How to Be Industrial Mechanic - Job Description, Skills, and Interview Questions
Industrial mechanics play a critical role in keeping the industrial sector running smoothly. As the demand for new products and services increases, they must ensure that all machines and equipment are properly maintained, repaired and replaced when needed. This cause and effect chain ensures that production remains efficient, and prevents costly breakdowns or accidents from occurring.
Without industrial mechanics, machinery and equipment would suffer from breakages and malfunction, leading to a decrease in production output, quality and efficiency. Industrial mechanics are also responsible for maintaining safety standards in the workplace, reducing the risk of injury and death for both employees and customers. The importance of industrial mechanics is further emphasized by the need for them to be knowledgeable about a wide range of mechanical systems and components, often including both electrical and hydraulic systems.
Steps How to Become
- Obtain a high school diploma or equivalent. Industrial mechanics typically require a high school diploma or equivalent to be considered for employment.
- Pursue a postsecondary program. Pursuing a postsecondary program in industrial mechanics or industrial technology can help a person gain the necessary skills and credentials needed to become an industrial mechanic. Programs can cover topics such as machine repair, welding, and hydraulics.
- Gain experience. Industrial mechanics typically require experience to be considered for employment. Obtaining an internship or apprenticeship with a company can give an aspiring industrial mechanic the necessary experience.
- Earn professional certification. Professional certification is not required but can help an industrial mechanic stand out from other applicants. The National Institute for Metalworking Skills offers several certifications for industrial mechanics.
- Seek employment. Industrial mechanics can seek employment with companies that manufacture products or repair machinery and equipment. They may also find employment with government agencies and other organizations that require maintenance and repair services.
In order to stay ahead and qualified as an Industrial Mechanic, one must stay up to date on the latest industry standards, technologies, and best practices. Regularly attending workshops, seminars and continuing education courses can help ensure that a Mechanic is equipped with the knowledge and skills needed to identify and address potential problems quickly and effectively. staying informed of the latest industry developments, such as new legislation or regulations, can help prevent potential costly mistakes.
Finally, keeping a network of professional contacts and mentors can provide invaluable support in times of need, as well as valuable information that can be used to make informed decisions. With the combination of these key steps, an Industrial Mechanic can remain up to date and qualified in their field.
You may want to check Heavy Duty Mechanic, Refrigeration Mechanic, and Structural Fabricator for alternative.
Job Description
- Inspect and test machinery and equipment in accordance with established maintenance schedules to ensure that machines are in proper working order.
- Read and interpret blueprints, diagrams, and schematics to determine the best method of repair.
- Dismantle, adjust, repair, and reassemble machinery, such as motors, pumps, and gearboxes.
- Fabricate and repair parts using machine tools such as lathes and milling machines.
- Assemble and install new machinery and equipment according to specifications.
- Test repaired machinery and equipment to verify proper functioning.
- Perform preventive maintenance on machinery and equipment to minimize downtime.
- Troubleshoot electrical and mechanical problems with machinery and equipment.
- Use hand tools, power tools, and measuring instruments to complete assignments.
- Monitor the performance of machinery and equipment, and make adjustments as needed.
Skills and Competencies to Have
- Knowledge of industrial machinery and equipment.
- Knowledge of safety protocols and procedures.
- Ability to troubleshoot and diagnose mechanical problems.
- Ability to read and interpret blueprints, diagrams, and schematics.
- Ability to fabricate, weld, and repair parts.
- Knowledge of hydraulic and pneumatic systems.
- Knowledge of electronic and electrical systems.
- Ability to use hand tools, power tools, and precision measuring instruments.
- Ability to work in confined spaces and at heights.
- Ability to lift heavy objects safely.
- Ability to work independently and as part of a team.
- Excellent communication and interpersonal skills.
- Attention to detail and ability to follow instructions precisely.
