How to Be Chemical Process Safety Engineer - Job Description, Skills, and Interview Questions
The role of a Chemical Process Safety Engineer is to ensure the safety of chemical processes, which involves the evaluation and mitigation of potential hazards. This requires a thorough understanding of the chemical processes, assessing the risks associated with them, and developing safety protocols to minimize these risks. An effective Chemical Process Safety Engineer will have knowledge of hazardous materials, safety regulations, and engineering principles.
They must also have strong communication and problem-solving skills to identify and address safety issues quickly and effectively. The results of their efforts are improved safety for the facility, its personnel, and the environment, as well as reduced costs associated with accidents and other incidents.
Steps How to Become
- Obtain a Bachelor's Degree. The first step to becoming a Chemical Process Safety Engineer is to gain a bachelor's degree in engineering, chemistry, or another related field. In order to be a successful engineer, you must have a good understanding of engineering principles and chemistry.
- Develop Your Skills. Chemical Process Safety Engineers use a variety of tools and software to analyze and design processes. It is important to develop your skills in these areas in order to be successful as a Chemical Process Safety Engineer.
- Obtain Certification. Many employers require Chemical Process Safety Engineers to have certification from the American Institute of Chemical Engineers (AIChE). This certification can be obtained by taking and passing an exam that tests your knowledge of chemical process safety systems.
- Gain Experience. Many employers prefer to hire engineers with experience in the field. It is important to gain experience by working as an intern or an entry-level engineer in a chemical plant or laboratory.
- Stay Up-to-Date. It is important to stay up-to-date on the latest advancements in engineering and safety practices. This can be done by reading industry journals, attending conferences, and taking additional courses.
- Consider Further Education. Some employers require that Chemical Process Safety Engineers have a master's degree or higher in engineering or a related field. Consider pursuing further education in order to advance your career.
Chemical process safety engineering is a crucial component of ensuring that hazardous chemical processes are operated safely and securely. To stay updated and competent in this field, it is essential to stay abreast of the latest developments in chemical processing technology, safety standards, and regulations. Ongoing training and education on the latest safety practices and technologies can help ensure that engineers remain knowledgeable and up-to-date.
networking and participating in professional organizations can help keep engineers connected to the latest safety trends and developments. Finally, developing working relationships with other safety professionals and engaging in research projects can help keep engineers informed of best practices and the latest advances in the field. By staying informed and prepared, chemical process safety engineers can help ensure the safe operation of hazardous chemical processes.
You may want to check Chemical Process Engineer, Chemical Regulatory Specialist, and Chemical Plant Manager for alternative.
Job Description
- Develop and maintain health, safety, and environmental policies and procedures related to chemical process safety.
- Analyze chemical process safety hazards associated with process operations and recommend appropriate control measures.
- Develop chemical process safety management plans including Process Hazard Analyses (PHA).
- Coordinate and/or conduct safety reviews of process equipment and processes.
- Track hazardous materials inventories and manage associated safety data sheets.
- Prepare and maintain safety documentation including reports, forms, and training materials.
- Assist in the development and implementation of emergency response plans.
- Develop and conduct chemical process safety training for personnel.
- Monitor compliance with applicable laws and regulations.
- Investigate incidents and develop corrective action plans as needed.
Skills and Competencies to Have
- Knowledge of safety standards, regulations, and best practices in chemical process safety
- Understanding of chemical processes and systems
- Knowledge of risk assessment techniques
- Ability to develop and implement safety management systems
- Ability to assess and monitor chemical process safety risks
- Proficiency in performing root cause analysis and hazard identification
- Experience in hazardous material handling and storage
- Expertise in process safety incident management
- Knowledge of process control systems and instrumentation
- Ability to write and review safety protocols, policies, and procedures
- Ability to effectively communicate safety information to staff and management
- Ability to provide technical guidance to personnel on safety issues
- Ability to develop and deliver safety training programs
- Proficiency in data analysis and statistical methods
Chemical Process Safety Engineering is a vital and highly specialized field of engineering that focuses on the prevention of accidents and injuries in chemical processes. It requires a combination of technical knowledge and problem-solving skills to identify, analyze, and control potential hazards in chemical processes. The Chemical Process Safety Engineer must have a deep understanding of chemistry, physics, mathematics, and engineering principles in order to recognize and evaluate hazardous events.
