How to Be Inventory Controller - Job Description, Skills, and Interview Questions
Inventory controllers are essential to businesses as they are responsible for controlling, monitoring and organizing the flow of inventory. The main cause of having an inventory controller is to ensure that there is an accurate record of all inventory, and that the business has enough on hand to meet customer demand. As a result, inventory controllers create and implement systems to keep track of all the items in the inventory and ensure that the right quantity is available at the right time.
They also oversee the purchase of new items, analyze data to identify trends, and work with suppliers to maintain inventory levels. Without an inventory controller, businesses may suffer from stock shortages, resulting in lost sales, decreased customer satisfaction, and financial losses.
Steps How to Become
- Earn a Bachelor's Degree. Pursuing a bachelors degree in business, accounting, or finance is the first step to becoming an inventory controller. Coursework in these degrees may include economics, mathematics, accounting, and business management.
- Gain Work Experience. It is beneficial to gain work experience in a related field such as accounting, auditing, or bookkeeping. This experience can be gained through internships or part-time jobs.
- Become Certified. Becoming certified as a Professional Inventory Controller (PIC) can help boost your resume and give you a competitive edge. The National Association of Inventory Control Professionals offers a certification program for those interested in becoming an inventory controller.
- Develop Your Skills. As an inventory controller, you will need to have strong analytical, organizational, and problem-solving skills. You should also be knowledgeable about inventory management, accounting principles, and purchasing processes.
- Apply for Jobs. Once you have earned your degree and gained relevant experience, you can start applying for jobs as an inventory controller. You can search for jobs online on job sites or in your local newspaper.
Inventory control is a key element of efficient supply chain management. When implemented correctly, it helps to ensure that the right amount of products are available, at the right time and in the right place. This, in turn, allows businesses to meet customer demands, minimize overhead costs, and maximize profits.
To be successful at inventory control, businesses must have skilled personnel with an understanding of forecasting and stock management practices. They must also have access to technology such as barcode scanners, software for tracking and reporting, and automated data collection systems. By utilizing these tools and techniques, businesses are able to keep accurate track of inventory levels, reduce losses due to theft or spoilage, and maximize their profits.
You may want to check Budget Controller, Systems Controller, and Process Controller for alternative.
Job Description
- Monitor inventory levels and order materials as needed.
- Prepare and submit purchase orders and track shipments.
- Receive, inspect, and store incoming materials.
- Maintain accurate records of inventory movements and adjustments.
- Analyze inventory data to identify trends in usage and demand.
- Plan and coordinate the disposal of excess or obsolete inventory.
- Develop and implement inventory control procedures and systems.
- Monitor inventory costs and ensure accuracy of financial records.
- Evaluate current inventory levels and forecast future requirements.
- Monitor supplier performance and ensure timely delivery of materials.
Skills and Competencies to Have
- Strong organizational and time management skills.
- Proficiency in computer systems, including Microsoft Office Suite, accounting software, and inventory tracking software.
- Attention to detail and accuracy in all tasks.
- Ability to work independently and in a team environment.
- Excellent problem-solving skills.
- Ability to handle multiple tasks simultaneously.
- Ability to analyze data and make appropriate decisions.
- Knowledge of basic accounting principles.
- Ability to identify discrepancies in inventory data and take timely corrective action.
- Ability to plan and manage inventory levels according to company needs.
- Knowledge of safety procedures, regulations, and best practices related to warehouse operations.
Inventory Control is an essential skill for any business as it helps to ensure that the right amount of products are available at the right time. This is achieved by monitoring the inventory levels and making orders as needed. It also involves tracking the movement of products in and out of a warehouse, and ensuring that the warehouse is kept in order.
Doing this requires an understanding of the supply chain and an ability to anticipate customer demand. It also requires excellent organizational and communication skills, as well as a good knowledge of accounting principles. Proper inventory control can help to reduce storage costs, minimize stockouts and improve customer service.
As a result, businesses can improve their bottom line, increase customer satisfaction and grow their operations.
Materials Controller, Risk Controller, and Plant Controller are related jobs you may like.
Frequent Interview Questions
- How do you ensure accuracy in inventory counts?
- Describe a time when you had to troubleshoot an inventory issue.
- How do you stay updated with changes in inventory management systems?
- What experience do you have with inventory software and databases?
- How do you keep track of inventory levels and manage stock adjustments?
- What techniques do you use to minimize errors in the inventory process?
- How would you respond to a situation where inventory is not accurately accounted for?
- What strategies do you use to improve inventory performance?
- What challenges have you encountered while managing inventory?
- How do you ensure that all inventory is tracked in a timely manner?
Common Tools in Industry
- Inventory Management Software. This software helps businesses manage their inventory by tracking stock levels, orders, sales, and deliveries. (e. g. QuickBooks Inventory)
- Barcode Scanner. A device that reads barcodes and provides a digital representation of the product's information. (e. g. Zebra Barcode Scanner)
- Point of Sale System. A system used to process sales transactions in retail stores. (e. g. Square POS System)
- Warehouse Management System. A software solution used to manage the movement, storage, and retrieval of materials within a warehouse. (e. g. Oracle WMS)
- RFID Reader. A device that reads radio-frequency identification tags and provides a digital representation of the product's information. (e. g. Alien Technology Reader)
- Automated Data Capture System. A system used to automatically capture data from various sources such as barcodes, RFID tags, and voice recognition systems. (e. g. DataLogic ADC System)
- Supply Chain Management Software. A software suite used to plan, track, and optimize the movement of goods from the supplier to the consumer. (e. g. SAP SCM Software)
- Warehouse Automation System. A system used to automate warehouse processes such as picking, packing, and shipping. (e. g. Kiva Robotics System)
Professional Organizations to Know
- American Production and Inventory Control Society (APICS)
- American Society for Quality (ASQ)
- Institute of Supply Chain Management (ISM)
- Association of Supply Chain Management Professionals (ASCM)
- International Warehouse Logistics Association (IWLA)
- National Association of Purchasing Management (NAPM)
- International Trade Administration (ITA)
- National Retail Federation (NRF)
- Council of Supply Chain Management Professionals (CSCMP)
- Material Handling Industry of America (MHIA)
We also have IT Controller, Cost Controller, and Quality Controller jobs reports.
