How to Be Textile Factory Manager - Job Description, Skills, and Interview Questions
The growth of the textile industry has had a significant impact on the role of the factory manager. As the demand for textile products increases, so too does the need for efficient and effective management of the production process. Factory managers are tasked with overseeing all aspects of the production process, from purchasing raw materials to scheduling production runs, inspecting quality, and managing personnel.
With the right strategies and tools in place, factory managers can increase productivity, reduce costs, and ensure that products are delivered on time and within budget. This in turn can lead to higher customer satisfaction, increased market share, and greater profitability for the business.
Steps How to Become
- Obtain a Bachelors Degree. To become a textile factory manager, you must first obtain a bachelors degree in a related field such as textile science, business, engineering, or management.
- Gain Relevant Work Experience. It is important to gain relevant work experience in textile production or management in order to become a textile factory manager. You can gain this experience through internships, apprenticeships, or on-the-job training.
- Obtain Professional Certifications. There are several professional certifications available that may give you an edge when applying for textile factory management positions. These include certifications from the American Textile Manufacturers Institute, the International Textile Manufacturers Federation, and the American Apparel and Footwear Association.
- Develop Leadership Skills. As a textile factory manager, it is important to have strong leadership skills in order to effectively manage and motivate employees. You can develop these skills by taking courses in management, communication, and problem-solving.
- Apply for Positions. Once you have obtained the necessary qualifications and experience, you can begin applying for positions as a textile factory manager. You can apply directly to companies or search for available positions on job boards and websites.
Being a textile factory manager, it is essential to stay updated and competent in order to manage the factory effectively. This can be achieved by constantly learning new production processes and staying informed of new trends in the textile industry. Keeping up with new technologies, investing in employee development, and attending industry conferences are key components to staying current.
it is important to have an understanding of the market and customer needs in order to make informed decisions about production and operations. By taking these steps, a textile factory manager can ensure that their factory remains up to date and competitive.
You may want to check Textile Finishing Supervisor, Textile Dyer, and Textile Designer Assistant for alternative.
Job Description
- Monitor and optimize production processes to ensure maximum efficiency and quality.
- Manage and oversee the day-to-day operations of the factory, including staff, machinery, materials, and resources.
- Develop and implement safety policies and procedures to ensure a safe working environment.
- Schedule production runs and coordinate with other departments to ensure timely delivery of orders.
- Ensure compliance with all relevant national and local regulations related to the production process.
- Monitor inventory levels and order supplies as needed.
- Train and supervise staff to ensure that all production tasks are completed properly and in a timely fashion.
- Analyze production data to identify potential areas for improvement.
- Develop strategies for increasing efficiency and reducing costs.
- Coordinate with suppliers to ensure timely delivery of raw materials and supplies.
Skills and Competencies to Have
- Knowledge of the textile manufacturing process
- Ability to troubleshoot production issues
- Time management skills
- Leadership and motivational skills
- Ability to multi-task and prioritize tasks
- Excellent communication and interpersonal skills
- Understanding of safety regulations
- Knowledge of quality control procedures
- Problem-solving skills
- Knowledge of relevant computer programs
- Ability to work collaboratively with a team
- Strong organizational skills
- Negotiation and budgeting skills
- Understanding of the latest trends in textile production
Being a successful textile factory manager requires a number of important skills and abilities. Strong leadership and communication skills are essential for managing teams and maintaining relationships with external stakeholders. The ability to think strategically and plan ahead is necessary to ensure the efficient running of the factory.
Effective problem solving skills and the ability to troubleshoot technical issues are also important, as are the ability to make decisions quickly and confidently. Knowledge of the latest industry trends and practices is also necessary for staying ahead of the competition. Finally, knowledge of finance, budgeting and cost management is key for keeping production costs low and ensuring profits are maximized.
These skills and abilities are crucial for successful textile factory managers.
Textile Maintenance Technician, Textile Sewing Machine Operator, and Textile Processor are related jobs you may like.
Frequent Interview Questions
- What experience do you have in managing a textile factory?
- What strategies have you implemented to increase efficiency in a textile factory?
- How would you handle a situation where a customer is unsatisfied with the quality of the product?
- How do you stay up to date with industry trends and best practices?
- Describe a time when you employed creative problem-solving in a textile factory.
- What methods do you use to motivate staff to meet goals on time?
- What safety protocols do you have in place to ensure the safety of the workers?
- How do you ensure the quality of the textiles produced meets standards?
- How do you work with suppliers to ensure timely delivery of supplies?
- What do you do to ensure compliance with labor laws and regulations?
Common Tools in Industry
- Textile Manufacturing Software. A specialized software designed to streamline the entire textile production process, from design and production to shipping and inventory management (e. g. Texbase).
- Fabrics Analysis Equipment. High-tech equipment used to test the properties of fabrics and textiles, such as strength, composition and colorfastness (e. g. Yoshida Textile Tester).
- Cutting Machines. Specialized machines used to cut fabrics into different shapes and sizes (e. g. Eastman Cutting Machine).
- Sewing Machines. Machines used to stitch two or more pieces of fabric together (e. g. Juki Industrial Sewing Machine).
- Weaving Machines. Machines used to produce fabric from yarn (e. g. Shuttleless Weaving Machine).
- Dyeing Machines. Machines used to apply color to fabrics (e. g. Dyeing Jiggers).
- Finishing Machines. Machines used to treat fabrics for a particular look or feel (e. g. Fabric Finishing Stenter).
- Quality Control Equipment. Equipment used to inspect fabrics for defects, such as color variation, shrinkage, etc. (e. g. Spectrophotometer).
