How to Be Logistics Operations Manager - Job Description, Skills, and Interview Questions
Logistics operations managers play an important role in the efficiency and success of any company. Their responsibilities include managing resources, allocating budgets, supervising personnel, and ensuring compliance with safety and industry regulations. As a result, they can ensure that business operations are running smoothly and efficiently, leading to increased productivity and reduced costs.
their strong communication, problem-solving, and organizational skills can help to foster better relationships with customers, suppliers, and other stakeholders. the presence of an experienced logistics operations manager can have a positive effect on the bottom line of any organization.
Steps How to Become
- Earn a Bachelor's Degree. The minimum educational requirement for a logistics operations manager position is typically a bachelor's degree. Employers may prefer candidates with a degree in logistics, supply chain management, business administration, economics, or a related field.
- Gain Relevant Work Experience. Many employers require at least several years of experience in the logistics field, such as working as a logistics coordinator or in a similar role. Additionally, gaining experience in related fields, such as customer service or inventory management, can be beneficial.
- Pursue Certification. Certification is not always required to become a logistics operations manager, but it may give you an edge over other candidates and demonstrate your commitment to the profession. The Council of Supply Chain Management Professionals (CSCMP) and the American Production and Inventory Control Society (APICS) both offer certification programs for logistics professionals.
- Develop Strong Analytical Skills. Because logistics operations managers are responsible for problem solving and making decisions, strong analytical and critical thinking skills are essential. Consider taking courses or workshops to develop these skills.
- Obtain Management Skills. Because logistics operations managers oversee teams of employees, strong leadership and management skills are essential. Courses in management and interpersonal communication can be beneficial. Additionally, taking on supervisory roles at work can provide invaluable experience.
Logistics Operations Managers must be reliable and competent to ensure a successful business operation. To become a reliable and competent Logistics Operations Manager, one must possess strong organization and problem-solving skills, excellent communication abilities, and the capacity to develop and maintain professional relationships with employees, vendors, customers, and other stakeholders. Furthermore, they must be able to plan and implement effective strategies for inventory control, transportation, warehousing, and distribution of goods.
having an understanding of relevant laws and regulations is essential in order to ensure compliance. Finally, staying up-to-date on the latest industry trends and best practices will help the Logistics Operations Manager excel in their role. By developing these skills and qualities, a Logistics Operations Manager can become reliable and competent.
You may want to check Operations Project Manager, Operations Research Analyst, and Operations Consultant for alternative.
Job Description
- Develop and implement logistics operations strategies, policies and procedures.
- Research, analyze and evaluate logistics operations data for optimal performance.
- Manage and monitor the daily operations of the logistics department.
- Develop and manage logistics budgets to ensure cost effectiveness.
- Negotiate contracts and rates with suppliers, vendors and carriers.
- Develop and maintain relationships with strategic partners and customers.
- Supervise the selection, training and performance of logistics staff.
- Monitor and track the progress of shipments, ensuring timely delivery.
- Troubleshoot and resolve supply chain issues in a timely manner.
- Collaborate with other departments to ensure a timely and cost effective supply chain process.
- Ensure compliance with domestic and international regulations and standards.
- Monitor trends in the logistics industry and identify areas for improvement.
- Develop reports to track and measure performance metrics.
Skills and Competencies to Have
- Leadership Skills
- Strategic Planning
- Problem Solving
- Communication Skills
- Project Management
- Budgeting and Cost Control
- Process Improvement
- Logistics and Supply Chain Management
- Inventory Management
- Risk Management
- Data Analysis
- Warehouse Management
- Transportation Management
- Quality Assurance
- Negotiation Skills
- Regulatory Compliance
- Technology Proficiency
- People Management
Logistics operations manager is a key role in any organization, as it requires a variety of skills to effectively oversee the supply chain process. The most important skill for a successful logistics operations manager is the ability to plan and coordinate activities across multiple departments. This means having the ability to identify areas of inefficiency, develop solutions to address them, and manage the execution of those solutions.
strong problem-solving skills are essential, as logistics operations managers must be able to identify and resolve any issues that arise during the course of their work. Furthermore, they must possess excellent communication skills in order to effectively collaborate with other departments and ensure that tasks are completed on time. Finally, having an understanding of digital technologies such as artificial intelligence and automation can help logistics operations managers stay ahead of the curve and keep the supply chain running smoothly.
