How to Be Sheet Metal Worker - Job Description, Skills, and Interview Questions
Sheet metal workers are skilled craftsmen who design, cut, form, and assemble metal products from sheet metal. This occupation requires a combination of both physical and technical skills to create a variety of products from HVAC systems to metal signs. The use of specialized tools such as shears, brakes, presses, and punch presses are essential to perform the job.
Sheet metal workers must also understand complex drawings, specifications, and schematics, as well as possess a high degree of precision and attention to detail. As a result of their expertise, sheet metal workers are able to craft sturdy and long-lasting products that are both aesthetically pleasing and safe for public use. Furthermore, due to the increased demand for metal products in the construction industry, sheet metal workers are expected to see job growth in the coming years.
Steps How to Become
- Obtain a high school diploma or GED. Sheet metal workers typically need at least a high school diploma or its equivalent.
- Consider enrolling in an apprenticeship. Apprenticeships are a great way to gain the skills and experience needed to become a sheet metal worker. Apprenticeships are available through trade unions, technical schools, and employers.
- Take a course in welding. Welding is an important skill for sheet metal workers. It is helpful to take a course in welding or to get on-the-job training in welding.
- Obtain necessary certifications. Sheet metal workers may need to obtain certifications in order to work in certain jurisdictions. These certifications may be obtained through trade unions or technical schools.
- Get on-the-job experience. It is important to gain experience in the field in order to become a successful sheet metal worker. Working with experienced sheet metal workers is a great way to learn the trade.
The sheet metal worker must stay ahead in order to remain qualified in their field. This means continuously updating their skillset, staying informed of the latest industry trends, and learning new ways of working with different materials. having a good work ethic, a positive attitude and an organized approach to their work can help them stay ahead and remain qualified.
Investing in tools and equipment to make their job easier is also important, as is participating in professional development courses to hone their skills. Finally, networking and building relationships with other professionals in the industry can open up opportunities and provide an additional source of knowledge and insight. By staying ahead and investing in their development, the sheet metal worker will be able to remain qualified and enjoy a successful career.
You may want to check Swimming Pool Technician, Boiler Operator, and Refrigeration Technician for alternative.
Job Description
- Read blueprints and drawings to determine the specific structural requirements of a project.
- Measure and mark dimensions and reference lines on material, according to drawings.
- Cut, bend and shape sheet metal components to build structures and products.
- Use hand tools such as shears, tin snips, hammers and punches to cut sheet metal.
- Assemble sheet metal parts using bolts, screws, rivets, soldering or welding equipment.
- Install sheet metal assemblies on walls and roofs using clamps, hinges, screws and bolts.
- Inspect completed work for conformance to specifications and quality standards.
- Perform basic maintenance on tools and equipment used in the course of work.
- Utilize computer-aided design (CAD) software for fabrication tasks.
- Suggest design modifications to reduce cost and improve efficiency.
Skills and Competencies to Have
- Familiarity with sheet metal tools and machinery
- Knowledge of sheet metal forming processes
- Ability to read and interpret technical drawings
- Ability to use layout tools such as rulers, calipers, and protractors
- Ability to accurately measure and mark sheet metal
- Understanding of proper safety procedures in the use of tools and machines
- Ability to set up and operate machines such as shears, punches, brakes, and presses
- Ability to form sheet metal into complex shapes using hand tools
- Knowledge of welding techniques
- Ability to work with a variety of metals, including aluminum, steel, and stainless steel
Being a successful sheet metal worker requires a combination of technical and practical skills. One of the most important skills is the ability to read and interpret technical drawings. This allows the metal worker to accurately follow the instructions and create a product that meets the specified requirements.
Another important skill is the ability to use tools such as saws, drills, grinders, and presses to shape and form the metal. Knowing how to use welding equipment is also essential, as it allows welds to be made in a safe and efficient manner. Finally, the sheet metal worker must possess good problem-solving skills in order to identify, troubleshoot and resolve any issues that arise.
Having these skills gives a sheet metal worker the knowledge and experience needed to produce quality products that meet customer specifications.
Septic System Installer, Heating Technicians, and Industrial Pipefitter are related jobs you may like.
Frequent Interview Questions
- What experience do you have in sheet metal fabrication?
- Are you familiar with the equipment and tools used in sheet metal fabrication?
- Describe a project that you have completed involving sheet metal fabrication.
- What safety protocols do you follow when working with sheet metal?
- How do you troubleshoot problems that arise with sheet metal fabrication?
- How do you ensure that the finished product meets customer specifications?
- What techniques do you use to ensure accuracy when working with sheet metal?
- How do you stay up to date on new technologies and methods in sheet metal fabrication?
- Do you have experience working with CNC machines for sheet metal fabrication?
- How do you prioritize tasks when working on multiple sheet metal projects?
Common Tools in Industry
- Tin snips. Used to cut sheet metals into smaller pieces. (eg: cutting a sheet of aluminum into a spare part).
- Spot welder. Used to weld two pieces of metal together. (eg: joining two pieces of steel to make a frame).
- Sheet metal shears. Used to cut sheet metals into specific shapes. (eg: cutting a circular shape from a sheet of aluminum).
- Cleco pliers. Used to temporarily clamp two sheets of metal together. (eg: holding two sheets together while welding).
- Hammer and dolly. Used to shape and form sheet metals. (eg: hammering a dented area in a sheet of aluminum to make it smooth).
- Power drill. Used to make holes in sheet metals. (eg: drilling mounting holes in a sheet of aluminum).
- MIG welder. Used to permanently weld two pieces of metal together. (eg: joining two pieces of steel together to make a frame).
- Hand files. Used to smooth and refine edges of sheet metals. (eg: filing the edges of a sheet of aluminum to make it smooth).
