How to Be Chemical Safety Coordinator - Job Description, Skills, and Interview Questions
The use of hazardous chemicals can cause a variety of serious health and environmental risks. As such, it is essential for any organization that utilizes such chemicals to employ a Chemical Safety Coordinator. This role is responsible for analyzing the potential risks of chemical exposure, informing staff about safety protocols, and monitoring the use of hazardous materials.
They also develop safety plans, provide emergency response training, and ensure compliance with all applicable safety regulations. The presence of a Chemical Safety Coordinator can help to prevent accidents, reduce the risk of contamination, and protect workers from potential harm. this position can be invaluable in helping to create a safe and healthy workplace.
Steps How to Become
- Obtain a Bachelors Degree in Chemistry. In order to become a Chemical Safety Coordinator, you will need to have at least a Bachelors Degree in Chemistry or a related field. This degree will provide you with the necessary knowledge and skills that you need to understand the complexities of the chemical industry.
- Obtain Professional Certification. Although not required, obtaining professional certification as a Chemical Safety Coordinator can help you stand out from the competition when seeking employment. The American Board of Industrial Hygiene (ABIH) offers the Certified Chemical Safety Professional (CCSP) credential, which you can obtain by passing an exam.
- Complete On-the-Job Training. Many employers will require you to complete an on-the-job training program to become a Chemical Safety Coordinator. This program may include instruction in hazardous materials management, chemical hazard assessment and control, emergency response planning, and other safety protocols.
- Obtain Experience. To become an effective Chemical Safety Coordinator, you must gain experience in the field. You can do this by volunteering, working as an intern, or taking on a job as a safety technician or assistant safety coordinator.
- Stay Up-to-Date with New Regulations. As a Chemical Safety Coordinator, it is important to stay up-to-date with changing regulations and industry trends. This includes attending seminars and conferences, reading industry publications, and networking with other chemical safety professionals.
The role of a Chemical Safety Coordinator is to ensure the safety of all personnel in the workplace by ensuring all chemicals are handled, stored, and disposed of in a safe and responsible manner. To be successful in this role, a Chemical Safety Coordinator must be highly skilled and competent. They must possess a thorough knowledge of applicable regulations and laws, comprehensive understanding of hazardous materials and their potential impacts, and the ability to develop and implement effective safety protocols.
they must be able to identify potential risks and respond quickly in the event of an emergency. Furthermore, they must be able to work with all levels of personnel from within the organization to ensure compliance with safety regulations. By having a skilled and competent Chemical Safety Coordinator, organizations can reduce the risk of accidents, injuries, and illnesses due to improper chemical handling.
You may want to check Chemical Sales Representative, Chemical Analytical Technician, and Chemical Plant Supervisor for alternative.
Job Description
- Develop and implement safety policies, procedures, and regulations.
- Monitor compliance with safety regulations and standards.
- Coordinate emergency response plans and conduct drills.
- Investigate accidents and incidents to determine root causes and areas of improvement.
- Develop, implement, and maintain chemical safety programs.
- Document and report chemical hazards and incidents.
- Provide safety training to personnel on the proper handling of hazardous chemicals.
- Monitor usage and storage of hazardous chemicals.
- Ensure proper disposal of hazardous materials.
- Design and implement safety systems to reduce risk of injury from exposure to hazardous chemicals.
- Keep up-to-date on safety regulations and standards.
- Develop safety awareness campaigns for employees.
Skills and Competencies to Have
- Expert knowledge of relevant safety regulations and best practices.
- Ability to identify and assess hazards in the workplace.
- Ability to develop and implement safety policies and procedures.
- Ability to develop and conduct comprehensive safety training programs.
- Ability to maintain accurate records and reports.
- Excellent communication, organizational, and problem-solving skills.
- Knowledge of emergency response planning and procedures.
- Ability to respond quickly and effectively to emergency situations.
- Ability to inspect and maintain safety equipment and supplies.
- Ability to work under pressure and manage multiple tasks simultaneously.
A Chemical Safety Coordinator must have strong organizational and communication skills to ensure a safe and secure environment for those working with hazardous chemicals. Their duties include identifying potential hazards, implementing necessary precautions, monitoring chemical usage, and ensuring compliance with safety regulations. The ability to assess risk and develop effective safety protocols is essential to the success of the position.
the Chemical Safety Coordinator must be able to effectively communicate with stakeholders, both inside and outside of their organization. By doing so, they can ensure that everyone is aware of the necessary safety protocols and that they are following them appropriately. Failure to do so can result in serious repercussions, including fines, legal action, and even injury or death.
