How to Be Textile Plant Manager - Job Description, Skills, and Interview Questions
The success of a textile plant largely depends on the manager's capability to efficiently manage the various facets of the facility. A textile plant manager must possess excellent organizational and leadership skills, as well as an in-depth knowledge of the production processes, in order to ensure that the plant runs smoothly. This includes overseeing the manufacturing process, ensuring proper maintenance of the machines and equipment, managing staff, meeting production goals, and adhering to safety measures.
When these tasks are successfully completed, the result is increased productivity, improved quality of the products produced, and higher profits for the plant. On the other hand, if any of these areas are neglected, it can lead to costly delays, decreased efficiency and profits, and even safety hazards.
Steps How to Become
- Earn a Bachelor's Degree. The first step to becoming a textile plant manager is to earn a bachelor's degree in a relevant field, such as business management, industrial engineering, or textile manufacturing. Most employers prefer applicants with a degree, as it provides a well-rounded understanding of the industry and a strong background of knowledge.
- Gain Relevant Experience. Many employers prefer job applicants to have at least two years of experience in the textile industry. It is important to gain experience in areas related to the position, such as machine operation, quality control, and product development.
- Obtain Certification. The International Textile and Apparel Association (ITAA) offers certification for textile plant managers. This certification can be used to demonstrate competency and expertise in the field. To obtain certification, applicants must pass an exam and complete a certain number of hours of continuing education.
- Find Employment. Once the necessary qualifications have been acquired, it is time to search for employment. Textile plant manager positions can often be found on job boards or through networking opportunities. Applying directly to plants or mills is another option.
- Develop Soft Skills. As a textile plant manager, it is important to have strong interpersonal skills, such as communication and problem-solving. It is also important to be able to work well with other departments and management teams.
- Maintain Professionalism. Professionalism is key in any job, but especially in a managerial role. It is important to maintain a professional image, both in appearance and attitude, in order to be successful in the position.
To become a successful and competent textile plant manager, it is important to have a combination of both skills and experience. One must understand the technical aspects of the production process, including design, production planning, quality control, and cost management. they must be able to effectively manage people and resources to improve efficiency, quality, and customer satisfaction.
To achieve this, they must have strong communication skills, problem-solving abilities, and organizational abilities. Furthermore, they must possess a deep knowledge of the industry and its regulations to ensure compliance. By having all these qualifications, a textile plant manager will be able to successfully lead a team and increase production and profit.
You may want to check Textile Chemical Technician, Textile Pattern Maker, and Textile Production Supervisor for alternative.
Job Description
- Oversee daily operations of the textile plant
- Develop and implement new production strategies
- Monitor and adjust production processes to maximize efficiency
- Ensure compliance with all safety regulations, environmental regulations, and labor laws
- Set and monitor production goals
- Monitor inventory levels and order materials as needed
- Manage personnel, including hiring, training, and evaluating performance
- Develop production budgets and monitor costs
- Maintain quality standards of the finished product
- Negotiate contracts with suppliers and vendors
- Participate in industry trade shows and conferences to stay up to date on the latest developments in the industry
- Troubleshoot production problems and resolve any issues that arise
Skills and Competencies to Have
- Leadership and Management: Demonstrated ability to lead and motivate a team, set goals, delegate work, and manage performance.
- Strategic Planning: Ability to develop and implement long-term strategies to achieve organizational objectives.
- Technical Knowledge: In-depth knowledge of textile production processes and technologies, as well as quality assurance principles and practices.
- Budgeting and Cost Control: Proficiency in budgeting and cost management techniques, including the ability to forecast production costs and identify areas of potential savings.
- Operations Management: Ability to plan and coordinate all aspects of production, including scheduling, material management, and equipment maintenance.
- Problem-Solving: Ability to troubleshoot operational issues and devise effective solutions.
- Communication: Excellent verbal and written communication skills, with the ability to provide clear direction and instruction to staff.
- Health and Safety: Knowledge of health and safety regulations in a textile production environment, along with the ability to ensure compliance and promote a safe working environment.
- Quality Control: Expertise in quality control processes, with a commitment to producing high-quality products in a timely fashion.
