How to Be Process Operations Manager - Job Description, Skills, and Interview Questions
The increasing need for efficient process management has led to the emergence of Operations Managers. These professionals are responsible for overseeing the production of goods and services, as well as ensuring that operations are organized, efficient and cost-effective. By monitoring the overall process, they can identify bottlenecks or inefficiencies that can be addressed to improve performance.
In addition, they can also develop and implement new strategies to streamline processes, such as automation and data analysis, which can lead to improved productivity, cost savings and customer satisfaction. the role of Operations Manager plays an important part in keeping businesses running smoothly and achieving high levels of success.
Steps How to Become
- Obtain a Bachelor's Degree. Obtaining a bachelor's degree in a relevant field such as process engineering, operations management, or business administration is the first step toward becoming a process operations manager.
- Gain Relevant Work Experience. It is important to gain relevant work experience before applying for a position as a process operations manager. This type of experience could involve working in positions such as an engineer, technician, or other operations-related roles.
- Get Certified. Acquiring a professional certification in project management, process engineering, or operations management can be beneficial when applying for a process operations manager role.
- Obtain Advanced Education. Employers may prefer to hire process operations managers with a master's degree in business administration, operations management, or a related field.
- Develop Leadership Skills. A successful process operations manager will be able to lead and manage employees, so developing leadership skills is essential.
- Seek Employment. Process operations managers are in high demand, so the job market is fairly competitive. It is important to network and apply for multiple positions to increase your chances of landing a job.
The success of any organization depends heavily on the efficiency and effectiveness of its operations. An Operations Manager plays a key role in ensuring this success. They must be reliable and capable in order to effectively manage the day-to-day activities of an organization.
To be reliable, an Operations Manager must have a proven track record of successfully managing operations, making sure that each process is completed on-time and within budget. They must have strong communication skills in order to efficiently collaborate with other team members and ensure everyone is working towards the same goal. they must be capable of utilizing resources wisely and making decisions that are beneficial to the organization.
With these qualities, an Operations Manager can effectively and reliably manage the operations of an organization and help to ensure its success.
You may want to check Operations Project Manager, Field Operations Manager, and Operations Research Analyst for alternative.
Job Description
- Monitor and analyze process performance to identify opportunities for improvement.
- Develop and implement process improvement plans for production, quality, and cost optimization.
- Develop and maintain process control systems and standards.
- Analyze process data and provide feedback to operations staff on performance trends.
- Establish process controls and procedures to ensure product meets quality standards.
- Collaborate with other departments to ensure product meets customer expectations.
- Maintain and update process documentation, workflow diagrams, and training materials.
- Develop and manage process-related budgets.
- Monitor and evaluate process performance metrics, such as throughput, cycle time, and scrap rate.
- Monitor and troubleshoot process issues and recommend corrective action plans.
- Lead process improvement projects and teams to deliver specific objectives.
- Train and mentor operations staff on process improvement techniques and best practices.
- Ensure compliance with safety, environmental, and quality regulations.
- Manage external vendors and contractors to ensure timely delivery of services.
Skills and Competencies to Have
- Knowledge of process management principles and best practices
- Ability to develop and implement process and system improvements
- Excellent problem-solving and decision-making skills
- Proficient in project management software
- Ability to manage multiple tasks and prioritize workload
- Strong communication and interpersonal skills
- Outstanding organizational and time management skills
- Ability to develop process documentation and training materials
- Ability to analyze and interpret data
- Understanding of process analysis tools and techniques
The primary skill for a Process Operations Manager is the ability to analyze and improve processes. This requires having excellent problem-solving and problem-identification skills, as well as the ability to apply process improvement methods such as Lean and Six Sigma. it is important to have strong communication skills, as they need to be able to effectively communicate with both internal and external stakeholders and ensure that all processes are running smoothly.
Furthermore, they need to have a good understanding of the systems and technologies involved in the process, in order to be able to effectively identify and resolve any issues that arise. Finally, having the ability to think strategically and plan for the future can be essential for a successful process operations manager, as they need to be able to anticipate potential problems and develop strategies to address them. These skills are all essential for effective process improvement and operations management.
Operations Research Scientist, Regional Operations Manager, and Operations Consultant are related jobs you may like.
Frequent Interview Questions
- What experience do you have in process operations management?
- What techniques do you use to ensure high-quality processes?
- How do you motivate teams to follow process operations standards?
- How do you handle unexpected problems in a process operation?
- Describe a time when you led a successful process improvement project.
- How do you ensure that process operations are compliant with industry regulations?
- What strategies do you use to create efficient and cost-effective processes?
- How do you track and measure process performance?
- How do you ensure that process operations run smoothly?
- What strategies do you use to maintain high customer satisfaction levels?
Common Tools in Industry
- Process Mapping Tool. A tool that helps to map out the different steps involved in a process, for better understanding and organization of the process (eg: Visio).
- Automation Tools. Tools that help to automate processes, improving the speed and accuracy of operations (eg: UiPath).
- Data Analysis Tools. Tools that help to analyze data and make informed decisions (eg: Tableau).
- Risk Management Tools. Tools that help to identify and manage risks (eg: Risk Register).
- Project Management Tools. Tools that help to manage projects, tasks and activities (eg: Trello).
- Quality Management Tools. Tools that help to ensure quality standards are met (eg: ISO 9001).
- Collaboration Tools. Tools that help teams collaborate and communicate effectively (eg: Slack).