Having these organizational, communication, and risk assessment skills is essential to keeping everyone safe when working with hazardous chemicals.
Chemical Regulatory Specialist, Chemical Plant Manager, and Chemical Laboratory Technician are related jobs you may like.
Frequent Interview Questions
- What experience do you have working with hazardous materials and chemical safety protocols?
- Describe a successful safety initiative you have implemented in a previous role.
- How do you stay up to date on the latest chemical safety regulations?
- How do you ensure that all staff are properly trained in chemical safety protocols?
- What techniques do you use to ensure accurate documentation of chemical safety training and procedures?
- What strategies do you implement to reduce risks associated with hazardous materials?
- How do you handle emergency situations involving hazardous chemicals?
- How do you manage chemical waste and disposal?
- What steps do you take to ensure compliance with environmental regulations?
- How do you ensure safety protocols are being followed in the workplace?
Common Tools in Industry
- Risk Assessment Tool. A tool to assess and analyze potential risks associated with chemical operations. (e. g. RMPComp)
- Hazard Communication Program. A program that outlines the requirements for identifying, labeling, and storing hazardous chemicals. (e. g. OSHAs HazCom Standard)
- Emergency Action Plan. A plan outlining procedures to be followed in the event of a chemical emergency. (e. g. OSHAs Emergency Action Plan)
- Safety Data Sheets. A document that provides detailed information about the properties, hazards, and safe handling of a hazardous chemical. (e. g. SDS Plus)
- Training Programs. Programs designed to educate personnel on the safe handling and use of hazardous chemicals. (e. g. OSHAs Hazardous Waste Operations and Emergency Response Standard)
- Spill Containment and Cleanup Plan. A plan outlining procedures for containing and cleaning up chemical spills. (e. g. OSHAs Hazardous Waste Operations and Emergency Response Standard)
- Chemical Storage Protocols. Protocols that outline proper storage requirements for hazardous chemicals. (e. g. NFPA 30)
- Chemical Inventory System. A system for tracking the quantity, location, and use of hazardous chemicals in a facility. (e. g. ChemTracker)
- Equipment Maintenance Plan. A plan outlining procedures for maintaining equipment used to handle hazardous chemicals. (e. g. NFPA 68)
- Monitoring and Detecting Technology. Technology used to detect the presence of hazardous chemicals in the environment or a workplace. (e. g. GasAlert MicroClip XL)
Professional Organizations to Know
- American Industrial Hygiene Association (AIHA)
- American Board of Industrial Hygiene (ABIH)
- International Association for Chemical Safety (IACS)
- American Chemistry Council (ACC)
- National Institute for Occupational Safety and Health (NIOSH)
- American Conference of Governmental Industrial Hygienists (ACGIH)
- The Hazardous Materials Control Resources Institute (HMCR)
- International Society of Exposure Science (ISES)
- Institute of Hazardous Materials Management (IHMM)
- Safety Management Association of America (SMAA)
We also have Chemical Inspector, Chemical Process Safety Engineer, and Chemical Quality Control Analyst jobs reports.
Common Important Terms
- Hazardous Chemicals. Chemicals that are capable of causing harm to people, animals, or the environment, either through direct contact or through indirect exposure.
- Risk Assessment. The process of assessing the potential risks associated with a particular activity, process, or chemical.
- Material Safety Data Sheet (MSDS). A document that provides information about the properties, safety precautions, and handling procedures for a particular chemical or substance.
- Emergency Response Plan. A plan that outlines the steps and procedures to be taken in the event of an emergency involving hazardous chemicals.
- Personal Protective Equipment (PPE). Clothing, protective gear, and other equipment worn by personnel to protect them from exposure to hazardous chemicals.
- Proper Storage and Disposal. Procedures for storing and disposing of hazardous chemicals safely and in accordance with local and federal regulations.
- Labeling and Marking. Requirements for labeling containers with information about the contents and any associated hazards.
Frequently Asked Questions
What is a Chemical Safety Coordinator?