- Vendor Relations: Experience in negotiating contracts with vendors and monitoring performance to ensure quality and reliability of services.
Textile Plant Managers must have a wide range of skills in order to effectively manage a textile plant. One of the most important skills is the ability to effectively manage personnel, as the Plant Manager is responsible for hiring, training, and motivating employees. they must have strong organizational and problem-solving skills to ensure that the production process runs smoothly.
They must be able to identify issues and resolve them quickly and efficiently. Furthermore, they must have an in-depth knowledge of the machinery and processes used in the plant, as well as an understanding of the materials used for production. Finally, Plant Managers must possess strong communication skills to maintain good relationships with customers, suppliers, and other stakeholders.
Without these skills, a Textile Plant Manager will be unable to effectively manage the plant and ensure successful operations.
Textile Quality Assurance Analyst, Textile Machine Operator, and Textile Fabricator are related jobs you may like.
Frequent Interview Questions
- What experience do you have in the textile industry?
- How would you manage a production line to ensure efficiency and quality standards are met?
- How have you identified areas of improvement in textile production processes?
- What strategies have you implemented to reduce costs and optimize profits in the textile industry?
- What methods do you use to stay up-to-date on the latest trends in the textile industry?
- How have you handled situations where employee safety was at risk?
- Describe your experience in developing and implementing operational plans for a textile plant.
- How do you ensure that all textile equipment is properly maintained and serviced?
- Describe a time when you had to collaborate with other departments in order to reach a successful outcome for the textile plant.
- What strategies do you use to motivate employees and maintain high morale in the workplace?
Common Tools in Industry
- Spinning machines. These machines are used to convert fibers into yarns. (eg: Cotton spinning machine)
- Weaving machines. These machines are used to interlace yarns to form fabrics. (eg: Rapier loom)
- Dyeing and Finishing Machines. These machines are used to give color, luster, and softness to fabrics. (eg: Flow dyeing machine)
- Cutting Machines. These machines are used to cut fabrics into desired shapes and sizes. (eg: Computer-controlled knife cutting machine)
- Sewing Machines. These machines are used to stitch fabrics together. (eg: Industrial overlock sewing machine)
- Quality Control Equipment. These machines are used to inspect the quality of the fabrics. (eg: Fabric inspection machine)
- Warehouse Management System (WMS). This system is used to track and manage the inventory of raw materials, intermediate products, and finished products. (eg: RFID-based WMS)
- Automation Software. This software is used to automate various processes such as material handling, inventory management, and production scheduling. (eg: ERP software)
Professional Organizations to Know
- American Textile Manufacturers Institute (ATMI)
- International Textile Manufacturers Federation (ITMF)
- National Council of Textile Organizations (NCTO)
- American Apparel & Footwear Association (AAFA)
- Textile Exchange
- International Association of Man-Made Fibre Producers (IAMFPR)
- Woolmark Company
- Cotton Council International (CCI)
- The Textile Institute
- International Textiles and Apparel Association (ITAA)
We also have Textile Dyer, Textile Sales Representative, and Textile Mill Worker jobs reports.
Common Important Terms
- Yarn. A continuous strand of interlocked fibers, used in weaving and knitting.
- Looms. Machines used to weave fabric from yarn.
- Weaving. Process of interlacing two sets of yarn or thread to create fabric.
- Knitting. Process of interlocking loops of yarn to create fabric.
- Sewing. Process of joining two pieces of fabric together using thread.
- Dyeing. Process of adding color to fabric through various dyes or pigments.
- Finishing. Final process of a garment or fabric production, which includes pressing, folding, and packaging.
- Quality Assurance. Process of ensuring that the product meets certain standards and requirements.
- Maintenance. Process of keeping equipment in good working condition and making necessary repairs when needed.
