How to Be Quality Controller - Job Description, Skills, and Interview Questions
The use of quality control in a business environment has a major impact on the success of an organization. When quality control measures are in place, they help ensure that the products or services offered meet the necessary standards. This helps to protect the companyâs reputation, which can lead to increased customer loyalty and larger profits.
Poor quality control, on the other hand, can have serious consequences, such as customer dissatisfaction and decreased sales. Quality control also helps to reduce costs by eliminating or reducing the need for costly repairs or replacements due to faulty products or services. This can result in lower overhead costs, improved efficiency, and increased customer satisfaction.
Quality control is thus an essential part of any successful business plan.
Steps How to Become
- Earn a bachelor's degree in a field related to quality control. Quality control professionals typically have a degree in engineering, science, business or technology.
- Take courses in statistics, mathematics and quality control. Quality control requires knowledge of mathematics and the ability to interpret data.
- Gain experience in the field. Many employers prefer to hire quality control professionals with at least two years of experience in a related field.
- Become certified. Certification is not required to work in the field, but it may help you stand out from other job applicants. The American Society for Quality offers several certification programs for quality control professionals.
- Join a professional organization. Professional organizations can provide job opportunities, continuing education and networking opportunities for quality control professionals.
You may want to check Logistics Controller, Materials Controller, and IT Controller for alternative.
Job Description
- Develop and maintain quality control standards
- Monitor production processes to ensure that products meet quality standards
- Inspect products for defects and non-conformity
- Test finished products for functionality and performance
- Investigate customer complaints about product quality
- Record and analyze quality data
- Update and implement quality control procedures
- Monitor compliance of production processes with standards and regulations
- Identify potential process improvements
- Train staff on quality control procedures
Skills and Competencies to Have
- Knowledge of Quality Control Principles
- Detailed Knowledge of Quality Control Processes
- Expertise in Statistical Analysis and Data Interpretation
- Ability to Identify and Resolve Quality Issues
- Knowledge of Health and Safety Regulations
- Excellent Organizational and Problem-Solving Skills
- Ability to Follow Detailed Instructions
- Strong Communication and Interpersonal Skills
- Attention to Detail
- Proficiency with Microsoft Office Suite
The ability to be a successful Quality Controller is largely dependent on the ability to pay attention to detail and have an eye for accuracy. Being able to spot errors and identify areas for improvement is essential for this role. having strong analytical skills and problem-solving capabilities is important for ensuring processes are efficient and effective.
Furthermore, good communication skills are necessary for relaying information and collaborating with other members of a team. Finally, having a solid understanding of relevant regulations, standards, and industry best practices is essential for achieving quality end results. These traits combined make a successful Quality Controller as they are able to ensure processes are compliant to industry standards and customer expectations.
Inventory Controller, Shipping Controller, and Data Controller are related jobs you may like.
Frequent Interview Questions
- What experience do you have in quality control?
- How do you ensure that a product meets quality standards?
- How do you prioritize tasks to meet deadlines?
- Describe a time when you had to resolve a quality-related issue.
- What techniques do you use to identify potential issues or defects?
- How do you verify that all production processes are compliant with quality standards?
- How do you ensure that all employees are following quality procedures?
- What methods do you use to document and track quality control data?
- How would you handle a situation where the customer is not satisfied with the quality of a product?
- What strategies do you employ to stay up-to-date on the latest industry trends and best practices in quality control?
Common Tools in Industry
- Gauges. Tools used to measure the dimensions of an item or part, such as a caliper (eg: measuring the diameter of a bolt).
- Scales. Tools used to measure weight, such as a balance (eg: weighing a package before shipping).
- Meters. Tools used to measure electrical current, voltage, and other physical quantities, such as a voltmeter (eg: measuring the voltage of a battery).
- Spectrometers. Tools used to analyze the composition of substances, such as an infrared spectrometer (eg: analyzing the composition of a chemical compound).
- Inspection Mirrors. Tools used to look into hard-to-reach places, such as a boroscope (eg: inspecting for corrosion inside a pipe).
- Optical Comparators. Tools used to compare a part to its blueprint, such as a profile projector (eg: checking the shape of a machined part).
Professional Organizations to Know
- International Institute of Quality Assurance (IIQA)
- American Society for Quality (ASQ)
- Institute for Quality Assurance Professionals (IQAP)
- The International Organization for Standardization (ISO)
- The Chartered Quality Institute (CQI)
- American Association for Quality (AAQ)
- National Association for Quality (NAQ)
- International Association for Six Sigma Certification (IASSC)
- International Society for Quality in Health Care (ISQua)
- The European Organisation for Quality (EOQ)
We also have Budget Controller, Configuration Controller, and Production Controller jobs reports.
