How to Be Plant Controller - Job Description, Skills, and Interview Questions
The Plant Controller is responsible for the financial planning and management of a manufacturing plant. This includes overseeing the budget, tracking expenses, and ensuring the financial accuracy of all operations. As a result, Plant Controllers play a critical role in the success of a manufacturing plant, as their decisions can directly influence the overall performance of the organization.
Poor management of finances can lead to a decrease in production, higher costs, and decreased profits. On the other hand, effective financial management can lead to increased efficiency, increased profits, and improved customer satisfaction.
Steps How to Become
- Obtain a bachelor's degree in accounting, finance, business administration, or a related field. Many employers prefer candidates with a master's degree in business administration (MBA) with a concentration in accounting or finance.
- Gain experience in accounting through internships or entry-level positions. Relevant experience could include cost accounting, financial analysis, budgeting, and forecasting.
- Seek out professional certifications to demonstrate expertise and credibility such as Certified Public Accountant (CPA), Certified Management Accountant (CMA) or Certified Internal Auditor (CIA).
- Develop strong communication skills to effectively explain financial results to plant management and other business partners.
- Develop an understanding of the plants industry, competitive landscape, and market position.
- Research the latest developments in plant controller roles and responsibilities to ensure a current understanding of best practices.
- Apply for open Plant Controller positions that match your experience and qualifications.
Staying ahead and competent as a Plant Controller requires constant effort and dedication. To stay ahead of the competition, one must focus on keeping up-to-date with changes in the industry, staying informed about the latest trends and technologies, and investing in professional development that can help refine skills and increase knowledge. it is important to remain organized, maintain accurate records and documents, and ensure compliance with relevant regulations.
Doing so will help ensure that the Plant Controller is prepared to handle any challenges that may arise. When these steps are taken, Plant Controllers can stay ahead and remain competent in their field.
You may want to check Inventory Controller, Configuration Controller, and Systems Controller for alternative.
Job Description
- Develop and maintain financial reporting systems to support the company's operations.
- Prepare monthly financial statements and reports for management.
- Analyze financial data to identify discrepancies and recommend corrective actions.
- Coordinate annual budget processes and related activities.
- Monitor and review cost accounting systems to ensure accuracy of financial data.
- Develop financial forecasts to assist in planning and decision-making.
- Implement internal controls to ensure compliance with regulations and corporate policies.
- Manage capital expenditure projects and ensure their successful completion.
- Analyze manufacturing costs and make recommendations to reduce expenses.
- Assist in the preparation of audited financial statements.
- Monitor inventory levels and reconcile with general ledger accounts.
- Evaluate inventory trends and develop strategies to reduce costs.
- Analyze data to determine plant performance and cost effectiveness.
- Provide guidance to plant personnel on financial matters.
- Work closely with other departments to ensure timely completion of tasks.
Skills and Competencies to Have
- Financial Analysis: Ability to analyze complex financial data, create financial models and generate meaningful insights.
- Strategic Planning: Ability to develop and implement long-term plans to support company objectives.
- Risk Management: Ability to identify, assess, and manage potential risks in order to protect the organization from financial losses.
- Cost Control: Ability to monitor and reduce costs while maintaining quality standards.
- Accounting: Knowledge of Generally Accepted Accounting Principles (GAAP) and financial reporting requirements.
- Budgeting: Ability to develop and manage budgets that align with organizational objectives.
- Auditing: Knowledge of auditing standards and procedures.
- Tax Compliance: Ability to maintain tax compliance and ensure accuracy of tax filings.
- Manufacturing Operations: Knowledge of manufacturing processes and operations management principles.
- Project Management: Knowledge of project management approaches and tools.
- Process Improvement: Ability to identify and implement process improvements that increase efficiency and productivity.
- Leadership: Ability to motivate and lead a team of financial professionals in achieving company objectives.
