How to Be Tooling Engineer - Job Description, Skills, and Interview Questions
Tooling Engineers play an important role in the manufacturing process by developing, designing, and creating tools and machines used to create parts and products. Their work impacts the efficiency of the production process, as well as the quality of the finished product. Poorly designed tooling can lead to longer production times, higher costs, and defective products.
On the other hand, proper tooling design can lead to shorter production runs, reduction in downtime, and improved quality control. Tooling Engineers are essential for ensuring that a company's products are made in an efficient and cost-effective manner.
Steps How to Become
- Obtain a bachelor's degree in engineering or a related field. Tooling engineers typically need a minimum of a bachelor's degree in engineering, although many employers prefer candidates with a master's degree. Programs might include classes in mathematics, physics and engineering principles.
- Pursue an internship. Internships are a great way to gain experience and learn more about the profession. Internships are often the best way to gain experience in the field, as well as to network with potential employers.
- Take additional classes or certification programs to become certified in tool engineering. Certification programs can be found through professional engineering associations and organizations, including the American Society of Tooling Engineers (ASTE).
- Research tooling technology and keep up with industry trends. Tooling engineers need to be knowledgeable about the latest technology and be able to identify and solve problems quickly.
- Obtain a job as a tooling engineer. Many tooling engineers work in manufacturing or research and development departments of larger companies. They may also teach at universities or work for consulting firms.
- Maintain professional certification. Tooling engineers may need to renew their certification every few years. This may involve additional courses or taking tests to demonstrate their knowledge of the field.
To stay ahead and competent as a Tooling Engineer, it is important to stay up-to-date with the latest advancements in tooling technology, as well as trends related to the industry. This can be achieved through continuing education and research, attending seminars, and networking with other professionals in the field. staying organized and on top of current projects is essential for success.
Regularly taking part in conversations within the engineering community and reading industry related blogs can help to keep an engineer well informed and ahead of the curve. Having a solid grasp of the fundamentals of tooling engineering, such as metalworking, machining, and robotics, is also critical in order to remain competent.
You may want to check Bioengineering/Biomedical Engineering Technicians, Process Engineer, and Reliability Engineer for alternative.
Job Description
- Develop, integrate and maintain CNC machining processes
- Analyze and improve machine tool process performance
- Design and improve tooling systems for CNC machining operations
- Troubleshoot and resolve tooling and machine-related issues
- Create, maintain, and update process documentation
- Communicate with production personnel to ensure accuracy and efficiency
- Research and recommend new tooling technologies to improve productivity
- Obtain quotes from suppliers for new tooling and fixtures
- Monitor inventory of tooling and supplies and order as needed
- Assist in developing preventive maintenance plans for machining tools
Skills and Competencies to Have
- Strong understanding of tooling principles and design
- Ability to develop tooling concepts, designs, and engineering drawings
- Knowledge of cutting tool materials, coatings, and manufacturing processes
- Experience with production engineering processes and practices
- Familiarity with Computer Aided Design (CAD) software
- Excellent problem-solving, troubleshooting, and analytical skills
- Ability to select and specify tooling components
- Ability to work with suppliers and vendors to coordinate tooling purchases
- Ability to develop and maintain tooling standards
- Knowledge of quality control systems and processes
- Understanding of safety regulations and industry standard practices
- Good communication skills, both verbal and written
Tooling engineers are essential for the successful operation of manufacturing plants. Their expertise in designing, creating, and maintaining tooling systems is essential for the efficient and cost-effective production of quality parts and components. Tooling engineers must possess a broad range of technical skills to be successful, but the most important skill is the ability to think critically and solve problems.
A tooling engineer needs to have strong analytical and problem solving skills to be able to identify and resolve any issues that may arise during the design or implementation of a tooling system. They must also think creatively to develop innovative solutions to improve the performance and efficiency of a system. tooling engineers must be knowledgeable in the latest technologies, materials, and processes used in tooling systems.
