How to Be Chemical Process Engineer - Job Description, Skills, and Interview Questions
The role of a chemical process engineer is to design, develop and implement chemical processes to improve efficiency, reduce costs and meet safety requirements. They must have a strong understanding of the principles of chemistry, physics and engineering to ensure that the process is designed correctly. The engineer must also ensure that the process meets all environmental regulations and is safe for workers.
If the process does not meet these standards, the engineer may need to make adjustments or even redesign entire systems. The success of a chemical process engineer depends on their ability to identify problems, develop solutions and monitor the process for any new changes or issues. This can help to ensure that the process runs smoothly and efficiently, leading to increased profits and customer satisfaction.
Steps How to Become
- Obtain a bachelor's degree in chemical engineering. In order to become a Chemical Process Engineer, you will need to have a minimum of a bachelor's degree in chemical engineering or a closely related field.
- Gain relevant experience. Most employers prefer job applicants to have at least one to two years of experience in a related field. Consider pursuing internships or working as an assistant to a chemical engineer during your studies.
- Research employers and job openings. Use job boards and other platforms to look for potential employers and job openings in the chemical engineering field.
- Create a resume and cover letter. Use your experience and qualifications to create a resume and cover letter that stand out from other applicants.
- Prepare for the interview process. Research common questions asked during the interview process and practice your answers with a friend or family member.
- Apply for jobs and attend interviews. Submit your application materials to employers and attend any scheduled interviews.
- Receive a job offer. If you impress during the interview process, you may receive a job offer as a Chemical Process Engineer.
- Begin working as a Chemical Process Engineer. Once you have accepted the offer, you can begin working as a Chemical Process Engineer.
The efficient operation of a chemical process engineering system depends on several key factors. Chief among these are the proper selection of materials, the proper design of the process equipment and the proper selection of operating conditions. Poor selection of materials can result in process failure, increased costs and safety risks.
An inadequate design may lead to inefficient use of resources and increased downtime. Operating conditions that are either too hot or too cold can impact the reaction rate and produce undesired products. The ideal chemical process engineer must be knowledgeable in all these areas to ensure that the process is optimized for maximum efficiency and safety.
You may want to check Chemical Reactor Operator, Chemical Process Design Engineer, and Chemical Laboratory Technician for alternative.
Job Description
- Develop and design new chemical processes and systems to improve production processes.
- Analyze chemical processes and systems to identify and resolve problems.
- Monitor performance of process equipment, analyze data, and adjust operations as needed.
- Collaborate with other engineers, technicians, and production personnel to ensure efficient operation.
- Design, install, and troubleshoot process control systems and instrumentation.
- Develop process flow sheets and mass/energy balance calculations.
- Specify process equipment and materials of construction.
- Develop safety procedures for hazardous operations.
- Perform cost analysis of processes, materials, and equipment.
- Estimate process capital and operating costs.
- Develop process simulations with computer models and software packages.
- Prepare process documentation and reports.
Skills and Competencies to Have
- Technical understanding and knowledge of chemical engineering processes and fundamentals
- Working knowledge of physical and chemical properties of materials
- Proficiency in designing, developing, and optimizing processes
- Ability to use engineering tools such as CAD, P&ID, and process simulation software
- Knowledge of safety requirements and industry standards related to chemical manufacturing processes
- Ability to monitor process performance and troubleshoot process-related problems
- Strong analytical and problem-solving skills
- Excellent communication and interpersonal skills
- Ability to work well in a team environment
- Ability to work independently with minimal supervision
Being a Chemical Process Engineer requires a comprehensive understanding of the fundamentals of chemical engineering and the ability to apply them to the design, operation, and optimization of chemical processes. A Chemical Process Engineer must be able to analyze data and use it to troubleshoot and optimize the process. They must have strong problem-solving skills, be able to think critically, and be detail-oriented.
They must also be able to communicate effectively with their team and other stakeholders. they must have strong knowledge of safety regulations and standards, along with the ability to design and implement process control strategies. As a Chemical Process Engineer, it is essential to be proficient with computer simulation software and process automation software, as well as understanding the principles of mass and energy balance calculations.
