How to Be Certified Welding Inspector (CWI) - Job Description, Skills, and Interview Questions
The importance of Certified Welding Inspector (CWI) is essential for ensuring the highest quality of welded products. The CWI certification requires a comprehensive understanding of welding processes, materials, and codes. By passing the certification, inspectors have demonstrated the necessary knowledge to identify any welds that do not meet quality standards, ensuring that the welded products comply with safety regulations.
This, in turn, helps to reduce the risk of costly rework or failure due to poor workmanship, and it can also protect against potential liability issues. Furthermore, the CWI certification is often a requirement for inspection personnel on certain projects, providing employers with an assurance that their inspectors have the necessary qualifications.
Steps How to Become
- Complete an Eligibility Application from the American Welding Society (AWS). The AWS offers an online application for those pursuing CWI certification. This application will provide information regarding the requirements for eligibility, including education and experience.
- Obtain a Welding Certificate. To be eligible for CWI certification, you must possess a welding certificate. The type of welding certificate you need varies depending on the type of CWI certification you are seeking.
- Pass the CWI Written Examination. The CWI written examination is composed of three parts: a multiple-choice exam, an open-book exam, and a practical demonstration. The multiple-choice and open-book exams are administered at AWS accredited testing centers.
- Pass the CWI Practical Examination. The CWI practical exam is administered in two parts: a welding skills assessment, and a visual inspection assessment. The welding skills assessment requires candidates to demonstrate their ability to weld, while the visual inspection assessment requires candidates to identify welding defects.
- Complete the Re-certification Requirement. Once you have achieved your CWI certification, you must maintain it by completing a re-certification every three years. This includes passing the written exam and practical exam again, as well as accumulating industry experience over the three year period.
The need for reliable and qualified Certified Welding Inspectors (CWI) has become increasingly important in recent years, due to the growing complexity of welding operations and the potential hazards they can cause. The certification process requires extensive training and experience in order to be reliable and qualified. It is a multi-faceted process that assesses a candidate's knowledge of the welding process, safety procedures, and code requirements.
This ensures that the CWI is able to effectively inspect welded components for quality and compliance with industry safety standards. The certification also allows the CWI to accurately document their findings, which is essential for ensuring the safety of welded structures. having a reliable and qualified CWI on staff helps to protect workers and the public from potential hazards associated with welding operations.
You may want to check Certified Professional Coder (CPC), Certified Nursing Assistant (CNA), and Certified Diagnostic Medical Sonographer (RDMS) for alternative.
Job Description
- Conduct visual and dimensional inspections of welds, weld preparations, and weldments to ensure compliance with quality standards.
- Review and interpret welding drawings, specifications, and welding procedures to ensure proper application of welding codes and standards.
- Monitor and document welding operations to ensure compliance with applicable codes and standards.
- Perform evaluations of weldersÂ’ qualifications and certificates to verify compliance with welding codes and standards.
- Troubleshoot weld defects and recommend corrective actions.
- Develop, review, and implement welding inspection plans, procedures, and specifications.
- Train and mentor personnel in welding inspection techniques, safety procedures, and quality assurance principles.
- Prepare reports on welding inspection activities, results, and recommendations for corrective action.
- Maintain records of all welding inspections and documents.
- Communicate with customers, suppliers, and other stakeholders to resolve welding issues or concerns.
Skills and Competencies to Have
- Knowledge of welding inspection principles, processes, and procedures
- Ability to interpret drawings, specifications, and other weld related documents
- Proficiency in the use of non-destructive testing methods (such as radiography, ultrasonic testing, and magnetic particle testing)
- Knowledge of applicable welding codes, standards, and regulations
- Ability to analyze welds to determine quality and conformance to standards
- Proficiency in visual inspection of welds
- Knowledge of destructive and non-destructive evaluation techniques
- Understanding of welding fabrication methods
- Knowledge of metallurgy and its application to welding
- Proficiency in the use of measuring instruments and gauges
- Ability to provide technical guidance and instruction to personnel involved in welding operations
- Knowledge of welding process variables and their effects on weld quality
- Ability to identify problems related to weld quality and make corrective recommendations
- Knowledge of heat treatment, post-weld heat treatment, and other heat treatment related processes
- Understanding of occupational hazards associated with welding
Becoming a Certified Welding Inspector (CWI) is an important skill for any welding professional to possess. The rigorous process of obtaining this certification requires an individual to possess a thorough knowledge of all welding techniques and processes as well as an understanding of metallurgy, fabrication, and inspection processes. This certification enables a welding inspector to conduct quality assurance inspections of welds and other structural components to ensure compliance with applicable codes and standards.
