How to Be Textile Printer - Job Description, Skills, and Interview Questions
Textile printing is an essential process in the clothing and apparel industry, as it allows for the production of unique, personalized designs. The process involves the application of inks and other colorants onto fabric using a variety of printing techniques. The result is a vivid, intricate pattern on the fabric that can be used to create garments and other items.
One of the primary advantages of textile printing is its ability to create detailed designs quickly and economically. the quality of the colors used can be manipulated to produce a wide variety of effects. This flexibility provides designers with more options for creating unique garments and products.
As an added benefit, the colors used in textile printing are usually highly durable, making them resistant to fading and wear. Textile printing is a crucial step in the apparel process, as it allows for the creation of unique products that stand out from the competition.
Steps How to Become
- Obtain a high school diploma or GED. Textile printing requires detailed knowledge of colors, fabric and design, so a high school education is a must.
- Consider taking college classes in art, design and color theory. These classes provide the foundational knowledge needed to become a successful textile printer.
- Enroll in a textile printing program at a trade school or community college. These programs provide hands-on experience with various types of fabric, inks and printing techniques.
- Apply for a job as a textile printer. Many employers prefer to hire employees with a few years of experience, so having a degree or certificate from a trade school can help you stand out.
- Gain experience in the field. Textile printing is a very specialized profession, and it takes time to learn how to create the best quality prints possible. Working with experienced professionals can help you learn the ropes quickly.
- Develop your portfolio. Showcase your best work to potential employers or clients. This will help demonstrate your skill level and give potential customers an idea of what you are capable of.
Textile printing is an art form that has been around for centuries, but it has only grown in popularity in recent years. The process of textile printing involves the transfer of a design onto fabric using specialized equipment and technology. To achieve ideal and qualified results, it is important to select the right equipment, supplies, and techniques.
Quality inks, a steady hand, and a well-maintained printing machine are necessary for a successful textile printing project. pre-treatment of the fabric is necessary to ensure a smooth transfer of the design. Taking the time to properly prepare the fabric will reduce errors and ensure a more consistent result.
With careful preparation and attention to detail, textile printing can produce beautiful and long-lasting results.
You may want to check Textile Sample Maker, Textile Designer Assistant, and Textile Sampler for alternative.
Job Description
- Set up and operate Textile Printer machines to print designs, text, or other images on fabric.
- Monitor the quality of prints and adjust the Textile Printer settings as needed.
- Select colors, patterns, and materials to be used for printing.
- Prepare screens for printing by coating them with light-sensitive emulsion and exposing them to ultraviolet light.
- Clean and maintain Textile Printer machines and equipment to ensure optimal performance.
- Troubleshoot and repair any malfunctioning Textile Printer machines.
- Design custom prints based on customer specifications.
- Monitor the progress of prints and make adjustments as needed.
- Keep accurate records of all work completed.
- Perform final quality checks before releasing prints to customers.
Skills and Competencies to Have
- Knowledge of different types of fabrics and materials used in textile printing
- Understanding of color theory and its application to textile printing
- Ability to read and understand design specifications
- Proficiency in operating textile printing equipment
- Experience with setting up and adjusting printing machines
- Ability to troubleshoot technical issues related to printing machines
- Understanding of different printing techniques and processes
- Ability to prepare and mix inks and dyes for various applications
- Knowledge of safety procedures in a textile printing environment
- Ability to manage projects from start to finish
- Excellent organizational and time management skills
- Strong communication skills
- Attention to detail
- Ability to work independently and in a team environment
Having an understanding of textile printing is an essential skill for anyone who wants to pursue a career in the textile industry. Knowing how to properly use and maintain a textile printer can be the difference between a successful print job and a failed one. To get the best results, it is important to have a good understanding of the different types of printers available, the steps involved in the printing process, and the materials that can be used with each type of printer.
it is also important to understand the various techniques used to achieve certain effects on the printed fabric. Knowing the correct settings, temperatures and ink types to use can help ensure that the desired results are achieved. Lastly, having knowledge of the different types of fabrics and how they react to inks and dyes can help ensure that the prints turn out correctly.
Textile Finishing Supervisor, Textile Presser, and Textile Supervisor are related jobs you may like.
Frequent Interview Questions
- What experience do you have in the textile printing industry?
- How would you describe your technical skills related to textile printing?
- What challenges have you faced in textile printing, and how did you overcome them?
- What strategies do you use to ensure the accuracy of your work?
- What is your experience with various types of fabrics and fibers?
- How do you keep up with changing trends in the textile printing industry?
- How do you handle customer requests for complex designs or prints?
- How do you stay organized and on schedule when working on multiple projects?
- How do you troubleshoot problems that arise during the printing process?
- What methods do you use to maintain the quality of prints throughout the production process?
Common Tools in Industry
- Heat Transfer Press. A tool used to press heat-applied materials onto textiles. (Example: Epson F2100 Heat Transfer Printer)
- Screen Printing Equipment. A tool used to print designs onto textiles with screens and inks. (Example: M&R Chameleon Automatic Screen Printer)
- Dye Sublimation Printer. A tool used to transfer dye onto fabric with heat and pressure. (Example: Epson SureColor F6200 Dye Sublimation Printer)
- Laser Cutter. A tool used to cut and engrave fabric with a laser beam. (Example: Trotec Speedy 300 Laser Cutter)
- Embroidery Machine. A tool used to embroider designs onto fabric with a needle and thread. (Example: Janome MB-4S Four Needle Embroidery Machine)
Professional Organizations to Know
- American Apparel and Footwear Association (AAFA)
- Textile Manufacturers Association (TMA)
- International Textile Manufacturers Federation (ITMF)
- International Textile and Apparel Association (ITAA)
- International Textile Market Association (ITMA)
- Textile Exchange
- International Association of Home Fashion Fabrics (IAHFF)
- Textile Distributors Association (TDA)
- International Textile Printers Association (ITPA)
- Specialty Graphic Imaging Association (SGIA)
We also have Textile Pattern Maker, Textile Merchandiser, and Textile Colorist jobs reports.