With all these skills in place, a logistics operations manager can ensure the efficient and effective running of an organization's supply chain.
Operations Clerk, Operations Research Manager, and Network Operations Manager are related jobs you may like.
Frequent Interview Questions
- How would you define logistics operations management?
- What experience do you have in managing logistics operations?
- Can you provide an example of a successful logistics operation you have managed?
- How do you approach problem-solving in regards to logistics operations?
- What strategies do you use to ensure the efficient utilization of resources?
- How do you stay up to date on the latest developments and trends in logistics operations?
- How do you manage teams to meet tight deadlines and achieve results?
- How do you handle conflicts with clients or customers in regards to logistics operations?
- What methods do you use to ensure customer satisfaction in regards to timely delivery of goods and services?
- How do you motivate your team to remain productive and efficient in a highly competitive environment?
Common Tools in Industry
- Transportation Management Systems (TMS). Automated software system that helps companies manage their freight shipping, from scheduling to cost optimization. (Example: Cerasis TMS)
- Warehouse Management System (WMS). Software system that helps companies manage their warehouse operations, from inventory control to order management. (Example: HighJump WMS)
- Supply Chain Management Software (SCM). Software system that helps companies manage their supply chain operations, from inventory to order fulfillment. (Example: SAP SCM)
- Business Intelligence (BI). Software system that helps companies analyze their data and make better decisions. (Example: Tableau BI)
- Order Management System (OMS). Software system that helps companies manage their orders, from order entry to order fulfillment. (Example: Oracle OMS)
- Logistics Management Software (LMS). Software system that helps companies manage their logistics operations, from shipping to tracking. (Example: Descartes LMS)
- Fleet Management System (FMS). Software system that helps companies manage their fleets, from vehicle maintenance to driver safety. (Example: TomTom FMS)
Professional Organizations to Know
- American Supply Chain and Logistics Association
- Council of Supply Chain Management Professionals
- Institute for Supply Management
- International Warehouse Logistics Association
- International Society of Logistics
- Material Handling Industry of America
- National Council of Chain Restaurants
- National Industrial Transportation League
- International Air Transport Association
- Transportation Intermediaries Association
We also have Manufacturing Operations Manager, Aviation Operations Manager, and Process Operations Manager jobs reports.
Common Important Terms
- Logistics. The process of planning, implementing, and controlling the efficient, effective flow of goods, services, and related information from point of origin to point of consumption for the purpose of satisfying customer requirements.
- Supply Chain. A network of organizations, people, activities, information, and resources involved in moving a product or service from supplier to customer.
- Warehousing. The process of storing, organizing, and managing materials and products within a facility.
- Inventory Management. The process of tracking and controlling the ordering, shipping, receiving, and storage of materials and products within an organization.
- Transportation Management. The process of planning, implementing, and controlling the efficient movement of goods from point of origin to point of consumption.
- Fleet Management. The process of managing a vehicle fleet, including maintenance, safety, routing, and performance monitoring.
- Procurement. The process of acquiring goods or services from an outside supplier at the best possible price with the appropriate quality and quantity.
- Logistics Network Design. The process of designing an efficient and cost-effective logistics network that meets customer service requirements.
