How to Be Welding Technician - Job Description, Skills, and Interview Questions
Welding is an essential part of many industrial processes, and as demand for skilled welders increases, the need for welding technicians also increases. Welding technicians are responsible for operating welding equipment, ensuring that the welds are performed correctly, and troubleshooting any problems that may arise. As a result, Welding Technician training has become increasingly important.
Welding Technician training covers a wide range of topics including safety procedures, metal fabrication techniques, welding technology, welding codes and standards, inspection techniques, and welding theory. Adequate Welding Technician training is essential to ensure that welders are properly qualified and able to perform quality work, while also protecting the welders from potential hazards. proper Welding Technician training can help to reduce the risk of accidents, increase productivity, and ensure the highest quality welds are produced.
Steps How to Become
- Obtain a High School Diploma or Equivalent. Before getting started on the path to becoming a welding technician, you will need to obtain a high school diploma or equivalent.
- Enroll in a Welding Program. The next step is to enroll in a welding program at a trade school or community college. This program should cover topics like welding techniques, metal fabrication, blueprint reading, and safety standards.
- Get Certified. After completing the welding program, you will need to get certified. There are several certifications available depending on the type of welding you wish to specialize in.
- Gain Work Experience. Before you can move into a more advanced position as a welding technician, you will need to gain some work experience. This can be done through an apprenticeship program or on-the-job training.
- Advance Your Career. Once you have gained enough experience, you can advance your career by taking additional courses and certifications. This will help you stay up-to-date on the latest welding techniques and technologies.
To stay ahead and capable as a Welding Technician, there are several steps to take. First, it is important to stay up-to-date on the latest welding techniques, by attending welding seminars or reading welding industry publications. Second, it is important to have the right tools and equipment for the job.
Having a complete set of welding tools and supplies will enable you to complete jobs quicker, as well as provide a higher quality of work. Third, having the right safety equipment, such as respirators and safety glasses, is essential for safety and protection. Fourth, it is important to practice regularly and keep up with industry standards.
Regular practice will help the technician stay ahead of the competition and help them deliver the best possible results. Finally, networking with peers in the welding industry can help to share ideas and keep up with the latest trends in welding technology. By taking these steps, Welding Technicians can stay ahead of the competition, while delivering the highest quality work.
You may want to check Avionics Technician, Generator Mechanic, and Plumbing Technician for alternative.
Job Description
- Operate welding equipment in order to join, fabricate, and repair metal parts.
- Inspect and test welds to ensure welds meet specified standards.
- Read and interpret blueprints and drawings to determine the specific welding requirements.
- Set up and adjust welding equipment, such as voltage, current, angle, speed, and amperage.
- Cut or trim metal pieces using hand tools, such as welders, saws, or torches.
- Repair worn or damaged parts by welding on extra layers of metal.
- Select appropriate filler rods and fluxes according to material being welded.
- Monitor the welds to avoid overheating of parts or warping, shrinking, distortion, or expansion of material.
- Maintain and repair welding equipment and accessories as needed.
- Follow safety protocols when operating welding equipment and handling hazardous materials.
Skills and Competencies to Have
- Knowledge of welding safety protocols and procedures
- Proficiency in working with a variety of welding equipment and materials
- Ability to read and interpret welding blueprints
- Understanding of welding processes such as MIG, TIG, arc and oxy-acetylene welding
- Ability to troubleshoot and resolve welding issues
- Knowledge of welding codes and standards
- Strong problem-solving skills
- Excellent attention to detail
- Ability to work independently and in a team setting
- Good communication and interpersonal skills
Welding technicians are essential members of any fabrication team. Their knowledge and experience in operating welding equipment and using welding techniques to join, cut, shape and fabricate metal components is critical for the success of any welding project. The most important skill a welding technician needs to have is the ability to understand and interpret blueprints, schematics and diagrams.
Good blueprints provide the necessary information for a technician to accurately complete the job. welding technicians must be knowledgeable in selecting appropriate welding techniques and equipment for different types of projects. They must also be aware of safety risks associated with welding and the proper usage of safety gear.
