How to Be Store Logistics Manager - Job Description, Skills, and Interview Questions
The Logistics Manager of a store plays a crucial role in ensuring efficient and effective operations. Proper management of the store's inventory, supplies, and transportation of goods, as well as timely customer service are all essential aspects of their job. By properly managing the logistics, the manager can ensure that goods arrive to the store on time, that customer orders are fulfilled with accuracy, and that the store is stocked with necessary inventory.
This, in turn, helps to increase customer satisfaction, improve sales performance, reduce costs, and maximize the store's profit margin. Furthermore, the Logistics Manager must also ensure adherence to legal regulations and compliance requirements, as well as maintain good relationships with suppliers and vendors.
Steps How to Become
- Earn a Bachelor's Degree. To become a store logistics manager, it is important to start by earning a bachelor's degree in a relevant field such as business administration, logistics, supply chain management, or a related area. Coursework should include classes in transportation, inventory control, warehousing, and supply chain management.
- Gain Work Experience. Store logistics managers often need to have at least several years of experience in the retail industry, preferably in store operations or supply chain management. Work experience can be gained through internships or through positions in the retail industry such as inventory control analyst or warehouse supervisor.
- Obtain Certifications. Although it is not required, obtaining additional certifications can help to demonstrate knowledge and proficiency in the field of store logistics management. Certifications such as Certified Logistics Professional (CLP), Certified Supply Chain Professional (CSCP), and Certified Global Logistics Professional (CGLP) can be helpful for those looking to advance their careers.
- Obtain Management Training. Most retail stores offer management training programs for store logistics managers. These programs can help prepare store logistics managers for their roles by teaching them about industry best practices, customer service, and problem solving.
- Pursue Advanced Education. Pursuing advanced education in the field can help store logistics managers stay up to date on industry trends and gain a better understanding of the logistics process. Graduate degree programs in supply chain management or logistics can be beneficial for those looking to advance their careers.
The role of a Logistics Manager is to ensure the safe and efficient movement of goods from point A to point B. To be successful in this role, the Logistics Manager must possess a wide range of skills, including analytical ability, problem solving, organization, communication, and computer proficiency. In addition, they must have an understanding of the latest logistics technology and techniques. By being skilled and capable in these areas, Logistics Managers can create efficient supply chains and reduce costs for their organization.
This helps to create a competitive advantage for the company and boosts its overall profitability. Furthermore, an effective Logistics Manager is able to ensure that goods are delivered on time and in good condition, avoiding costly delays and disruptions.
You may want to check Store Maintenance Technician, Store Controller, and Store Buyer for alternative.
Job Description
- Manage and coordinate daily logistics operations, including warehousing and transportation.
- Develop, implement, and manage all store logistics processes.
- Create and maintain standards of operational excellence in logistics, including inventory management, order fulfillment, and customer service.
- Oversee the accuracy of inventory levels and ensure timely delivery of all store orders.
- Monitor and analyze performance of logistics operations, identify areas for improvement and develop strategies to optimize efficiency.
- Develop, monitor, and manage logistics budget and ensure cost effectiveness.
- Negotiate contracts with vendors and suppliers for cost savings.
- Act as a liaison between store personnel and logistics providers.
- Ensure compliance with applicable health and safety regulations.
- Analyze data to identify inefficiencies, devise solutions, and enhance performance.
- Train and coach store personnel on best practices for logistics operations.
- Establish relationships with store personnel to maintain effective communication and ensure customer satisfaction.
Skills and Competencies to Have
- Leadership and Management Skills
- Strategic Planning
- Organizational and Time Management
- Communication and Interpersonal Skills
- Problem-Solving and Decision-Making Skills
- Budgeting and Financial Management
- Inventory Management
- Warehouse Operations and Logistics
- Supply Chain and Distribution
- Quality Assurance
- Customer Service
- Project Management
- Technology and Software Proficiency
- Safety and Compliance
- Data Analysis and Reporting
Being a Logistics Manager requires a wide range of skills and abilities to ensure the successful operation of a store. A strong understanding of customer service, inventory management, and communication are essential for a Logistics Manager to be successful. Proper customer service is necessary to ensure customer satisfaction, while inventory management involves tracking stock levels and ordering new merchandise to meet customer demands.
