How to Be Textile Presser - Job Description, Skills, and Interview Questions
Textile pressers are responsible for a variety of tasks related to pressing and finishing textiles. The primary cause of their job is to ensure that the finished product meets quality standards. As a result, they often take careful measurements and inspect fabrics for any flaws or imperfections.
They also use a variety of pressing techniques such as steam pressing, dry pressing, and using a flatiron. These techniques help to remove wrinkles, shrinkage, or other irregularities from the fabric. Furthermore, textile pressers are also responsible for folding and packaging the finished product for shipment.
textile pressers play a vital role in the manufacturing process, providing the final touches to ensure that the end product is of the highest quality.
Steps How to Become
- Obtain a High School Diploma or GED. Most employers require a high school diploma or equivalent for Textile Pressers. Those without a diploma can pursue a GED and take courses in mathematics, science, and English.
- Complete On-the-Job Training. Textile Pressers typically require on-the-job training. Employers provide training to teach the basics of pressing and fabric care.
- Become Knowledgeable About Textiles. Textile Pressers must be knowledgeable about textiles and pressing techniques. They must be familiar with various fabrics and their properties, as well as the various pressing methods used to achieve different results.
- Practice with Different Fabrics. Textile Pressers must become proficient at pressing different fabrics. This requires practice with fabrics such as wool, cotton, linen, and silk.
- Become Certified. Textile Pressers can become certified in their field through organizations such as the International Fabricare Institute (IFI). This certification is not required, but it can help demonstrate a level of expertise to employers.
- Continue Education. Continuing education is important for Textile Pressers. Staying up-to-date on new processes and techniques is essential to staying competitive in the field.
Textile pressers play an important role in the clothing and textile industry, as they are responsible for pressing clothes and other fabric items to achieve a professional finish. To become a skilled and qualified presser, it is important to have a good knowledge of the different fabrics, their properties, and the pressing techniques associated with them. technical skills such as the ability to set up and operate pressing equipment, use a steam iron, and hang garments properly are essential.
Furthermore, physical strength is important as pressers often need to move heavy pressing machines and handle bulky materials. Finally, communication and organizational skills are also important for success as pressers need to work with customers to understand their needs and meet their specifications. With the right combination of technical, physical, and interpersonal skills, textile pressers can become highly skilled and qualified professionals.
You may want to check Textile Plant Manager, Textile Finisher, and Textile Engineer Technician for alternative.
Job Description
- Inspect textiles to determine the need for pressing or steaming.
- Set up and adjust pressing equipment according to fabric type and customer specifications.
- Apply steam, pressure and heat to fabrics to create the desired shape.
- Monitor the pressing process to ensure fabric is not damaged.
- Remove finished items from pressing equipment and inspect for quality.
- Touch up items with irons or steamers as needed.
- Fold, wrap, and package items for shipment according to customer specifications.
- Maintain a clean and organized workspace.
- Keep accurate records of production and quality control results.
- Repair and maintain pressing equipment as needed.
Skills and Competencies to Have
- Knowledge of pressing techniques and methods.
- Ability to read and interpret fabric care labels.
- Skillful manipulation of pressing equipment and tools such as irons, steamers and pressing machines.
- Ability to maintain a clean and organized workspace.
- Ability to identify fabric characteristics such as fibers, weaves, finishes, etc.
- Attention to detail to ensure quality work.
- Ability to work quickly and efficiently while maintaining quality standards.
- Ability to lift and move heavy bundles of fabric.
- Ability to follow verbal and written instructions.
- Good communication skills.
Textile Pressers play an important role in the production of clothing, linens, and other textiles. Their job is to press and finish the fabric so that it looks its best. The primary skill required for this position is a great attention to detail.
Textile Pressers must have the ability to inspect the fabric for imperfections and then use their expertise to press it to perfection. Textile Pressers must have knowledge of different fabrics and be able to adjust the temperature and pressure of the press to suit the material. They must also be able to identify basic patterns and have a good working knowledge of the industry.
With all of these skills, Textile Pressers can help ensure the quality of the garments they are working on, while also helping protect the longevity of the fabric. In the end, their attention to detail and knowledge of the industry can contribute greatly to the success of any textiles-related business.
Textile Colorist, Textile Maintenance Technician, and Textile Knitting Technician are related jobs you may like.
Frequent Interview Questions
- How have you handled difficult situations with customers in the past?
- What experience do you have in pressing large volumes of fabric quickly and accurately?
- In your experience, what techniques have you found to be most effective when pressing fabric?
- Describe a time when you had to problem-solve a pressing issue with a piece of fabric.
- Do you have any experience with computer-controlled pressing machines?
- What safety protocols do you follow when operating a textile press?
- How do you ensure that the material is pressed evenly with no wrinkles or creases?
- How do you react to sudden changes in production orders or deadlines?
- What methods do you use to keep track of the fabric and garment pieces you are pressing?
- How do you handle tasks that require a high degree of accuracy?