Professional Organizations to Know
- Sheet Metal and Air Conditioning Contractors National Association (SMACNA)
- National Association of Sheet Metal Workers International Association (SMWIA)
- Sheet Metal Workers Local Union
- American Welding Society (AWS)
- National Fire Protection Association (NFPA)
- American Society of Mechanical Engineers (ASME)
- International Association of Sheet Metal, Air, Rail, and Transportation Workers (SMART)
- American Society for Quality (ASQ)
- International Brotherhood of Boilermakers (IBB)
- The American Institute of Architects (AIA)
We also have Solar Thermal Installer, Solar Hot Water Installer, and Gas Line Installer jobs reports.
Common Important Terms
- Sheet Metal. Sheet metal is a type of metal that is formed into thin, flat sheets. It can be used in a variety of applications, such as automotive parts, roofing, or even aircraft structures.
- Sheet Metal Fabrication. The process of cutting, bending, and forming sheet metal into specific shapes and products.
- Metal Working. The process of manipulating metal to create objects and structures. This includes processes such as cutting, forming, welding, and machining.
- Welding. The process of joining two or more pieces of metal by applying heat to the pieces and using a filler material to form a bond between them.
- Machining. The process of cutting, drilling, grinding, and other operations performed on metal objects to create parts with specific shapes and sizes.
- Forming. The process of shaping metal by bending, stretching, or compressing it. This can be done by hand or through the use of specialized machinery.
- Cutting. The process of removing material from metal by using a tool such as a saw, drill, or grinder.
- Layout. The process of marking out and measuring the dimensions of a piece before it is cut or formed.
Frequently Asked Questions
What is Sheet Metal Working?
Sheet metal working is the process of forming and fabricating sheet metal into components and parts for a wide range of industries and applications, such as automotive, construction, medical, aerospace, and computer components.
What materials are used in Sheet Metal Working?
Common materials used in sheet metal working include stainless steel, aluminum, copper, brass, and galvanized steel.
What tools are used in Sheet Metal Working?
Tools used in sheet metal working include shears, brakes, punches, press brakes, rollers, and bending machines.
What processes are involved in Sheet Metal Working?
Processes involved in sheet metal working include cutting, forming, bending, welding, drilling, and finishing.
What are the benefits of Sheet Metal Working?
Benefits of sheet metal working include the ability to create complex parts with precision and accuracy, increased speed of production, and cost-effectiveness.
What are jobs related with Sheet Metal Worker?
- Irrigation Technician
- Gasfitters
- Pipe Welder
- Fire Sprinkler Fitter
- Boiler Installer
- Gas Plumber
- Hydronic Technician
- Facility Maintenance Technician
- Underground Pipelayer
- Sprinkler Technician
Web Resources
- Sheet Metal Worker - The Apprentice School www.as.edu
- Tri-C Sheet Metal Worker Certificate: Cleveland www.tri-c.edu
- Sheet Metal Worker - Human Resources www.etsu.edu
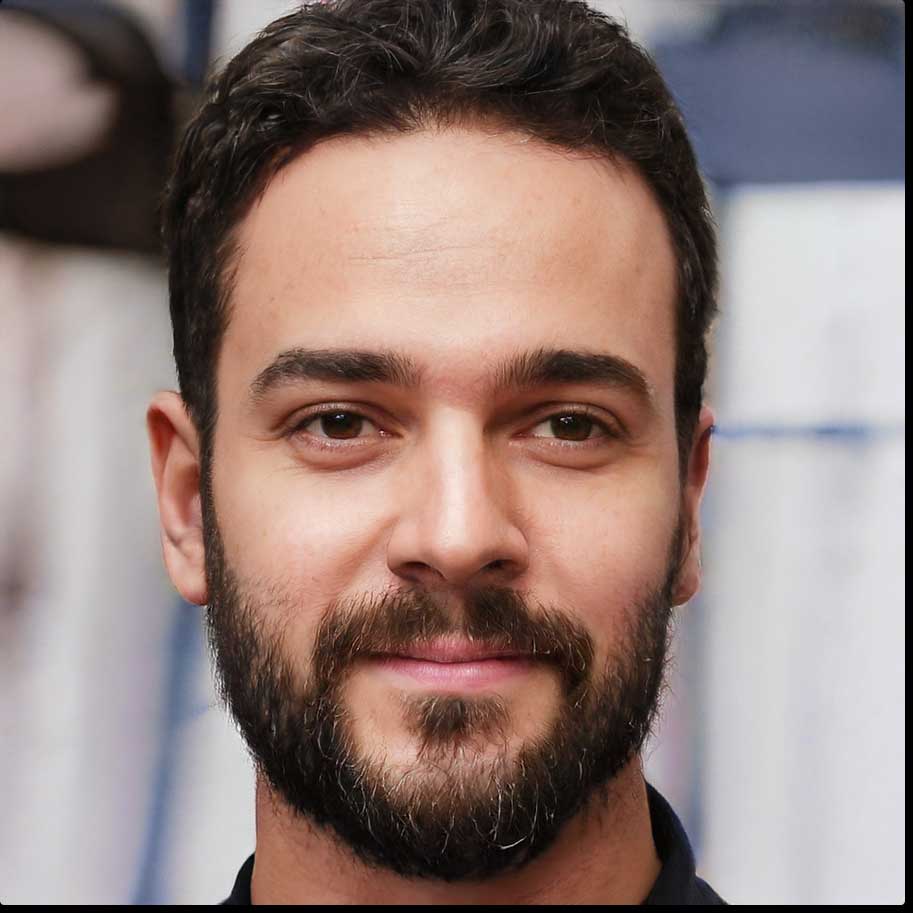