How to Be Quality Control Specialist - Job Description, Skills, and Interview Questions
Steps How to Become
- Earn a Bachelor's Degree. Most employers require quality control specialists to hold at least a bachelor's degree in a field like engineering, chemistry or industrial management.
- Gain Experience. Gain experience through internships or part-time positions in quality control or related fields.
- Get Certified. Obtain certifications to demonstrate knowledge of quality control processes and procedures, such as a Certified Quality Engineer or Certified Quality Inspector designation from the American Society for Quality.
- Develop Specialized Skills. Develop specialized skills, such as experience with Six Sigma, Lean manufacturing or statistical process control.
- Register with Professional Organizations. Register with organizations related to quality control, such as the American Society for Quality and the International Society for Quality.
- Stay Current. Stay up-to-date on new technologies, best practices and industry trends by reading journals and attending seminars and conferences.
Quality Control Specialists are responsible for ensuring the quality of products and services that a company produces. In order to ensure reliable and efficient quality control, it is important for Quality Control Specialists to use the most up-to-date techniques and technologies. This may involve conducting inspections and tests, examining materials, analyzing data, and using sophisticated software.
Quality Control Specialists must stay up-to-date on industry regulations and standards in order to ensure compliance. Further, Quality Control Specialists must be able to identify and resolve issues quickly and effectively as well as provide recommendations for improvement. By using the most up-to-date techniques and technologies, maintaining awareness of industry regulations, resolving issues quickly, and providing recommendations for improvement, Quality Control Specialists are able to ensure reliable and efficient quality control.
You may want to check Network Specialist, Claims Processing Specialist, and Project Management Specialist for alternative.
Job Description
- Maintain quality standards in production processes.
- Monitor product quality and performance.
- Develop and implement quality control systems.
- Investigate customer complaints and take appropriate corrective action.
- Establish and maintain testing procedures and standards.
- Analyze data to identify areas for improvement in the production process.
- Monitor compliance with quality standards.
- Develop and implement quality assurance training programs.
- Analyze product failure data and recommend corrective actions.
- Track and report on quality issues, customer complaints, and other related metrics.
- Develop, modify, and document inspection criteria for product acceptance.
- Lead root cause analysis for product defects and quality issues.
- Audit quality systems for compliance with established standards.
- Manage and coordinate the calibration of inspection and test equipment.
Skills and Competencies to Have
- Attention to detail
- Knowledge of quality control procedures and standards
- Problem-solving skills
- Data analysis and interpretation
- Communication and interpersonal skills
- Ability to work independently and as part of a team
- Knowledge of industry regulations
- Computer proficiency
- Documentation skills
- Planning and organizational skills
- Time-management skills
- Technical writing skills
Quality control specialists play an important role in ensuring the quality and safety of products and services. A key skill for a quality control specialist is attention to detail. Quality control specialists must have a keen eye for even the smallest discrepancies in products, services, or processes.
They must be able to quickly identify defects and other problems, and take appropriate actions to correct them. Quality control specialists must also have strong communication skills, as they must be able to explain their findings to management and other personnel. In addition, they must possess excellent analytical skills to analyze data and draw meaningful conclusions.
By utilizing these skills, quality control specialists help businesses to produce high-quality products and services that meet customer expectations, resulting in customer satisfaction and increased sales.
Safety Management Specialist, Instructional Design Specialist, and Marketing Specialist are related jobs you may like.
Frequent Interview Questions
- What experience do you have in quality control?
- How do you ensure that quality standards are met?
- Describe a time when you identified and addressed a quality control issue.
- What methods do you use to evaluate product quality?
- How do you stay up-to-date with the latest quality control trends and techniques?
- What techniques do you use to identify potential risks and issues?
- Can you provide examples of how you have successfully implemented quality control initiatives?
- How do you work with other departments to ensure quality standards?
- Describe a difficult situation where you had to manage a quality control issue.
- How do you ensure compliance with industry regulations and standards?
Common Tools in Industry
- Quality Management System (QMS). A comprehensive set of procedures and processes designed to ensure that a product or service meets quality standards. (e. g. ISO 9001)
- Quality Control Plan. An organized and documented system for controlling the quality of a product or service. (e. g. Six Sigma)
- Statistical Process Control (SPC). A technique used to control and monitor quality by analyzing data collected during the production process. (e. g. Run charts)
- Failure Mode and Effects Analysis (FMEA). A method used to identify potential risks associated with a product or process and develop strategies to prevent them from occurring. (e. g. Design FMEA)
- Metrology. The science of measuring objects and processes. (e. g. Calibration)
- Root Cause Analysis (RCA). A process used to identify the underlying cause of a problem or failure so that corrective action can be taken. (e. g. Ishikawa Diagrams)
- Quality Assurance (QA). A system of activities designed to ensure that a product or service meets quality standards. (e. g. Process Audits)
Professional Organizations to Know
- American Society for Quality (ASQ)
- Institute of Quality Assurance (IQA)
- International Quality Federation (IQF)
- International Organization for Standardization (ISO)
- National Institute of Standards and Technology (NIST)
- Association for Quality and Participation (AQP)
- International Association for Six Sigma Certification (IASSC)
- American Conference for Quality and Safety (ACQS)
- Global Association for Quality Management (GAQM)
- International Society for Quality in Healthcare (ISQua)
We also have Credit Analyst Specialist, Graphic Design Specialist, and Application Development Specialist jobs reports.