Communication is also essential for successful operations as it ensures that all staff members are on the same page when it comes to store processes and procedures. Furthermore, good problem-solving skills are needed for a Logistics Manager to resolve customer issues and supply chain challenges. Finally, strong organizational abilities are necessary for a Logistics Manager to effectively manage both personnel and operational tasks.
Store Leader, Store System Analyst, and Store Security Officer are related jobs you may like.
Frequent Interview Questions
- How would you organize and manage a team of store logistics personnel?
- What experience do you have with inventory control and order management systems?
- What strategies do you use to ensure accurate and timely delivery of goods?
- How do you handle customer service issues related to store logistics?
- What is your experience with managing budgets related to store logistics?
- What challenges have you faced in store logistics and how did you address them?
- How do you ensure compliance with regulations related to store logistics?
- How do you stay up-to-date on new technologies and trends related to store logistics?
- How do you manage relationships with vendors and suppliers related to store logistics?
- How do you measure the success of store logistics operations?
Common Tools in Industry
- Inventory Management Software. A software program used to manage stock levels, orders, sales and deliveries. (Eg: Fishbowl Inventory)
- Warehouse Management System (WMS). A software program used to oversee and coordinate the daily operations of a warehouse. (Eg: HighJump WMS)
- Order Fulfillment Software. A software program used to automate and streamline order fulfillment processes. (Eg: ShipStation)
- Transportation Management System (TMS). A software program used to plan, execute and optimize transportation logistics. (Eg: MercuryGate TMS)
- Warehouse Control System (WCS). A software program used to control and manage warehouse processes and equipment. (Eg: Wynright WES)
- Logistics Optimization Software. A software program used to optimize logistics operations by analyzing data and generating solutions. (Eg: LLamasoft Supply Chain Guru)
- Asset Tracking Software. A software program used to track and manage assets in a warehouse or other facility. (Eg: CribMaster Asset Tracking)
- Labor Management System (LMS). A software program used to track and manage labor costs, productivity and efficiency in a warehouse. (Eg: RedPrairie LMS)
Professional Organizations to Know
- Council of Supply Chain Management Professionals (CSCMP)
- Warehousing Education and Research Council (WERC)
- International Warehouse Logistics Association (IWLA)
- American Logistics Association (ALA)
- Material Handling Industry of America (MHIA)
- International Association of Refrigerated Warehouses (IARW)
- National Retail Federation (NRF)
- National Association of Fleet Administrators (NAFA)
- International Foodservice Distributors Association (IFDA)
- National Private Truck Council (NPTC)
We also have Store Party Planner, Store Advertising Specialist, and Store Business Analyst jobs reports.
Common Important Terms
- Inventory Management. The process of tracking, organizing, and managing the stock of goods in a store.
- Warehouse Management. The process of managing the storage and movement of goods in a warehouse.
- Supply Chain Management. The coordination of all activities related to the flow of materials from suppliers to customers.
- Logistics. The management of the flow of resources between the point of origin and the point of consumption.
- Distribution Management. The management of the movement of products from the point of production to the point of sale.
- Shipping and Receiving. The process of receiving products from suppliers and sending them to customers.
- Purchase Order Management. The process of managing orders from suppliers and customers.
- Sales Forecasting. The process of predicting future sales based on past sales data.
- Demand Planning. The process of predicting customer demand for products and services.
- Stock Control. The process of monitoring and managing the level of stock in a store or warehouse.
