How to Be Facility Maintenance Technician - Job Description, Skills, and Interview Questions
Facility maintenance technicians are responsible for ensuring that the interior and exterior of buildings are well-maintained and in good condition. This job requires a combination of technical skills, physical stamina, and problem-solving abilities. When facility maintenance technicians are successful in their duties, the building will be able to operate efficiently and safely.
However, if the technician fails to carry out the necessary responsibilities, this can lead to costly repairs and other issues that can disrupt the building's function. These issues can range from electrical and plumbing problems to HVAC malfunctions and even structural damage. In addition, facility maintenance technicians are also responsible for performing preventative maintenance, which can help avoid these problems from occurring in the first place.
Steps How to Become
- Earn a High School Diploma or GED. Most facility maintenance technicians must have a high school diploma or GED. Completion of vocational training in a related field is beneficial as well.
- Complete a Technical Program. If it is available in your area, completing a technical program in building maintenance technology will give you the most comprehensive knowledge and skills needed for the job.
- Obtain Certification. Certification is not required to become a facility maintenance technician, but it can give you an edge in the job market. There are various certifications available, such as the HVAC Excellence certification and the EPA refrigerant certification.
- Get On-the-Job Training. Many employers will provide on-the-job training as part of the hiring process. During this time, you will learn the specific skills and protocols required for the job.
- Get Certified in Other Specialties. Certain specialties may require additional certifications. For example, if you are working in a building that requires specialized knowledge of HVAC systems, you may need to get certified in HVAC maintenance.
Having a reliable and qualified Facility Maintenance Technician is essential for the smooth running of any business. Without a qualified technician, buildings can fall into disrepair and break down more frequently, leading to costly repairs and lost productivity. Proper maintenance can also prevent the need for emergency repairs, which can be expensive and time consuming.
A qualified technician will have the skills and knowledge to properly diagnose and repair any issues that may arise with the facility, as well as prevent them from occurring in the first place. They will be able to identify potential problems quickly and take proactive steps to fix them before they become a larger issue. they will be able to keep the facility up to code and in compliance with any relevant regulations.
Having a reliable and qualified Facility Maintenance Technician will not only save money in the long run, but it will also provide a safe, comfortable, and efficient environment for employees and customers alike.
You may want to check Chiller Technician, Heating Technicians, and Master Plumber for alternative.
Job Description
- Inspect and maintain assigned facility systems and equipment, such as HVAC, plumbing, electrical, security systems, and fire protection.
- Repair and replace defective parts and components, using hand tools and other equipment.
- Perform preventive maintenance on assigned facility systems and equipment, such as cleaning, lubricating, and changing filters.
- Respond to emergency maintenance requests in a timely manner.
- Monitor, test, and adjust all building systems including ventilation, temperature control, lighting, and alarms.
- Perform general carpentry work, painting, and minor plumbing repairs.
- Maintain accurate records of all maintenance activities.
- Comply with safety regulations and maintain clean and orderly work areas.
- Assist with the installation of new equipment and fixtures.
- Operate hand tools and other power tools in a safe and responsible manner.
Skills and Competencies to Have
- Knowledge of electrical, plumbing, HVAC, and carpentry systems.
- Ability to troubleshoot and diagnose equipment malfunctions.
- Ability to read and interpret blueprints, schematics, technical manuals, and other technical documents.
- Ability to use power tools and hand tools safely.
- Ability to perform basic calculations to measure materials and calculate costs.
- Ability to lift heavy objects and climb ladders.
- Excellent communication and customer service skills.
- Strong organizational skills and attention to detail.
- Knowledge of safety regulations and OSHA standards.
- Knowledge of the proper use of chemicals for cleaning, lubrication, and other maintenance tasks.
Maintaining a facility requires a wide range of skills and knowledge. A Facility Maintenance Technician must be able to troubleshoot and repair a variety of equipment and systems, including plumbing, electrical, and HVAC systems. They must also be able to follow safety protocols and use proper personal protective equipment when working with hazardous materials.