Frequently Asked Questions
Q1: What is the main responsibility of a Textile Plant Manager? A1: The primary responsibility of a Textile Plant Manager is to ensure efficient production and operations of the plant, overseeing all personnel, equipment, and processes. Q2: How many employees does a Textile Plant Manager typically oversee? A2: A Textile Plant Manager typically oversees a team of anywhere from 10 to 100 employees. Q3: What skills are required to be a successful Textile Plant Manager? A3: A successful Textile Plant Manager must possess strong leadership and organizational skills, be detail-oriented, have excellent communication skills, and have a thorough understanding of the textile industry. Q4: What type of educational background is necessary to become a Textile Plant Manager? A4: Most Textile Plant Managers have a Bachelor's degree in business, engineering, or a related field. In some cases, extensive experience in the textile industry may be sufficient. Q5: What is the average salary of a Textile Plant Manager? A5: The average salary of a Textile Plant Manager ranges from $50,000 to $90,000 per year, depending on experience and the size of the plant.What are jobs related with Textile Plant Manager?
- Textile Finishing Supervisor
- Textile Designer Assistant
- Textile Factory Manager
- Textile Quality Inspector
- Textile Knitter Operator
- Textile Processor
- Textile Technologist
- Textile Dry Cleaner
- Textile Inspector
- Textile Spinner
Web Resources
- Fashion & Textile Management | Majors - North Carolina State ¦ majorsandminors.dasa.ncsu.edu
- Textile and Apparel Management | NC State University Libraries www.lib.ncsu.edu
- Plants and Textiles | Cornell Garden-Based Learning gardening.cals.cornell.edu
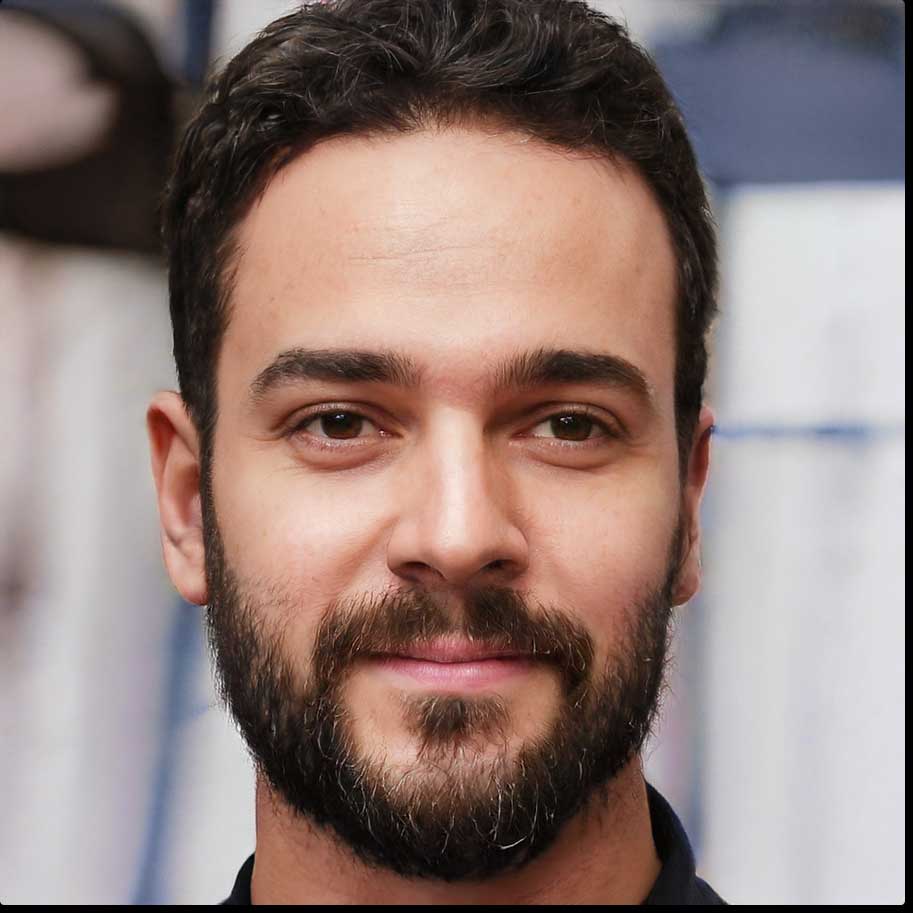