How to Be Quality Control Coordinator - Job Description, Skills, and Interview Questions
Steps How to Become
- Obtain a Bachelor's Degree. The first step to becoming a quality control coordinator is to obtain a bachelor's degree in a related field, such as engineering, business, or quality control management.
- Earn Certification. Quality control coordinators should consider earning professional certification to demonstrate their expertise and knowledge in the field. Organizations such as the American Society for Quality offer certification programs that require passing an exam and meeting other guidelines.
- Gain Experience. Most employers prefer to hire quality control coordinators with at least two years of experience in a related field. Individuals can gain experience through internships or volunteer positions while they are in school or by working in a related entry-level position.
- Develop Skills. Quality control coordinators should develop strong problem-solving, communication, and organizational skills. They must also be comfortable working with computers and other technology.
- Stay Up to Date. Quality control coordinators must stay up to date on new regulations, techniques, and products in their field. They should take advantage of online courses and other educational resources that are available to stay current with industry trends.
Quality Control Coordinators are responsible for ensuring a high level of quality and consistency in all products produced. They are reliable and capable individuals who monitor and inspect products to ensure that they meet quality standards. To be successful in this role, Quality Control Coordinators must possess a strong attention to detail, excellent problem-solving skills, and the ability to work independently.
They must also be adept at creating and implementing quality control plans, inspecting raw materials and finished products, and documenting results. The impact of these activities is twofold: by ensuring that products are up to standard, Quality Control Coordinators help reduce the risk of customer dissatisfaction and product recalls, while also helping to maintain or increase company profits.
You may want to check Scheduling Coordinator, Maintenance Coordinator, and Volunteer Coordinator for alternative.
Job Description
- Oversee the quality control process for all products and services
- Develop and implement quality control standards and procedures
- Monitor and inspect products and services for compliance with quality standards
- Test and analyze products to ensure they meet quality standards
- Troubleshoot and resolve quality problems
- Maintain records of product inspections and test results
- Prepare reports on quality assurance activities
- Develop and implement corrective actions to improve product quality
- Monitor customer feedback and product reviews
- Train staff in quality control processes
- Track supplier performance to ensure product quality
- Collaborate with other departments to ensure customer satisfaction
Skills and Competencies to Have
- Attention to Detail
- Knowledge of Quality Assurance Principles
- Ability to Interpret Technical Drawings
- Analytical and Problem-Solving Skills
- Computer Proficiency
- Excellent Interpersonal and Communication Skills
- Organizational Skills
- Leadership Skills
- Self-Motivation
- Ability to Work Under Pressure
- Critical Thinking
- Ability to Make Decisions
- Documentation and Record Keeping Skills
- Understanding of Quality Auditing and Inspections Procedures
Quality Control Coordinators play an important role in ensuring the quality of products and services. They are responsible for creating and implementing quality control policies and procedures to ensure that products meet established standards. Quality control coordinators must have several key skills in order to be successful.
These include strong organizational and communication skills, attention to detail, problem-solving abilities, and the ability to work well with teams. They must also possess a deep understanding of the product or service they are overseeing, and be able to identify potential problems or concerns before they become major issues. Quality control coordinators must also have the ability to stay up to date on industry trends and regulations, as well as develop innovative solutions to improve quality control processes.
By having these skills, Quality Control Coordinators can ensure that the products their company produces meet the required standards, thus increasing customer satisfaction and improving the reputation of the organization.
Workshop Coordinator, Distribution Coordinator, and Client Services Coordinator are related jobs you may like.
Frequent Interview Questions
- What experience do you have in quality control and assurance?
- What techniques do you use to ensure quality control?
- How do you ensure accuracy and consistency in your work?
- How do you handle customer complaints and inquiries?
- What strategies do you employ to motivate team members to strive for the highest quality standards?
- How do you keep up with the latest trends and advancements in quality control?
- What steps do you take to identify potential issues and recommend solutions?
- How do you stay current with changes in quality assurance regulations?
- What types of reports have you written related to quality control?
- How have you used data analysis to improve quality control processes?
Common Tools in Industry
- Quality Assurance Software. Quality assurance software provides companies with an automated way to monitor, detect, and track quality issues in their products. (Eg: Checkmarx)
- Root Cause Analysis Tool. Root cause analysis tools are used to identify the underlying reasons for failed processes or systems. (Eg: Fishbone Diagrams)
- Defect Management Software. Defect management software is designed to help organizations track, manage, and resolve defects in their products. (Eg: Bugzilla)
- Automated Testing Tools. Automated testing tools are used to execute tests on software applications or systems and provide feedback quickly. (Eg: Selenium)
- Process Mapping Software. Process mapping software helps organizations visualize their processes, enabling them to identify bottlenecks, inefficiencies, and areas for improvement. (Eg: Lucidchart)
- Risk Management Tool. Risk management tools help organizations identify, assess, and mitigate risks associated with their products and processes. (Eg: RiskLens)
Professional Organizations to Know
- American Society for Quality
- International Quality Federation
- Total Quality Management Association
- Institute of Quality Assurance
- International Association for Six Sigma Certification
- Global Association for Quality Management
- Association for Quality and Participation
- Chartered Quality Institute
- International Organization for Standardization
- National Quality Forum
We also have Marketing Coordinator, Security Coordinator, and Networking Coordinator jobs reports.