Having strong organizational skills is an essential attribute for a Plant Controller. A Plant Controller is responsible for overseeing the financial performance of a manufacturing plant and ensuring that it is in compliance with both internal and external regulations. This requires attention to detail and the ability to organize and analyze large amounts of data to make informed decisions.
Plant Controllers must be able to work with a variety of teams, such as the production team, supply chain team, and finance team. This requires strong communication and interpersonal skills to effectively collaborate with team members. Finally, Plant Controllers must be able to think strategically, looking at the big picture while still managing day-to-day operations.
This requires problem-solving skills and an understanding of the industry trends that can affect the plant's performance. With these skills, a Plant Controller can make a real difference in the success of the plant.
Compliance Controller, Document Controller, and Materials Controller are related jobs you may like.
Frequent Interview Questions
- How do you stay up-to-date on the most recent accounting regulations and best practices?
- Describe a time when you had to reconcile conflicting data.
- What strategies do you use to ensure accuracy in financial reporting?
- Have you ever successfully identified process improvements in a plants financial operations?
- How have you managed the budgeting process for a plant?
- What experience do you have working with different ERP systems?
- Describe how you have developed and implemented financial controls for a plant.
- How do you measure the success of financial operations in a plant?
- What do you think is the most important aspect of a plant controllers job?
- How have you used data analytics to improve cost savings or profitability in a plant?
Common Tools in Industry
- Microsoft Dynamics GP (formerly Great Plains). An enterprise resource planning (ERP) solution for managing financials, supply chain, operations, and analytics. (e. g. Automation of financial processes and real-time reporting).
- Microsoft Access. A database application used to store, manipulate, and report data. (e. g. Creation of custom reports and tracking of inventory).
- Microsoft Excel. A spreadsheet application used to analyze data and create charts and graphs. (e. g. Forecasting future costs and financial analysis).
- Budgeting Software. Software used to create, manage, and track budgets. (e. g. Automating budget cycles and tracking actual vs. budgeted spending).
- Business Intelligence Software. Software used to analyze business data and identify trends and opportunities. (e. g. Identifying areas of growth or inefficiencies in operations).
- Cost Control Software. Software used to identify cost savings opportunities and analyze current expenses. (e. g. Identifying areas for cost reduction or eliminating waste from operations).
Professional Organizations to Know
- Institute of Management Accountants (IMA)
- American Society for Training and Development (ASTD)
- Association for Financial Professionals (AFP)
- Financial Executives International (FEI)
- American Institute of CPAs (AICPA)
- National Association of Corporate Directors (NACD)
- Institute of Internal Auditors (IIA)
- Chartered Institute of Management Accountants (CIMA)
- Association for Corporate Treasurers (ACT)
- Strategic Finance Magazine
We also have Network Controller, Cost Controller, and IT Controller jobs reports.
Common Important Terms
- Cost Accounting. A branch of accounting that focuses on the collection and analysis of costs associated with the production of goods or services.
- Financial Reporting. The process of preparing and presenting financial statements that provide information about a companys financial performance, position, and cash flows.
- Budgeting. The process of creating a spending plan for a given period of time, typically an organizations fiscal year.
- Internal Controls. Policies and procedures implemented by organizations to protect their assets and ensure the accuracy and reliability of financial records.
- Regulatory Compliance. The process of ensuring that an organization is adhering to laws and regulations applicable to its operations.
- Risk Management. The process of identifying, assessing, and controlling risks related to the operations of an organization.
- Strategic Planning. The process of determining an organizations long-term goals and objectives and establishing a plan to achieve them.
Frequently Asked Questions
What is a Plant Controller?
A Plant Controller is a financial professional who is responsible for overseeing the financial operations of a manufacturing facility. They are responsible for developing and managing budgets, analyzing financial performance, as well as creating and implementing financial strategies.
What are some key responsibilities of a Plant Controller?