Professional Organizations to Know
- Institute of Industrial and Systems Engineers (IISE)
- Project Management Institute (PMI)
- American Production and Inventory Control Society (APICS)
- Association for Operations Management (APOM)
- American Society for Quality (ASQ)
- International Society of Logistics (SOLE)
- Manufacturing Skill Standards Council (MSSC)
- Society for Manufacturing Engineers (SME)
- Operational Research Society (ORS)
- International Institute of Business Analysis (IIBA)
We also have Operations Coordinator, Global Operations Manager, and Operations Supervisor jobs reports.
Common Important Terms
- Process Improvement. A continuous effort to optimize processes and systems for better performance and efficiency.
- Process Modeling. The process of creating an abstract representation of a process or system in order to analyze it and make improvements.
- Business Process Management (BPM). A systematic approach to improving an organizations processes and operations by using advanced technologies and methodologies.
- Process Mapping. A graphical representation of a process that illustrates the sequence of tasks, interactions, and decisions involved.
- Process Automation. The process of automating business processes with the help of software applications.
- Quality Assurance. The practice of ensuring that products or services meet certain standards of quality.
- Risk Management. A set of techniques used to identify, assess, and manage potential risks in a given situation.
- Lean Manufacturing. A production system aimed at reducing costs and increasing efficiency through waste elimination.
- Six Sigma. A business strategy focused on improving the quality of processes by reducing defects to a near-zero level.
Frequently Asked Questions
What is a Process Operations Manager?
A Process Operations Manager is responsible for overseeing the day-to-day operations of an organization's processes, ensuring that they are efficient, effective and in compliance with applicable regulations.
What duties are included in the role of a Process Operations Manager?
The duties of a Process Operations Manager include developing and implementing process improvement plans, monitoring performance metrics, identifying areas of improvement, resolving process discrepancies, and coordinating with other departments to ensure successful implementation of plans.
What qualifications are required for a Process Operations Manager?
Qualifications for a Process Operations Manager typically include a bachelor's degree in business, industrial engineering or a related field, as well as several years of experience in process management and/or operations.
What are the benefits of having a Process Operations Manager?
The benefits of having a Process Operations Manager include improved efficiency, reduced costs, increased customer satisfaction, improved quality control and better compliance with regulations.
What is the average salary of a Process Operations Manager?
According to data from PayScale, the average salary of a Process Operations Manager ranges from $53,000 to $112,000 per year.
What are jobs related with Process Operations Manager?
- IT Operations Manager
- Operations Support Specialist
- Aviation Operations Manager
- Operations Engineer
- Manufacturing Operations Manager
- Operations Director
- Network Operations Manager
- Logistics Operations Manager
- Operations Research Manager
- Supply Chain Operations Manager
Web Resources
- What Does a Operations Manager Do? - Western Governors ¦ www.wgu.edu
- Operations Manager Job Description, Qualifications and Salary tsa.edu.au
- Introduction to operations management: 2 The inputprocess www.open.edu
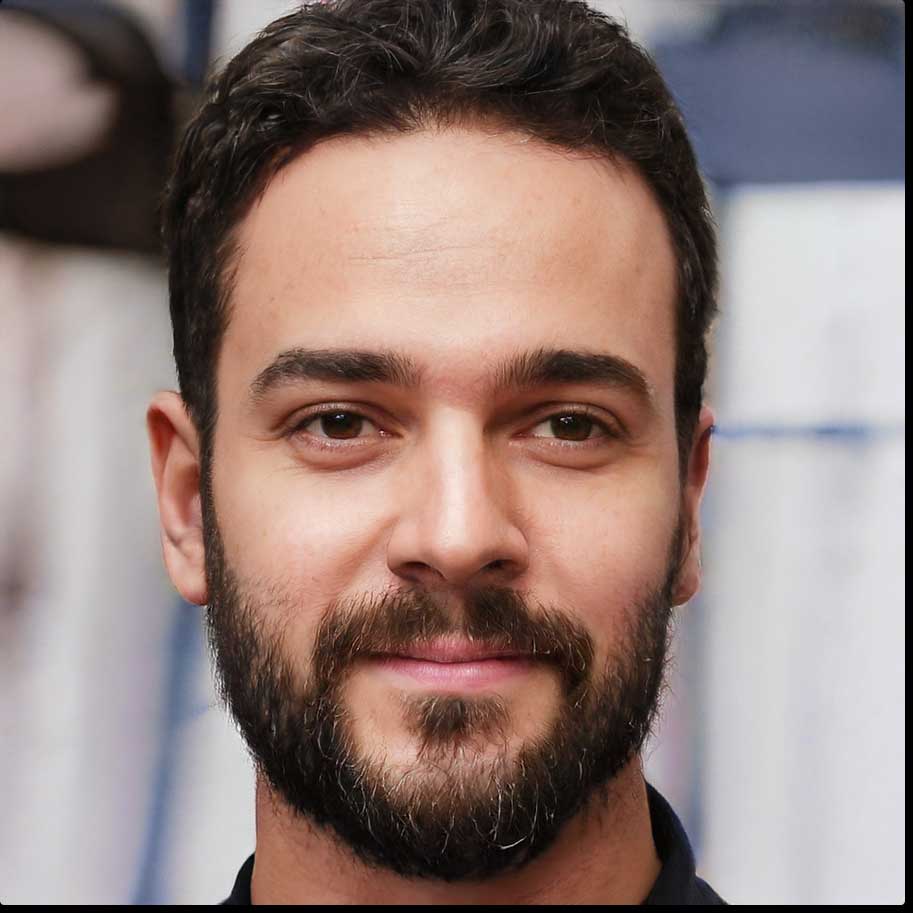