They must be able to use this knowledge to develop safety procedures, analyze safety data, and design safety equipment. The Chemical Process Safety Engineer must also have excellent communication skills in order to effectively explain safety requirements to personnel and stakeholders. they must possess strong problem-solving skills in order to identify potential risks and develop solutions to prevent them.
All of these skills are essential for any Chemical Process Safety Engineer who wishes to be successful in this field.
Chemical Analytical Technician, Chemical Laboratory Technician, and Chemical Plant Process Engineer are related jobs you may like.
Frequent Interview Questions
- What qualifications do you have that make you a suitable candidate for the chemical process safety engineering position?
- How familiar are you with safety regulations and standards related to the chemical industry?
- How comfortable are you in helping to create process safety related procedures and documents?
- What experience do you have in conducting hazard and risk assessments?
- How do you go about troubleshooting and resolving process safety-related issues?
- How do you ensure that process safety measures are followed and maintained in a facility?
- What strategies do you employ to ensure compliance with process safety regulations?
- How do you work with teams to implement process safety initiatives?
- What tools and techniques do you use to monitor process safety performance?
- How do you stay up-to-date on the latest developments in chemical process safety engineering?
Common Tools in Industry
- HAZOP Analysis. A risk assessment technique used to identify hazards and reduce risks in chemical processes. (eg: Identifying potential hazards and ways to reduce them in a factory producing plastics. )
- Hazard Analysis and Critical Control Points (HACCP). A system used to identify and control safety risks in food production. (eg: Establishing safety protocols for a food production plant. )
- Safety Integrity Level (SIL). A method of classifying the performance level of safety systems, used in industrial automation. (eg: Setting SIL ratings for safety systems such as emergency shut-down systems. )
- Process Hazard Analysis (PHA). A risk assessment method used to identify hazards and reduce risks in chemical processes. (eg: Identifying potential hazards and ways to reduce them in a steel production plant. )
- Fault Tree Analysis (FTA). A risk assessment technique used to identify potential causes of accidents or failures. (eg: Identifying potential causes of a fire in a factory. )
- Layer of Protection Analysis (LOPA). A risk assessment technique used to identify hazards and reduce risks in hazardous processes. (eg: Identifying potential hazards and ways to reduce them in a fuel storage facility. )
Professional Organizations to Know
- American Institute of Chemical Engineers (AIChE)
- American Chemical Society (ACS)
- Institute of Chemical Engineers (IChemE)
- International Society of Automation (ISA)
- National Fire Protection Association (NFPA)
- American Society of Safety Engineers (ASSE)
- International Society of Explosives Engineers (ISEE)
- American Society for Testing and Materials (ASTM)
- Center for Chemical Process Safety (CCPS)
- European Process Safety Centre (EPSC)
We also have Chemical Production Technician, Chemical Research Scientist, and Chemical Quality Control Analyst jobs reports.
Common Important Terms
- Hazardous Materials Management (HMM). A process of managing hazardous materials to ensure safety in the workplace.
- Risk Assessment. A process of identifying potential risks and assessing the likelihood of their occurrence.
- Process Hazard Analysis (PHA). An analysis of a process to identify potential hazards and develop methods to mitigate them.
- Process Safety Management (PSM). A system of managing processes to ensure safety and compliance with regulatory requirements.
- Emergency Response Planning (ERP). A plan for responding to emergency situations, including evacuations and containment of hazards.
- Personal Protective Equipment (PPE). Clothing and equipment used to protect workers from hazards.
- Fire Prevention. Measures taken to reduce the risk of fire in the workplace.
- Explosion Prevention. Measures taken to reduce the risk of explosions in the workplace.
- Contamination Control. Measures taken to reduce the risk of contamination in the workplace.
- Incident Investigation. An in-depth examination of an incident to determine its cause and develop methods to prevent future occurrences.
Frequently Asked Questions
What does a Chemical Process Safety Engineer do?
A Chemical Process Safety Engineer is responsible for developing and implementing safety processes, procedures and systems that protect personnel and the environment from hazardous materials and chemicals used in the manufacturing process.
What qualifications are needed to become a Chemical Process Safety Engineer?
