How to Be Industrial Maintenance Technician - Job Description, Skills, and Interview Questions
The role of an Industrial Maintenance Technician is essential to the successful operation of any business that relies on manufacturing and production. When machines fail or need repair, it is the Industrial Maintenance Technician who steps in to identify the cause of the problem and then take the necessary steps to fix it. This ensures that production can continue and that the business can remain competitive.
The technician's knowledge and expertise in the field of industrial maintenance can also help to prevent problems from occurring in the future, thus eliminating costly downtime. By providing timely maintenance services, the technician can help reduce the risk of equipment malfunctions and increase the overall efficiency of production processes.
Steps How to Become
- Obtain a high school diploma or equivalent, such as a GED. Most employers require that Industrial Maintenance Technicians have at least a high school diploma or equivalent.
- Acquire technical training. Industrial Maintenance Technicians need to have a strong background in electrical, mechanical and hydraulic systems. Technical training can be completed through a college or vocational school program, through on-the-job training, or through a combination of the two.
- Pursue certifications. Many employers prefer to hire Industrial Maintenance Technicians who have obtained professional certification in their desired industry. Certifications can be obtained through organizations such as the National Center for Construction Education and Research (NCCER) or the International Maintenance Institute (IMI).
- Gain experience. Employers often prefer to hire Industrial Maintenance Technicians who have prior experience in the field. Working as an apprentice or intern in an industrial maintenance environment is a great way to gain valuable experience and make connections in the industry.
- Stay up-to-date on the latest technologies and techniques. As the industrial maintenance field continues to evolve, Industrial Maintenance Technicians must stay up-to-date on the latest technologies and techniques. Taking continuing education courses, attending industry conferences and reading industry publications can help Industrial Maintenance Technicians stay ahead of the curve.
You may want to check Paint Technician, Aircraft Technician, and Diesel Mechanic for alternative.
Job Description
- Perform scheduled and unscheduled preventive and corrective maintenance on industrial equipment.
- Diagnose, troubleshoot and repair mechanical, electrical and electronic equipment.
- Read electrical and mechanical schematics and blueprints.
- Monitor and adjust systems to ensure proper operation.
- Perform safety inspections and testing.
- Install, start-up and commission new equipment.
- Troubleshoot and repair pneumatic and hydraulic systems.
- Maintain accurate records of maintenance activities and parts inventory.
- Assist in the training of other maintenance personnel.
- Perform minor fabrication and welding tasks.
Skills and Competencies to Have
- Mechanical aptitude and troubleshooting skills
- Knowledge of electrical components, wiring and safety protocols
- Ability to read and understand technical diagrams and schematics
- Understanding of plumbing and piping systems
- Familiarity with industrial tools and equipment
- Ability to use diagnostic equipment to identify problems
- Understanding of basic hydraulics and pneumatics
- Proficiency in operating a computer
- Good communication skills
- Ability to take initiative and work independently
- Ability to think critically and resolve complex problems
- Ability to maintain accurate records of maintenance activities
- Ability to lift heavy objects safely
Industrial maintenance technicians must possess a wide range of skills to effectively maintain industrial equipment and ensure efficient operations. One of the most important skills for an industrial maintenance technician to have is troubleshooting. Troubleshooting involves being able to identify and diagnose problems with industrial equipment, as well as being able to identify the root causes.
This skill is essential for industrial maintenance technicians because it enables them to quickly and accurately repair and replace faulty parts, as well as to prevent future problems by identifying and addressing potential issues before they become major problems. industrial maintenance technicians must also have strong problem-solving skills, as well as good communication and interpersonal skills. These skills are valuable in order to effectively collaborate with other technicians and engineers, troubleshoot problems, and provide input into the design and implementation of new industrial processes.
As a result, having these skills is essential for industrial maintenance technicians in order to ensure that industrial equipment is reliably maintained and functions properly.
Mechanical Technician, Boiler Technician, and HVAC Technician are related jobs you may like.
Frequent Interview Questions
- What experience do you have in industrial maintenance?
- What safety protocols do you follow when performing maintenance tasks?
- What is your experience with electrical systems, such as motors and power tools?
- How do you troubleshoot and diagnose mechanical issues in industrial machinery?
- What is your experience with preventive maintenance and inspections?
- How do you prioritize tasks and handle multiple projects?
- What experience do you have with welding and fabrication?
- How do you research and understand technical manuals and schematics?
- Describe a challenging maintenance project you have completed in the past.
- How do you stay up-to-date on the latest industry trends and technologies?
Common Tools in Industry
- Wrenches. Used to tighten or loosen nuts and bolts (eg: adjustable wrench).
- Drill Press. Used to make precise holes in materials (eg: bench-top drill press).
- Socket Set. Used to drive and remove nuts and bolts (eg: ratchet socket set).
- Screwdrivers. Used to drive screws and remove screws (eg: Phillips screwdriver).
- Pliers. Used to grip and hold objects (eg: needle-nose pliers).
- Soldering Iron. Used to join metal parts together (eg: electronic soldering iron).
- Grinders. Used to grind, cut, and polish materials (eg: angle grinder).
- Hammer. Used to drive nails or other fasteners into surfaces (eg: claw hammer).
- Crimpers. Used to attach wires to terminals or connectors (eg: insulated crimpers).
- Band Saw. Used to cut irregular shapes in materials (eg: bench top band saw).