Common Important Terms
- Quality Assurance. The process of ensuring that products and services meet quality standards.
- Continuous Improvement. The process of identifying and making changes to processes and products to continually improve their performance.
- Root Cause Analysis. A process used to identify the underlying causes of problems so that the most appropriate solution can be identified.
- Kaizen. A Japanese term meaning “improvement”, referring to a continuous improvement process.
- Six Sigma. A set of techniques and tools for process improvement that aim to reduce defects and improve quality.
- ISO 9001. A standard issued by the International Organization for Standardization that sets out the requirements for a quality management system.
- Quality Management System. A system that defines the processes, procedures, and responsibilities necessary to achieve and maintain quality standards.
- Data Analysis. The process of collecting, organizing, and interpreting data in order to draw conclusions and make informed decisions.
- Quality Audit. An independent review of a quality system to verify its adequacy and effectiveness, and identify areas for improvement.
- Statistical Process Control (SPC). The use of statistical methods to monitor and control a process or product in order to maintain quality standards.
Frequently Asked Questions
What is the primary responsibility of a Quality Control Specialist?
The primary responsibility of a Quality Control Specialist is to ensure that products meet quality standards and specifications by inspecting, testing, and measuring products.
What qualifications should a Quality Control Specialist possess?
A Quality Control Specialist should possess strong attention to detail, problem-solving skills, and an understanding of quality control principles. They should also possess a technical background in engineering or a related field and knowledge of relevant industry standards.
What tools might a Quality Control Specialist use?
Quality Control Specialists might use various tools such as measuring devices, test equipment, microscopes, and chemical testing kits to inspect, test, and measure products.
How often do Quality Control Specialists report their findings?
Quality Control Specialists typically report their findings on a daily basis. They may also be required to submit weekly or monthly reports, depending on the requirements of their job.
What is the average salary for a Quality Control Specialist?
According to Payscale.com, the average salary for a Quality Control Specialist ranges from $40,000 to $50,000 per year.
What are jobs related with Quality Control Specialist?
- Legal Compliance Specialist
- Administrative Support Specialist
- Training Specialist
- Customer Service Specialist
- Systems Administrator Specialist
- Procurement Specialist
- Public Relations (PR) Specialist
- Accounting Specialist
- Operations Specialist
- Production Control Specialist
Web Resources
- Quality Control Specialist - Stanford University Careers careersearch.stanford.edu
- Quality Control Specialist at Stanford Medicine medcareers.stanford.edu
- Quality Control Specialist - Stanford University Careers careersearch.stanford.edu
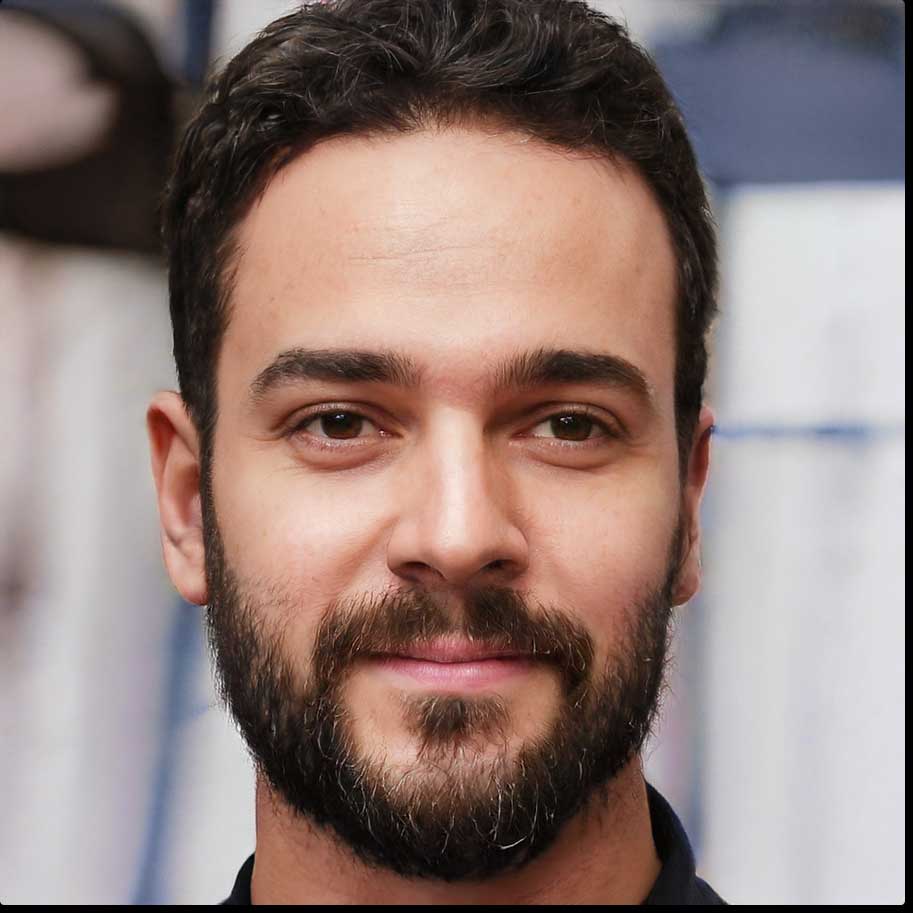