Having this knowledge helps them make informed decisions when selecting the best tools, components, and materials for a project. Finally, successful tooling engineers must be good communicators in order to collaborate with other engineers, customers, and suppliers.
Marine Engineers and Naval Architects, Drafter/CAD Engineer, and Automotive Engineer are related jobs you may like.
Frequent Interview Questions
- What experience do you have in tooling engineering?
- What challenges have you faced in tooling engineering?
- Describe your experience with CNC machining and tooling.
- How do you ensure the accuracy of molds, dies, and other custom tools?
- How do you ensure the quality of finished products?
- What strategies do you use to reduce costs associated with tooling engineering?
- Describe your experience working with rapid prototyping methods and technologies.
- What CAD/CAM software have you worked with in the past?
- What processes have you implemented to ensure the safety of tooling materials and equipment?
- How have you used simulation software to optimize tooling performance?
Common Tools in Industry
- Power Tools. These are tools powered by electricity, compressed air, or a battery, such as drills, saws, and sanders. (eg: electric drill)
- Hand Tools. These are tools that require physical labor, such as hammers, wrenches, and screwdrivers. (eg: hammer)
- Measuring Tools. These tools measure and layout workpieces, such as rulers, calipers, and micrometers. (eg: protractor)
- Cutting Tools. These tools are used to cut materials, such as knives, shears, and saws. (eg: hacksaw)
- Boring Tools. These tools create or enlarge holes in materials, such as drills and taps. (eg: drill bit)
- Forming Tools. These tools shape or form materials, such as dies and punches. (eg: die)
- Finishing Tools. These tools polish or finish surfaces, such as files, sandpaper, and buffers. (eg: sandpaper)
Professional Organizations to Know
- American Society of Mechanical Engineers (ASME)
- Society of Automotive Engineers (SAE)
- International Society of Automation (ISA)
- Institute of Industrial and Systems Engineers (IISE)
- American Welding Society (AWS)
- Tooling and Manufacturing Association (TMA)
- National Tooling and Machining Association (NTMA)
- Society of Manufacturing Engineers (SME)
- National Institute of Metalworking Skills (NIMS)
- International Manufacturing Technology Show (IMTS)
We also have Telecommunications Engineer, Aerospace Engineers, and Safety Engineer jobs reports.
Common Important Terms
- Tool Design. The process of designing, constructing, and maintaining tools used in manufacturing processes.
- CNC Machining. Computer numerical control (CNC) machining is a process in which a machine is programmed to perform a specific set of tasks.
- CAD/CAM. Computer-aided design (CAD) and computer-aided manufacturing (CAM) are computer-based tools used to design and manufacture products.
- GD&T. Geometric dimensioning and tolerancing (GD&T) is a system used to specify the size and location of parts in a design.
- Fixture Design. Fixture design is the process of creating a device that can securely hold a workpiece in place for machining, welding, or assembly operations.
- Process Planning. Process planning is the planning and development of the sequence of operations and processes required to produce a given product.
- Reverse Engineering. Reverse engineering is the process of analyzing an object to understand its design, technology, or structure.
- Quality Control. Quality control is the process of ensuring that products meet specific quality standards before they are sold or released to consumers.
Frequently Asked Questions
What is a Tooling Engineer?
A Tooling Engineer is a professional who designs, develops, and maintains tools and equipment used in the manufacturing process. They are responsible for ensuring that the tools are efficient, reliable, and cost-effective for their intended purpose.
What skills do Tooling Engineers need?
Tooling Engineers need to have a strong understanding of design principles, materials science, manufacturing processes, and computer-aided design (CAD). They must also have excellent problem-solving skills, attention to detail, and the ability to work with a variety of stakeholders.
What type of job opportunities are available for Tooling Engineers?
Tooling Engineers can find jobs in a variety of industries, including automotive, aerospace, medical device manufacturing, and consumer goods. Job titles can include Design Engineer, Manufacturing Engineer, Quality Engineer, Project Engineer, and more.