To become a Chemical Process Safety Engineer, one must typically possess a bachelor's degree in chemical engineering, safety engineering, or a related field, as well as experience in safety engineering and chemical process safety.
What are the job duties of a Chemical Process Safety Engineer?
As a Chemical Process Safety Engineer, one's job duties may include identifying potential hazards and risks related to chemicals and materials used in the manufacturing process, developing safety protocols and systems to ensure personnel safety, inspecting equipment and machinery for compliance with safety standards, and training personnel on safety protocols.
What is the average salary of a Chemical Process Safety Engineer?
The average salary of a Chemical Process Safety Engineer is approximately $80,000 per year, depending on experience and location.
What are some examples of Chemical Process Safety Engineer roles in the industry?
Some examples of roles for a Chemical Process Safety Engineer in the industry include overseeing chemical process operations, ensuring compliance with safety regulations, implementing safety protocols and systems, and conducting safety audits.
What are jobs related with Chemical Process Safety Engineer?
- Chemical Reactor Operator
- Chemical Inspector
- Chemical Safety Coordinator
- Chemical Plant Operator
- Chemical Process Design Engineer
- Chemical Plant Supervisor
- Chemical Sales Representative
Web Resources
- Process Safety | Chemical Engineering | Michigan Tech www.mtu.edu
- What Is Process Safety Engineering? - Texas A&M University psc.tamu.edu
- Chemical Process Engineer | NC State Online and Distance online-distance.ncsu.edu
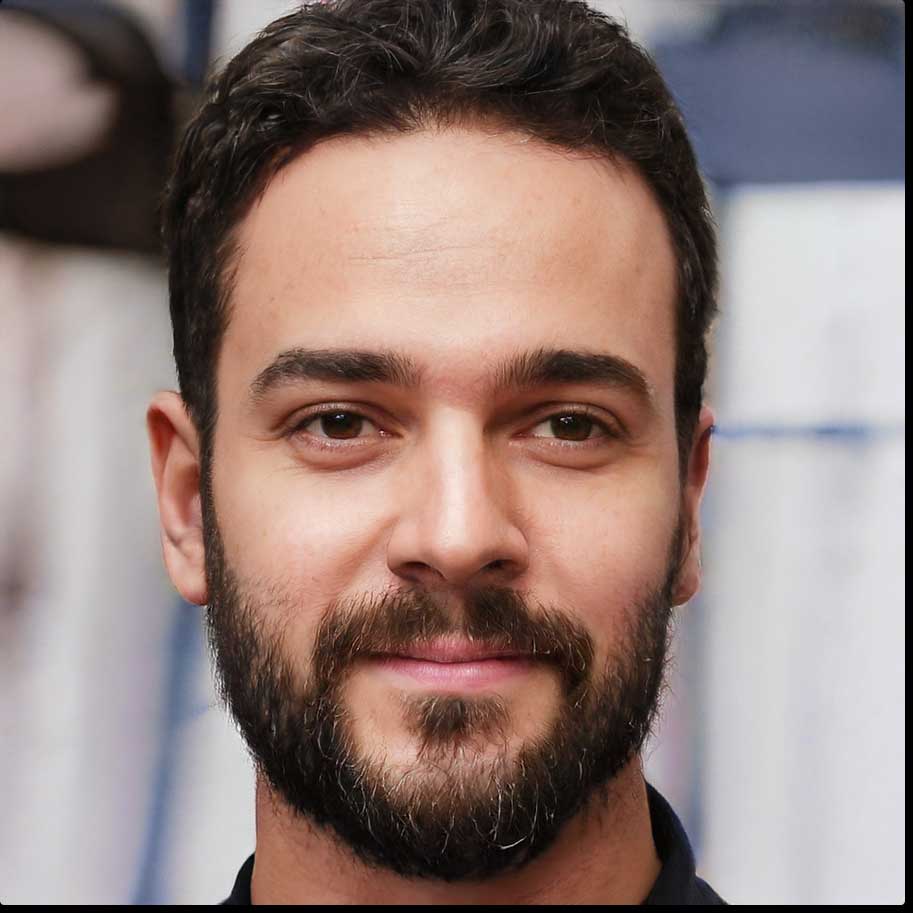