How to Be Safety Coordinator - Job Description, Skills, and Interview Questions
The lack of a safety coordinator in a workplace can lead to a range of costly consequences, such as an increase in accidents, injuries, and illnesses. When employees aren't informed of essential safety practices, they are more likely to put themselves and each other at risk of harm. This can lead to higher insurance costs, higher levels of absenteeism, and lower productivity levels.
not having someone to monitor safety protocols can lead to costly fines from regulatory bodies. Investing in a safety coordinator is a smart move for any business; it can help keep everyone safe and save money in the long run.
Steps How to Become
- Obtain a degree in a safety-related field. To become a safety coordinator, it is important to have a degree in a safety-related field such as Occupational Safety and Health, or Industrial Hygiene.
- Earn relevant certifications. Depending on the industry and employer, certifications such as Certified Safety Professional (CSP) or Associate Safety Professional (ASP) may be required.
- Gather experience. Most employers will require at least a few years of experience in a safety-related role before they hire a safety coordinator.
- Apply for safety coordinator jobs. Once you have the required qualifications, you can start applying for safety coordinator jobs.
- Develop safety programs. Once hired, you'll need to develop and implement safety programs that protect workers and comply with government regulations.
- Monitor safety operations. As a safety coordinator, you'll need to monitor safety operations and processes in the workplace to ensure compliance with regulations and identify areas for improvement.
- Investigate incidents. When accidents or incidents occur, you'll need to investigate them to determine the root cause and take corrective actions to prevent similar incidents from happening again.
- Establish safety policies and procedures. As a safety coordinator, you'll need to establish safety policies and procedures that ensure compliance with local, state, and federal regulations.
- Train employees. You'll also need to train employees on safety procedures and best practices so they can work safely and reduce the risk of accidents and injuries.
Safety coordinators play a critical role in ensuring that workplaces are safe and compliant with relevant laws and regulations. Without a skilled and competent safety coordinator, companies are at risk of facing serious financial and legal consequences due to workplace accidents, injuries, and illnesses. A safety coordinator must have a thorough understanding of safety regulations and procedures, as well as the ability to effectively communicate and enforce them.
they must continuously stay up-to-date on new regulations and changes in the industry, to ensure that the workplace remains safe and compliant. Having a safety coordinator that is skilled and competent is essential for the success of any business, as it will reduce the risk of costly accidents and provide employees with a safe working environment.
You may want to check Risk Management Coordinator, Graphic Design Coordinator, and Logistics Coordinator for alternative.
Job Description
- Develop and implement safety policies, procedures, and programs to ensure a safe work environment.
- Monitor compliance with safety regulations and standards.
- Investigate incidents, accidents, and near misses to determine root cause and recommend corrective action.
- Develop and deliver safety training programs.
- Monitor and inspect workplace conditions to identify and correct potential hazards.
- Develop and implement emergency response plans.
- Conduct safety audits and inspections.
- Monitor changes in regulations and industry standards.
- Maintain records of safety inspections, training, and incidents.
- Provide advice and guidance to employees on safe working practices.
Skills and Competencies to Have
- Knowledge of safety regulations and best practices
- Ability to create and enforce safety procedures
- Ability to identify and reduce safety risks
- Excellent communication and interpersonal skills
- Strong problem-solving and analytical skills
- Experience with safety management systems
- Ability to manage emergency situations
- Proficient in safety training and audits
- Ability to develop effective safety policies
- Knowledge of hazardous materials handling, storage, and disposal
Safety coordination is a critical skill to have in any workplace, as it is responsible for ensuring the safety of all personnel and equipment. Inadequate safety measures can lead to serious accidents, injuries and even fatalities, which can have a devastating effect on individuals, organisations and society as a whole. Safety coordination requires an understanding of the relevant laws, regulations and procedures, as well as the ability to develop and implement effective safety plans.
