use? A5: A Cello Maker/Repairer/Restorer may use specialized tools such as planes, chisels, saws, files, routers, and clamps in their work. They may also employ the use of measuring devices such as calipers and micrometers.What are jobs related with Cello Maker/Repairer/Restorer?
- Sponsorship Manager/Cellist
- Session Cellist
- Contractor/Hired Musician Cellist
- Hospitality Manager/Cellist
- Orchestra Section Cellist
- Cruise Ship Cellist
- Studio Cellist
- Sound Technician/Cellist
- Stage Manager/Cellist
- Church Music Director/Cellist
Web Resources
- Cello - Music music.colostate.edu
- Cello | Strings - University of North Texas strings.music.unt.edu
- Cello - University of Hartford www.hartford.edu
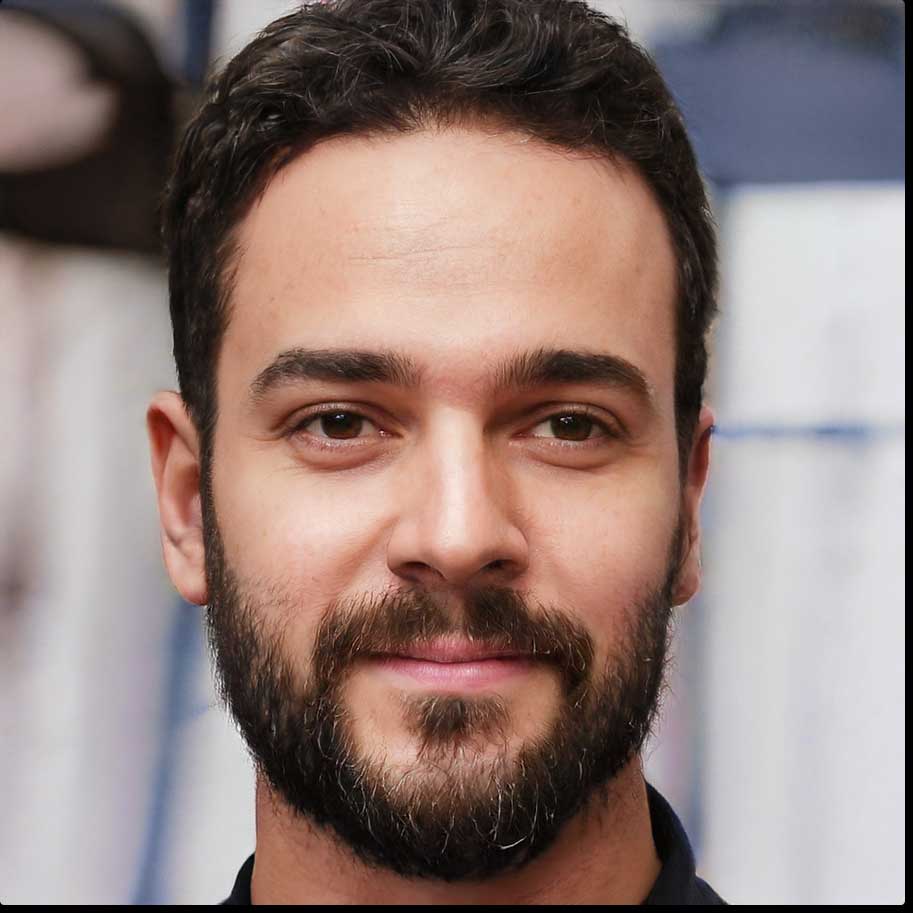