Common Tools in Industry
- Iron. Used to press fabric and remove wrinkles. (eg: steam iron)
- Steam Press. A machine used to press fabric with steam to remove wrinkles. (eg: SINGER Steam Press)
- Hand Steamer. A handheld device used to press fabric with steam to remove wrinkles. (eg: Rowenta Hand Steamer)
- Tailors Ham. A thick, rounded ham-shaped ironing pad used to press curved areas of fabric. (eg: Hoffman Tailors Ham)
- Seam Roll. A cylindrical ironing tool used to press seams flat. (eg: The Presser Seam Roll)
- Clothing Ironing Board. A board with a heat-resistant surface and adjustable height that is used to press fabric. (eg: Household Essentials Ironing Board)
- Press Cloth. A thin, lightweight cloth placed between the iron and the fabric to protect it from direct heat. (eg: Magic Press Cloth)
Professional Organizations to Know
- International Textile and Apparel Association (ITAA)
- American Apparel Producers Network (AAPN)
- Association of Textile, Apparel and Materials Professionals (ATAM)
- National Cleaners Association (NCA)
- Drycleaning and Laundry Institute (DLI)
- American Association of Textile Chemists and Colorists (AATCC)
- International Fabricare Institute (IFI)
- National Council of Textile Organizations (NCTO)
- American Textile Machinery Association (ATMA)
- International Fabricare Association (IFA)
We also have Textile Engineer, Textile Sampler, and Textile Supervisor jobs reports.
Common Important Terms
- Textile Finishing. The process of making fabric look and feel better by applying a variety of treatments such as softening, water repellency, and flame retardancy.
- Fabric Dyeing. The process of coloring fabrics with dyes or pigments to make them more attractive.
- Textile Printing. The process of applying a design to fabric using digital or screen printing.
- Textile Weaving. The process of interlacing two sets of yarns or threads to make fabric.
- Textile Cutting. The process of cutting fabric into different shapes and sizes using tools such as scissors or a rotary cutter.
- Textile Pressing. The process of applying pressure or heat to fabric in order to make it flat, smooth, and wrinkle-free.
Frequently Asked Questions
What does a Textile Presser do?
A Textile Presser is responsible for operating pressing machines to press, shape and finish garments, linens and other fabrics to achieve a desired look and texture.
What qualifications are needed for a Textile Presser?
Textile Pressers typically need a high school diploma or equivalent, as well as experience operating various pressing machines. Most employers will provide on-the-job training.
What is the average salary of a Textile Presser?
According to PayScale, the average salary for a Textile Presser ranges from $22,959 - $36,621 per year.
What type of environment do Textile Pressers work in?
Textile Pressers typically work in commercial laundry and dry-cleaning establishments, apparel manufacturing facilities or textile mills. The working environment is usually loud and may involve standing for long periods of time.
What are the primary responsibilities of a Textile Presser?
The primary responsibilities of a Textile Presser include operating pressing machines, inspecting pressed garments for any defects, and finishing fabrics according to customer specifications. Additionally, they may be responsible for maintaining their equipment and reporting any issues to their supervisor.
What are jobs related with Textile Presser?
- Textile Factory Manager
- Textile Dry Cleaner
- Textile Sales Representative
- Textile Merchandiser
- Textile Printer
- Textile Dyer
- Textile Inspector
- Textile Pattern Maker
- Textile Dye House Worker
- Textile Testing Technician
Web Resources
- Wilson College of Textiles textiles.ncsu.edu
- Textile Design | Wilson College of Textiles textiles.ncsu.edu
- Comfort Performance | Textile Protection And Comfort Center | NC Stat¦ textiles.ncsu.edu
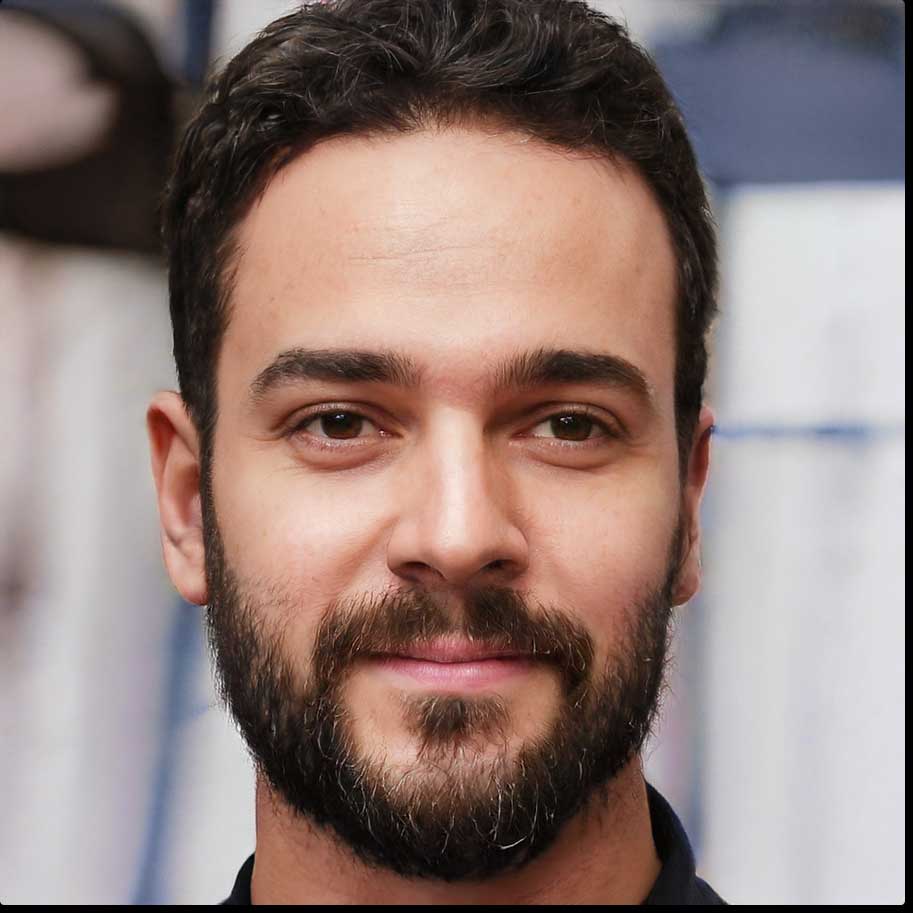