Common Important Terms
- Quality Assurance. The practice of ensuring that a product or service meets the agreed upon quality standards.
- Quality Standard. A set of criteria that a product or service must meet in order to be considered of acceptable quality.
- Quality Management System. A system used to ensure that quality standards are met throughout the production and delivery process.
- Quality Audit. An independent assessment of a product or service to ensure that it meets the required quality standards.
- Quality Improvement. The process of continually striving to improve the quality of a product or service.
- Quality Control. The practice of monitoring and verifying the quality of a product or service to ensure that it meets the required standards.
Frequently Asked Questions
What is Quality Control?
Quality Control is a process used to ensure that products or services meet the required quality standards set out by the organization.
What are the key roles of a Quality Controller?
The key roles of a Quality Controller include inspecting and testing products, ensuring that quality standards are met, identifying any defects or non-conformities, and providing feedback to the relevant departments.
What qualifications are needed to become a Quality Controller?
In order to become a Quality Controller, one must typically have a degree in an engineering field, such as quality engineering, or a related field such as industrial engineering. Additionally, knowledge of quality assurance and control principles is often preferred.
What tools and technologies are used in Quality Control?
Some of the tools and technologies used in Quality Control include analytical tools such as statistical process control (SPC), defect tracking systems, automated testing tools, and other quality management systems.
What is the average salary for a Quality Controller?
The average salary for a Quality Controller is around $60,000 per year.
What are jobs related with Quality Controller?
- Plant Controller
- Compliance Controller
- Document Controller
- Systems Controller
- Cost Controller
- Risk Controller
- Network Controller
Web Resources
- What is a Manufacturing Quality Controller? | Goodwin University www.goodwin.edu
- How to become a quality controller - Open www.open.edu.au
- Quality Control in Engineering Management | A-State Online degree.astate.edu
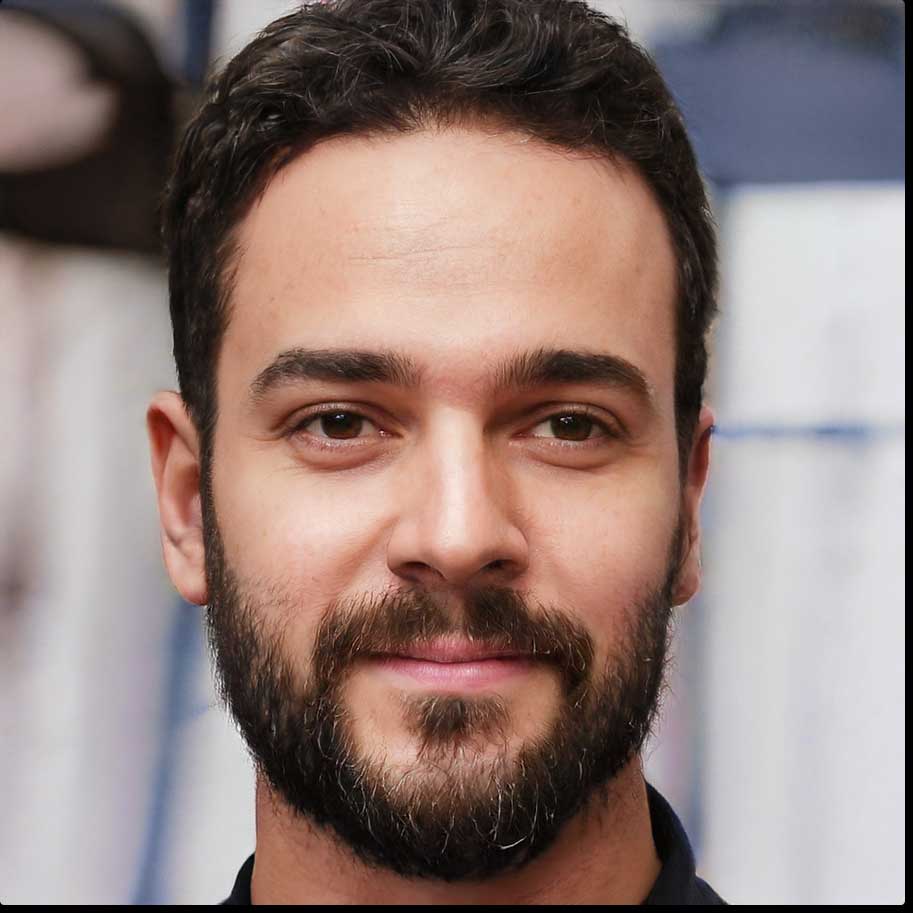