Professional Organizations to Know
- Association for Maintenance Professionals (AMP)
- American Society for Quality (ASQ)
- International Maintenance Institute (IMI)
- Institute of Industrial and Systems Engineers (IISE)
- Reliability and Maintainability Symposium (RAMS)
- Society for Maintenance and Reliability Professionals (SMRP)
- Plant Engineering and Maintenance Association of Canada (PEMAC)
- American Society of Mechanical Engineers (ASME)
- Association for Facilities Engineering (AFE)
- International Facility Management Association (IFMA)
We also have Heavy Duty Mechanic, Precision Machinist, and Wind Turbine Technician jobs reports.
Common Important Terms
- Preventive Maintenance. Maintenance of equipment or machinery that is regularly scheduled in order to reduce the chances of it breaking down or malfunctioning.
- Troubleshooting. Diagnosing and resolving problems with machinery or equipment.
- PLC Programming. Programming of programmable logic controllers, which are used to automate industrial processes.
- Robotics. The use of robots to perform tasks such as assembly, welding, and packaging.
- Automation. The use of technology to automate processes and reduce the need for manual labor.
- Hydraulics. The use of liquids to power machinery, including pumps and valves.
- Electrical Theory. Understanding of the principles of electricity and electrical circuits.
- Welding. Joining two pieces of metal together using heat and a filler material.
- Machine Tool Operation. Operating various types of machine tools such as lathes, milling machines, and drill presses.
- Quality Control. Monitoring and inspecting products to ensure they meet a certain standard of quality.
Frequently Asked Questions
What is an Industrial Maintenance Technician?
An Industrial Maintenance Technician is a skilled professional who is responsible for the repair, maintenance, and installation of industrial machinery and equipment.
What qualifications are necessary to become an Industrial Maintenance Technician?
Most employers require Industrial Maintenance Technicians to have a high school diploma or GED and at least two years of experience in industrial maintenance. Additionally, some employers may require certification in a specific field or technology.
What type of tasks do Industrial Maintenance Technicians typically perform?
Industrial Maintenance Technicians typically perform tasks such as troubleshooting and repairing malfunctioning equipment, installing and configuring new machinery, performing preventive maintenance, and conducting safety inspections.
What tools might an Industrial Maintenance Technician use?
Industrial Maintenance Technicians typically use a variety of tools such as multimeters, power tools, welders, and computer diagnostic software.
What is the average salary for an Industrial Maintenance Technician?
The average salary for an Industrial Maintenance Technician is $47,820 per year, according to the Bureau of Labor Statistics.
What are jobs related with Industrial Maintenance Technician?
- Hydraulic Technician
- Automation Mechanic
- Bicycle Mechanic
- Generator Mechanic
- Appliance Mechanic
- Refrigeration Mechanic
- Structural Fabricator
- HVAC Mechanic
- Farm Equipment Mechanic
- Marine Mechanic
Web Resources
- What is an Industrial Maintenance Technician? miat.edu
- Industrial Maintenance Technician | Germanna Community College germanna.edu
- Industrial Maintenance Technician - STLCC stlcc.edu
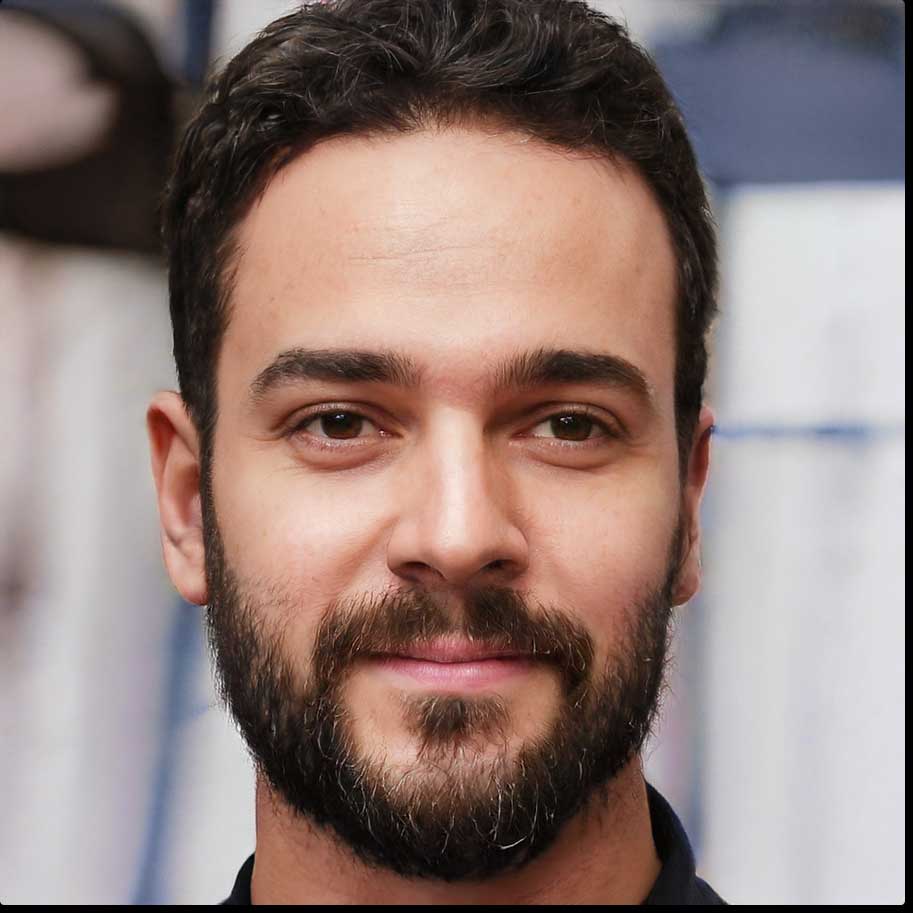