How to Be Store Warehouse Supervisor - Job Description, Skills, and Interview Questions
Warehouse supervisors are responsible for ensuring efficient warehouse operations, which is essential for the success of any organization. The supervisor is responsible for managing the resources available to them, such as inventory, equipment, and personnel. By doing so, they can ensure that the warehouse is operating at optimal levels, leading to increased productivity and customer satisfaction.
This can result in improved customer service, higher profits, and better business relationships. supervisors also play an important role in safety, by ensuring that all safety protocols are followed and that the warehouse is free from hazards. the effective management of a warehouse by a supervisor can have a hugely positive impact on an organizationâs success.
Steps How to Become
- Earn a High School Diploma or GED. Store warehouse supervisors typically need a high school diploma or equivalent in order to qualify for the position.
- Obtain Work Experience. Most employers will require applicants to have prior work experience in a warehouse setting or in a related area, such as shipping and receiving.
- Get Certified. Some employers may require store warehouse supervisors to possess a certification in warehouse management or supply chain management. To obtain this certification, individuals must complete a training program and pass an exam.
- Obtain Additional Training. Many employers require store warehouse supervisors to complete additional training, such as safety training and customer service training.
- Obtain Leadership Skills. Store warehouse supervisors must possess strong leadership skills in order to manage the staff and operations of the warehouse. They should also be good at problem-solving, communication, and organization.
- Consider Obtaining a Degree. Some employers may require store warehouse supervisors to have a degree in business, logistics, or a related field. Additionally, a degree may help applicants stand out from other applicants.
In order to keep a warehouse running efficiently and up-to-date, a Warehouse Supervisor should ensure that the right systems are in place. This includes monitoring warehouse inventory, implementing protocols for the storage and handling of goods, and maintaining accurate records of all transactions. Good communication between the warehouse staff and other departments is essential for the smooth running of the warehouse.
By having the right systems and processes in place, the Warehouse Supervisor can ensure that goods are delivered in a timely manner, that inventory is accurately tracked, and that any discrepancies are addressed quickly. In addition, the Supervisor should regularly review the warehouse operations to identify areas for improvement and ensure that all health and safety regulations are adhered to.
You may want to check Store Coordinator, Store Salesperson, and Store Manager Assistant for alternative.
Job Description
- Oversee the day-to-day warehouse operations, including inventory control, order fulfillment, and shipping/receiving.
- Develop and implement warehouse policies and procedures.
- Monitor and maintain stock levels, identify and resolve discrepancies.
- Coordinate with internal departments and external vendors to ensure efficient operations.
- Ensure compliance with safety standards and regulations.
- Hire, train, and supervise warehouse staff.
- Develop and implement strategies to maximize efficiency and minimize costs.
- Monitor and manage performance of warehouse employees.
- Ensure accurate and timely order fulfillment, shipping/receiving, and inventory control.
- Troubleshoot and resolve any warehouse issues or problems.
Skills and Competencies to Have
- Leadership and management skills
- Problem-solving and decision-making abilities
- Excellent communication and interpersonal skills
- Knowledge of inventory management systems
- Ability to use computer software to track inventory, manage orders, and generate reports
- Ability to plan and organize work effectively
- Ability to set priorities and handle multiple tasks simultaneously
- Knowledge of safety procedures
- Ability to lift heavy objects and move stock
- Knowledge of warehouse operations and best practices
Effective communication is an essential skill for a Warehouse Supervisor to possess. The ability to clearly and concisely communicate instructions to team members is key to managing a successful warehouse operation. With effective communication, Warehouse Supervisors can ensure that tasks are completed on time and that instructions are followed accurately.
In addition, effective communication helps build strong working relationships between supervisors and their team members, which improves morale and overall productivity. Furthermore, Warehouse Supervisors need to be able to communicate with their own supervisors and managers in order to provide feedback, suggest improvements, and keep them informed of progress or any issues that arise. Poor communication can lead to inefficiencies, misunderstandings, and delays, so it is crucial that Warehouse Supervisors have strong communication abilities.
Store Procurement Specialist, Store Inventory Coordinator, and Store Director are related jobs you may like.
Frequent Interview Questions
- What experience do you have in managing a warehouse?
- How do you ensure the safety of warehouse personnel?
- Have you ever had to deal with a difficult customer complaint related to the warehouse?
- How would you handle a situation where there is a conflict between warehouse workers?
- How do you ensure proper inventory control and accuracy of orders?
- What strategies do you have for cost-effectively managing warehouse operations?
- How do you motivate and engage your team members?
- What techniques have you used to increase productivity and efficiency in the warehouse?
- Are you familiar with new technologies that can be used to improve inventory management?
- What systems do you have in place to monitor warehouse performance and track key metrics?
Common Tools in Industry
- Warehouse Management System (WMS) . A computerized system that manages the storage and movement of inventory within a warehouse. (eg: Oracle WMS)
- Inventory Control Software . Software used to track and manage inventory levels, orders, and deliveries. (eg: Fishbowl Inventory)
- Warehouse Layout Planning Software . Software used to plan, design, and optimize the layout of warehouses for efficient operations. (eg: Logistyx Technologies)
- Barcode Scanner . A device used to scan barcodes and record data in order to track inventory. (eg: Honeywell Voyager)
- Automated Guided Vehicle (AGV) . A robotic vehicle used to transport goods within a warehouse. (eg: Locus Robotics)
- Pick-to-Light System . An automated system that uses lights to indicate where items should be picked in order to fulfill an order. (eg: Knapp Pick-To-Light System)
- Voice System . A voice-activated system that enables workers to receive instructions hands-free while picking orders. (eg: VoicePick)
- Radio Frequency (RF) Scanner . A device that uses radio frequencies to scan and read barcodes, as well as track inventory movements. (eg: Zebra RFD8500 RFID Reader)
Professional Organizations to Know
- International Warehouse Logistics Association (IWLA)
- Material Handling Industry of America (MHIA)
- National Association of Warehouse and Logistics Managers (NAWLM)
- Association for Supply Chain Management (ASCM)
- Council of Supply Chain Management Professionals (CSCMP)
- American Society of Transportation and Logistics (ASTL)
- International Council of Systems Engineering (INCOSE)
- Supply Chain Council (SCC)
- National Retail Federation (NRF)
- National Institute for Storage Tank Management (NISTM)
We also have Store Logistics Manager, Store Buyer, and Store Design Manager jobs reports.