Finally, a welding technician must have a good understanding of metallurgy and the processes involved in welding different metals. These skills enable them to complete jobs effectively, efficiently and safely.
Heavy Duty Mechanic, Tire Technician, and HVAC Technician are related jobs you may like.
Frequent Interview Questions
- What experience do you have in welding?
- How familiar are you with the different types of welding processes (MIG, TIG, Arc, etc. )?
- Have you ever worked with automated welding systems?
- Describe a project or job youve completed that involved welding.
- How do you ensure that your welds meet quality standards?
- Are you comfortable working with hazardous materials?
- Are you familiar with any welding certifications such as AWS or ASME?
- How capable are you at reading and interpreting blueprints?
- What safety measures do you take when welding?
- How do you stay up to date on the latest advances in welding technology?
Common Tools in Industry
- Welding Torch. Used to heat and join metals together (e. g. stainless steel welding).
- MIG Welder. An electric welding machine that uses an electrode wire to create an arc and join two pieces of metal together (e. g. aluminum MIG welding).
- TIG Welder. An electric welding machine that uses a tungsten electrode to create an arc and join two pieces of metal together (e. g. aluminum TIG welding).
- Spot Welder. A welding machine that creates a spot weld by pressing two pieces of metal together with pressure and electricity (e. g. steel spot welding).
- Plasma Cutter. A tool used to cut metal with a high-temperature stream of plasma (e. g. stainless steel plasma cutting).
- Grinder. A tool used to shape and finish metals by grinding them (e. g. aluminum grinding).
- Sander. A tool used to smooth surfaces by sanding them (e. g. wood sanding).
- Drill. A tool used to create holes in materials (e. g. concrete drilling).
- Soldering Iron. A tool used to make electrical connections by melting a metal alloy (e. g. copper soldering).
- Safety Gear. Protective gear used to protect welders from harm (e. g. welding helmet).
Professional Organizations to Know
- American Welding Society (AWS)
- National Association of Professional Welders (NAPW)
- International Institute of Welding (IIW)
- American Society of Mechanical Engineers (ASME)
- American Metal Fabricators Association (AMFA)
- American Society of Metals (ASM)
- American Society for Metals International (ASMI)
- International Institute of Welding Inspectors (IIWI)
- The American Institute for Welding Inspection and Certification (AIWIC)
- Canadian Welding Bureau (CWB)
We also have Refrigeration Mechanic, Robotics Technician, and Precision Machinist jobs reports.
Common Important Terms
- Arc Welding. A type of welding that uses an electric current to form an arc between an electrode and the material being welded, creating intense heat that melts the metal and allows it to be joined.
- MIG Welding. A type of welding that uses an electric arc to create extremely high temperatures for welding. It is commonly used for thin-gauge materials, and is often used in automotive and industrial applications.
- TIG Welding. A type of welding that uses a non-consumable tungsten electrode to form the arc and create intense heat for welding. It is used for a variety of metals, including aluminum, stainless steel and copper alloys.
- Gas Metal Arc Welding (GMAW). A type of welding that uses a consumable wire electrode to create an arc and form the weld. It is often used in automotive manufacturing and construction.
- Flux-Cored Arc Welding (FCAW). A type of welding that uses a consumable flux-cored electrode to form the arc and create intense heat for welding. It is often used on thicker materials, as it produces fewer fumes than MIG welding.
- Shielded Metal Arc Welding (SMAW). A type of welding that uses a non-consumable electrode to form the arc and create intense heat for welding. It is often used on thicker materials, as it produces fewer fumes than other methods.
- Submerged Arc Welding (SAW). A type of welding that uses a consumable electrode to form the arc and create intense heat for welding. It is often used on thicker materials, as it produces fewer fumes than other methods.
- Oxyfuel Welding (OFW). A type of welding that uses a flame produced by burning a fuel gas such as Acetylene or Propylene, to form the arc and create intense heat for welding. It is often used on thicker materials, as it produces fewer fumes than other methods.
Frequently Asked Questions
What is a Welding Technician?
A Welding Technician is a skilled tradesperson who specializes in welding, cutting, and joining metals and other materials. They use a variety of tools and techniques to create and repair structures, equipment, and machinery.
