How to Be Safety Management Specialist - Job Description, Skills, and Interview Questions
Steps How to Become
- Obtain a Bachelor's Degree. A bachelor's degree in occupational safety, industrial hygiene, or a related field is the minimum educational requirement for a safety management specialist. Coursework typically includes topics such as risk management, ergonomics, environmental laws and regulations, and organizational behavior.
- Gain Experience. Many employers prefer safety management specialists who have experience in the field. Obtaining work experience through internships, volunteer positions, or entry-level jobs can be beneficial when applying for jobs.
- Pursue Professional Certification. Professional certifications are available for safety management specialists. These certifications can demonstrate a commitment to the profession and help qualify individuals for certain job opportunities.
- Join Professional Organizations. Joining professional organizations related to safety management can provide networking opportunities and access to continuing education.
- Maintain Current Knowledge. Staying up-to-date on safety regulations and technological developments is essential for safety management specialists. Participating in workshops, conferences, and webinars can help ensure that knowledge is current.
Safety management is essential in any organization to ensure the safety of employees, customers, and the public. An effective safety management specialist is key to making sure that the workplace is a safe place for everyone. To be an ideal and efficient safety management specialist, one must be knowledgeable in the latest safety regulations, have excellent communication skills, be able to coordinate safety programs, and be organized and detail oriented.
Having knowledge of safety regulations ensures that safety protocols are followed and up to date and that employees are aware of their responsibilities. Communication skills are critical to ensure that everyone understands the safety policies and procedures. Coordinating safety programs such as fire drills, emergency response plans, and hazard assessments helps to ensure that the workplace is prepared in the event of an emergency.
Being organized and detail oriented ensures that all safety procedures are completed and tracked. By having these skills and knowledge, a safety management specialist can help create a safe environment for everyone.
You may want to check Quality Control Specialist, Marketing Specialist, and Customer Service Specialist for alternative.
Job Description
- Develop and implement Safety Plans, Procedures, and Systems
- Investigate accidents and report findings
- Monitor production processes to ensure compliance with safety regulations
- Provide safety training and instruction to employees
- Analyze safety data to identify trends and recommend corrective measures
- Inspect workplaces for hazardous conditions and safety violations
- Develop and implement safety policies and procedures
- Evaluate the effectiveness of safety programs
- Prepare and submit reports on safety related activities
- Track, review, and analyze safety statistics and track corrective action
- Monitor equipment for safe operation
- Oversee safety drills and exercises
- Coordinate emergency response procedures
Skills and Competencies to Have
- Safety and Risk Management: Ability to identify and assess potential safety and health risks and develop strategies to mitigate them.
- Regulatory Compliance: Knowledge of safety regulations and compliance procedures.
- Organizational Skills: Ability to organize, prioritize and manage multiple tasks simultaneously.
- Leadership Skills: Ability to lead and motivate a team of safety and health professionals.
- Communication Skills: Excellent verbal and written communication skills.
- Training Skills: Ability to provide safety training and instruction.
- Investigation Skills: Ability to conduct investigations into safety incidents and develop corrective actions.
- Problem Solving Skills: Ability to identify and analyze safety problems, develop solutions and implement corrective actions.
- Technical Skills: Understanding of technical systems and processes related to safety management.
- Computer Skills: Proficiency in the use of computers, software and related technologies.
A Safety Management Specialist must possess a range of skills in order to be successful. Communication is key, as they need to be able to effectively convey safety policies and procedures to both staff and visitors. They must also be organized and detail-oriented, as they need to be able to maintain accurate records of safety information, training, and compliance.
they must have knowledge of applicable laws and regulations, such as OSHA and EPA standards, to ensure that their organization is compliant. Furthermore, they must be able to identify and mitigate potential risks and hazards, as well as develop and implement effective safety programs. Finally, strong problem-solving and critical thinking skills are essential for successful Safety Management Specialists, as they need to be able to respond quickly and efficiently to any problems or issues that arise.