A good safety coordinator must also have excellent communication and interpersonal skills, enabling them to work with all levels of personnel and to effectively coordinate safety initiatives. they need to be able to identify potential hazards and take proactive steps to ensure the safety of personnel and equipment. By having a good safety coordinator, organisations can minimise the risk of accidents and ensure the safety of everyone involved.
Inventory Coordinator, Procurement Coordinator, and Quality Control Coordinator are related jobs you may like.
Frequent Interview Questions
- What experience do you have working in safety and risk management?
- How would you ensure a safe and secure work environment?
- What safety protocols do you have in place to reduce the risk of injury and illness?
- How do you stay up-to-date with the latest safety regulations and standards?
- What strategies do you use to ensure compliance with safety regulations?
- How do you motivate employees to follow safety procedures?
- How do you handle challenging or difficult situations related to safety?
- What measures do you take to investigate accidents and injuries?
- How do you ensure that safety training is effective and up-to-date?
- What experience do you have developing and implementing safety policies?
Common Tools in Industry
- Risk Assessment Tool. A tool used to identify and measure potential risks and hazards in the workplace (eg: SafetyCulture iAuditor).
- Emergency Response Plan. A plan outlining procedures to be followed in the event of an emergency (eg: Ready. gov Emergency Preparedness Plan).
- Accident Reporting System. A system used to collect and report data regarding workplace accidents (eg: OSHA Accident Reporting Tool).
- Training Management Software. A software tool used to manage employee training programs and ensure compliance with safety regulations (eg: Intelex Training Management Software).
- Compliance Audit Tool. A tool used to audit and verify that safety standards are being met in the workplace (eg: SafetyNet Compliance Audit Tool).
- Safety Data Sheets. A document that provides information about hazardous chemicals and materials in the workplace (eg: OSHA Hazard Communication Standard).
- Safety Inspections. A process used to identify and address potential safety hazards in the workplace (eg: OSHA Safety Inspections).
- Incident Investigation Software. A software tool used to document and analyze workplace incidents, accidents, and near misses (eg: Vivid Learning Systems Incident Investigation Software).
Professional Organizations to Know
- American Society of Safety Professionals
- National Safety Council
- International Safety Council
- National Fire Protection Association
- American Industrial Hygiene Association
- American Conference of Governmental Industrial Hygienists
- National Institute for Occupational Safety and Health
- American Society of Safety Engineers
- Voluntary Protection Programs Participants' Association
- International Association of Safety Professionals
We also have Membership Coordinator, Financial Coordinator, and Workshop Coordinator jobs reports.
Common Important Terms
- Risk Assessment. A process to identify potential hazards and analyze the risk associated with them in order to develop measures to minimize or eliminate the risk.
- Accident Prevention. Strategies and procedures put in place to reduce the likelihood of an accident or injury occurring.
- Emergency Response Plan. A written document outlining the procedures to be followed in the event of an emergency or disaster.
- Hazard Communication. A system used to ensure that employees are aware of potential hazards in their work environment and what steps they should take to minimize the risk of injury or illness.
- Safety Training. Training designed to help employees recognize, respond to, and prevent hazards in the workplace.
- Personal Protective Equipment (PPE). Clothing, equipment, and other items used to protect workers from potential hazards.
- Job Safety Analysis (JSA). A systematic review of a job to identify any potential hazards and develop safe work methods to reduce the risk of injury or illness.
Frequently Asked Questions
What is a Safety Coordinator?
A Safety Coordinator is a professional responsible for creating and enforcing safety policies in a workplace, ensuring that all employees adhere to safety regulations and providing support for the implementation of safety programs.
What qualifications are needed to become a Safety Coordinator?
To become a Safety Coordinator, you typically need a minimum of a bachelors degree in occupational health and safety, environmental health or a related field. You must also have experience in safety management and relevant certifications such as Certified Safety Professional (CSP) or Certified Industrial Hygienist (CIH).
What are the duties of a Safety Coordinator?