Common Important Terms
- Quality Assurance (QA). The process of ensuring that products or services meet established standards of quality.
- Quality Management (QM). The systematic approach to managing the quality of an organization's products and services.
- Quality Control (QC). The process of inspecting, testing, and verifying that products or services meet specified requirements.
- Defects. An imperfection or fault in a product or service that prevents it from meeting its required specifications.
- Root Cause Analysis (RCA). A systematic method to identify the underlying cause of a product or service failure.
- Non-conformance. An instance in which a product or service does not meet the required specifications.
- Corrective Action. The process of identifying and eliminating the root cause of a product or service failure.
- Continuous Improvement. The process of making ongoing changes to improve the quality of products and services.
Frequently Asked Questions
What duties does a Quality Control Coordinator typically perform?
Quality Control Coordinators are responsible for overseeing quality control processes and procedures, ensuring that products and services meet established standards, and recommending corrective actions when necessary. They also monitor quality control metrics, inspect products, analyze quality trends, and develop and implement quality control initiatives.
What qualifications are needed to become a Quality Control Coordinator?
To become a Quality Control Coordinator, individuals should possess a bachelor's degree in a related field such as engineering, science or quality assurance. Additionally, experience in quality control and quality assurance processes, knowledge of ISO 9001 standards, and proficiency with Microsoft Office is highly beneficial.
How many hours does a Quality Control Coordinator typically work?
The typical work schedule for a Quality Control Coordinator is full-time, with approximately 40 hours per week. However, the number of hours may vary depending on the organizations needs.
What type of environment does a Quality Control Coordinator usually work in?
Quality Control Coordinators typically work in an office or factory setting. They may be required to inspect products and materials in both indoor and outdoor environments, depending on the nature of their job.
What is the average salary of a Quality Control Coordinator?
The average salary of a Quality Control Coordinator is approximately $52,000 per year. This figure can vary depending on experience, location, and other factors.
What are jobs related with Quality Control Coordinator?
- Membership Coordinator
- Facilities Coordinator
- Media Coordinator
- Inventory Coordinator
- Logistics Coordinator
- Production Coordinator
- Financial Aid Coordinator
- Safety Coordinator
- Development Coordinator
- Documentation Coordinator
Web Resources
- Quality Control/Human Resources Coordinator Greene Center ... careereducation.rochester.edu
- Human Resources/Quality Control Coordinator Career and ¦ career.mercy.edu
- What is a Manufacturing Quality Controller? | Goodwin University www.goodwin.edu
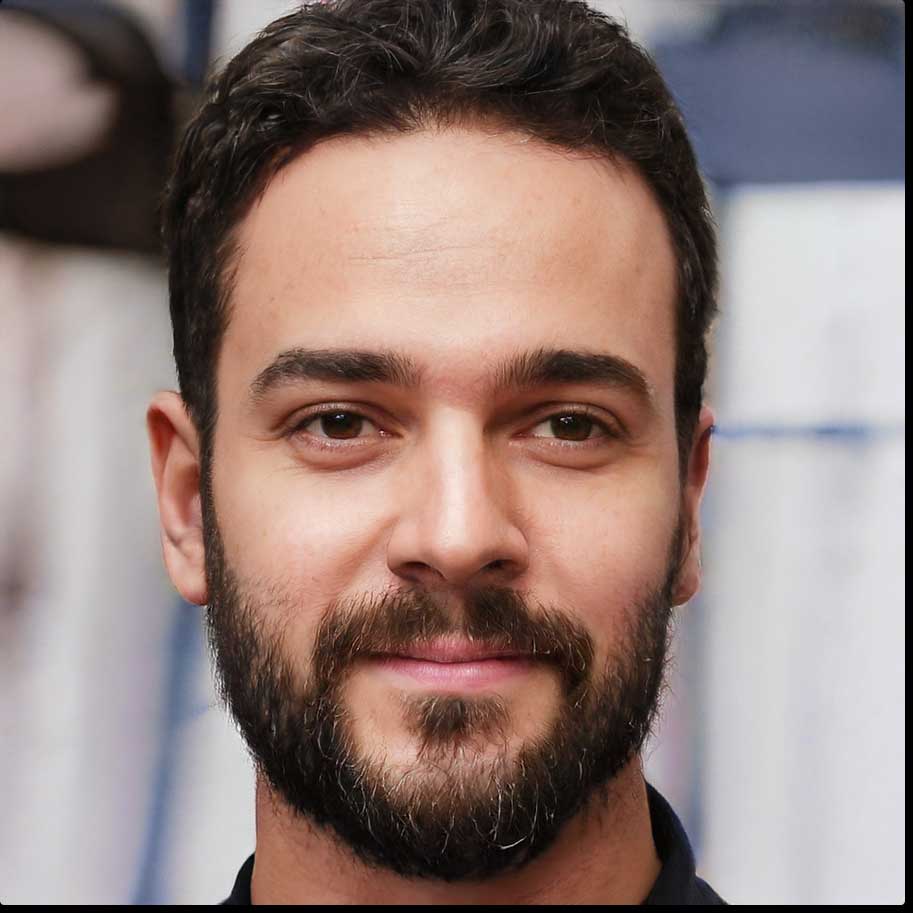