When combined, these skills provide a strong foundation for a successful Safety Management Specialist.
Procurement Specialist, User Experience (UX) Designer Specialist, and Logistics Specialist are related jobs you may like.
Frequent Interview Questions
- What experience do you have in safety management?
- What do you believe are the key elements of a successful safety program?
- Describe your experience in developing and managing safety processes and procedures.
- How would you handle a situation in which a safety risk is identified but not addressed by management?
- What strategies have you implemented to ensure that safety standards are met?
- How do you stay current with safety regulations and best practices?
- What steps have you taken to ensure that safety protocols are followed?
- How do you handle situations where employees do not comply with safety procedures?
- What methods do you use to analyze and assess safety risks in the workplace?
- What techniques do you use to educate and train employees on safety procedures and protocols?
Common Tools in Industry
- Risk Assessment Tools. These tools help identify potential risks and hazards and analyze their severity. (eg: HAZOP methodology)
- Accident Investigation Tools. These tools help in the investigation of accidents that occur and identify areas for improvement. (eg: TapRoot Problem Solving)
- Safety Auditing Tools. These tools help to assess the safety of a workplace and identify areas for improvement. (eg: OSHA Compliance Audit)
- Risk Mitigation Tools. These tools help to reduce the risks and hazards present in the workplace. (eg: Job Safety Analysis)
- Emergency Response Planning Tools. These tools help to plan for emergency events and ensure the safety of personnel. (eg: Fire Drill Simulation)
- Training Management Tools. These tools help to track employee training and ensure that all personnel are adequately trained in safety procedures. (eg: eLearning Software)
- Document Management Tools. These tools help to organize safety-related documents and ensure they are easily accessible. (eg: Electronic Document Management System)
Professional Organizations to Know
- American Society of Safety Professionals (ASSP)
- International Institute of Risk and Safety Management (IIRSM)
- National Safety Council (NSC)
- British Safety Council (BSC)
- Institute of Risk Management (IRM)
- The American Board of Industrial Hygiene (ABIH)
- International Safety Management (ISM)
- The American Society of Safety Engineers (ASSE)
- National Association of Safety Professionals (NASP)
- Safety and Health Practitioners Association (SHPA)
We also have Public Relations (PR) Specialist, Travel Agent Specialist, and Inventory Control Specialist jobs reports.
Common Important Terms
- Risk Management. The process of identifying, assessing, and controlling potential risks or hazards in order to create a safe working environment.
- Incident Investigation. The process of gathering and analyzing evidence to identify the root cause of an incident that has occurred.
- Auditing. The process of evaluating a company's safety management system to ensure that it is compliant with applicable regulations.
- Training. The process of educating employees on safe work practices and procedures, to ensure they are aware of risks and how to safely perform their job duties.
- Hazard Identification. The process of identifying potential hazards in the workplace, such as chemical spills or electrical dangers.
- Emergency Response Planning. The development of plans on how to respond to an unexpected event, such as an earthquake or fire, in the workplace.
- Compliance. The practice of following applicable regulations and laws, to ensure that the workplace is safe and secure.
- Documentation. The process of recording safety information such as incident reports and safety audits.
- Accident Prevention. The process of implementing measures to reduce the risk of accidents in the workplace.
- Occupational Health and Safety. The practice of ensuring the health, safety, and welfare of workers in the workplace.
Frequently Asked Questions
What is a Safety Management Specialist?
A Safety Management Specialist is a professional who is responsible for developing, managing and assessing safety management systems, policies, and procedures to ensure compliance with relevant regulations.
What qualifications are needed to become a Safety Management Specialist?
To become a Safety Management Specialist, one should have a bachelors degree in occupational health and safety, environmental health and safety, or a related field. Additionally, passing the Certified Safety Professional (CSP) exam and obtaining professional certifications such as the Certified Safety Manager (CSM) and/or the Certified Industrial Hygienist (CIH) are also desirable.