Frequently Asked Questions
Q1: What is a Logistics Operations Manager? A1: A Logistics Operations Manager is responsible for managing the supply chain process and ensuring the efficient flow of goods from point of origin to point of consumption. This includes overseeing the procurement, storage and distribution of materials and products. Q2: What skills are needed to be successful as a Logistics Operations Manager? A2: A Logistics Operations Manager should have strong organizational, problem solving and communication skills, as well as a thorough understanding of supply chain processes and logistics operations. They should also be able to effectively manage personnel, meeting deadlines, budgets and customer requirements. Q3: What are the primary responsibilities of a Logistics Operations Manager? A3: The primary responsibilities of a Logistics Operations Manager include planning and coordinating the supply chain process; managing the procurement, storage and distribution of materials and products; optimizing logistics operations; and collaborating with stakeholders such as suppliers, customers and other departments. Q4: How many employees does a Logistics Operations Manager typically manage? A4: The number of employees a Logistics Operations Manager typically manages will depend on the size and scope of the organization they work for. However, they may be responsible for managing teams of up to 10-15 people. Q5: What is the best way to measure the success of a Logistics Operation Manager? A5: The success of a Logistics Operations Manager can be measured by their ability to successfully manage the supply chain process, optimize logistics operations, meet customer requirements and deadlines, manage personnel effectively, and adhere to budgets.What are jobs related with Logistics Operations Manager?
- Supply Chain Operations Manager
- Operations Support Specialist
- Global Operations Manager
- Operations Coordinator
- Field Operations Manager
- Operations Director
- IT Operations Manager
- Operations Research Scientist
- Operations Supervisor
- Operations Engineer
Web Resources
- Logistics Operations Management - Spoon River College www.src.edu
- Logistics Operations Management | SRC.edu www.src.edu
- Logistics and Operations Management Certificate - Penn State York www.york.psu.edu
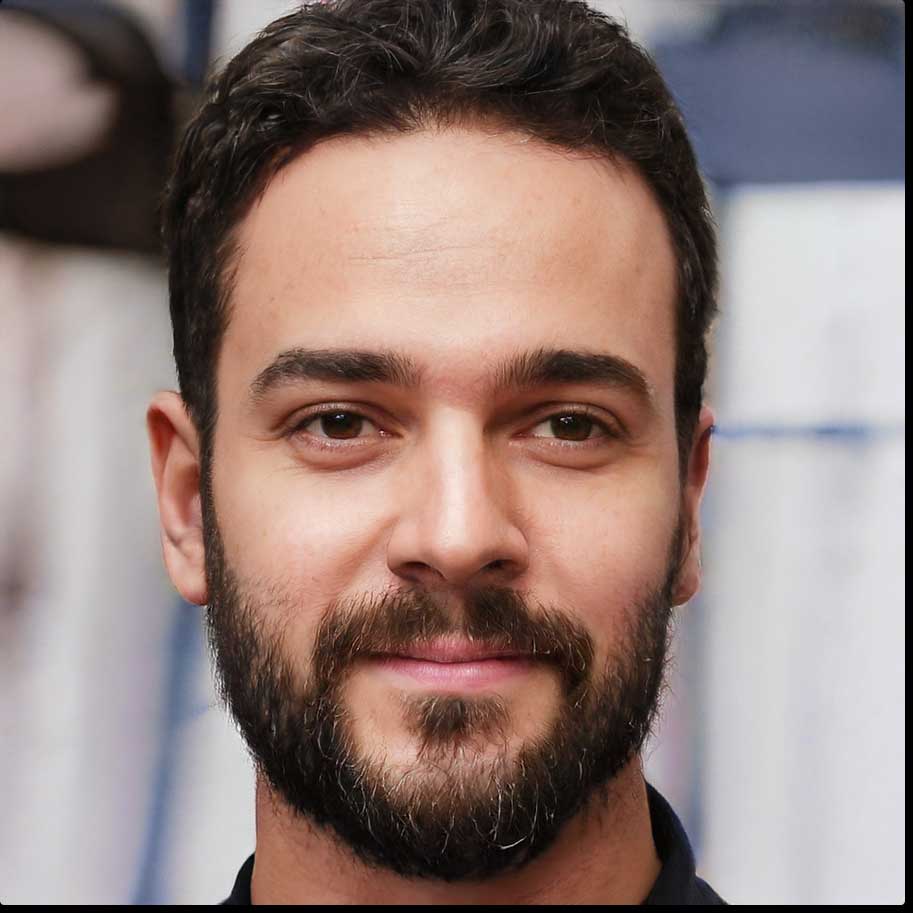