What qualifications are needed to become a Welding Technician?
To become a Welding Technician, one must typically have a high school diploma or equivalent and complete a welding program or apprenticeship. Some may also need to obtain welding certifications.
What types of welding techniques are used by Welding Technicians?
Welding Technicians may use a variety of techniques such as Shielded Metal Arc Welding (SMAW), Gas Metal Arc Welding (GMAW), Flux-Cored Arc Welding (FCAW), and Gas Tungsten Arc Welding (GTAW).
What safety measures do Welding Technicians use?
Welding Technicians use safety measures such as wearing protective gear including helmets, gloves, and protective clothing, as well as proper ventilation systems to reduce exposure to fumes.
What is the average pay for a Welding Technician?
The average annual salary for a Welding Technician is approximately $45,000. Salaries may vary based on experience, location, and type of welding technique used.
What are jobs related with Welding Technician?
- HVAC Mechanic
- Structural Fabricator
- Automation Mechanic
- Automotive Mechanic
- Construction Equipment Mechanic
- Building Maintenance Technician
- Small Engine Mechanic
- Plant Maintenance Mechanic
- Wind Turbine Technician
- Carpet Installer
Web Resources
- Welding Technician - Institute of Technology (IOT) www.iot.edu
- Welding Technician | Waukesha County Technical College www.wctc.edu
- What are the roles and responsibilities of a welding technician ptt.edu
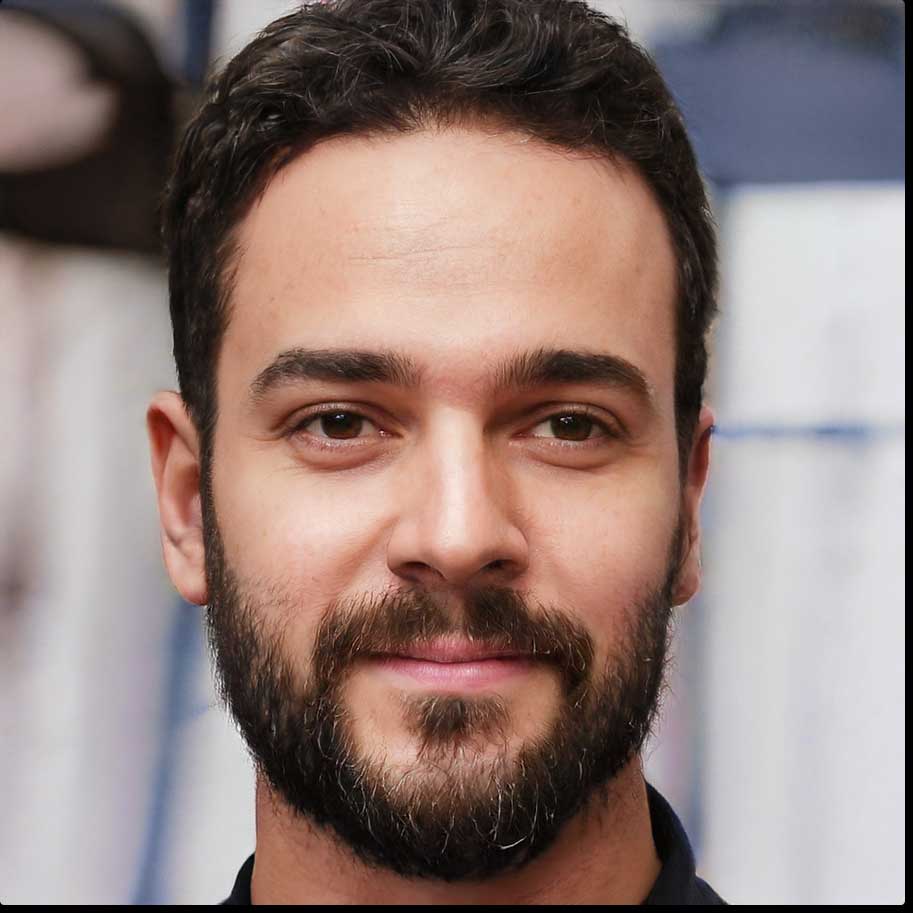