Professional Organizations to Know
- American Apparel Producers Network (AAPN)
- Association of Textile, Apparel & Materials Professionals (ATAMP)
- National Council of Textile Organizations (NCTO)
- Textile Manufacturer's Association (TMA)
- International Textile Manufacturers Federation (ITMF)
- International Textile and Apparel Association (ITAA)
- American Manufacturing Trade Action Coalition (AMTAC)
- Textile Distributors Association (TDA)
- National Industrial Fabric Association (NIFA)
- American Yarn Spinners Association (AYSA)
We also have Textile Presser, Textile Inspector, and Textile Inspector and Grader jobs reports.
Common Important Terms
- Quality Assurance. The process of ensuring that products and services meet the required standards of quality.
- Production Scheduling. The process of developing and maintaining a production schedule to ensure that goods are produced on time and to the required specifications.
- Inventory Control. The process of managing available stock to ensure that it meets demand and is used in an efficient manner.
- Cost Control. The process of monitoring costs to ensure that operations remain within budget.
- Machine Maintenance. The process of keeping machines in good condition and making sure that they are regularly serviced.
- Safety Regulations. Requirements for the protection of workers, the public, and the environment from harm due to working conditions or operations.
- Industrial Relations. The relationship between employers and employees, including collective bargaining, grievance procedures, and dispute resolution.
- Human Resources. The process of recruiting, hiring, training, and managing employees in an organization.
Frequently Asked Questions
What is the role of a Textile Factory Manager?
A Textile Factory Manager is responsible for overseeing the operations of a textile manufacturing facility, including production, quality control, maintenance, safety, and personnel management.
What qualifications are needed to be a Textile Factory Manager?
Generally, a minimum of a Bachelor's degree in a related field such as textile engineering, textile technology, or industrial management is required to become a Textile Factory Manager. Experience in a manufacturing environment is also beneficial.
What are the primary responsibilities of a Textile Factory Manager?
The primary responsibilities of a Textile Factory Manager include setting production goals and targets, monitoring production efficiency, ensuring workplace safety, managing personnel, and maintaining quality standards.
What type of salary can a Textile Factory Manager expect to earn?
According to PayScale.com, the average salary for a Textile Factory Manager is $67,000 per year. Salaries can vary depending on experience and location.
What challenges does a Textile Factory Manager face?
Textile Factory Managers face a variety of challenges including meeting production goals and targets within budget, ensuring quality control, managing personnel, and ensuring compliance with safety regulations.
What are jobs related with Textile Factory Manager?
- Textile Estimator
- Textile Dry Cleaner
- Textile Supervisor
- Textile Finishing Operator
- Textile Embroidery Machine Operator
- Textile Testing Technician
- Textile Pattern Maker
- Textile Sampler
- Textile Yarn Winder
- Textile Production Planner
Web Resources
- Textile Technology Management - North Carolina State University catalog.ncsu.edu
- Textile and Apparel Management | Degree Category | University ¦ gradschool.missouri.edu
- The Factory Girl | National Museum of American History americanhistory.si.edu
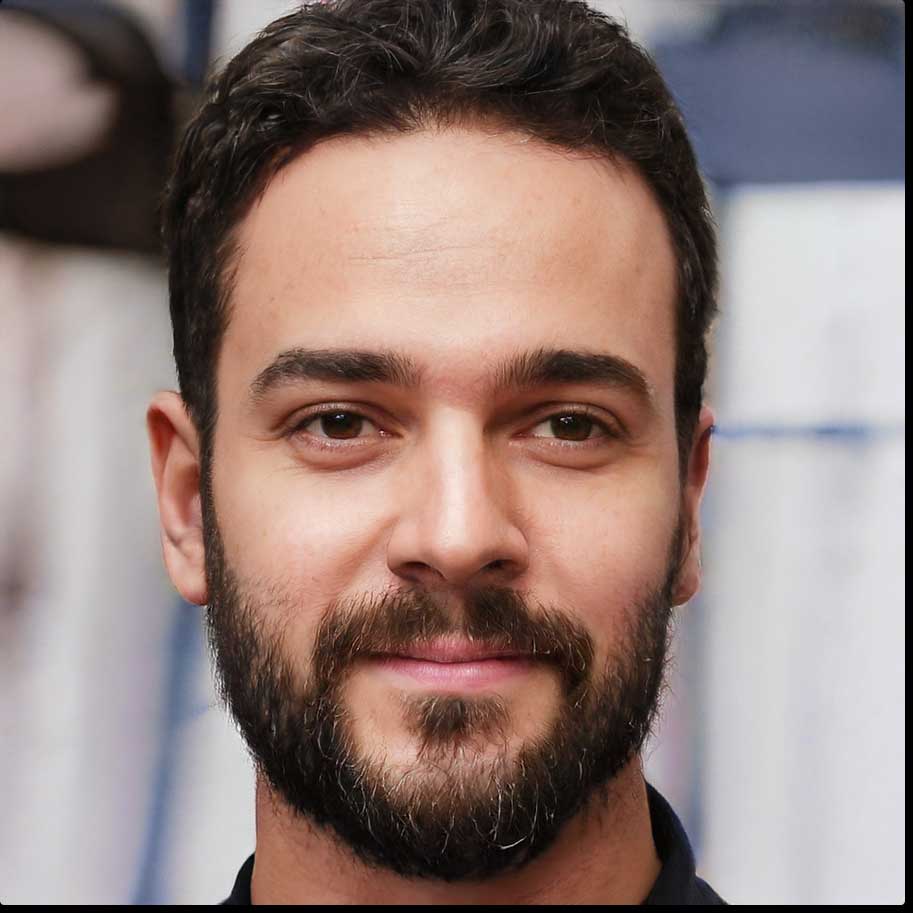