Key responsibilities of a Plant Controller include developing and managing annual budgets, analyzing financial performance, creating and implementing financial strategies, managing cash flow, monitoring inventory levels, and ensuring compliance with financial regulations.
What qualifications are necessary for a Plant Controller?
Qualifications for a Plant Controller typically include a bachelor's degree in accounting or finance, as well as 5+ years of experience in financial management. In addition, Plant Controllers should be knowledgeable in accounting principles, cost accounting, and financial analysis.
What skills do Plant Controllers need?
Plant Controllers should have strong analytical, organizational, problem-solving, and communication skills. They should also be highly proficient in the use of accounting software and other financial management tools.
What are the typical salary ranges for Plant Controllers?
Typical salary ranges for Plant Controllers vary based on experience and geographic location, but generally range from $85,000 to $115,000 per year.
What are jobs related with Plant Controller?
- Shipping Controller
- Logistics Controller
- Budget Controller
- Process Controller
- Data Controller
- Risk Controller
- Quality Controller
Web Resources
- Plant Accounting | Controller's Office controller.berkeley.edu
- Plant Funds and Equipment - Controller controller.tennessee.edu
- Controller's Office | USU www.usu.edu
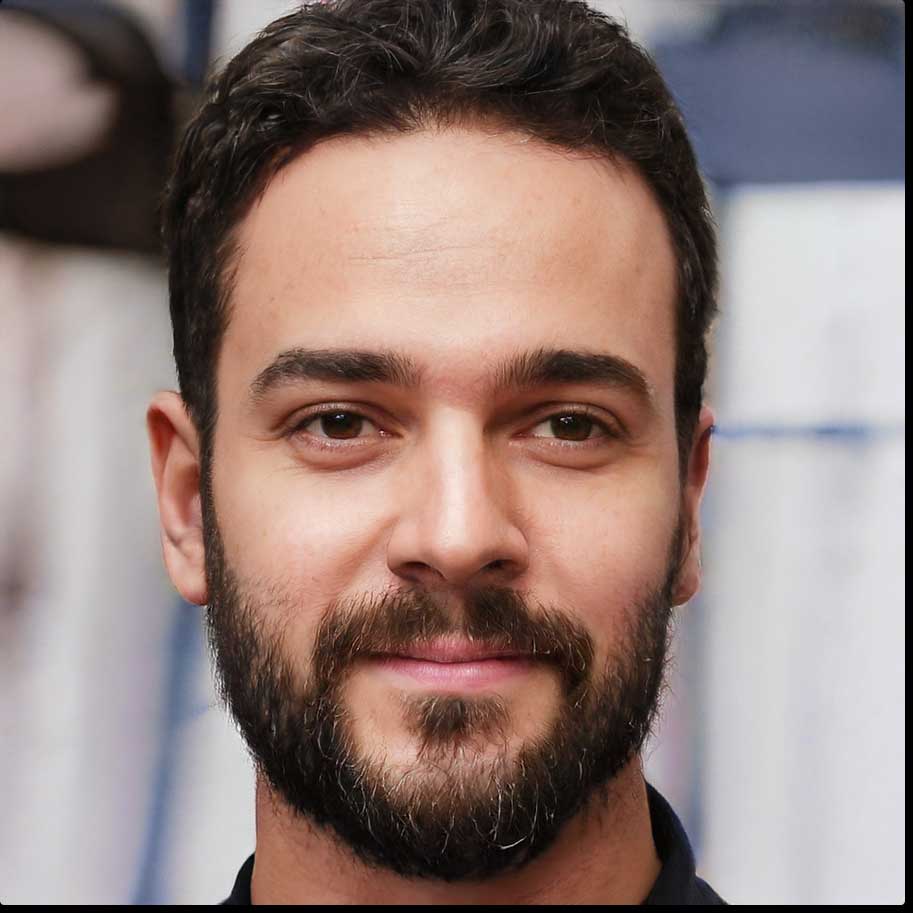