All these skills are necessary for a Chemical Process Engineer to be successful in the industry.
Chemical Research Scientist, Chemical Analytical Technician, and Chemical Plant Supervisor are related jobs you may like.
Frequent Interview Questions
- What experience do you have with chemical process engineering?
- What challenges have you faced in your previous roles as a chemical process engineer?
- Describe a chemical process project you have worked on and the results.
- How do you stay up to date on the industrys best practices?
- What process design software have you used?
- How do you ensure cost-efficiency in your designs?
- How do you troubleshoot process engineering problems?
- What safety protocols do you follow in your chemical process engineering work?
- How would you handle a stakeholder who disagrees with your design decisions?
- What methods do you use to optimize production time?
Common Tools in Industry
- Aspen HYSYS. A process modeling software used to simulate and analyze process operations. (eg: Modeling of a distillation column)
- Process Flow Diagrams (PFD). Visual representation of a process that shows the flow of materials, instrumentation, and equipment. (eg: Block flow diagram of a refinery)
- Process and Instrumentation Diagrams (P&ID). Detailed diagrams showing the process flows, instrumentation, and control systems. (eg: P&ID for a cryogenic air separation unit)
- Computer Aided Design (CAD). CAD software used for design and drafting of process systems. (eg: AutoCAD for the design of a piping system)
- Material Balance Calculations. Perform mass and energy balance calculations to evaluate process performance. (eg: Estimate the amount of product produced in a distillation column)
- Statistical Process Control (SPC). Monitor process performance and identify potential issues. (eg: Implementing SPC techniques to identify out of control conditions in a chemical reactor)
- Process Simulators. Simulate process operations to identify potential issues. (eg: Simulating a reaction process to optimize catalyst loading)
- Hazard and Operability Studies (HAZOP). Identify potential hazards and operability issues in a process. (eg: Identifying potential hazards in a chlorine production facility)
Professional Organizations to Know
- American Institute of Chemical Engineers (AIChE)
- American Chemical Society (ACS)
- Society of Chemical Engineers and Biologists (SCEB)
- Institute of Chemical Engineers (IChemE)
- International Society of Automation (ISA)
- International Federation of Automatic Control (IFAC)
- American Society of Mechanical Engineers (ASME)
- American Society of Heating, Refrigerating and Air-Conditioning Engineers (ASHRAE)
- National Society of Professional Engineers (NSPE)
- Association for the Advancement of Automation (A3)
We also have Chemical Regulatory Specialist, Chemical Engineer Intern, and Chemical Plant Manager jobs reports.
Common Important Terms
- Process Flow Diagram. A process flow diagram is a graphical representation of the process steps used in a chemical process or system. It shows the sequence of steps that materials go through, from raw material to finished product.
- Mass Balance. A mass balance is a mathematical equation that relates input and output of materials in a chemical process. It is used to calculate the amount of material that needs to be added or removed in order to achieve the desired output.
- Chemical Reactions. This refers to the process of breaking and forming bonds between atoms or molecules to form different substances. It is an essential part of chemical engineering as it helps to design and control processes.
- Material and Energy Balances. Material and energy balances are equations that are used to calculate the amount of energy and materials in a system. They are used to understand how much energy is used in a process and how it is distributed among different components.
- Heat Transfer. Heat transfer is the process of transferring heat from one place to another. It is important in chemical engineering as it helps to control the temperature of a process and ensure that enough heat is available for chemical reactions.
- Process Design. Process design is the process of creating a detailed plan for a chemical process. It involves developing the process flow diagram, material and energy balances, and other necessary calculations for a safe and efficient operation.
- Process Optimization. Process optimization is the process of adjusting a chemical process to make it more efficient. This involves making changes to the process design, such as changing the reactor size, adjusting feed rates, or changing temperatures and pressures.
Frequently Asked Questions
What is a Chemical Process Engineer?
A Chemical Process Engineer is a professional who uses chemistry, engineering, and technology to develop, design, improve, and maintain chemical processes in industrial settings.
What qualifications are required to become a Chemical Process Engineer?