Common Important Terms
- Inventory Management. A business practice of tracking and managing the products or goods a company has in its possession.
- Warehouse Layout. The physical arrangement of the facility, including the placement and design of storage areas, loading docks, and other elements.
- Picking/Packing. The process of selecting items from inventory and loading them into boxes or containers for shipment.
- Shipping/Receiving. Managing the inbound and outbound flow of goods, including verifying shipments and preparing them for delivery.
- Quality Control. Ensuring that products meet the companys standards before they are shipped out.
- Forklift Operation. The use of a forklift to move merchandise within the warehouse.
- Health and Safety Protocols. Following guidelines to ensure a safe workplace for employees.
Frequently Asked Questions
What is the average salary for a Store Warehouse Supervisor?
According to PayScale, the average salary for a Store Warehouse Supervisor is $45,719 per year.
What duties does a Store Warehouse Supervisor typically perform?
A Store Warehouse Supervisor is responsible for overseeing warehouse operations, ensuring efficient and safe storage and retrieval of goods, managing inventory control systems, and leading warehouse staff.
What qualifications should a Store Warehouse Supervisor have?
A Store Warehouse Supervisor should have strong leadership and organizational skills, knowledge of warehouse operations and safety protocols, and experience managing a team.
What are the typical working hours for a Store Warehouse Supervisor?
Typical working hours for a Store Warehouse Supervisor may vary depending on the company and their individual schedules, but generally involve 40-50 hours per week.
What is the job outlook for Store Warehouse Supervisors?
The job outlook for Store Warehouse Supervisors is expected to grow at an average rate over the next decade, with an estimated 5% employment growth rate through 2029.
What are jobs related with Store Warehouse Supervisor?
- Store Operations Manager
- Store Keeper
- Store Manager of Operations
- Store Department Head
- Store Planner
- Store Cashier
- Store Manager In Training
- Store Quality Assurance Supervisor
- Store Security Officer
- Store Project Manager
Web Resources
- Warehouse / Distribution Supervisor | NC State Online and ¦ online-distance.ncsu.edu
- Warehouse Supervisor Career and Professional Development ¦ cpd.cau.edu
- Managing the Critical Role of the Warehouse Supervisor - A gbr.pepperdine.edu
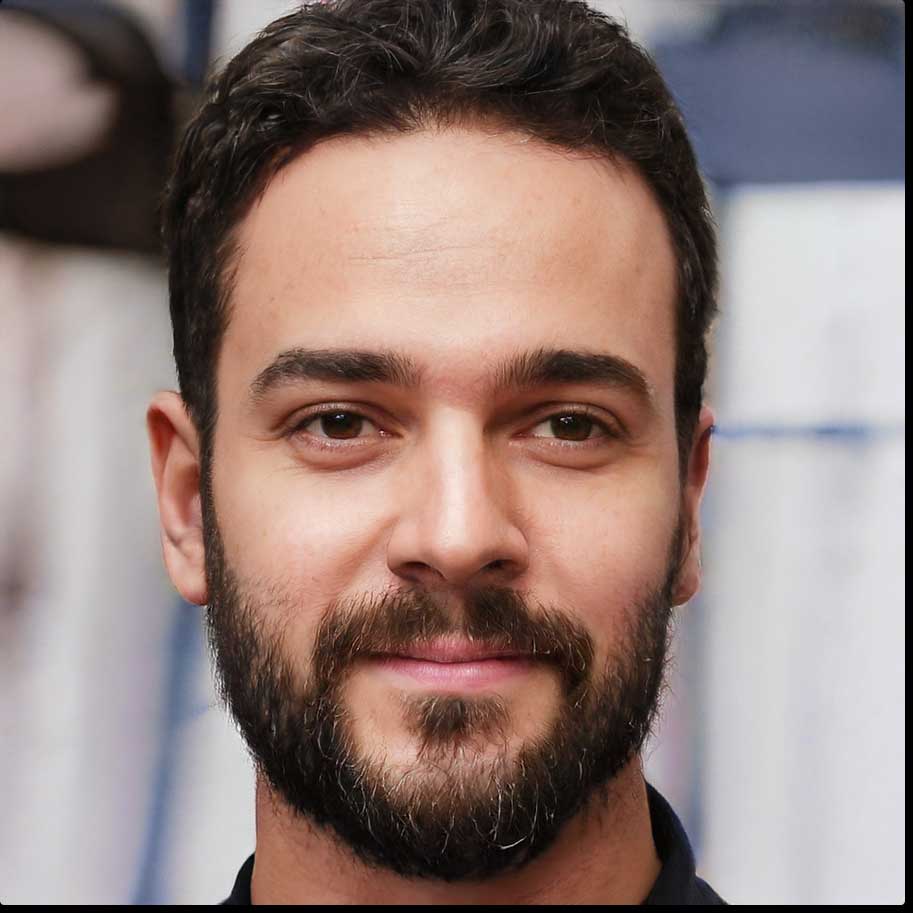