What is the average salary of a Tooling Engineer?
The average salary of a Tooling Engineer varies depending on experience, location, industry, and other factors. According to Glassdoor, the average salary for a Tooling Engineer in the United States is $76,844 per year.
What is the job outlook for Tooling Engineers?
The job outlook for Tooling Engineers is positive. The Bureau of Labor Statistics estimates that employment of industrial engineers, which includes Tooling Engineers, will grow 6 percent from 2019 to 2029. This growth is expected to be driven largely by increased demand for automation and better efficiency in manufacturing processes.
What are jobs related with Tooling Engineer?
- CAD/CAM/CAE Engineer
- Applications Engineer
- Chemical Engineer
- Marine Engineer
- DevOps Engineer
- Nuclear Engineer
- Environmental Engineer
- Maintenance Engineer
- Structural Engineer
- Software Engineer
Web Resources
- Tooling Engineer Career Services | Nebraska careers.unl.edu
- What is Tool Engineering? - Courses, Colleges, Scope leverageedu.com
- Tooling Engineer Career and Advising Center North Dakota career-advising.ndsu.edu
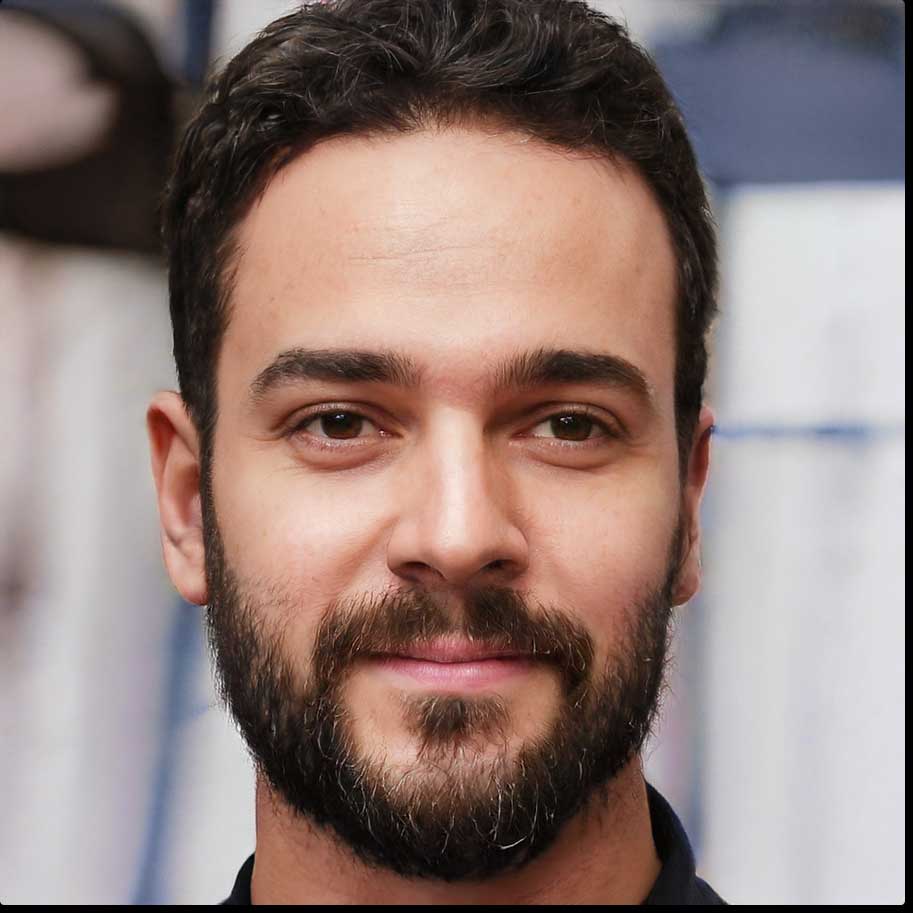