Generally, a Chemical Process Engineer requires at least a bachelor's degree in chemical engineering or a related field such as applied science or chemistry. Additionally, knowledge of engineering principles and experience working in a chemical plant are beneficial.
What are the job duties of a Chemical Process Engineer?
The job duties of a Chemical Process Engineer include designing, testing, and overseeing the implementation of chemical processes; troubleshooting existing processes; developing safety protocols; and conducting experiments to optimize process efficiency.
What types of industries employ Chemical Process Engineers?
Chemical Process Engineers are employed in a wide range of industries, including oil and gas, manufacturing, pharmaceuticals, biotechnology, food and beverage processing, and energy production.
What is the salary range for a Chemical Process Engineer?
According to the U.S. Bureau of Labor Statistics, the median annual salary for a Chemical Process Engineer is $103,520. Salaries can vary depending on experience, location, industry, and employer.
What are jobs related with Chemical Process Engineer?
- Chemical Safety Coordinator
- Chemical Sales Representative
- Chemical Quality Control Analyst
- Chemical Process Safety Engineer
- Chemical Plant Operator
- Chemical Inspector
- Chemical Plant Process Engineer
Web Resources
- Chemical Process Engineer | NC State Online and Distance ¦ online-distance.ncsu.edu
- Process Engineer/Chemical Engineer Career & Internship ¦ careers.uw.edu
- BSc (Hons) Chemical & Process Engineering | The Department of Chem¦ sta.uwi.edu
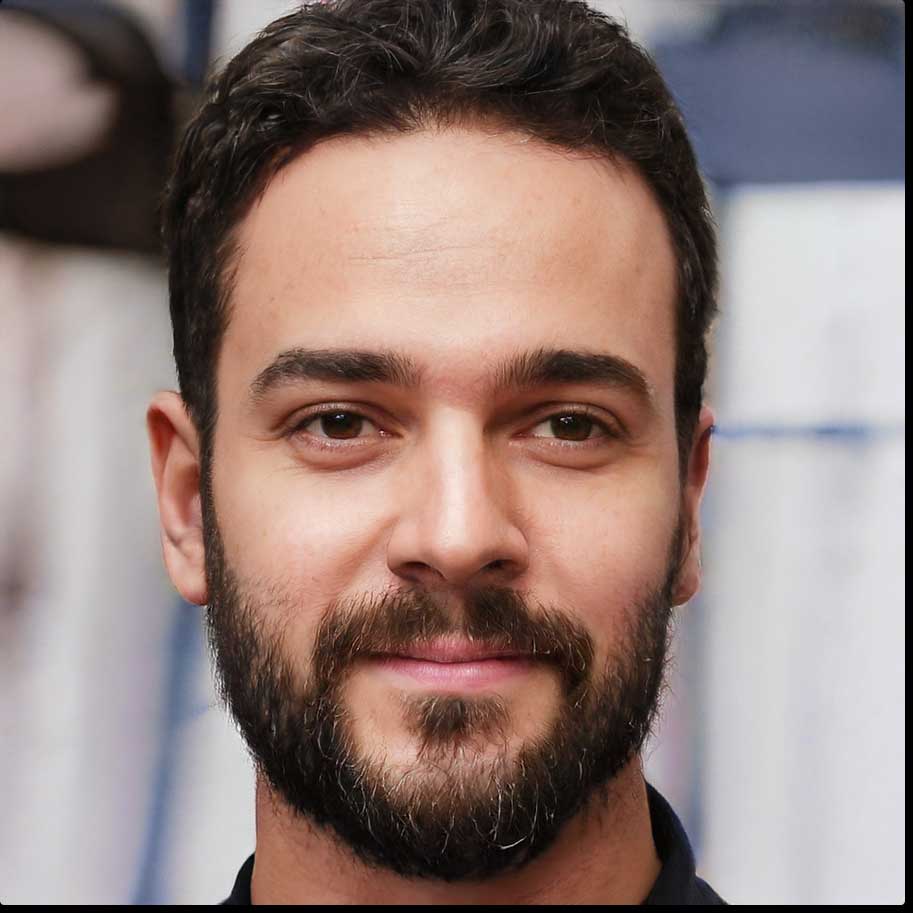