Having this certification will give welders the confidence to know that their work is being inspected to the highest standards, thus leading to a higher quality product. As a result, certified welding inspectors are more likely to be hired by employers and are in high demand due to their expertise and knowledge.
Certified Medical Assistant (CMA), Certified Professional Coach (CPC), and Certified Surgical Technician (CST) are related jobs you may like.
Frequent Interview Questions
- What experience do you have as a Certified Welding Inspector?
- How would you ensure the quality and integrity of a welding project?
- What welding codes and standards are you familiar with?
- How would you handle a situation where a welding procedure did not meet specifications?
- What techniques do you use to inspect welds and weld joints?
- What steps do you take when performing a welding inspection?
- How do you ensure safety during welding inspections?
- What challenges have you faced while performing welding inspections?
- How do you stay current with the latest welding technologies and techniques?
- What processes do you use to document and report your findings from a welding inspection?
Common Tools in Industry
- Welding Torch. A handheld device used to join metal pieces together by melting and fusing them. (eg: Oxy-Acetylene Torch)
- Grinder. A tool used to shape or sharpen metal pieces using abrasive grinding wheels. (eg: Electric Grinder)
- Wire Brush. A tool used to clean or prepare surfaces for welding by removing rust, scale, and other contaminants. (eg: Steel Wire Brush)
- Gauge. A measuring device used to measure the size and shape of metal pieces. (eg: Dial Thickness Gauge)
- Chipping Hammer. A tool used to chip away weld spatter and other metal debris. (eg: Hand Chipping Hammer)
- Magnetic Particle Inspection (MPI). A non-destructive testing method used to detect surface and subsurface cracks in metal parts. (eg: Portable Magnetic Particle Inspection)
- X-Ray Testing. A non-destructive testing method used to detect internal flaws in metal parts. (eg: Digital X-Ray Testing)
- Ultrasonic Testing. A non-destructive testing method used to detect cracks, flaws, and other imperfections in metal parts. (eg: Handheld Ultrasonic Testing Unit)
Professional Organizations to Know
- American Welding Society (AWS)
- American Society of Mechanical Engineers (ASME)
- American Society for Nondestructive Testing (ASNT)
- International Institute of Welding (IIW)
- International Association for Bridge and Structural Engineering (IABSE)
- The Welding Institute (TWI)
- American Society of Civil Engineers (ASCE)
- National Board of Boiler and Pressure Vessel Inspectors (NBBI)
- American Institute of Steel Construction (AISC)
- American Society of Metals (ASM)
We also have Certified Legal Assistant (CLA), Certified Dietary Manager (CDM), and Certified Quality Engineer (CQE) jobs reports.
Common Important Terms
- Visual Inspection. The process of examining objects or materials visually to identify any defects or damage.
- Non-Destructive Testing (NDT). A type of testing that is used to determine the integrity of a material, component, or structure without causing damage to it.
- Welding. Joining two pieces of metal together by applying heat and pressure to form a permanent bond.
- Welding Standards. A set of guidelines and rules that govern the practice of welding, including safety and quality requirements.
- Heat Treatment. A process of heating and cooling metal to alter its physical and mechanical properties.
- Metallurgy. The study of the physical and chemical properties of metals and their behavior under different conditions.
- AWS D1. 1. The American Welding Society's Structural Welding Code - Steel, which provides guidance on welding practices for steel structures.
- AWS D1. 2. The American Welding Society's Structural Welding Code - Aluminum, which provides guidance on welding practices for aluminum structures.
- AWS D17. 1. The American Welding Society's Standard for Fusion Welding for Aerospace Applications, which provides guidance on welding practices for aerospace applications.
Frequently Asked Questions
What is a Certified Welding Inspector (CWI)?
A Certified Welding Inspector (CWI) is a trained and qualified professional who is certified to inspect welding projects for compliance with applicable codes and standards.
What qualifications are required to become a CWI?
