How to Be Precision Machinist - Job Description, Skills, and Interview Questions
Precision machinists are highly specialized engineers who use sophisticated machinery and tools to create parts that are exact replicas of a given design. As a result, these professionals are in high demand in a variety of industries, from automotive and aerospace to medical device manufacturing and electronics. Precision machinists play an integral role in the production process, as they use their expertise to generate components with extremely tight tolerances.
This attention to detail helps ensure that the end product meets the highest standards of quality and safety, while also meeting any customer specifications. Furthermore, precision machinists are able to work with a wide range of materials, such as metals, plastics, and ceramics, allowing them to fabricate components for a variety of applications. Therefore, precision machinists are essential to the production of complex parts that require high levels of accuracy.
Steps How to Become
- Earn a high school diploma or GED. To become a Precision Machinist, individuals must have a high school diploma or GED equivalent.
- Consider earning a post-secondary certificate. Although not required, many employers prefer to hire individuals who have a post-secondary certificate in machining or a related field.
- Obtain on-the-job training. Once hired, most employers provide their employees with on-the-job training to teach them the specific skills needed to become a precision machinist.
- Get certified. Although not always required, voluntary certification may help individuals stand out from the competition when applying for jobs.
- Join a professional organization. Joining a professional organization can help individuals stay up-to-date on industry trends and network with other precision machinists.
As the use of technology in machining continues to advance, it is important for precision machinists to stay up-to-date and capable of working with the latest technological advancements. This requires a dedication to learning and staying informed on industry trends, as well as an understanding of the various tools and techniques that are available. Developing a strong skill set and understanding of the latest technology can also help machinists remain competitive in the job market.
staying abreast of industry changes and trends can help machinists anticipate potential problems and develop solutions before they become a costly issue. By keeping their knowledge up-to-date, precision machinists can ensure they are equipped to handle any machining challenge that comes their way.
You may want to check Sheet Metal Worker Mechanic, Elevator/Escalator Technician, and Industrial Mechanic for alternative.
Job Description
- Set up and operate conventional, manual, and/or CNC machine tools to produce precision parts and instruments.
- Interpret engineering drawings and specifications to determine product dimensions and tolerances.
- Select proper cutting tools, materials, and machine speeds and feeds for each operation.
- Monitor machining operations to ensure quality standards are met.
- Perform preventative maintenance on machines and equipment.
- Troubleshoot machining problems and make necessary adjustments.
- Measure, examine, and test completed units to detect defects and ensure conformance to specifications.
- Record production data such as parts produced, scrap, and time required for each operation.
- Maintain detailed records of all work performed.
- Follow all safety guidelines and procedures.
Skills and Competencies to Have
- Knowledge of machining operations and processes
- Ability to read blueprints, technical drawings, and schematics
- Knowledge of mathematics, including trigonometry and geometry
- Ability to use precision measuring tools such as calipers and micrometers
- Ability to operate manual, CNC, and computer-controlled machines
- Ability to troubleshoot mechanical problems and make necessary repairs
- Ability to set up and operate various types of production machinery
- Demonstrated ability to work with close tolerances
- Knowledge of proper safety protocols in a machining environment
- Ability to work independently with minimal supervision
Being a precision machinist requires a keen eye for detail and an impeccable understanding of machining processes. The most important skill to have is the ability to accurately measure and program parts to a high level of precision. This requires having a thorough knowledge of tolerances, geometric dimensioning and tolerancing (GD&T) and the ability to use advanced measuring technology such as coordinate measuring machines (CMMs).
To ensure accuracy, the machinist must be able to read blueprints and other engineering drawings, understand complex mathematics, and be familiar with the different types of metals and alloys used to create parts. Furthermore, it is essential for the machinist to have a good working knowledge of computer-aided design (CAD) and computer-aided manufacturing (CAM) software that is used to create parts. With these skills, the machinist can create components with accuracy, which helps maintain quality control and improves the efficiency of production.
Robotics Technician, Small Engine Mechanic, and Aircraft Maintenance Technician are related jobs you may like.
Frequent Interview Questions
- What experience do you have with precision machining?
- How do you troubleshoot a machining problem?
- Describe a particularly challenging machining project you have completed.
- What safety protocols do you follow when operating a precision machining machine?
- What sets your precision machining skills apart from other machinists?
- What tools and techniques do you use while machining?
- How do you ensure accuracy and precision when machining?
- How do you use mathematics when machining parts?
- What steps do you take to ensure a smooth production process?
- How quickly can you set up a machine for a new machining project?
Common Tools in Industry
- Lathe. A machine used to shape metal or wood by turning the material against a stationary cutting tool. (eg: A lathe is used to produce intricate parts for vehicles. )
- Milling Machine. A machine used for the shaping of metal and other solid materials through the use of a rotating cutter. (eg: A milling machine is used to create complex shapes and patterns in metal. )
- Drill Press. A machine designed to drill holes into materials with a rotating drill bit. (eg: A drill press is used to create holes in metal for bolts and screws. )
- Grinder. A machine used to grind material down to its desired shape or size. (eg: A grinder is used to sharpen tools and grind away excess material. )
- CNC Machine. A computer-controlled machine used to create intricate shapes and parts with great precision. (eg: A CNC machine is used to create parts for airplanes and spacecraft with extreme accuracy. )
Professional Organizations to Know
- American Machine Tool Distributors Association (AMTDA)
- Association for Manufacturing Technology (AMT)
- National Institute for Metalworking Skills (NIMS)
- Society of Manufacturing Engineers (SME)
- Association for Manufacturing Excellence (AME)
- International Association of Machinists and Aerospace Workers (IAMAW)
- National Tooling and Machining Association (NTMA)
- Precision Machined Products Association (PMPA)
- CNC Programming & Technology Association (CPTA)
- National Center for Metalworking Skills (NCMS)
We also have Welding Technician, Fire Protection Technician, and Appliance Mechanic jobs reports.