Frequently Asked Questions
Q1: What is the role of a Store Logistics Manager? A1: A Store Logistics Manager is responsible for the efficient transportation, receiving, and distribution of goods within a retail store. They ensure the timely and accurate delivery of products, oversee inventory control systems, and coordinate with suppliers to maintain sufficient stock levels. Q2: What qualifications are required to become a Store Logistics Manager? A2: Store Logistics Managers typically need a minimum of a high school diploma or equivalent. Additionally, several years of experience in a related field, such as warehouse operations or supply chain management, is preferred. Q3: What are the primary responsibilities of a Store Logistics Manager? A3: The primary responsibilities of a Store Logistics Manager include coordinating the delivery of goods to the store, managing inventory control systems, overseeing staff members responsible for receiving and stocking goods, and ensuring compliance with safety regulations. Q4: What tools do Store Logistics Managers use to manage inventory? A4: Store Logistics Managers use a variety of tools to manage inventory, such as barcode scanners, computerized inventory management systems, and automated inventory tracking software. Q5: What metrics are used to measure the performance of a Store Logistics Manager? A5: Common metrics used to measure the performance of a Store Logistics Manager include on-time delivery rates, accuracy of inventory records, cost savings from efficient operations, and customer satisfaction with product availability.What are jobs related with Store Logistics Manager?
- Store Manager Trainee
- Store Salesperson
- Store Cleaner
- Store Trainer
- Store Department Head
- Store Maintenance Worker
- Store Administrative Assistant
- Store Associate
- Store Coordinator
- Store Keeper
Web Resources
- What Is a Logistics Manager? | GCU Blog - gcu.edu www.gcu.edu
- What Is a Logistics Manager and How to Become One www.wgu.edu
- What is a Logistics Manager? The Supply Chain Specialists www.rasmussen.edu
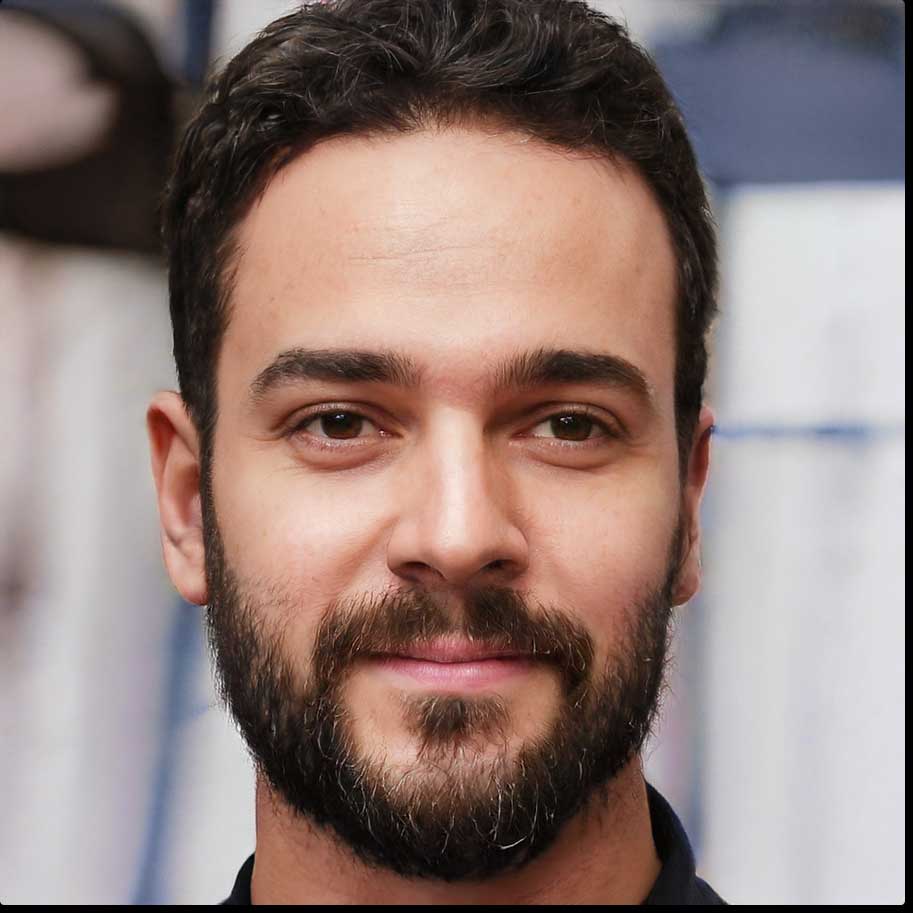