Industrial mechanics require a variety of technical and problem-solving skills in order to perform their job functions effectively. The most important skill for an industrial mechanic is the ability to troubleshoot equipment and machinery. This means being able to identify an issue with a piece of equipment, diagnose the problem, and then fix it.
Troubleshooting requires an understanding of the principles of physics, mechanics, and electricity. Industrial mechanics must also have an in-depth knowledge of various types of materials, tools, and techniques used in industrial maintenance and repair. they must be able to read and interpret blueprints, diagrams, and technical manuals.
Good communication skills are also essential for a successful industrial mechanic, as they need to be able to clearly explain problems and solutions to customers, supervisors, and colleagues.
Automotive Technician, Automation Mechanic, and Automotive Mechanic are related jobs you may like.
Frequent Interview Questions
- What experience do you have working with large industrial machinery?
- What safety training have you completed?
- What equipment have you worked on in the past?
- Describe a project in which you had to troubleshoot and repair a machine.
- How do you stay up to date with the latest industrial mechanic technology?
- What do you consider your biggest challenge when maintaining industrial machinery?
- How do you prioritize tasks when multiple machines need repairs?
- How do you handle high-pressure situations when repairing complicated machinery?
- What strategies do you use to remain organized while servicing different machines?
- How do you approach diagnosing and troubleshooting mechanical issues?
Common Tools in Industry
- Ratchet Wrench. Used for tightening and loosening nuts and bolts. (eg: tightening a nut on a machine)
- Allen Wrench. Used to drive bolts and screws with hexagonal sockets. (eg: tightening a screw on a machine)
- Socket Wrench. Used to drive nuts and bolts with various sizes of sockets. (eg: removing a bolt from a machine)
- Crescent Wrench. Used to adjust the tension on nuts and bolts. (eg: adjusting the tension on a belt)
- Hammer. Used to drive nails, remove nails, or break apart objects. (eg: removing a rusty nail)
- Pliers. Used to grip, twist and turn objects. (eg: gripping a bolt to loosen it)
- Screwdriver. Used to drive screws into or out of materials. (eg: removing a screw from a machine)
- Impact Driver. Used to drive screws and bolts quickly and with more force than a screwdriver. (eg: driving screws into wood)
- Power Drill. Used to drill holes into materials. (eg: drilling a hole in a metal plate)
- Soldering Iron. Used to join two pieces of metal together with solder. (eg: rewiring an electrical connection)
Professional Organizations to Know
- Association of Machinery and Equipment Appraisers
- Automotive Service Association
- American Society of Mechanical Engineers
- National Institute for Metalworking Skills
- National Fluid Power Association
- Industrial Maintenance Mechanics Association
- Society of Maintenance and Reliability Professionals
- International Association of Machinists and Aerospace Workers
- National Tooling and Machining Association
- International Union of Operating Engineers
We also have Auto Body Technician, Welding Technician, and Tire Technician jobs reports.
Common Important Terms
- Lubrication. The process of applying lubricant to a moving machine part in order to reduce friction, wear and heat.
- Bearing. A device used to support and guide rotary or linear motion.
- Torque. A force that causes an object to rotate or turn around an axis.
- Fasteners. Nuts, bolts, screws, rivets, and other mechanical pieces used to fasten parts together.
- Gears. A rotating machine part that is used to transfer motion or power between two other moving parts.
- Pneumatics. The use of compressed air or gas to create mechanical motion.
- Hydraulics. The use of liquid pressure to create mechanical motion.
- Welding. A process of joining two or more pieces of metal by applying heat and pressure.
- Pumps. Devices used to move liquids or gases from one location to another.
- Motors. Devices used to convert electrical energy into mechanical energy.
Frequently Asked Questions
What is an Industrial Mechanic?
An Industrial Mechanic is a skilled tradesperson that is responsible for the installation, repair, and maintenance of industrial machinery and equipment.
What type of tools do Industrial Mechanics use?