Common Important Terms
- CNC (Computer Numerical Control) Machining. The process of cutting, milling, shaping, and drilling materials using a computer-controlled machine.
- CAD (Computer-Aided Design). A computer program used for 3D modeling and creating technical drawings.
- Jigs and Fixtures. Devices used to securely hold a workpiece in place during machining operations.
- Tooling. Specialized tools used in machining operations, such as cutting tools, drill bits, taps, reamers, and milling cutters.
- Tolerances. The allowable variations in dimensions in a machined part.
- Gearing. The combination of two or more gears that transmits motion from one shaft to another.
- Heat Treating. The process of heating and cooling metals to alter their physical properties.
- Die Casting. A manufacturing process in which molten metal is injected into a mold cavity to form a desired shape.
- EDM (Electrical Discharge Machining). A process that uses high-powered electrical currents to erode metal and other materials.
- Quality Control. Procedures and processes used to ensure that products are being made according to specifications.
Frequently Asked Questions
What is a Precision Machinist?
A Precision Machinist is a skilled craftsperson who operates machine tools such as lathes, mills, grinders, and other specialized equipment to produce precision parts and components.
What qualifications are necessary to become a Precision Machinist?
To become a Precision Machinist, one must have a high school diploma or equivalent and complete a machinist apprenticeship program. Additionally, some employers may require a post-secondary education in machining or related fields.
What are some of the duties of a Precision Machinist?
The duties of a Precision Machinist include reading blueprints and engineering drawings, measuring and inspecting parts for accuracy, operating various machinery and tools to create parts and components, and performing maintenance on machinery and tools.
What is the average salary of a Precision Machinist?
The average salary of a Precision Machinist is approximately $48,000 per year.
What type of environment does a Precision Machinist typically work in?
A Precision Machinist typically works in a manufacturing or production environment such as a factory or machine shop.
What are jobs related with Precision Machinist?
- Automotive Technician
- Tire Technician
- Diesel Mechanic
- Industrial Maintenance Technician
- Tool and Die Maker
- Plant Maintenance Mechanic
- HVAC Technician
- Marine Mechanic
- Heavy Duty Mechanic
- HVAC Mechanic
Web Resources
- Precision Machining | Everett Community College www.everettcc.edu
- What is Precision Machining? | Goodwin College www.goodwin.edu
- Precision Machining - Delgado Community College www.dcc.edu
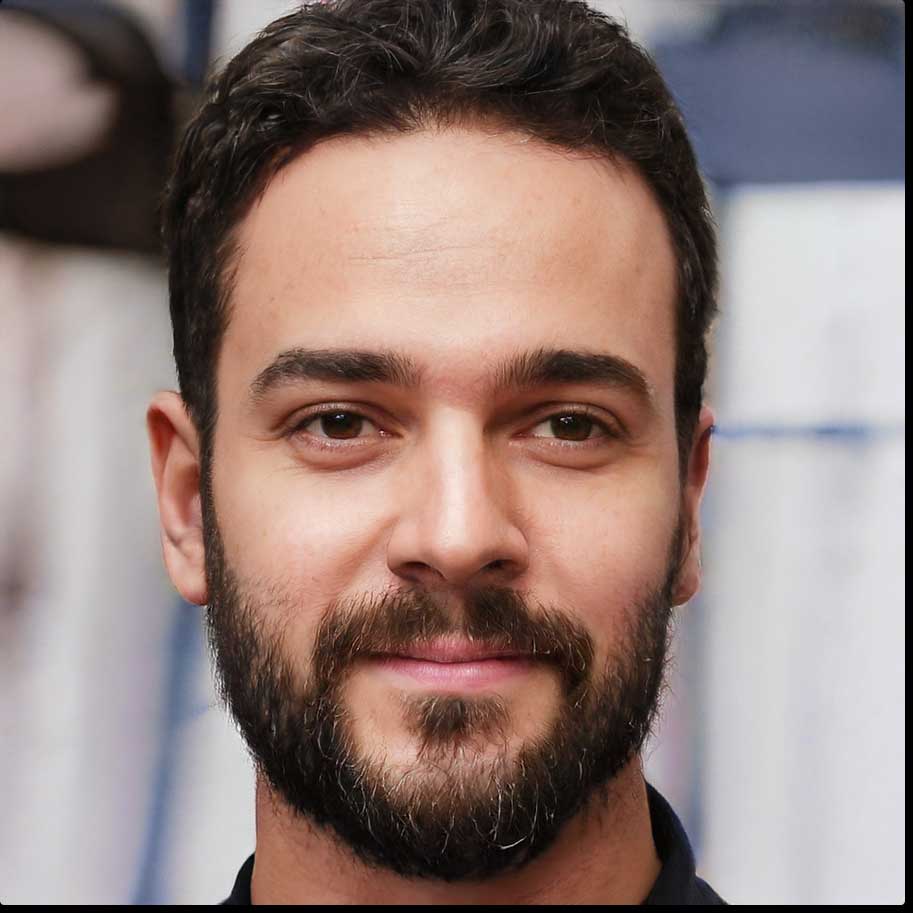