Common Important Terms
- Digital Printing. A printing process that uses computer-generated data to create an image onto a printable material.
- Dye-Sublimation. A printing process that uses heat to transfer dye onto materials such as fabric, paper, and plastic.
- Direct to Garment (DTG). A printing process that uses inkjet technology to directly apply ink onto fabric.
- Heat Transfer. A printing process that uses heat to transfer a design onto fabric or other materials.
- Screen Printing. A printing process that uses a mesh screen with ink to transfer a design onto fabric or other materials.
- Pre-treatment. A process used to prepare fabric for printing, such as spraying a chemical solution onto the fabric to help the ink adhere better.
- White Base Print. A printing process that involves printing a white layer of ink first, followed by the desired design, in order to make colors appear brighter and more vibrant on dark-colored fabrics.
Frequently Asked Questions
What is a Textile Printer?
A Textile Printer is a type of printer used for printing on fabrics, such as t-shirts and other apparel.
What type of ink is used in Textile Printing?
Textile Printing typically uses water-based or pigment ink, which is designed to be durable and colorfast.
What types of fabrics can be printed with a Textile Printer?
Textile Printers can be used to print on a variety of fabrics, including cotton, polyester, nylon, and other synthetic fabrics.
What is the maximum print size for a Textile Printer?
The maximum print size for a Textile Printer will vary depending on the model, but many models can print up to 16"x20" or even larger.
What are some common uses for a Textile Printer?
Textile Printers are commonly used for printing custom t-shirts, apparel, banners, flags, and other fabric items.
What are jobs related with Textile Printer?
- Textile Maintenance Technician
- Textile Finishing Operator
- Textile Mill Worker
- Textile Quality Inspector
- Textile Technologist
- Textile Dyer
- Textile Dye House Worker
- Textile Factory Manager
- Textile Testing Technician
- Textile Bleacher
Web Resources
- Textiles Unit Printers | Textile Connect - apps.tx.ncsu.edu apps.tx.ncsu.edu
- Textile Printing: An Introduction - SVA sva.edu
- Electronics, Textiles, and 3D Printing - Iowa State University sictr.iastate.edu
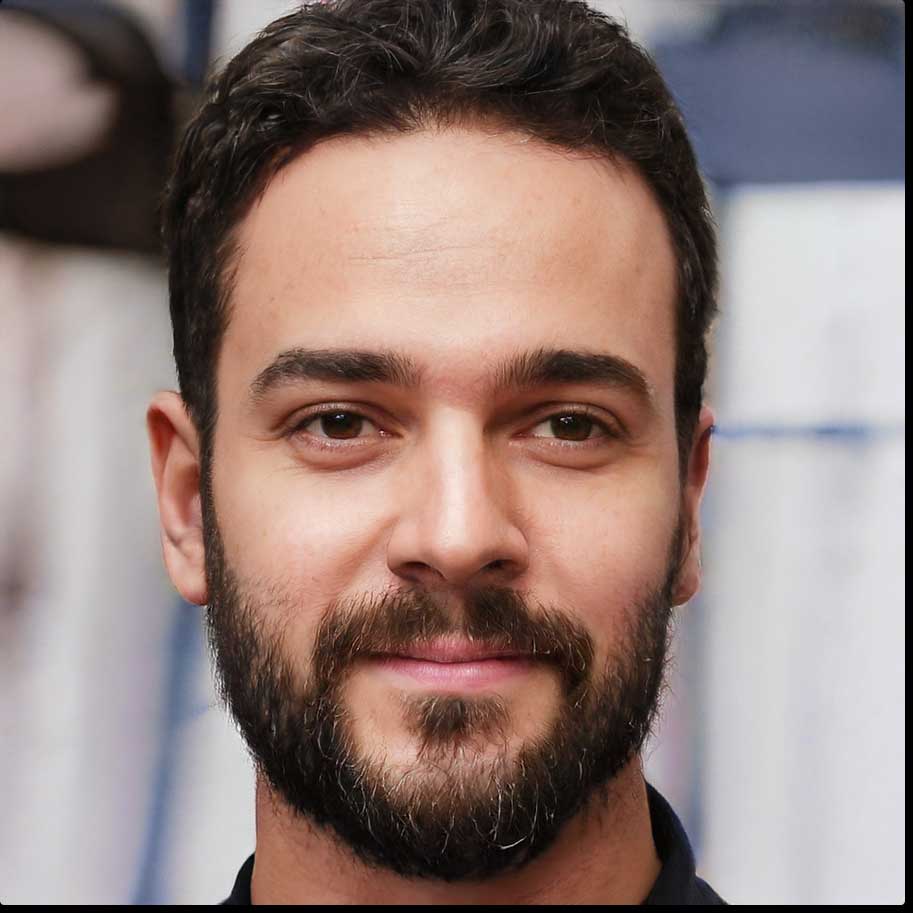