The duties of a Safety Coordinator may include developing, implementing and monitoring safety policies; conducting safety inspections; training and educating employees on safety practices; investigating accidents and incidents; and preparing reports on safety hazards and violations.
What is the average salary for a Safety Coordinator?
The average salary for a Safety Coordinator is about $60,000 per year, according to Payscale.com. Salaries can vary greatly depending on factors such as experience, job location and employer.
What is the job outlook for Safety Coordinators?
Job growth for Safety Coordinators is expected to be strong over the next 10 years, with an estimated 11% increase in jobs through 2029. This growth is due to the increasing demand for workplace safety and health regulations as well as technological advances that make workplaces safer.
What are jobs related with Safety Coordinator?
- Documentation Coordinator
- Technical Support Coordinator
- Data Coordinator
- Marketing Coordinator
- Office Coordinator
- Volunteer Coordinator
- Production Coordinator
- Distribution Coordinator
- Scheduling Coordinator
- Development Coordinator
Web Resources
- Safety Coordinator Program | Emergency Management & Safety emergency.unt.edu
- Safety Coordinators - Safety - Naval Postgraduate School www.nps.edu
- Safety Coordinator - ANR Environmental Health & Safety safety.ucanr.edu
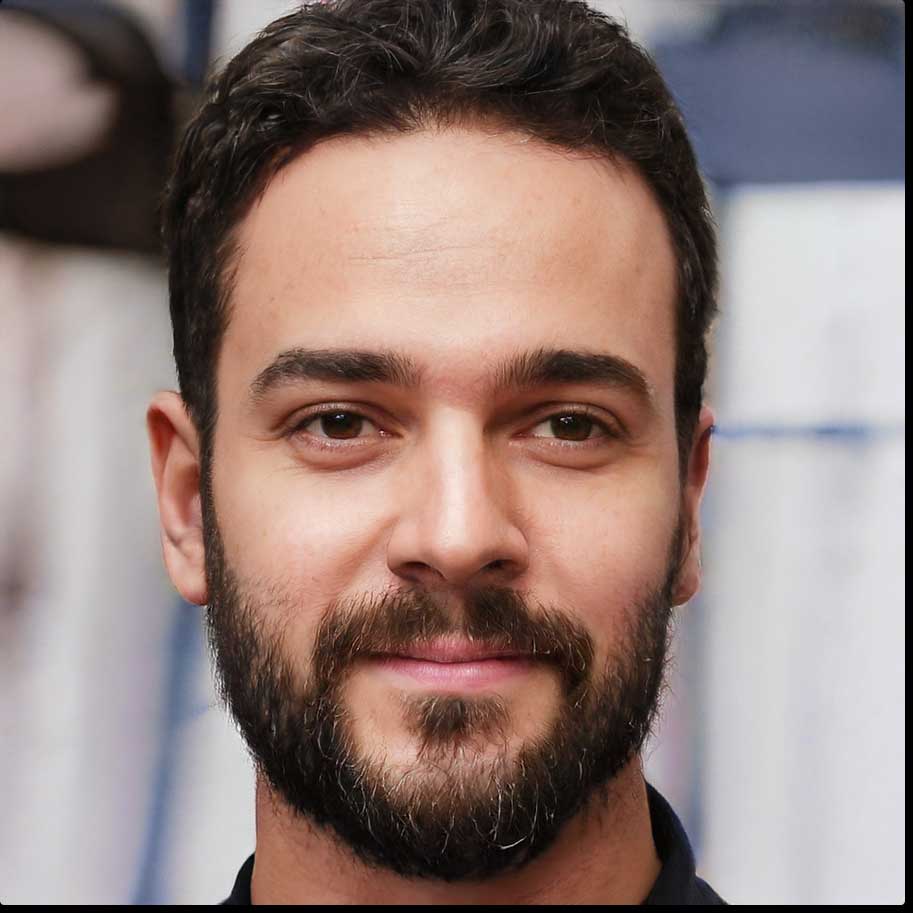