A Chemical Safety Coordinator is responsible for creating and overseeing safety protocols for the handling of hazardous materials in an industrial or educational setting.
What duties does a Chemical Safety Coordinator perform?
The duties of a Chemical Safety Coordinator include developing, implementing and monitoring safety procedures, conducting chemical inventories, providing training and compliance auditing, and responding to emergency situations.
What qualifications are needed to be a Chemical Safety Coordinator?
To be a Chemical Safety Coordinator, you typically need a degree in chemistry, engineering, safety or a related field, as well as experience in the field of chemical safety.
How often should safety protocols be reviewed by a Chemical Safety Coordinator?
Safety protocols should be reviewed on a regular basis, at least annually, by a Chemical Safety Coordinator in order to ensure they are up-to-date and can adequately protect workers.
What organizations are responsible for setting safety standards for Chemical Safety Coordinators?
Organizations such as the National Fire Protection Association (NFPA) and the Occupational Safety and Health Administration (OSHA) are responsible for setting safety standards for Chemical Safety Coordinators.
What are jobs related with Chemical Safety Coordinator?
- Chemical Process Engineer
- Chemical Process Design Engineer
- Chemical Plant Process Engineer
- Chemical Plant Operator
- Chemical Production Technician
- Chemical Engineer Intern
- Chemical Reactor Operator
Web Resources
- Chemical Safety - UCF Environmental Health and Safety ehs.ucf.edu
- Chemical Safety | Environmental Safety, Sustainability and Risk essr.umd.edu
- Chemical Safety | Environmental Health & (EHS) | The University ehs.utexas.edu
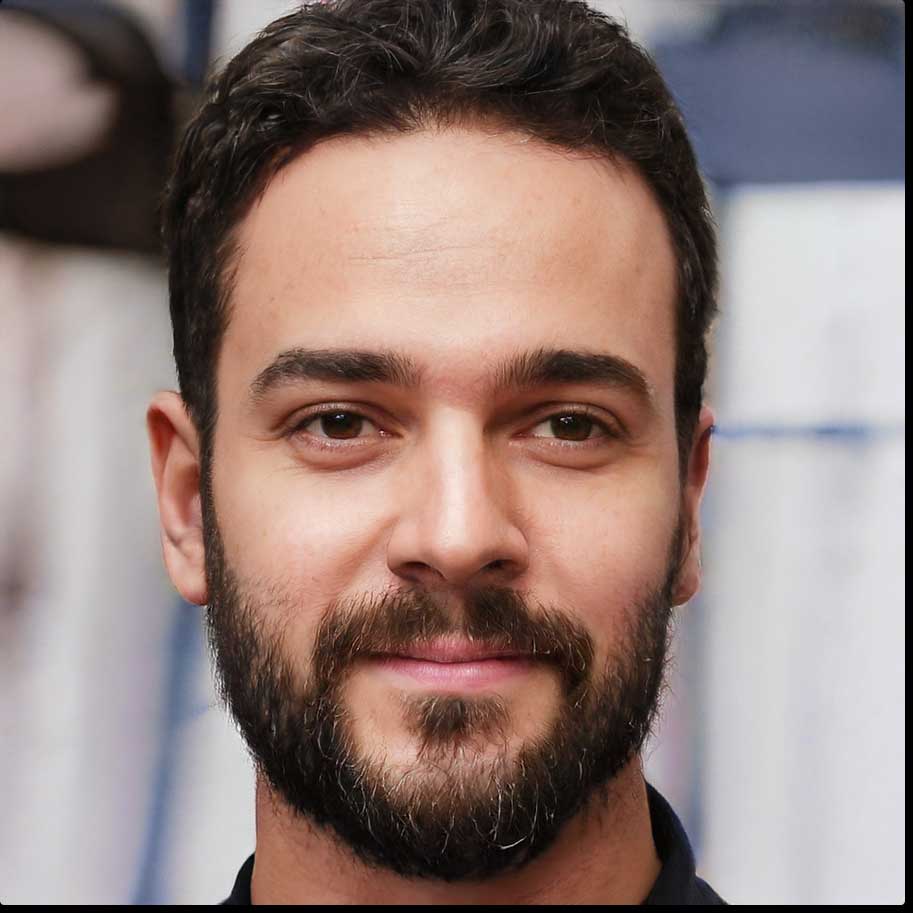