To become a CWI, applicants must have at least four years of relevant welding experience, pass an American Welding Society (AWS) exam, and complete a practical examination demonstrating their proficiency in welding inspection.
What responsibilities do CWIs have?
The primary responsibility of a CWI is to ensure that any welding project meets the applicable codes and standards. This includes inspecting welds for quality, ensuring proper techniques are used, and verifying the welding materials meet the required specifications.
What organizations offer CWI certification?
The American Welding Society (AWS) is the primary organization offering CWI certification. The National Board of Boiler and Pressure Vessel Inspectors (NBBI) also offers similar certifications.
How often do CWIs need to renew their certifications?
CWIs must renew their certifications every three years to maintain their qualifications. During this time, they must obtain continuing education credits and demonstrate their knowledge of current codes and standards.
What are jobs related with Certified Welding Inspector (CWI)?
- Certified Information Security Manager (CISM)
- Certified Personal Trainer (CPT)
- Certified Industrial Hygienist (CIH)
- Certified Professional Photographer (CPP)
- Certified Pharmacy Technician (CPhT)
- Certified Veterinary Technician (CVT)
- Certified Medical Laboratory Technician (MLT)
- Certified Professional in Supply Management (CPSM)
Web Resources
- How to Become a (CWI) Certified Welding Inspector in 2022 - NEIT www.neit.edu
- Certified Welding Inspector (CWI) Prep Certificate | gotoLTC gotoltc.edu
- Welding and Metals Fabrication Program at CWI - College of Â… cwi.edu
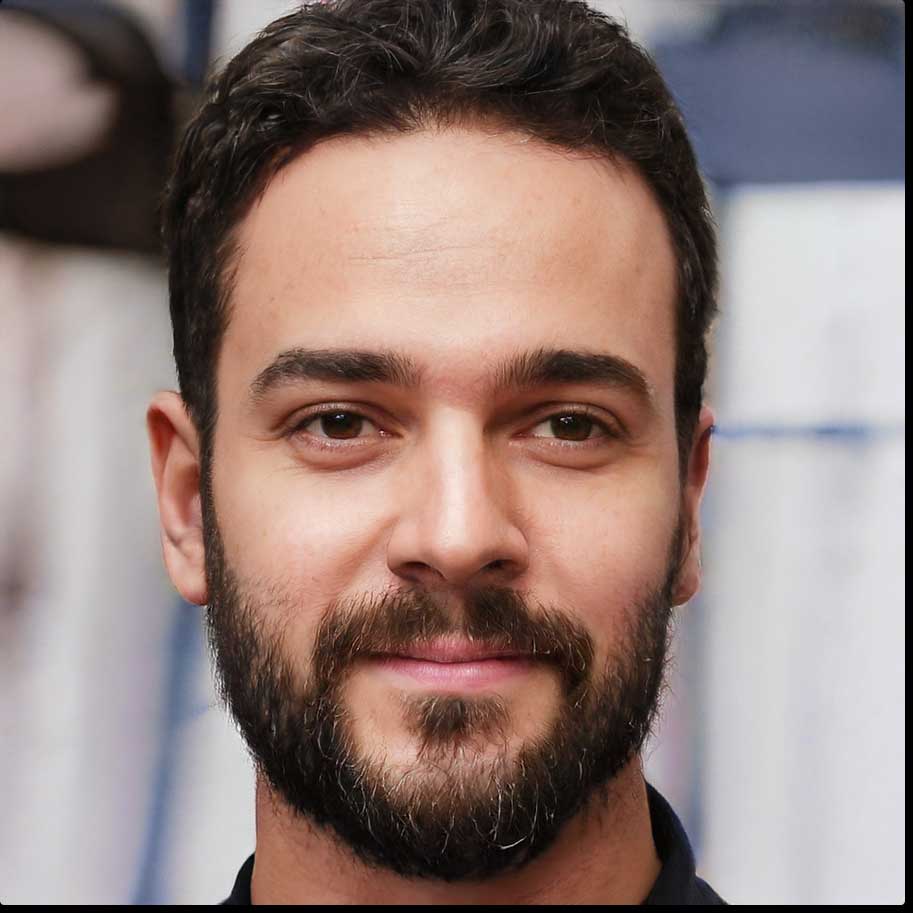