Industrial Mechanics use a wide range of tools including hand tools, power tools, welding and cutting equipment, precision measuring instruments, and specialized machinery.
What skills are required to be an Industrial Mechanic?
Industrial Mechanics need to possess a range of skills including mechanical aptitude, problem-solving, manual dexterity, and the ability to read blueprints.
What kind of job growth is expected for Industrial Mechanics?
According to the Bureau of Labor Statistics, the job outlook for Industrial Mechanics is projected to grow by 4% through 2029.
What kind of salary can an Industrial Mechanic expect to earn?
The median salary for an Industrial Mechanic in the United States is $51,950 per year.
What are jobs related with Industrial Mechanic?
- Hydraulic Technician
- Construction Equipment Mechanic
- Wind Turbine Technician
- Farm Equipment Mechanic
- Electronics Technician
- Bicycle Mechanic
- Machine Tool Technician
- Aircraft Technician
- Telecommunications Technician
- Aircraft Mechanic
Web Resources
- Industrial Mechanics | Technical Education www.snow.edu
- Industrial Mechanic program offered at Southwest Tech www.swtc.edu
- Industrial Mechanic Degree | Industrial Mechanic Training www.nicoletcollege.edu
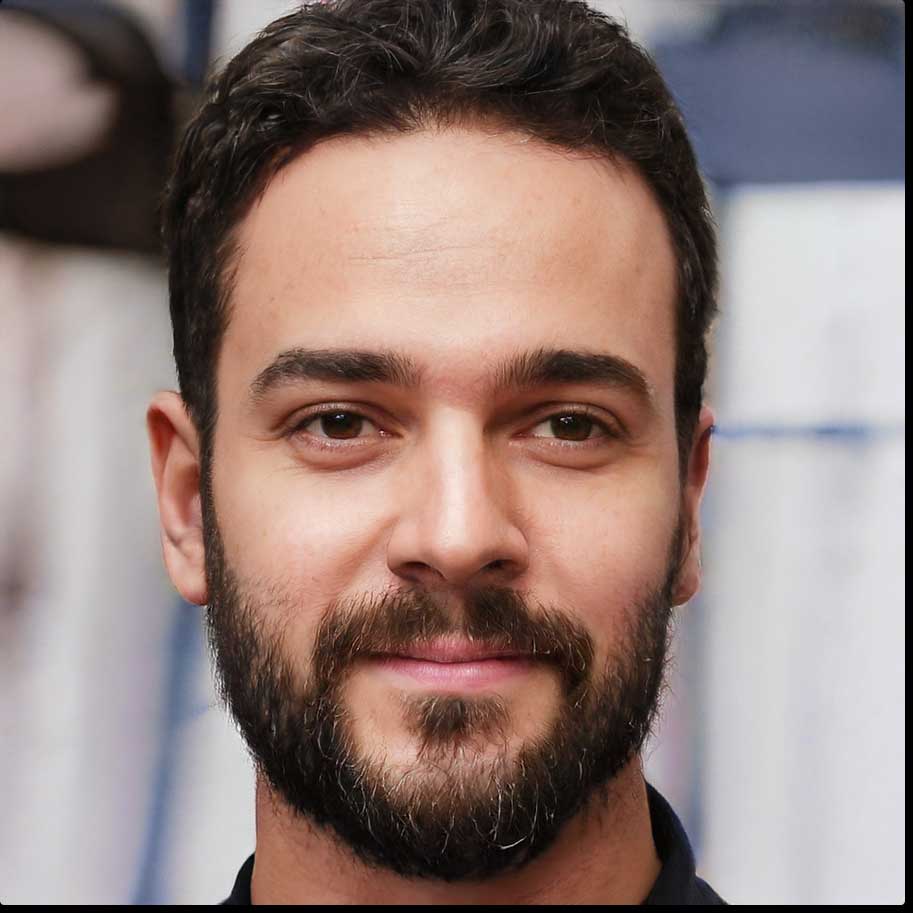