Knowledge of building codes, regulations, and guidelines is also essential. Facility Maintenance Technicians must have excellent customer service skills to interact with clients and co-workers. Most importantly, they must have the ability to think critically and problem solve in order to quickly diagnose and repair any issues that arise.
Without these skills, a Facility Maintenance Technician would not be able to properly maintain the facility, leading to costly repairs and dissatisfied customers.
Well Pump Installer, Irrigation Technician, and Industrial Plumber are related jobs you may like.
Frequent Interview Questions
- What experience do you have in facility maintenance?
- How do you handle difficult situations when working with coworkers or customers?
- Describe a time when you had to troubleshoot or solve a complex problem related to facility maintenance.
- How would you prioritize multiple tasks and ensure they are completed in a timely manner?
- What safety measures do you take when performing maintenance duties?
- Describe the methods you use to monitor the condition of a facility and its equipment.
- How do you stay informed of new regulations, policies, and technology related to facility maintenance?
- What strategies do you use to keep up with daily maintenance requests?
- What methods do you use to keep accurate records and logs of maintenance activities?
- How do you ensure that all necessary supplies and materials are available when needed?
Common Tools in Industry
- Power drill. used to create holes in metal, wood, plastic, and other materials. (eg: drilling screws into a wall)
- Impact Wrench. Used to quickly loosen or tighten nuts and bolts. (eg: tightening lug nuts on a car wheel)
- Hammer. Used to drive nails and other objects into surfaces. (eg: installing drywall)
- Socket Set. Used to tighten and loosen nuts and bolts. (eg: replacing a sink faucet)
- Pliers. Used to grip objects to pull, twist, crimp, or cut them. (eg: cutting and bending wire)
- Wrenches. Used to tighten or loosen nuts and bolts of different sizes. (eg: changing a bicycle tire)
- Screwdrivers. Used to drive screws into different types of materials. (eg: replacing a door handle)
- Ladder. Used to reach elevated areas. (eg: cleaning gutters or changing light bulbs)
- Flashlight. Used to see in dark places or small spaces. (eg: inspecting behind a wall for a water leak)
- Safety Equipment. Used to protect the user from potential hazards. (eg: wearing protective gloves when handling sharp objects)
Professional Organizations to Know
- American Institute of Plant Engineers (AIPE)
- Building Performance Institute (BPI)
- International Facility Management Association (IFMA)
- Association of Energy Engineers (AEE)
- National Association of Power Engineers (NAPE)
- Society of Maintenance and Reliability Professionals (SMRP)
- American Society for Healthcare Engineering (ASHE)
- American Society of Heating, Refrigerating and Air-Conditioning Engineers (ASHRAE)
- National Fire Protection Association (NFPA)
- American Society of Safety Engineers (ASSE)
We also have Plumbing Inspector, Commercial Plumber, and Swimming Pool Technician jobs reports.
Common Important Terms
- HVAC. Heating, Ventilation and Air Conditioning. A facility maintenance technician is responsible for installing, maintaining, and repairing HVAC systems to ensure a comfortable environment in buildings.
- Plumbing. The installation, maintenance, and repair of pipes, fixtures, and other apparatus for the distribution and use of water in a building.
- Electrical. The installation, maintenance, and repair of electrical wiring and equipment in a building.
- Appliance Repair. The installation, maintenance, and repair of appliances such as refrigerators, ovens, washers, and dryers.
- Carpentry. The fabrication and installation of wooden structures such as walls, floors, doors, and windows.
- Painting. The application of paint or other protective coatings to walls, ceilings, and other surfaces.
- Flooring. The installation, maintenance, and repair of flooring materials such as tile, hardwood, and carpet.
- Building Maintenance. The planning and implementation of regular inspections, repairs, and maintenance of a building's physical components.
- Landscaping. The construction and maintenance of outdoor areas such as gardens, walkways, patios, and driveways.
- Safety/Security. The implementation of security systems and safety protocols to protect the occupants of a building.
Frequently Asked Questions
What is the average salary for a Facility Maintenance Technician?
According to PayScale, the average salary for a Facility Maintenance Technician is $17.48 per hour.
What duties does a Facility Maintenance Technician typically perform?