What duties does a Safety Management Specialist perform?
Duties of a Safety Management Specialist include developing safety plans and policies, conducting risk assessments and audits, providing training to employees on safety protocols, monitoring operations for compliance with safety standards, and investigating workplace accidents.
What skills are important for a Safety Management Specialist to possess?
Skills important for a Safety Management Specialist include knowledge of relevant regulations and standards, problem-solving skills, excellent communication and interpersonal skills, sound judgment, and the ability to lead and motivate employees.
What is the average salary for a Safety Management Specialist?
The average salary for a Safety Management Specialist is $68,000 per year. This may vary depending on experience, certifications, and other factors.
What are jobs related with Safety Management Specialist?
- Network Specialist
- Graphic Design Specialist
- Administrative Support Specialist
- Instructional Design Specialist
- Tax Specialist
- Data Processing Specialist
- Credit Analyst Specialist
- Project Management Specialist
- Research and Development Specialist
- Application Development Specialist
Web Resources
- Safety Management Degree Program - Wayne State College www.wsc.edu
- Safety Management M.S. | WVU Online | West Virginia University online.wvu.edu
- Safety Management | Slippery Rock University www.sru.edu
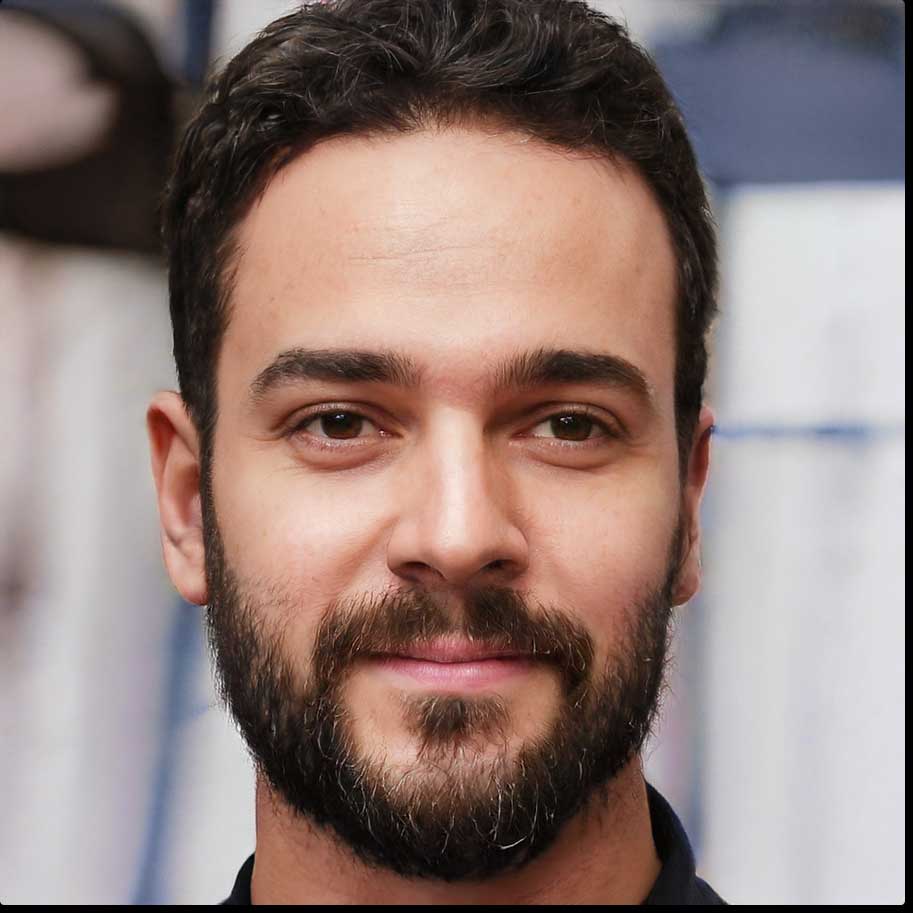