Common Important Terms
- Inventory Planning. The process of determining the appropriate size and level of inventory to meet customer needs while minimizing total costs associated with the inventory.
- Stock Control. The process of managing the inventory to ensure that the right items are in the right place at the right time.
- Order Management. The process of managing customer orders, from receipt to delivery.
- Stock Level Management. The process of monitoring, measuring, and adjusting the amount of inventory in a warehouse.
- Reorder Point. The level of inventory at which it is necessary to reorder stock to maintain a certain level of inventory.
- Forecasting. The process of predicting future demand based on past and current trends.
- Bill of Materials (BOM). A list of all the components that go into making a product or service.
- Just-in-Time (JIT). A method of inventory management where items are only ordered when they are needed, eliminating excess inventory and reducing costs.
Frequently Asked Questions
Q1: What is an Inventory Controller? A1: An Inventory Controller is a person or system responsible for managing and tracking inventory levels, orders, and deliveries. They ensure that a company has the right amount of stock on hand to meet customer needs. Q2: What are the main responsibilities of an Inventory Controller? A2: The main responsibilities of an Inventory Controller include monitoring stock levels, ensuring that products are stored properly, processing orders, and coordinating deliveries. They also are responsible for overseeing inventory reports and budgeting. Q3: What qualifications are required to be an Inventory Controller? A3: To be an Inventory Controller, you need to have experience in the field, such as a degree in business management or logistics. Knowledge of inventory control software and warehouse management systems is also beneficial. Q4: What skills are necessary to be an effective Inventory Controller? A4: To be an effective Inventory Controller, you need to have excellent organizational skills, attention to detail, and strong communication skills. You also need to have strong analytical and problem-solving abilities to analyze data and make decisions regarding inventory levels. Q5: What type of technology do Inventory Controllers use? A5: Inventory Controllers use technology such as inventory management software, barcode scanners, RFID tags, and warehouse management systems to track and manage stock levels, orders, and deliveries.What are jobs related with Inventory Controller?
- Shipping Controller
- Logistics Controller
- Production Controller
- Configuration Controller
- Network Controller
- Data Controller
- Document Controller
Web Resources
- Inventory Control / Capitalization | Accounting Office accountingoffice.uconn.edu
- Inventory Control - InsideEWU inside.ewu.edu
- Inventory Control | The University of New Mexico inventory.unm.edu
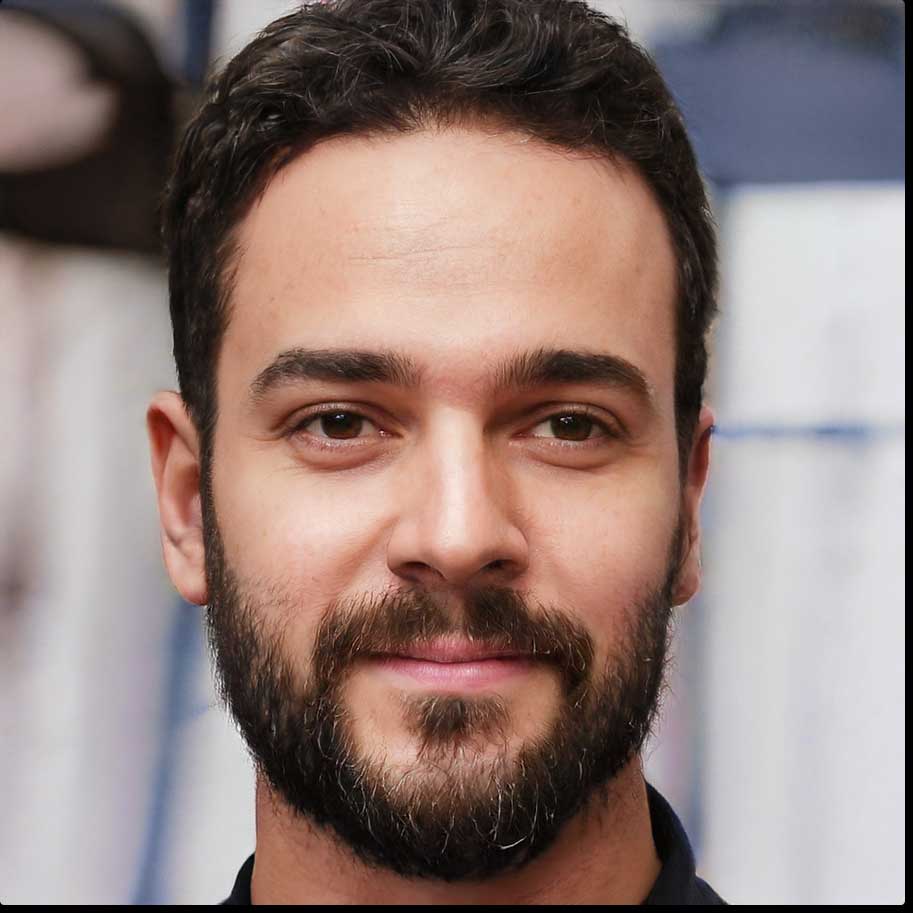