Facility Maintenance Technicians are responsible for performing a variety of maintenance and repair tasks on buildings and grounds, including plumbing, electrical, carpentry, and HVAC repairs, as well as painting and general cleaning.
What qualifications are required to become a Facility Maintenance Technician?
Typically, Facility Maintenance Technicians need to have a high school diploma or equivalent, along with some experience in general maintenance and repair work.
How many hours do Facility Maintenance Technicians typically work?
Facility Maintenance Technicians usually work 40 hours per week, with some occasional overtime or on-call shifts.
What safety protocols should a Facility Maintenance Technician adhere to?
Facility Maintenance Technicians should always follow safety protocols such as wearing the appropriate safety gear and following Occupational Safety and Health Administration (OSHA) regulations.
What are jobs related with Facility Maintenance Technician?
- Gas Line Installer
- Boiler Operator
- Hydrojetter
- Septic System Installer
- Backflow Prevention Technician
- Septic Tank Technician
- Drain Cleaner
- Gasfitters
- Mobile Home Plumber
- Refrigeration Technician
Web Resources
- Facility Maintenance Technician - Center for Employment Training cetweb.edu
- Facility Maintenance Technician | Maintenance ¦ www.ccnn.edu
- What Does a Facilities Maintenance Technician Do? www.rsi.edu
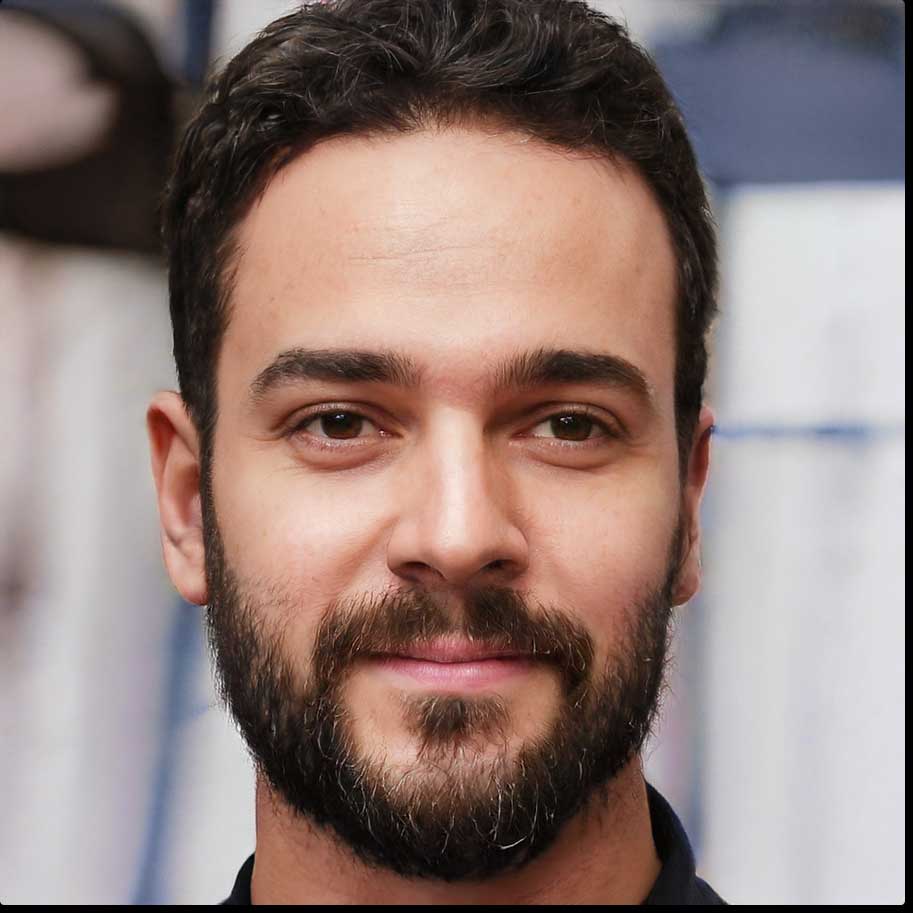